A Step-by-Step Guide To Successful CMMS Implementation
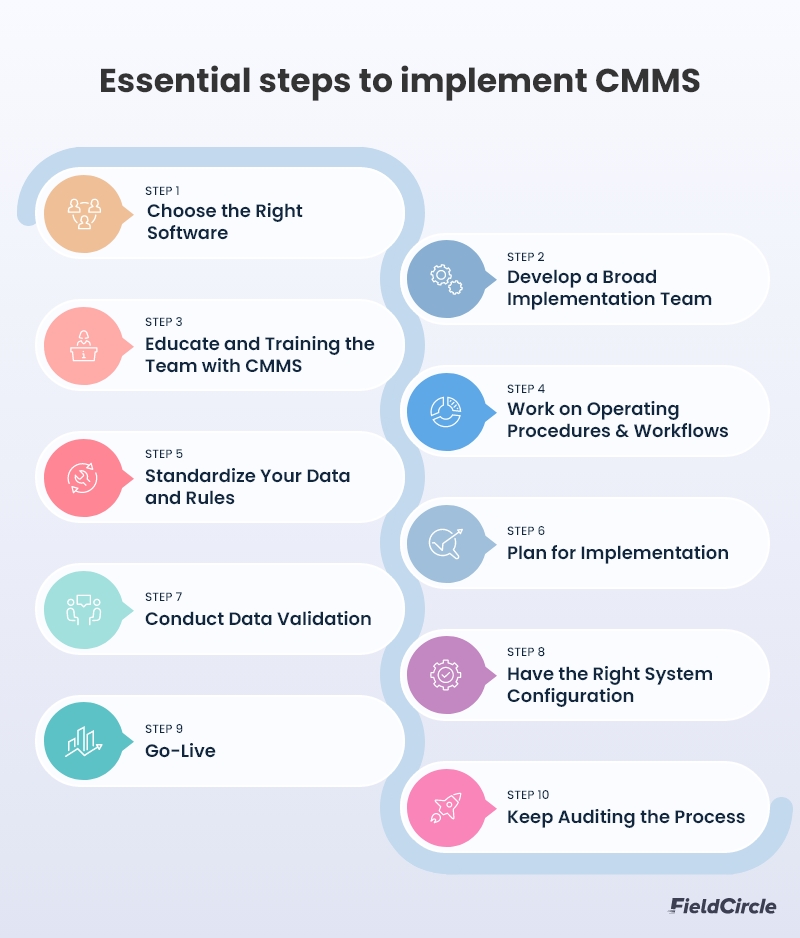
With the way technology adoption has happened across maintenance departments, CMMS implementation has been at the forefront for achieving process transformation and operational effectiveness.
But 65-70% of CMMS implementations fail and 45-50% fail to meet expectations after implementation. Why does it happen?
How to plan a CMMS implementation?
Is there a framework or step by step process to follow for successful CMMS implementation?
How do you get your organization and department ready?
We discussed these questions with numerous maintenance leaders, observed our implementation that went seamlessly and where we faced challenges, and compiled a list of steps to implement a CMMS successfully. If CMMS is a new system that you are looking to implement, then read through this ultimate guide.
What are the CMMS implementation Steps To Follow?
A successful CMMS implementation project plan follows a well-structured approach guided by the following steps:
- Step 1:Choose the Right Maintenance Management Software
- Step 2:Select an Expert and Develop a Broad Implementation Team
- Step 3:Educate and Train the Team with CMMS
- Step 4:Work on Operating Procedures and Workflows
- Step 5:Standardize Your Data and Rules
- Step 6:Plan for Implementation
- Step 7:Conduct Data Validation
- Step 8:Have the Right System Configuration
- Step 9:Go-Live
- Step 10:Keep Auditing the Process
Follow these ten steps to streamline your implementation and maximize long-term value from your maintenance operations.
Step 1: Choose the Right Maintenance Management Software
The correct CMMS software can make the difference between time and money being wasted and successful implementation. It’s crucial to consult the users of the software before making a decision. In this approach, you can rate your performance, identify your flaws, and work out what’s to blame for them.
A CMMS software system is intuitive and made to assist teams in managing maintenance plans, observing facility lifecycles, and managing spare parts inventories. However, the correct platform will rely on your organizational needs. Additionally, it should be simple to install, configure, and offer 100 percent server availability and dependability.
A good CMMS is flexible to accommodate organizations of different sizes and industry requirements. Whether you operate a small business with a handful of assets or a multinational corporation with an extensive infrastructure, CMMS can be tailored to meet your specific needs.
For smaller organizations, a CMMS with essential features like preventive maintenance scheduling and asset tracking may suffice. Conversely, larger enterprises will require a more comprehensive solution with advanced functionalities such as predictive maintenance analytics and enterprise-wide integration capabilities.
In general, when selecting a CMMS, you must look for these features so that the tool aligns with your organizational objectives:
- Preventive Maintenance Scheduling: There must be a strong functionality that enables proactive maintenance planning so that you can prevent equipment breakdowns.
- Work Order Management: You should be able to create, assign, and track maintenance tasks for timely resolution of issues smoothly.
- Inventory Management: The functionalities around inventory must offer a holistic ecosystem for inventory management whereby spare parts and consumable can be managed effectively.
- Asset Tracking: The tool must offer visibility into the location, condition, and maintenance history of assets, and aid in effective resource allocation.
- Reporting and Analytics: For all processes, you should be able to generate insightful reports and drive data-based decision-making.
- Integration Capabilities: In any case, the CMMS must integrate with essential external systems such as the existing ERP.
- User-Friendly Interface: Since the users may or may not be technical experts but come from technical as well as non-technical teams, the CMMS must offer an intuitive interface and easy navigation so that its features are leveraged in the best possible way.
- Scalability: The maintenance software product must be built using a robust technical architecture, considering that the business will grow and the tool will be able to accommodate the growth comfortably.
By taking into account these elements, you can be confident that as you proceed with the CMMS setup and utilization process, you won’t encounter any obstacles.
Step 2: Select an Expert and Develop a Broad Implementation Team
Implementing a software is not just one technical step; it is not a step to enhance a single function, but it fits in the whole spectrum of your business reengineering project. This is why it is crucial to make sure that every stakeholder in the CMMS implementation process understands your objective, your vision, and the need for the maintenance management software.
The expert must assist you in rallying support from other department specialists from diverse fields and get the best out of each of them in the implementation process. This is how a dedicated implementation team should be formed and work.
Since the implementation process extends across functions, consider hiring someone with expertise in purchasing, materials management, software engineering, and other relevant areas. By broadening the implementation team, you will also demonstrate to everyone the benefits of using a CMMS to the entire organization, especially the bottom line.
In terms of team dynamics, it’s crucial to consider how each member’s skill set and background contribute to the implementation process. Ideally, the team structure for CMMS software implementation will be made of
- Director-level Team: Provides strategic direction and authorizes funding for the implementation of the CMMS.
- Maintenance Leaders: Oversee and coordinate maintenance activities during the implementation process.
- System Administrator: Manages documentation requirements, assisting in the smooth operation and configuration of the CMMS.
- Project Manager: Coordinates tasks, schedules, and resources to ensure timely and successful implementation of the CMMS.
- Subject-matter Experts: Provides specialized knowledge and insights to tailor the CMMS to specific organizational needs.
- Implementation Specialists: Offer guidance, support, and expertise in implementing CMMS systems, optimizing the implementation process.
Step 3: Educate and Training the Team with CMMS
Earlier, the biggest assumption used to be that a new CMMS would be rolled out and people would adopt it easily. As more implementations started failing, businesses realized the importance of team training during CMMS implementation. When setting up a CMMS, make sure everyone on the maintenance team knows how to use the system effectively. Since you are going to use a new tool, you need to understand how it works, right? That’s why educating the team about how the CMMS functions is mandatory.
The team needs to be familiar with all its features. Make them know how by replacing manual, error-prone processes with automated, accurate maintenance management will lead to optimized asset performance.
Comprehensive training maximizes the team’s ability to use the CMMS effectively, reducing downtime through better maintenance practices. So, training must guide the team on customizing the CMMS to fit the organization’s needs. Train them in each CMMS process. Give them a thorough walk-through for setting up maintenance schedules, organizing equipment hierarchies, and creating workflows for managing work orders and inventory.
With the right training, the team can tweak the CMMS to match their existing processes, and make the transition smoother. Plus, it can connect it with other software it uses or equipment sensors to automate some tasks, which will save it time and effort in the long run.
Lastly, training should cover data hygiene and data security practices. Guide the team on following data privacy norms to abide by, because the tool would be handling loads of maintenance data volumes, and the rules will help keep this data safe.
Step 4: Work on Operating Procedures and Workflows
Examine your current processes carefully. Before deploying your CMMS, you must first map out your fundamental workflows, including your planning, maintenance scheduling, and coordinating procedures. It is essential to define work activity process flows to make sure that work is completed and properly documented.
Utilize workflow diagrams and develop flowcharts to illustrate the workflows involved in maintenance management, such as how work orders are initiated, assigned to technicians, completed, and closed. This helps visualize the sequence of actions and decision points. Implement version control for maintenance procedures to track changes and updates and ensure that all team members are working with the latest version of SOPs and workflows.
Next, expand your workflow documentation to reflect equipment-specific processes, asset classes, and different priority levels of work orders. For example, reactive maintenance for safety-critical equipment demands a different set of actions than scheduled inspections on low-impact assets. Break down each workflow into discrete steps, include escalation protocols, and identify triggers for notification rules and audit logging.
Further, add system-specific attributes such as role-based access to workflow steps, automated status changes, and time-stamped checkpoints. These elements help bridge the gap between manual procedures and digital execution. Don’t forget to plug in compliance checks and maintenance KPIs and metrics into your workflow nodes to give your CMMS teeth and not just bells and whistles.
Step 5: Standardize Your Data and Rules
Consistent data formats and rules ensure that the software behaves predictably and produces reliable results. Without standardization, inconsistencies can arise, leading to errors, confusion, and inefficiencies in the software.Likewise, when data formats and rules are standardized, it becomes easier to exchange data and integrate various software components seamlessly.
Lack of clarity in procedures gives more challenges in implementing CMMS. You must decide precisely how you want to format items, including how you describe assets and how you record asset maintenance work, to share, exchange, and understand data effectively.
By putting rules in place, you enable data uniformity. Data standardization is especially important during data migration, where poorly structured or inconsistent information can lead to complications when transferring data from legacy systems. To support this, define the following areas clearly when implementing CMMS:
- Field attributes
- Descriptions, Naming Conventions and Abbreviations
- Maintenance codes
- Priority work orders and Categories
- Data classification and taxonomy
- Data Units and Measurement Standards
- Data Encoding and Serialization Formats
- Data Validation and Integrity Constraints
Once you define these areas, create a master data dictionary before configuring the CMMS. Every term, abbreviation, category, and field type should be documented with definitions, permissible values, and usage context. Tie each data point to its parent table or asset hierarchy to eliminate ambiguity. Keep this reference available for both technical users and field personnel to avoid speaking at cross-purposes.
Next, integrate validation scripts and input controls into your CMMS forms. Mandatory fields, dropdown lists, regular expressions, and range checks stop garbage data from creeping in. You must assign data ownership roles to specific users or teams so the buck doesn’t get passed when a data mismatch shows up. Lastly, don’t forget to back your rules with real examples and edge cases to plug gaps in interpretation.
Step 6: Plan for Implementation
Planning the implementation of a computerized maintenance management system (CMMS) begins with a thorough understanding of maintenance requirements and organizational goals. Initially, define the CMMS project scope. Document the requirements in a Software Requirements Specification (SRS), outlining functionalities and performance criteria.
The CMMS implementation plan must then delve into architectural design, breaking down the system into different modules for various tasks. Then you build design patterns and develop testing strategies, covering unit, integration, and system testing to validate functionality and reliability.
Next, you must integrate continuous integration (CI) and continuous deployment (CD) practices and establish contingency measures to address potential risks or challenges. Throughout, the plan emphasizes adaptability and resilience, so that the CMMS meets evolving maintenance needs while aligning with organizational objectives.
Step 7: Conduct Data Validation
If you’re importing data from another system, conversion protocols need to be established and implemented, and lots of cleanups are necessary. Decide in advance who will be in charge of this phase and how you want to check high-quality data. Once the technical aspects have been resolved, it is time to gather data, proceed with your execution plan, and implement the standards you established.
Develop comprehensive data validation scripts to automate the detection and correction of anomalies, such as data type mismatches and formatting errors. By implementing robust conversion protocols and leveraging advanced validation techniques, you will streamline the integration process and seamlessly transfer high-quality data into the CMMS environment.
Validated data lays the groundwork for reliable asset management within the CMMS. Clean, verified data drives more accurate tracking, analysis, and reporting, all of which are important for streamlining asset management practices in the long run.
Step 8: Have the Right System Configuration
System configuration is important for several reasons; firstly, for application performance and stability, as a mismatched configuration creates chances of resource bottlenecks, such as insufficient CPU power or memory, causing slowdowns or crashes. Moreover, compatibility issues with required libraries or runtime environments renders the application unusable.
Outdated software versions or misconfigured settings also increase vulnerabilities, making the system susceptible to cyber threats and data breaches. Regular updates and security patches help mitigate these risks. Additionally, a well-configured system enhances reliability by minimizing hardware failures and software conflicts. Therefore, maintaining an up-to-date and properly configured system is essential for performance optimization and robust security.
Step 9: Go-Live
Many organizations choose to implement a CMMS in different phases with their unique dependability journey. However, every organization’s implementation process is not the same. By integrating the CMMS software gradually, you can address pinpointed issues at a rate that fits your organization’s capacity as well as expand the system as it expands.
Running a pilot program in one place first will support a phased rollout strategy if your firm has numerous locations. You can find out what functions well and what poorly by putting the system to the test at one facility. A trial run gives you the opportunity to precisely tailor the CMMS to your needs and objectives.
Step 10: Keep Auditing the Process
The process of implementing a CMMS is ongoing, and there is always room for improvement in maintenance operations. Determine what is effective and what needs to be changed. The system requires maintenance after it is put into place, just like your assets do. Setting up key performance indicators (KPIs) enables you to monitor your objectives for continuous improvement. So, you must evaluate the health of your CMMS from time to time with regular audits and sustain productivity levels. Use historical data from the CMMS to:
- Make judgments about the maintenance process and asset breakdowns and their causes.
- Build reports to communicate your team’s progress and accomplishments to the leadership.
- Determine the improvement areas.
- Continuously provide training to avoid the emergence of negative habits and insufficient data.
Meticulously Follow These Steps to Implement CMMS Software
Implementing a Computerized Maintenance Management System (CMMS) requires a comprehensive evaluation at strategic, tactical, and operational levels to ensure its effectiveness and following CMMS best practices. Strategically, it’s crucial to reassess maintenance goals in light of technological advancements, considering factors like plant dependability and future infrastructure needs.
From a tactical perspective, existing assumptions about failure modes and criticality analysis must be reviewed to align with evolving plant layouts and procedures. Operationally, maintenance managers need to evaluate the effectiveness of planned maintenance work. This is what a good CMMS vendor will always follow.
To derive value out of your investment, seek expertise from FieldCircle. By offering a demo, our CMMS implementation consultants will guide you through the practical process of implementation and demonstrate how a well-approached implementation process fetches positive outcomes.