Manufacturing Maintenance Software
Streamline factory maintenance operations with FieldCircle’s manufacturing maintenance software. Designed specifically for industrial production environments, our Manufacturing CMMS simplifies management of essential assets such as heavy machinery, production lines, conveyors, and industrial equipment through real-time machine performance tracking and automated work order management. Featuring preventive maintenance, predictive analytics, and spare parts management, our manufacturing maintenance software reduces downtime, minimizes equipment failures, and enhances workplace safety. By extending equipment lifespan and supporting cost control, our manufacturing maintenance solution drives long-term operational success, ensuring consistent productivity and reduced downtime across factory operations.
How Manufacturing Maintenance Software Works?
Explore how the key features work without signing up for a trial or demo.
Manufacturing maintenance software integrates various features and functionalities to streamline maintenance processes, optimize resources, and ensure the smooth operation of manufacturing facilities.
Data Input and Collection
The software collects relevant data from various sources, including equipment sensors, maintenance logs, work orders, and inspection reports. The collected data also includes information about equipment performance, maintenance schedules, inventory levels, and resource allocation.
Work Order Assignment
The system prioritizes work orders based on urgency and importance, then assigns maintenance personnel or contractors according to their skills, availability, and workload.
Centralized Database
A maintenance manufacturing software stores the collected data in a centralized database, providing a single source of insight for maintenance-related information. This database is accessible to authorized users, including maintenance technicians, managers, and administrators.
Work Execution
Maintenance personnel access detailed work order information, including equipment details and instructions. They document completed tasks, materials used, and any additional issues discovered during the maintenance process. Mobile apps enable real-time updates in the field.
Asset Management
The software allows users to input and track information about manufacturing equipment and assets, which includes details such as equipment specifications, maintenance history, warranty information, and repair records.
Maintenance Scheduling
Based on the collected data and predefined maintenance schedules, the software generates maintenance tasks and schedules, including both preventive and maintenance tasks. All the tasks are scheduled at regular intervals to prevent equipment failures, along with corrective maintenance tasks, which are triggered in response to equipment breakdowns or failures.
Work Order Management
Work orders are created and assigned to maintenance technicians based on priority, availability, and expertise. Technicians receive notifications about new work orders and can access detailed instructions, checklists, and documentation related to each task.
Execution and Documentation
The maintenance software can help technicians execute maintenance tasks, record work performed, and update maintenance logs in real time. Additionally, this software performs tasks such as equipment inspections, repairs, replacements, and preventive maintenance activities. In some cases, documentation such as photos, videos, and notes can be attached to each work order for reference and future analysis.
Inventory and Supplies Management
The software tracks inventory levels of spare parts, supplies, and consumables needed for maintenance activities. It also sets automatic reorder alerts to ensure that critical items are restocked promptly, minimizing downtime due to stockouts.
Reporting and Analytics
The software provides tools for generating reports and analyzing maintenance performance, which includes metrics such as equipment uptime, mean time between failures (MTBF), mean time to repair (MTTR), maintenance costs, and compliance with maintenance schedules and industry regulations. Customizable dashboards of the software allow users to visualize data and identify trends, patterns, and areas for improvement.
Integration with Other Systems
Manufacturing maintenance software may integrate with other systems, such as enterprise resource planning (ERP) software, asset management systems, and equipment monitoring systems, which allows for seamless data exchange and coordination across different departments and functions within the organization.
Features of Manufacturing Maintenance Software That Help You Unlock Efficiency
Manufacturing maintenance software plays a pivotal role in coordinating maintenance activities,
minimizing
equipment downtime,
and ensuring a timely response to maintenance requests with some exclusive
features
Calendar-based Scheduling
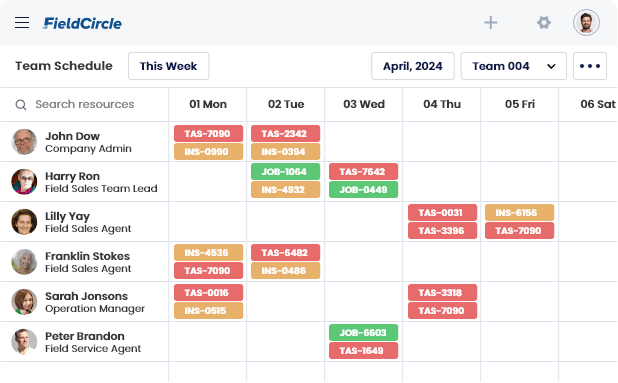
Streamlines maintenance activities by organizing them into an intuitive, easy-to-use calendar format. This feature facilitates efficient planning and tracking of maintenance tasks, ensuring they are performed timely and systematically. Users can set reminders, schedule recurring maintenance, and allocate resources effectively, thereby avoiding overlaps or conflicts in the maintenance schedule.
Preventive Maintenance & Inspection
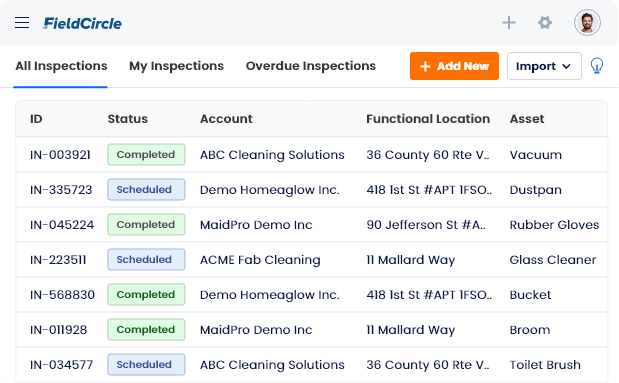
Schedules regular maintenance and inspections, thereby helping prevent equipment failures. Other perks of this feature include a prolonged extension of equipment life, reduced unplanned downtime, and optimized maintenance costs.
Work Order Management
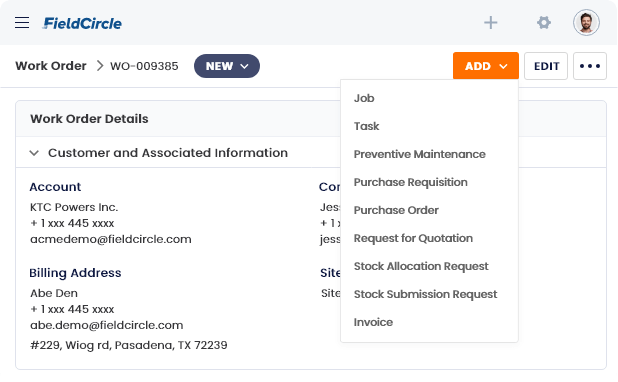
Streamlines the creation, assignment, tracking, and completion of work orders. An essential feature that organizes maintenance tasks, enhances communication between teams, and ensures accountability and transparency in the maintenance process.
Inspection Score & Failed Item Reports
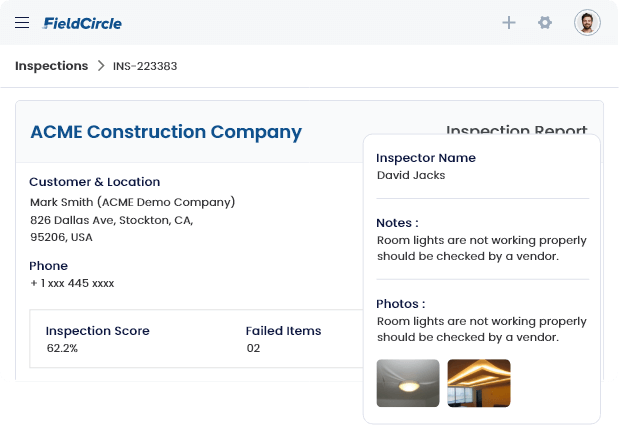
Provides detailed insights into equipment performance and maintenance needs. This exclusive feature plays a crucial role in identifying potential issues before they escalate, enabling proactive maintenance strategies, and maintaining high-quality standards and compliance with industry regulations.
Equipment Management
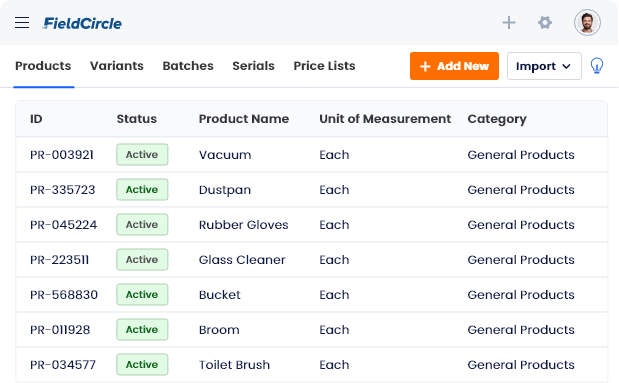
Offers comprehensive tracking and management of all manufacturing equipment. This feature also assists users in recording equipment history, tracking usage, and monitoring performance effectively.
Location and Site Management
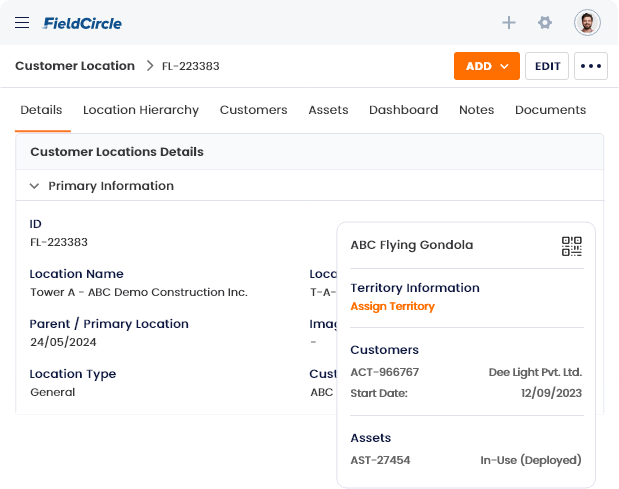
Enables effective tracking and management of equipment, machinery, and resources across different locations within a site or across multiple sites. With this feature, users can simplify complex tasks like monitoring maintenance schedules, asset performance, and resource allocation, resulting in higher productivity and reduced downtime in manufacturing operations.
Vendor Management with RFQ and PO
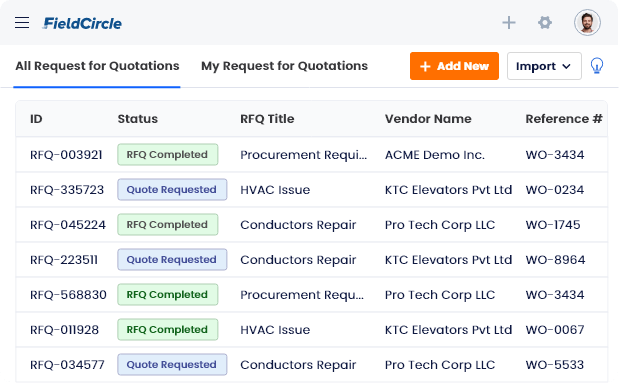
Facilitates managing vendors, creating and tracking Requests for Quotation (RFQs), and managing Purchase Orders (POs). In short, this feature helps streamline the procurement process, manage supplier relationships, and ensure cost-effective operations.
Time-tracking & Timecards
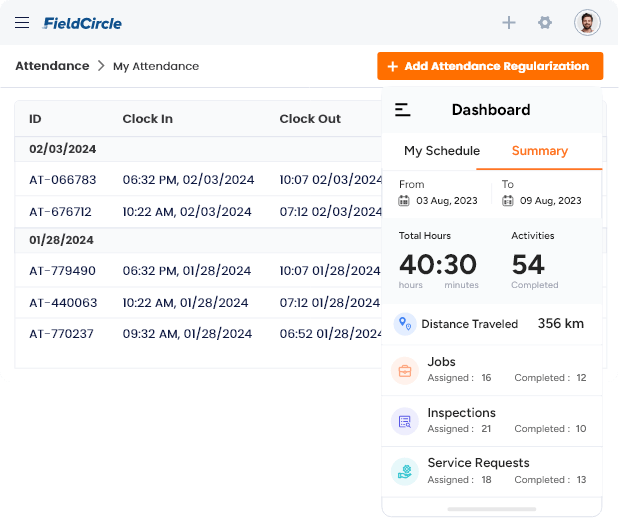
Tracks the time spent by technicians on specific tasks, enabling improved workforce management, efficient billing, and enhanced productivity analysis.
Contract & SLA Management
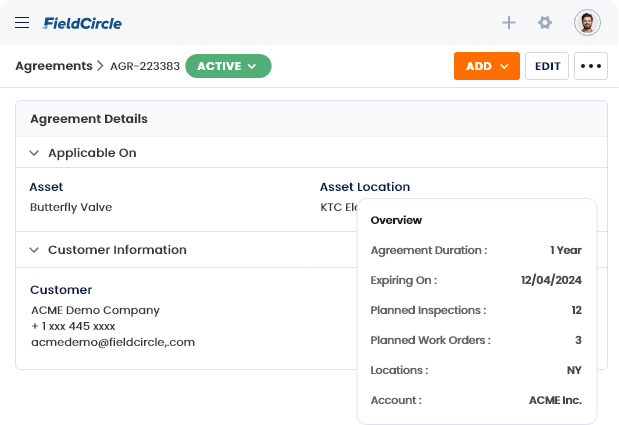
Simplifies tracking agreements and warranty claims, improving efficiency and reducing costs due to expired warranties or overlooked contract terms. This ability of our manufacturing management software alerts users to approaching renewal dates or warranty expirations is particularly beneficial.
Inventory & Supplies Management
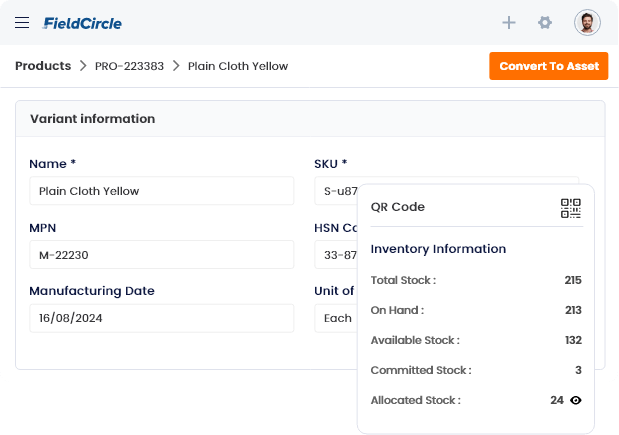
Enables real-time tracking of parts and supplies, ensuring availability and minimizing downtime. With exclusive features like automatic reorder alerts, inventory audits, and the ability to analyze inventory trends for better resource planning are included.
Reports, Analytics and Dashboards
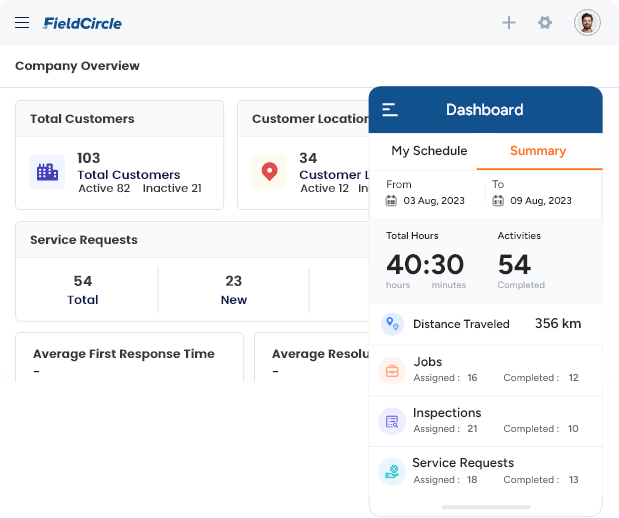
Offers insights into maintenance operations, cost trends, and performance metrics with customizable dashboards for different user roles. With the help of this feature, users can view and get relevant data at a glance.
Full Mobile Accessibility
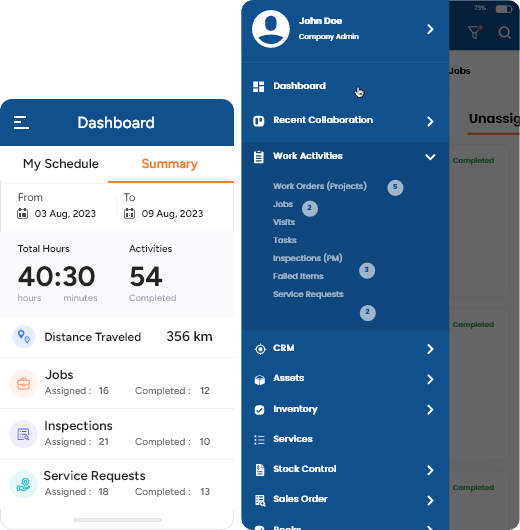
Facilitates the technicians and managers to access information, update records, and receive notifications on the go. This feature thus enhances responsiveness and operational flexibility.
QR Code Labelling and Scanning
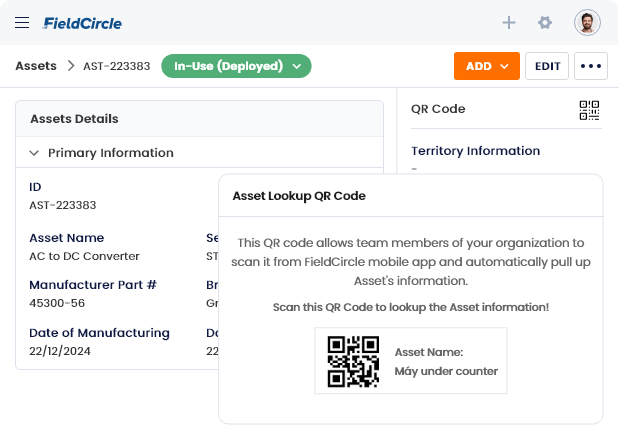
Provide easy access to technicians regarding the asset’s maintenance history, specifications, and manuals by scanning its QR code, enhancing efficiency and accuracy in maintenance tasks.
Asset Management
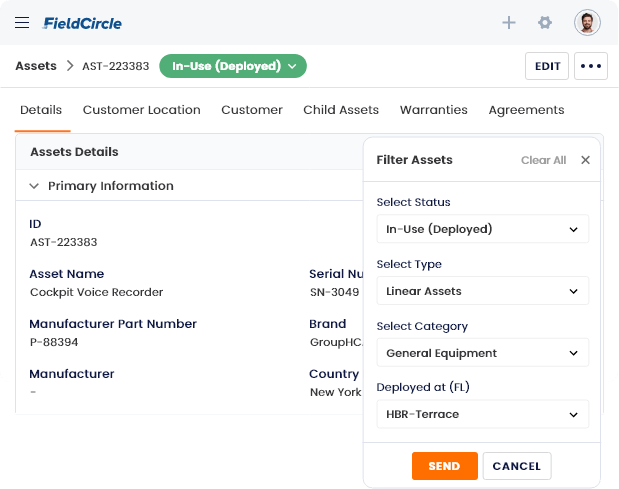
Tracks the life cycle of manufacturing equipment in addition to monitoring asset performance, scheduling preventive maintenance, and recording repair histories effectively increasing productivity and reducing manufacturing downtime.
Checklist Template Management
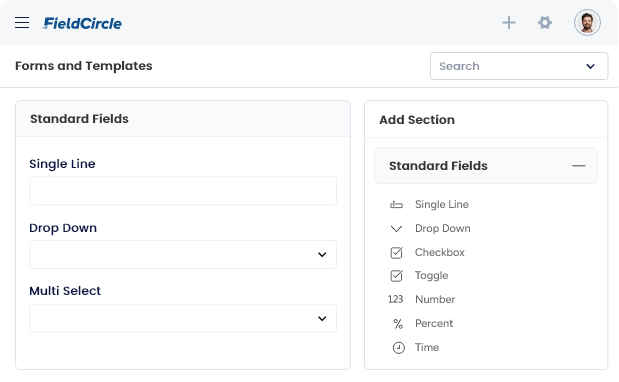
Ensures consistency in maintenance procedures and compliance with industry standards to maintain efficiency, visibility, and collaboration among teams.
Technician and Crew Management
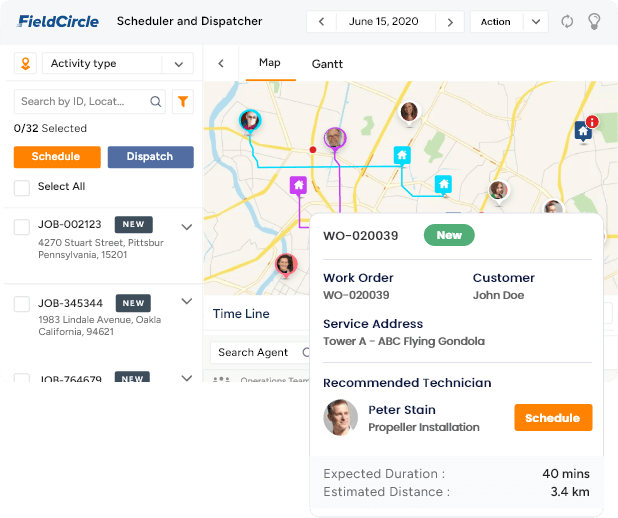
Aids in scheduling, tracking work hours, assessing performance, and ensuring the right technician is assigned to each task based on their expertise and workload.
The Impact of FieldCircle’s Manufacturing Maintenance Software that Customers Experience
Why Businesses Pick FieldCircle Over Other Manufacturing CMMS
Our CMMS disrupts the way you have been managing your manufacturing plant,
Integrations That Empower Your to Fully Leverage Our Manufacturing Maintenance Software
FieldCircle’s maintenance manufacture software enhances the functionality and efficiency of a manufacturing unit by seamlessly integrating with the existing systems
Companies Like Yours Are Seeing These Results
With Our Manufacturing Maintenance Software
FieldCircle has provided a positive experience by significantly improving our service and maintenance operations through its robust features and reliable performance.

FieldCircle has been transformative for our ops. We were already using technologies but FC has replaced most due to its comprehensiveness and awesome support team.

Success Stories Led by Our Manufacturing Maintenance Management Software
Discover the remarkable impact of FieldCircle as our trusted clients share their success stories and
client feedback on how
they have transformed their service operations.

Cushman & Wakefield
Cushman & Wakefield, a global powerhouse in the commercial real estate services sector, enhances customer satisfaction, improves operational profitability, and achieves better vendor collaboration with FieldCircle.
Read the Story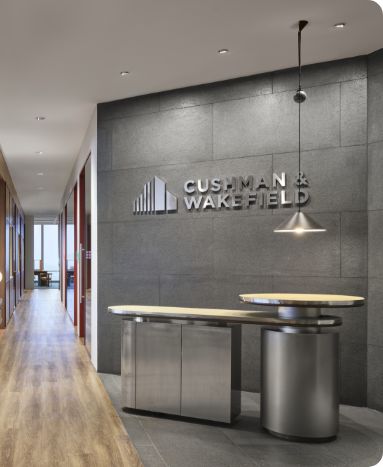

TSI Power
A leading US-based manufacturer, TSI Power Corporation, USA improves resource utilization, enhances productivity with FieldCircle implementation.
Read the Story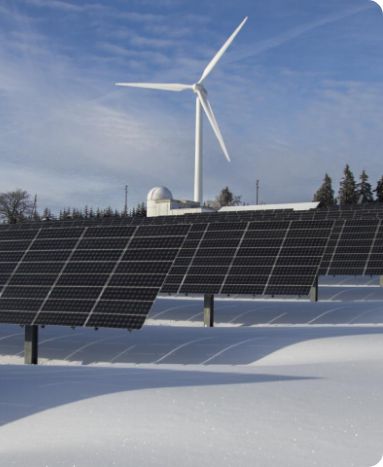

Yourspace
YourSpace partners with FieldCircle to achieve service operations excellence leading to higher profitability and customer experience.
Read the Story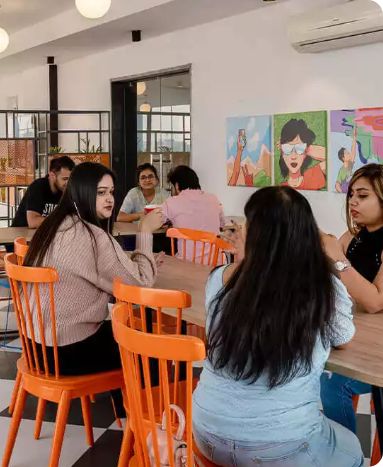

Nicco Engineering
Speciality maintenance service provider achieves more agile, transparent, and resilient service operations with FieldCircle.
Read the Story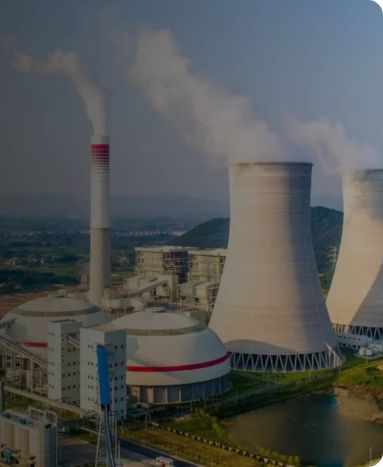
Book a Personalized Demo
Learn how your businesses can use FieldCircle’s Manufacturing Maintenance Software to achieve more efficient, transparent, and profitable service operations.
By submitting your details, you agree that we may contact you by call, email, and SMS and that you have read our terms of use and privacy policy.
Frequently Asked Questions (FAQs)
Quick answer to questions you may have.
What is Manufacturing Maintenance Software?
Manufacturing maintenance software is a digital solution designed to manage, schedule, and track maintenance activities for manufacturing equipment and machinery. It helps reduce downtime and ensure efficient production.
Would Field Circle Help Us Import Data From Other Maintenance Platforms?
Yes, with FieldCircle’s manufacturing maintenance software, you can synchronize and access your data across all platforms and devices. Furthermore, our software permits complete integration with popular systems and applications.
Is Training Sessions Available for Our Employees To be Proficient With Your CMMS?
Absolutely! We offer dedicated training programs that enable your employees to understand and operate our CMMS proficiently.
How Often Do Your CMMS Get Update?
Yes, we do frequently update our CMMS to ensure you always have access to the latest features and enhancements. These updates also enhance our product’s functionality, security, and usability.
Do Future Updates Cost Me An Additional Amount?
Our motto is to provide your business with continuous value without additional costs. However, the commitment to provide future updates as part of our service must confirm our service level agreements as well.