Predictive Maintenance Software
Unplanned downtimes reduce asset productivity and increase maintenance overheads. FieldCircle’s Predictive Maintenance Software applies real-time IoT data, machine learning, and automated diagnostics to detect performance anomalies and forecast failures before they happen. The system helps identify risks early, trigger automated maintenance actions, and improve decision-making across field operations. Designed for businesses managing critical infrastructure or distributed assets, the platform delivers condition-based alerts, data-backed scheduling, and cross-site visibility—supporting a shift from reactive repairs to predictive planning. With reduced downtime, optimized maintenance costs, and extended equipment life, FieldCircle enables long-term operational reliability.
How Predictive Maintenance Software Works?
Explore how the key features work without signing up for a trial or demo.
Predictive Maintenance (PdM) Software leverages advanced technologies to foresee potential equipment failures, enabling businesses to schedule maintenance efficiently and avoid costly downtime. Here’s a detailed look at the workflow process of FieldCircle’s Predictive Maintenance Software:
Data Collection
Predictive maintenance begins with the collection of data from equipment achieved through sensors and IoT devices installed on the machinery, which continuously gather real-time information on various metrics such as temperature, vibration, pressure, and operational status. Additionally, historical maintenance records and performance data are integrated into the system, providing a comprehensive dataset that captures the equipment’s current and past conditions.
Data Transmission
Once collected, the data is transmitted to a central system via wired or wireless connections, ensuring that it is accessible in real-time for immediate analysis. Cloud storage solutions are typically employed to store this data, offering scalability and ease of access.
Data Processing and Analysis
In the data processing stage, raw data undergoes cleansing to remove any noise or irrelevant information, thereby ensuring its accuracy. Following this, relevant features and patterns are extracted from the data. This involves identifying significant trends, such as fluctuations in vibration levels or temperature changes, which are critical for predicting equipment health and potential failures.
Machine Learning and AI Algorithms
Advanced machine learning algorithms are then employed to analyze the processed data. These algorithms are trained using historical and real-time data to understand normal operating conditions and identify patterns that precede equipment failures. The resulting predictive models can analyze deviations from normal conditions, thus forecasting potential issues before they occur.
Real-Time Monitoring
Our PdM software continuously monitors the equipment in real-time, applying predictive models to assess the machinery’s current state. This constant surveillance allows the system to detect anomalies or deviations from normal operating conditions as soon as they occur, flagging them for further analysis and potential intervention.
Alerts and Notifications
When the predictive models detect a potential issue, the system automatically generates alerts and notifications. These alerts can be sent via email, SMS, or a dedicated app, ensuring that maintenance teams are promptly informed. Alerts are categorized by priority levels, helping teams prioritize and address the most urgent issues.
Diagnostic Insights
The software provides detailed diagnostic insights into the potential causes of the predicted failures by conducting root cause analysis to understand why a deviation has occurred and offering actionable maintenance recommendations. These insights help maintenance teams to not only fix the immediate issue but also to prevent future occurrences by addressing the underlying causes.
Maintenance Scheduling
Based on the predictive insights, the software integrates with maintenance management systems to automate the scheduling of maintenance activities. This ensures that maintenance tasks are planned efficiently, avoiding unnecessary downtime.
Execution and Reporting
Technicians carry out the scheduled maintenance activities, addressing the predicted issues before they lead to equipment failure. The outcomes of these maintenance tasks are reported back into the system, providing valuable feedback. This feedback loop helps refine and improve the predictive models, ensuring they remain accurate and reliable.
What are the Features of Predictive Maintenance Software?
Predictive Maintenance (PdM) Software offers a range of powerful features designed to enhance the efficiency and effectiveness of your maintenance operations. Here are some of our software’s key features:
Real-Time Monitoring
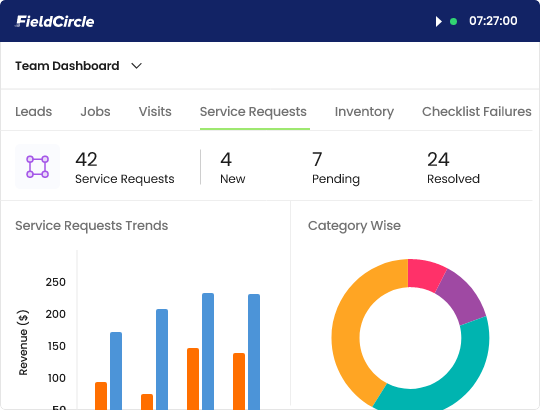
Our PdM software provides continuous real-time equipment monitoring through sensors and IoT devices. This feature ensures that all operational parameters are constantly tracked, allowing for immediate detection of any anomalies or deviations from normal conditions.
Data Integration
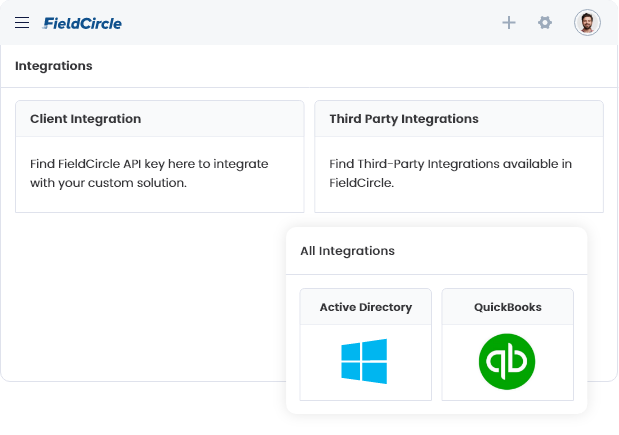
The software integrates various data sources, including historical maintenance records, real-time sensor data, and external data sets. This comprehensive integration ensures a robust dataset for accurate analysis and predictive modeling.
Advanced Analytics and Machine Learning
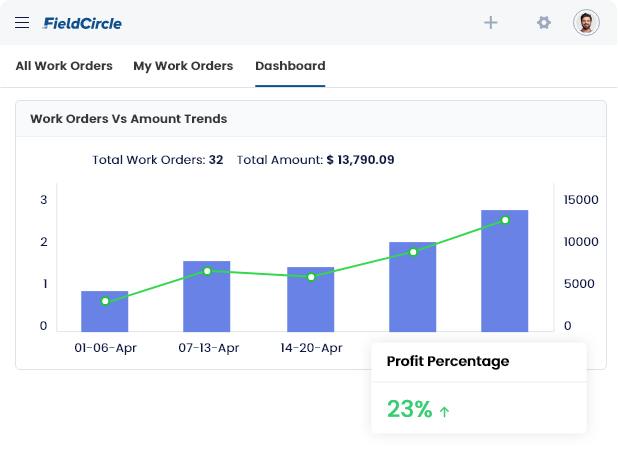
Leveraging advanced analytics and machine learning algorithms, our PdM software can analyze vast data to identify patterns and predict potential equipment failures. These predictive models continuously learn and improve over time, increasing their accuracy and reliability to offer the most incredible results.
Automated Alerts and Notifications
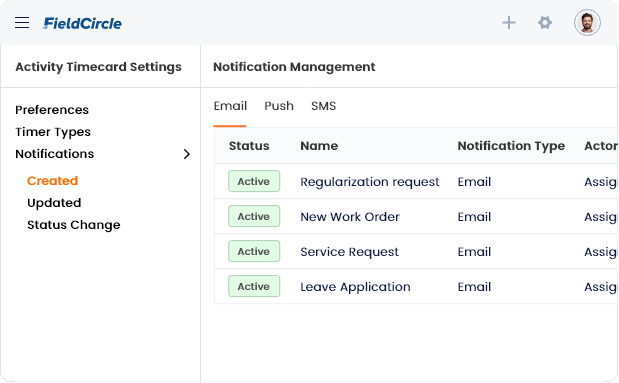
Our PdM software automatically generates alerts and notifications when potential issues are detected. These alerts can be customized and prioritized based on severity, ensuring that maintenance teams are informed promptly and can take timely action.
Diagnostic Insights and Root Cause Analysis
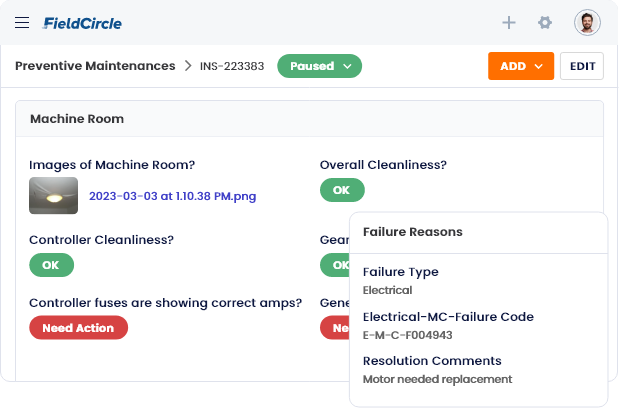
The software provides detailed diagnostic insights and root cause analysis for any detected anomalies. This feature helps maintenance teams understand the underlying causes of issues and take appropriate corrective actions to prevent future occurrences.
Maintenance Scheduling and Planning
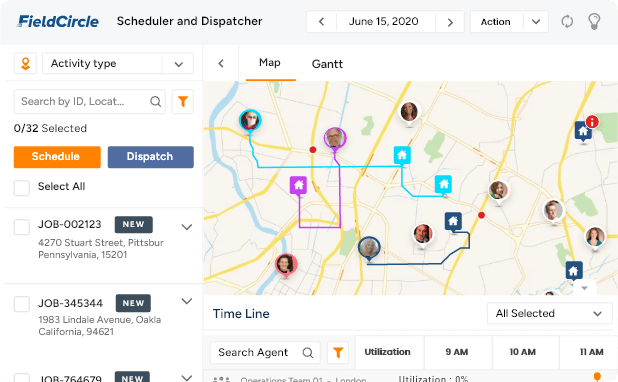
Our PdM software integrates with maintenance management systems to automate maintenance activity scheduling. It ensures that maintenance tasks are efficiently planned, minimizing downtime and optimizing resource allocation.
Asset Health Dashboard
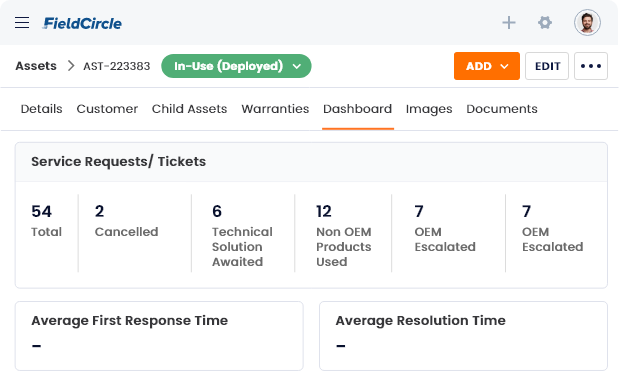
An intuitive asset health dashboard offers a comprehensive view of the condition of all monitored equipment. This dashboard provides real-time insights and key performance indicators (KPIs), enabling maintenance teams to make informed decisions quickly.
Customizable Reports and Analytics
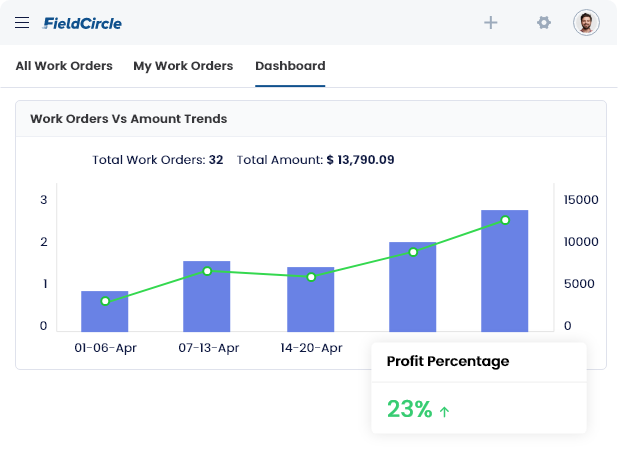
The software can generate customizable reports and analytics, providing valuable insights into maintenance performance, equipment health, and predictive accuracy. These reports support data-driven decision-making and continuous improvement efforts.
Integration with Enterprise Systems
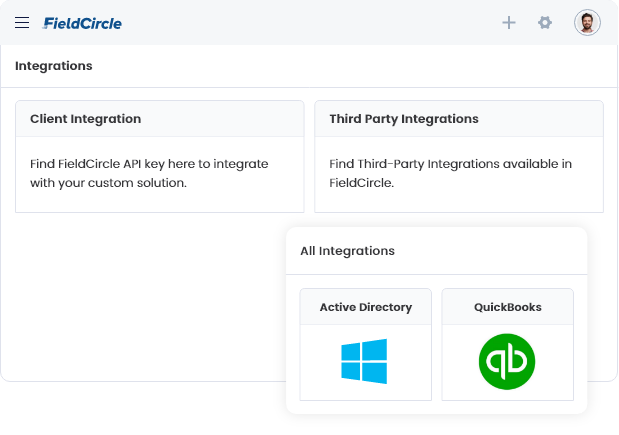
FieldCircle’s PdM software can be integrated with various enterprise systems such as ERP (Enterprise Resource Planning), CMMS (Computerized Maintenance Management Systems), and EAM (Enterprise Asset Management). This seamless integration ensures a unified approach to maintenance management across the organization.
The Impact of FieldCircle’s Predictive Maintenance Software
FieldCircle’s Predictive Maintenance Software revolutionizes how businesses approach equipment maintenance, delivering significant benefits that enhance operational efficiency, reduce costs, and extend asset life. Here’s a closer look at the transformative impact:
Why Choose Fieldcircle For Predictive Maintenance Software?
Choosing FieldCircle for Predictive Maintenance Software offers a multitude of compelling reasons:
Industries That Can Benefit
From Our Predictive Maintenance Software
FieldCircle’s Predictive Maintenance Software offers tailored solutions to meet the unique needs of each industry, helping businesses across diverse sectors improve operational efficiency, reduce costs, and enhance asset reliability.
What Customers Say
About Our Predictive Maintenance Software?
FieldCircle has provided a positive experience by significantly improving our service and maintenance operations through its robust features and reliable performance.

FieldCircle has been transformative for our ops. We were already using technologies but FC has replaced most due to its comprehensiveness and awesome support team.

Business That Trust Us For Predictive Maintenance Software
Discover the remarkable impact of FieldCircle as our trusted clients share their success stories and
client feedback on how
they have transformed their service operations.

Cushman & Wakefield
Cushman & Wakefield, a global powerhouse in the commercial real estate services sector, enhances customer satisfaction, improves operational profitability, and achieves better vendor collaboration with FieldCircle.
Read the Story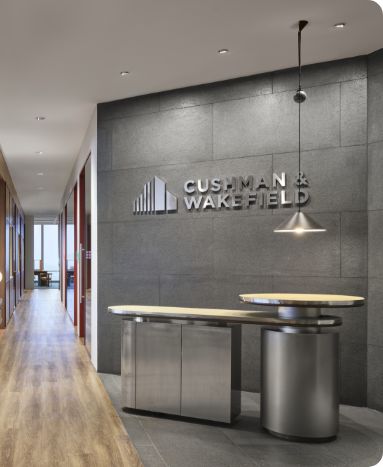

TSI Power
A leading US-based manufacturer, TSI Power Corporation, USA improves resource utilization, enhances productivity with FieldCircle implementation.
Read the Story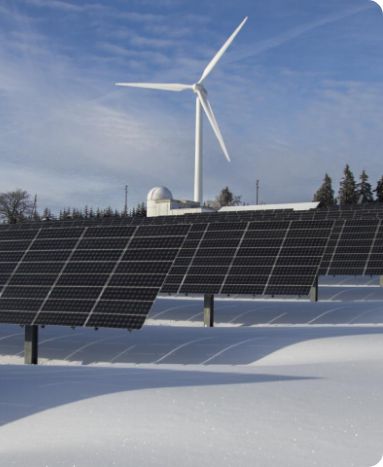

Yourspace
YourSpace partners with FieldCircle to achieve service operations excellence leading to higher profitability and customer experience.
Read the Story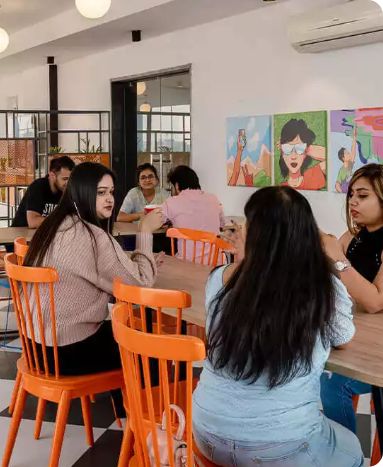

Nicco Engineering
Speciality maintenance service provider achieves more agile, transparent, and resilient service operations with FieldCircle.
Read the Story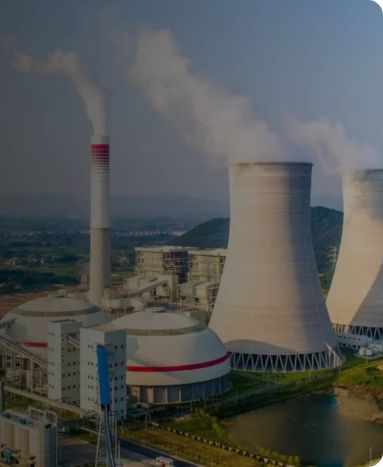
Book a Personalized Demo
Learn how your business can use FieldCircle’s predictive maintenance software to achieve more efficient,
transparent operations.
By submitting your details, you agree that we may contact you by call, email, and SMS and that you have read our terms of use and privacy policy.
Frequently Asked Questions (FAQs)
Quick answer to questions you may have.
What is Predictive Maintenance Software?
Predictive Maintenance Software utilizes advanced analytics and machine learning algorithms to forecast potential equipment failures before they occur. By analyzing real-time data from sensors and historical maintenance records, the software predicts when maintenance is needed, helping businesses avoid costly downtime and extend the lifespan of their assets.
How does Predictive Maintenance Software differ from other maintenance approaches
Predictive Maintenance Software differs from traditional maintenance approaches, such as reactive and preventive maintenance, by leveraging data-driven insights to predict equipment failures before they happen. Instead of waiting for equipment to break down or performing maintenance based on a fixed schedule, predictive maintenance allows for proactive, targeted interventions, optimizing maintenance efforts and minimizing disruptions.
What are the benefits of using Predictive Maintenance Software?
Some key benefits of using Predictive Maintenance Software include:
- Reduced downtime and increased operational efficiency
- Cost savings through optimized maintenance scheduling and resource allocation
- Extended equipment lifespan and improved reliability
- Enhanced safety for personnel and assets
- Data-driven decision-making and continuous improvement
Is Predictive Maintenance Software suitable for businesses of all sizes?
Yes, Predictive Maintenance Software can benefit businesses of all sizes across various industries. Whether you’re a small business with a handful of critical assets or a large enterprise managing a complex fleet of machinery, the software can be tailored to meet your specific needs and scale with your organization’s growth.
How easy is it to integrate Predictive Maintenance Software into existing systems
FieldCircle’s Predictive Maintenance Software is designed for seamless integration with existing enterprise systems, including ERP, CMMS, and EAM platforms. Our team works closely with clients to ensure smooth integration, providing personalized onboarding and support throughout the process.
Is Predictive Maintenance Software secure and compliant with industry standards?
Yes, FieldCircle prioritizes the security of your data and complies with industry standards and regulations. Our Predictive Maintenance Software employs robust encryption protocols, data protection measures, and best security practices to safeguard your sensitive information and ensure compliance with relevant standards.
How can I get started with FieldCircle’s Predictive Maintenance Software?
Getting started with FieldCircle’s Predictive Maintenance Software is easy! Simply reach out to our team to schedule a demo and discuss your specific requirements. We’ll guide you through the process, from initial setup to personalized training and ongoing support, to ensure that you maximize the benefits of our software for your business.