What is CMMS Used for? And How Does It Help Maintenance Management?
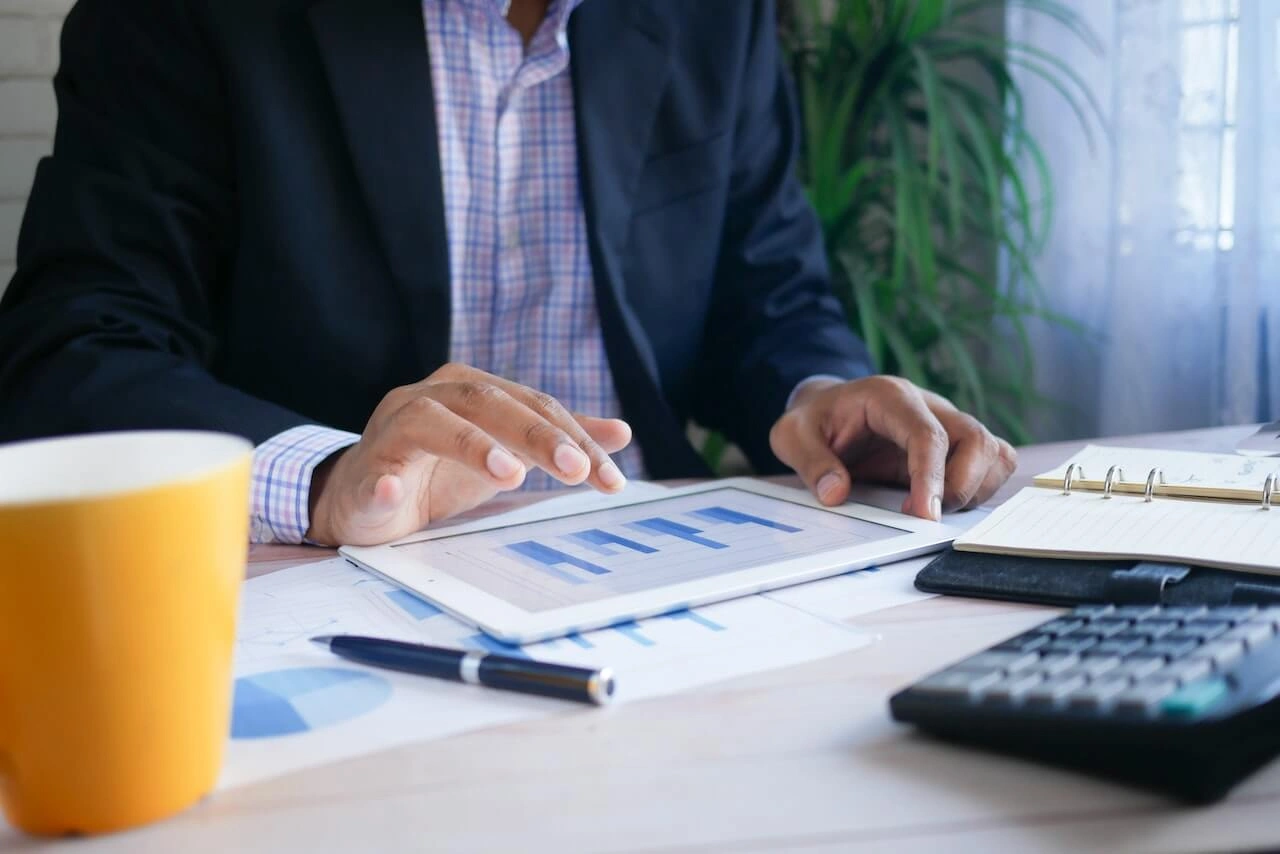
You know how every second counts when it comes to staying ahead in your game. It’s all about maximizing efficiency and minimizing downtime, right?
Well, let me introduce you to CMMS – the Computerized Maintenance Management System, the industry’s best-kept secret that’s here to revolutionize your maintenance management journey.
Interestingly embracing CMMS, businesses like yours are saving up to 20% in maintenance costs and experiencing a 60% reduction in equipment downtime as per ReliabilityWeb. These stats don’t lie, and the impact is truly mind-blowing.
In this blog, we’ll uncover its myriad of applications and show you how it can effortlessly solve even your most intricate maintenance challenges. Discover how CMMS empowers you to fully control your assets, streamline workflows, and optimize maintenance schedules for peak performance.
What is CMMS Used for?
Professionals use such solutions to plan and manage operations and production efficiency with streamlined tasks. It helps improve the assets’ life span, reduce equipment downtime, and lower repair costs. This increases the overall productivity of the company.
The analytical dashboard in the application enables the management of equipment and inventory data and stores the history of assets and service management-related activities in one location. This supports the manager to plan and make accurate decisions.
Previously, professionals used paper and pen or spreadsheets to manage operations. This method had many disadvantages and couldn’t streamline operations effectively. As the need for efficiency grew, professionals began adopting software tools specifically for maintenance management—a shift that marked a significant milestone in the history of CMMS. These systems evolved to make maintenance processes more structured, automated, and data-driven.
Work order management
The main use of the service management solution is to help managers track work orders. All information related to the work history is stored in the database. The tracking solution provides access to data for planning and scheduling, equipment, costs, materials, other work-related documents, and failure analysis. After the work is completed, the technicians can mark it as completed, and the manager gets notifications about it in real-time. This ensures that no equipment stays under maintenance for a long period.
Preventive maintenance
It helps to prevent the equipment from being repaired. This is carried out by scheduling proper care before equipment failure.
How do the managers know which equipment needs maintenance? The digital tool carries out this work by analyzing the equipment performance, asset care activities, etc.
It helps to purchase new parts for the item, so there will be no delay in purchasing by avoiding last-minute confusion.
Asset management
Asset management is protecting your assets, similar to the preventive maintenance service. Asset management provides basic data like the image and specification of the asset, warranty, history, lifetime, purchase date, parts manufacturers, and some important information.
Using this data, you can predict and plan for operational upkeep before they arise. Asset care can be easily tracked and handled with a feature-rich management framework.
Task Scheduling
Task scheduling is an important feature of management digital applications.
Every piece of equipment and asset needs preventive maintenance at a particular period. The PM is a task scheduled priorly to balancing the work order. It acts as a calendar for equipment and asset care tasks. The application tool will send reminders to the appropriate technicians about the work schedule.
Auditing
The management database is very helpful for gathering and organizing information for auditing.
The inspectors can quickly determine whether the equipment care was carried out at the right time. This also helps to document regular details for further use.
Reporting & Analysis
The reports and analytics generated by the portal help managers and employees make wise decisions. Through maintenance reporting, managers can generate reports across various categories, such as asset availability, vendor assessments, material costs, etc. This structured reporting helps analyze operations effectively to support business decisions. Maintaining dashboards, audit logs, and operation reports plays a crucial role in overcoming the major challenges of operational management.
Where is CMMS used?
The solution is used to manage and assign routine tasks for operations and generate reports. Numerous industries use CMMS software solution to achieve their unique management requirements. Here are some of the major areas where it can be used:
Manufacturing, oil and gas, data & communication centers, farming, educational institutions, mining, ports, power plants, hospitals, sports arenas, stadiums, zoos, amusement parks, food industry, real estate, and government organizations.
The Key Users of CMMS
Let’s answer who uses a CMMS. Anyone who manages equipment or properties can use a computerized management portal to streamline operations and improve efficiency. These are key users inside the organization directly involved with the management solution.
1. Maintenance manager
The manager is the central user of the management solution. The manager and the system administrators are the people who use digital interfaces and heavily rely on the selection, implementation, and optimization of the solution. Using this service, they can create, manage and schedule work orders and assets, create reports, and so on.
2. Inventory manager
Inventory managers can use the information about the spare parts, equipment history, stocks, and quantity checks. By this, they can send purchase orders for the missing parts. The application leads to better inventory tracking so the team can get the right details at the right time. This supports the coordination between both departments and provides more accurate reports.
3. Operation manager
The operation managers must see the performance metrics and schedules across different equipment to improve efficiency, plan budgets, purchase inventory, and more.
4. Executives
Executives use the digital management program to know about the performance of the operations, KPIs, and challenges to decide for the organization’s success.
5. Technicians
They are the ones who use the platform and its features to complete operational tasks. Technicians need to view the work orders and schedules, add information about the completed assignments, and check asset profiles and other features related to the repair and operational process. This allows them to make their work efficient and accurate by adding real-time data.
6. Contractors
Sometimes, contractors can use the tool to view work orders, task lists, and other operational resources to complete the tasks.
7. Health and safety manager
Health and safety are significant for workers to avoid accidents and safety compliance. The policies, checklists, certificates, and audit results give the ability to put health and safety information in a centralized network. This ensures the safety of the workers and the organization.
8. Reliability managers
These are the people who work for the standard improvement of the company. They need to collect the data from the application and turn it into actions. It allows them to access all the necessary data, run reports and analytics, and create processes to reduce downtime and costs for repair and enhance efficiency.
9. IT department
The IT teams take care of the digital medium of the company, including CMMS. They use it to monitor integrations, updates, security risks, and data storage to ensure the company follows proper methods.
10. Production workers
Machine operators, production line leaders, and supervisors use the digital platform for everyday use. This helps them to detect the sign of failure early before the breakdown occurs. They can submit the details about the work order and repair process.
With the availability of reasonably priced computerized management solutions, companies striving to achieve maximum return on investment, longevity, and efficiency for their equipment can use the portal.
Conclusion
Think of CMMS as your facility’s secret weapon for streamlined maintenance and operations. With this digital solution, you can bid farewell to tedious paperwork and guesswork.
It’s all about maximizing efficiency and minimizing downtime. This powerful tool allows you to track work orders, manage assets, and generate insightful reports.
The key here is understanding that a well-implemented application can transform your facility management game. By focusing on measurable outcomes like CMMS ROI, you can justify your investment while boosting operational efficiency. Take a proactive approach, stay ahead of tasks, and unlock the true potential of your operations. Embrace the management program, and watch your facility thrive.
If you need a CMMS that caters to your unique needs, connect with our team. Share your CMMS RFP (Request for Proposal) with us and we will carefully evaluate all your requirements. Based on your requirements, we will offer a custom CMMS product, which soon will fetch innumerable benefits of CMMS for your business.