How Can CMMS Reporting Improve Maintenance Management?
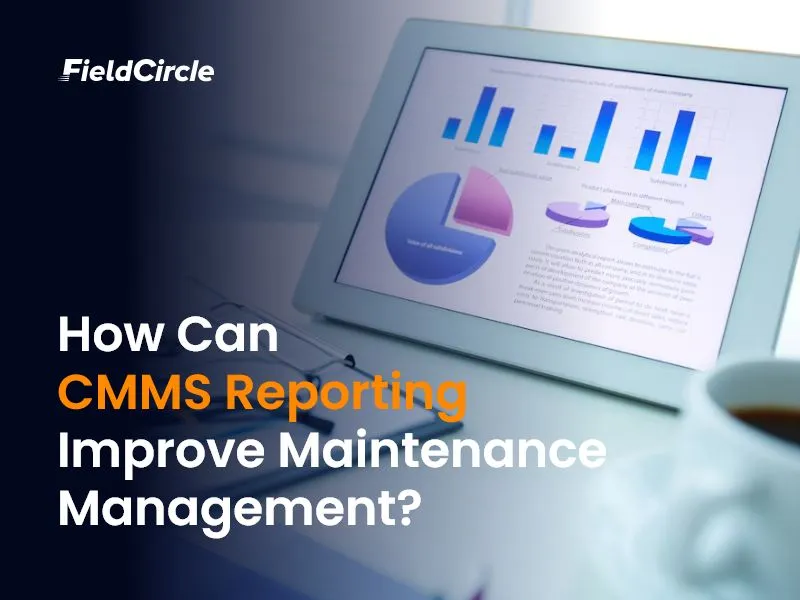
Capital equipment is undoubtedly the foundation of every asset-intensive industry. The manufacturing industry is expansive, spanning from food and beverage to computers and electronics, electrical equipment, fabricated metals, and transportation equipment, which are extensively equipment-reliant. Organizations are hence turning to Computerized Maintenance Management Systems (CMMS) for reliability, enhancing their maintenance procedures, and upholding the prime condition of their machinery amidst the challenges of equipment downtime, regulatory compliance, and resource optimization. However, it is not merely the implementation of CMMS that revolutionizes maintenance strategies; it’s the utilization of its robust reporting capabilities that truly empowers organizations to excel.
This shift towards technology is not just a trend but a proactive approach driven by a business’s desire to prolong the lifespan of its physical assets. It’s about enhancing availability and reliability and ensuring seamless operational continuity through cautious monitoring of critical assets. This is the essence of a maintenance management strategy, and it is what CMMS can help your business achieve.
A recent survey revealed that 88% of organizations delegate some or all of their maintenance operations, with the typical facility entrusting a third-party contractor with approximately 23% of their maintenance tasks. This underscores the significance of comprehensive visibility across all business operations when devising an effective strategy for equipment maintenance.
In this article, we will delve into how the adoption of a computerized maintenance management system (CMMS) reports can empower maintenance professionals, elevating their role in the organization’s maintenance management strategy and ultimately leading to optimal equipment performance. By automating scheduled maintenance tasks and meticulously tracking work orders, CMMS equips these professionals with the tools they need to efficiently manage their maintenance workflows and ensure the smooth functioning of operations.
Key Takeaways
Here are our key takeaways on CMMS Reporting
- Actionable Insights
- Optimized Maintenance Strategies
- Illuminate Operations
- Predictive Maintenance
- Improved Productivity
CMMS reporting and analytics provide maintenance managers with detailed data and insights into various aspects of maintenance operations. These insights include equipment performance metrics, maintenance costs, work order history, and inventory levels.
Leveraging CMMS reporting capabilities, maintenance managers can optimize their maintenance strategies based on historical data and performance trends. They can identify patterns of equipment failures, prioritize maintenance tasks, and allocate resources where they are most needed.
CMMS reporting provides insights on maintenance operations by providing clarity and insight into underlying issues. Utilizing CMMS reporting, managers gain visibility into maintenance performance metrics, allowing them to address problems proactively and prevent future issues.
One of the most valuable features of CMMS reporting is its ability to support predictive maintenance strategies. It analyzes historical maintenance data and equipment performance metrics, maintenance managers to identify patterns that indicate potential equipment failures.
CMMS reporting helps improve labor productivity by providing insights into work order status, technician performance, and time spent on maintenance tasks. Managers can identify bottlenecks in maintenance workflows, streamline processes, and allocate resources more effectively. Additionally, by optimizing inventory management strategies based on CMMS reports, managers ensure that technicians have access to the right parts and materials when needed, further enhancing productivity.
What is CMMS Report?
CMMS reporting refers to the process of capturing, storing, and analyzing maintenance data within a Computerized Maintenance Management System (CMMS) to enhance decision-making in maintenance management. It captures data related to maintenance activities such as work orders, equipment inspections, repairs, and preventive maintenance tasks. This data is then stored within the CMMS database, providing a centralized repository for all maintenance-related information.
CMMS reporting then analyses the collected data to extract meaningful insights that can inform decision-making. It further leverages advanced analytics tools, enabling maintenance managers to identify trends, patterns, and anomalies in maintenance data. This analysis enables proactive decision-making, such as predicting equipment failures, optimizing maintenance schedules, and allocating resources more effectively.
CMMS reporting transcends traditional maintenance reporting by offering real-time insights and data-driven decision-making capabilities. Unlike traditional reporting methods, which often rely on manual data entry and static reports, CMMS reporting provides dynamic, up-to-date information that reflects the current state of maintenance operations. This real-time visibility allows managers to respond quickly to changing conditions and make informed decisions based on the most recent data available.
Furthermore, CMMS reporting offers a diverse range of reports tailored to different aspects of maintenance management. These reports include, but are not limited to:
- Maintenance Work Orders – Reports that provide details about work orders, including their status, priority, assigned technicians, and completion times.
- Equipment History – Reports that track equipment’s maintenance history, including past repairs, inspections, and maintenance activities.
- Inventory Management – Reports that monitor inventory levels of spare parts and consumables, as well as tracking usage and reorder points.
Other types of reports may include asset performance reports, cost analysis reports, compliance reports, and labor productivity reports.
What are the benefits of CMMS Analytics and Reports?
CMMS analytics and reports offer a plethora of benefits to organizations in various industries. Here are some of the key advantages:
- Data-Driven Decision Making
- Optimized Maintenance Strategies
- Predictive Maintenance
- Cost Reduction
- Improved Compliance
- Enhanced Asset Performance
- Increased Productivity
CMMS analytics provide valuable insights into maintenance operations, allowing decision-makers to base their decisions on factual data rather than assumptions or guesswork. This leads to more informed and effective decision-making across all levels of the organization.
CMMS analytics analyze historical maintenance data and performance metrics. They help organizations identify patterns, trends, and areas for improvement in their maintenance processes. Hence, businesses can optimize maintenance strategies, prioritize tasks, and allocate resources more effectively, leading to improved equipment reliability and reduced downtime.
CMMS predictive maintenance strategies use analytics to anticipate equipment failures before they occur based on data analysis. The system identifies early warning signs of potential issues, enabling organizations to schedule maintenance activities proactively. This approach minimizes unplanned downtime and extends equipment lifespan.
Through detailed cost analysis reports, CMMS analytics help organizations identify opportunities for cost savings and optimization in their maintenance operations. This may include reducing unnecessary maintenance activities, optimizing inventory levels, and improving labor productivity, all of which contribute to lower maintenance costs and improved profitability.
CMMS analytics enable organizations to track and report on compliance with regulatory requirements, industry standards, and internal policies. It monitors key performance indicators and generates compliance reports. With the help of CMMS, organizations can ensure that maintenance activities are conducted in accordance with relevant regulations and standards, reducing the risk of fines, penalties, and legal liabilities.
CMMS analytics help organizations identify underperforming assets and take corrective actions to improve their reliability and efficiency by analyzing equipment performance metrics and maintenance history. This may involve adjusting maintenance schedules, implementing equipment upgrades, or replacing outdated assets, ultimately leading to enhanced asset performance and operational excellence.
CMMS analytics help organizations streamline maintenance workflows, reduce administrative overhead, and improve overall productivity. It automates routine tasks, provides real-time visibility into maintenance activities, and facilitates better resource allocation. CMMS analytics enable maintenance teams to work more efficiently and effectively, accomplishing more with fewer resources.
8 CMMS Reports To Improve Your Organization’s Maintenance Management
CMMS reporting provides valuable insights into the performance of an organization’s maintenance operations. Here are some of the most common types of reports that can be generated with CMMS software:
1. Equipment History Report
The Equipment History Report within a CMMS offers a detailed retrospective of equipment maintenance activities, encompassing repairs, inspections, and performance metrics. This maintenance software analyzes the collected data, allowing organizations to gain insights into the health and performance of their assets over time aiding in predictive maintenance initiatives, allowing for the anticipation of potential issues before they occur. Additionally, the report facilitates asset valuation and lifecycle cost analysis, assisting decision-makers in determining the optimal timing for equipment replacement or additional investments.
2. Maintenance Work Order Report
The Maintenance Work Order Report provides a comprehensive view of all maintenance work orders within an organization. It captures critical information such as work order statuses, technician assignments, time to completion, and recurring maintenance issues. Analyzing this data, helps maintenance managers improve maintenance scheduling activities, prioritize tasks effectively, and allocate resources efficiently. Key metrics such as completion rate, on-time completion, and backlog of maintenance work offer valuable insights into the performance of the maintenance team and the overall health of maintenance operations.
3. Inventory Management Report
The Inventory Management Report plays a crucial role in maintaining optimal levels of spare parts and materials required for maintenance activities. This report tracks inventory levels, usage patterns, and reorder points, helping organizations prevent stockouts, reduce carrying costs, and optimize inventory turnover. With the help of this report, businesses can also identify surplus inventory for potential liquidation, further streamlining inventory management processes. Effective inventory management directly impacts the overall maintenance budget and cost control, making it an essential aspect of maintenance management strategy.
4. Preventive Maintenance Report
The Preventive Maintenance Report supports organizations in planning and tracking preventive maintenance activities to ensure the reliability and longevity of their assets. This report monitors the business’s compliance with industry standards and tracks equipment uptime to help organizations identify opportunities for improvement in their preventive maintenance practices. Key metrics such as PM compliance rate and equipment uptime in this report offer valuable insights into the effectiveness of preventive maintenance efforts, guiding decision-makers in optimizing maintenance schedules and resource allocation.
5. Maintenance Cost Report
The Maintenance Cost Report provides a comprehensive view of all costs associated with maintenance activities, including labor, parts, and external services. This report analyzes all the collected data to aid organizations in identifying cost-saving opportunities, optimizing vendor negotiations, and improving process efficiencies. Crucial information such as maintenance cost per unit and total maintenance cost area are also included in this report, offering insights into the financial performance of maintenance operations, guiding budget control efforts, and strategic decision-making.
6. Labor Report
The Labor Report offers detailed insights into labor utilization and productivity within maintenance operations. It tracks hours worked, overtime, and productivity rates helping organizations optimize staffing levels, identify training needs, and balance workloads effectively. This report also helps to recognize high performers and address underperformance, thus promoting accountability and continuous improvement within the maintenance team.
7. Compliance Report
The Compliance Report ensures that maintenance activities meet regulatory and internal standards, reducing the risk of penalties or operational shutdowns. Leveraging CMMS compliance capabilities, organizations can efficiently track adherence to safety, environmental, and industry-specific regulations, enabling them to identify gaps and take corrective actions proactively. Key metrics such as compliance rate and audit readiness offer insights into the overall compliance posture of maintenance operations, guiding efforts to mitigate operational risks and maintain regulatory alignment.
8. Downtime Report
The Downtime Report focuses on minimizing downtime and ensuring operational continuity within maintenance operations so that organizations can identify opportunities for improvement in maintenance processes and equipment reliability. This report also helps monitor compliance with safety and environmental regulations, reducing the risk of penalties or operational disruptions.
Measuring KPI with CMMS Reporting
Measuring key performance indicators (KPIs) through CMMS reporting is integral to evaluating the success and efficiency of maintenance activities within an organization. CMMS reports offer valuable insights into metrics such as equipment uptime, analysis of downtime, and the percentage of planned versus unplanned downtime. Furthermore, it utilizes downtime data so that organizations can implement corrective actions to reduce unplanned downtime and enhance production efficiency.
Moreover, CMMS reporting enables the identification of patterns or trends in downtime, aiding in the recognition of problematic assets or processes. These insights justify investments in maintenance improvements or new equipment purchases.
Each type of CMMS report provides valuable data that can be used to measure specific KPIs related to maintenance management, helping organizations in the following ways:
- Enhanced Decision-Making—CMMS reporting enables informed decision-making regarding maintenance strategies and resource allocation by providing accurate and timely data.
- Improved Asset Reliability and Performance – Monitoring KPIs such as equipment uptime helps organizations optimize maintenance schedules and enhance asset reliability and performance.
- Cost Control and Optimization – Analysis of maintenance KPIs supports cost control efforts by identifying inefficiencies and optimizing resource utilization.
- Compliance and Safety – CMMS reporting ensures compliance with regulatory standards and enhances workplace safety by monitoring KPIs related to maintenance activities.
- Continuous Improvement—CMMS reporting tracks KPIs over time so that organizations can identify areas for improvement and implement continuous improvement initiatives to enhance overall maintenance effectiveness and efficiency.