How CMMS Streamlines Audits and Compliances in Maintenance Operations
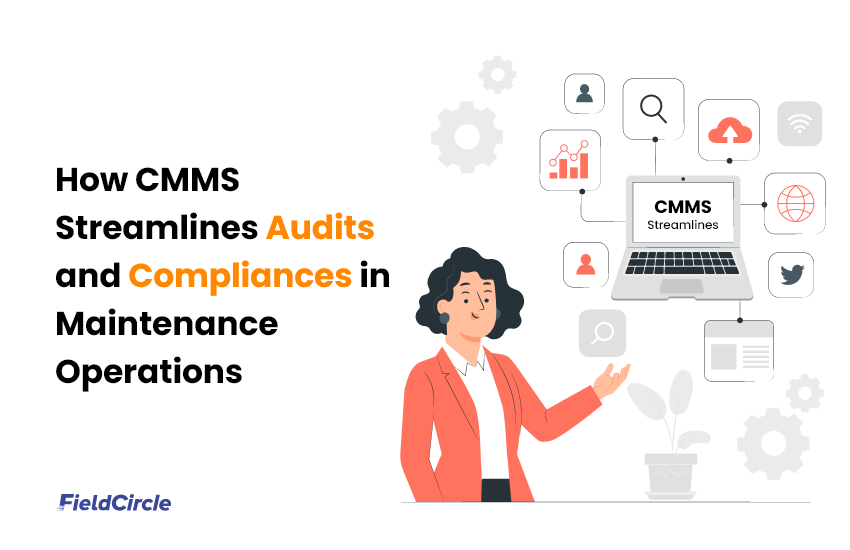
Maintenance operations have to work under the purview of safety standards, environmental concerns, or industry-specific guidelines, as decided by the law of the land and global standards.
Traditionally, audit procedures would be carried out manually, but this approach to maintenance management poses significant challenges in meeting compliance requirements. Characterized by spreadsheets, paperwork, and disjointed business processes, manual methods lead to inefficiencies and headaches for maintenance personnel.
Adopting a Computerized Maintenance Management System (CMMS) can prove to be a transformative move. By digitizing and organizing information, CMMS brings unprecedented efficiency to the maintenance process, reducing the complexity of and time required for managing compliances. And these are just some of the manifold benefits of CMMS for maintenance auditing.
We delve into the multifaceted ways in which a CMMS revolutionizes maintenance operations, unfolding its indispensable role in fostering compliance, as we touch upon, before that, certain important dimensions in maintenance compliance.
What Auditors Want to See in the Maintenance Process?
Executing maintenance tasks against established compliance criteria is a must for the comprehensive evaluation of operations. Keeping with this requirement, during audits and inspections of a maintenance process auditors typically look for the presence of:
- Well-documented maintenance procedures and schedules
- Industry-specific compliance standards
- Regulatory compliance with environmental and safety norms
- Competence documentation for maintenance personnel
- Version Control for documentation
- Methodical asset management and inventory control
- Effective Response plans for emergency situations
- Measurement and reporting of key performance indicators (KPIs)
21 CFR and its Importance in Maintenance Compliance
21 CFR, or Title 21 of the Code of Federal Regulations, is a set of regulations established by the Food and Drug Administration (FDA) that governs various aspects of the food, drug, and medical device industries.
Specifically, 21 CFR Part 11 focuses on requirements for electronic records and electronic signatures. It defines eSigns as legally binding equivalents to those of handwritten ones. Compliance with 21 CFR Part 11 is one essential criterion for maintenance operations in FDA-regulated industries, such as food and beverage, pharmaceuticals, medical devices, cosmetics, and tobacco products. Because, the prescribed norms make sure that electronic records, including maintenance schedules, work orders, and equipment calibration reports, are managed and stored in a manner that meets the regulatory requirements.
Any maintenance team must adhere to 21 CFR to ensure the safety of their operations and ensure efficacy of their processes. Compliance with these regulations establishes quality and safety standards for equipment used in production and maintenance. Adherence to 21 CFR can prove beneficial in preventing equipment failures that could otherwise compromise product integrity, stakeholder safety, and regulatory compliance. Further, non-compliance may lead to legal consequences, product recalls, and reputational damage.
By following 21 CFR guidelines, businesses can contribute to the overall reliability and quality of their operations, and succeed in meeting regulatory requirements.
Why adopting CMMS is a key step towards becoming compliant
Using a CMMS helps you manage your maintenance activities with utmost perfection. Apart from how it can be operationally beneficial, let’s see how a CMMS can help you adhere to regulations and compliances.
Strengthening the Safety Net
Possible risks associated with equipment and asset management include:
- Unsafe conditions or practices
- Non-identification of Periods during which equipment or assets are non-operational
- Unscheduled repairs or upkeep activities
- Non-tracking of asset performance in general and wear and tear of older assets in particular.
- Insufficient proactive upkeep
With a maintenance software you can effortlessly eliminate these risks. In fact, meeting safety compliances is one of the significant benefits of CMMS. It assists in assessing the likelihood of these risks and becomes pivotal in managing their potential impact. It achieves this through the utilization of risk matrices, which evaluate risk levels using both quantitative and qualitative data. Subsequently, CMMS prioritizes actions such as adjusting maintenance schedules, inspections, and workflows to mitigate the identified risks effectively.
A good CMMS will align with standard compliances, adhering to laws and regulations. It will quickly evaluate risks linked to equipment failure and safety hazards.
Telling of the Past and Present
CMMS software acts as a centralized repository for documents, which maintenance professionals can use and update using the version control feature that it provides. The centralized approach minimizes the risk of errors associated with manual document handling and promotes consistency in communication. In this way, it meets one stringent audit requirement.
CMMS also automatically enforces the documentation of regulatory compliance processes, aligning with the required norms.
As regards the role of the software in reporting, it offers built-in reports that teams can utilize in various ways to track if the processes are complying with prescribed standards and norms. These reports cover equipment status, status of work orders, labor, etc., providing a comprehensive overview of adherence to regulations. With FieldCircle CMMS, you can customize these reports and easily adapt to evolving compliance audit needs.
Building an Auditable Trail
Audit trail capabilities offered by CMMS can prove instrumental for enterprises in managing all maintenance audits. With granular details on alterations, CMMS makes the maintenance department accountable and transparent. It is with an automated logging feature that the software captures all updates on audit, which includes specifics on alterations, responsible individuals, and timestamps.
The detailed work order history, meeting the needs of organizations with multiple locations, provides thorough documentation essential for passing audits. Assisted with these capabilities, maintenance personnel can swiftly present detailed records to auditors and can efficiently address inspection requests in a satisfactory manner. Thus, a CMMS reduces liability and ascertains the integrity of its processes.
Streamlining operations with Inkless Efficiency
In industries governed by the FDA Title 21 CFR Part 11 standards, such as pharmaceuticals, medical, and food and beverage, CMMS proves quite useful as it streamlines the compliance process through electronic signatures, and provides a digital alternative to paper records.
CMMS helps maintenance personnel meet various compliances through electronic sign-offs on work orders. For instance, if a work order has to be closed, the permissions can be configured to mandate approval. A CMMS will provide a flow that would make electronic sign-offs on documentation mandatory for regulatory compliance.
As a CMMS provider, FieldCircle ensures that its CMMS adheres to the specific criteria outlined in CFR Part 11. These include the printed name of the signer, the date and time of the signature, and the associated meaning (if it was for approval or to indicate accountability). CMMS also streamlines the process which maintenance teams can otherwise find difficult and time-consuming. For instance, it will verify if electronic signatures are unique, assigned to verified individuals, certified by the signer, and secured with distinct identifiers, such as a username and password.
CMMS provides industry-specific benefits through electronic signatures. If we talk about medical device manufacturing, which is a highly regulated industry, CMMS simplifies the process of aligning with Current Good Manufacturing Practice (CGMP) standards that the FDA (Food and Drug Administration) applies. The software makes sure that written procedures are in accordance with the prescribed norms and comply with quality standards.
Enforcing Barrier Governance
Access Control, a key component of compliance frameworks such as ISO 27001 and regulatory standards like GDPR, is essential for safeguarding maintenance-related information. CMMS pitches in here, too, to comply with these standards and regulate access control.
CMMS platforms enable granular user access management, as it assigns specific roles and permissions to individuals based on their responsibilities. Using a combination of access control mechanisms, it grants authorization so that only permitted data is accessible to individuals. Through graded access and strict policies, it prevents unauthorized or inappropriate alterations that could lead to compliance violations.
To talk of FieldCircle CMMS, we integrate authentication mechanisms such as Single Sign-On (SSO) or multi-factor authentication (MFA) to ensure the utmost security of client maintenance data. By aligning with industry-specific compliance requirements, such as those in healthcare or finance, our CMMS minimizes the risk of data breaches and brings integrity in maintenance operations.
Perfecting Paraphernalia Performance
To prove compliance with standards such as ISO 9001, maintenance professionals have to demonstrate the equipment’s accuracy and reliability. For, calibrated equipment is a mark of operational excellence.
As we saw earlier, a CMMS maintains a centralized repository of equipment information, including calibration schedules and historical data. As calibration activities are consistently documented, maintenance personnel have the details about when a certain activity was undertaken at their fingertips.
Most importantly, CMMS automates calibration schedules and alerts, and there remains no risk of oversight or missed calibration deadlines, which minimizes the chances of non-compliance penalties. So, let’s say, if a piece of equipment requires calibration every six months, the CMMS can automatically generate work orders and notifications for the responsible personnel.
CMMS-generated reports and documentation around calibration serve as evidence during regulatory audits. They detail stakeholders involved in calibration activities, deviations, and corrective actions, and thus ensure a transparent and auditable trail of compliance.
Simplify your Audits By Meeting Compliances With FieldCircle CMMS
Implementing a CMMS stands as a strategic move for businesses aiming to improve compliance in their maintenance operations. Apart from arming with predictive and preventive maintenance capabilities, the software tool ensures that the teams are prepared for audits and inspections.
To understand how a CMMS solution can bring these manifold improvements in your compliance framework, you can schedule a demo of FieldCircle CMMS. We will guide you through the nuts and bolts of how it integrates with your processes and make sure that each of them adheres to prescribed regulations.