How to Build a Comprehensive Predictive Maintenance Program with a CMMS
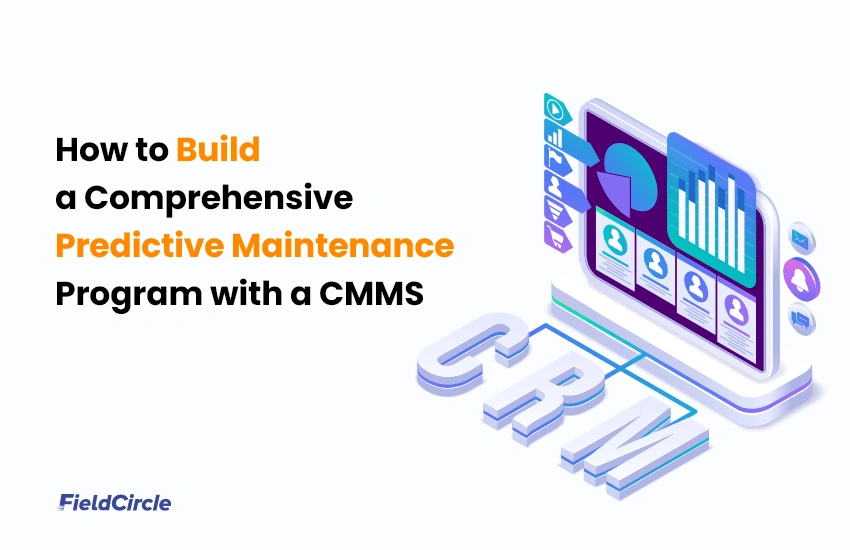
Unscheduled downtime remained a nemesis of productivity and profitability in maintenance operations, unless the idea of predictive maintenance (PdM) arose. To monitor equipment health and preemptively tackle issues before they escalate, enterprises are adopting PdM.
PdM is highly cost-effective as it can save organizations between 8% to 12% over preventive maintenance and up to 40% over reactive maintenance. The benefits extend beyond cost savings; predictive maintenance is a catalyst for increased productivity, as it can curtail breakdowns by a substantial 70% and reduce maintenance costs by 25%.
So, PdM acts as a resource spinner as it drives the improvement of equipment utilization and helps optimize resources. Its essence lies in a meticulous, multi-step process: monitoring equipment conditions, analyzing data to glean actionable insights, and acting in accordance with established policies.
The best way to develop and deploy a PdM strategy is to use a computerized maintenance management system (CMMS). This approach moves away from traditional, model-based time intervals for maintenance, instead opting for a need-based schedule determined by real-time conditions and performance metrics.
As you might be curious to create a predictive maintenance program with CMMS software, here are the steps that you must meticulously implement in order.
Approach to setup a Predictive Maintenance (PdM) program with a CMMS
Using CMMS-driven PdM is one of the best strategies to improve maintenance performance. You can use it as a potential lever to manage maintenance costs. While the benefits of predictive maintenance with CMMS are many, it’s also important to consider CMMS software cost when evaluating tools and building a scalable predictive maintenance strategy. Understanding both the value and investment will help you plan more effectively.
Develop a PdM plan with CMMS
Predictive maintenance planning demands a systematic approach to maximize asset reliability and asset performance while minimizing downtime and costs. The sole motive of this process is to streamline maintenance operations using predictive capabilities.
You would define how to
- Carry out the assessment of historical maintenance data to identify patterns and failure modes.
- Select appropriate predictive maintenance techniques, such as vibration analysis, thermal imaging, or oil analysis, tailored to the specific equipment.
- How the CMMS would be configured to integrate data from sensors and other monitoring devices.
- How real-time data would be used for condition monitoring.
- Which algorithms the system would use to analyze the data and predict potential equipment failures?
These predictions form the basis for the predictive maintenance plan, allowing organizations to schedule maintenance activities proactively, reducing the likelihood of unexpected breakdowns.
Business considerations play a crucial role in the planning process. Factors such as production schedules, equipment criticality, and budget constraints must be considered when determining the frequency and timing of maintenance tasks.
Build a team for PdM with CMMS
When building a team for PdM, the important step is to choose the team-building model that will align each team member’s skills with the overall goals. One good model to build a team is Bruce Tuckman’s Forming-Storming-Norming-Performing model, which bases the team formation on three important parameters viz. Stage, Goal, and Key Activities and Considerations. You can use the model to build a PdM team, as:
Stage | Goal | Key Activities and Considerations |
Forming | team |
|
Storming | Address conflicts and differing approaches |
|
Norming | Develop unity for effective collaboration |
|
Performing | Achieve optimal efficiency in maintenance |
|
Extract and Integrate data from CMMS
PdM starts from this stage when you start using the data from CMMS for monitoring equipment functioning and performance. There are two ways you can follow. First, you can extract the data from CMMS and take it through various stages to build your own predictive analytics models. Or you can use the predictive capabilities that your CMMS provides. Usually, a good CMMS provider will incorporate predictive functionalities considering your niche requirements. However, you may encounter the need to build custom models, as the maintenance needs may evolve with time. We discuss this further.
The process begins with a meticulous extraction of data from CMMS data, recognizing the system’s role as the repository for critical maintenance data, including equipment specifications, historical maintenance records, and real-time sensor data.
Then comes the integration phase that amalgamates CMMS data and creates a unified dataset poised for advanced analytics. Feature engineering further enhances the dataset, making it more suitable for deemed analysis. Then you conduct Exploratory Data Analysis (EDA) that brings out preliminary insights and helps identify patterns in maintenance data.
Finally, with a carefully selected predictive maintenance model, the dataset undergoes training and validation, ensuring its readiness for use.
Integrate CMMS with Decision-Making Systems
You would use CMMS to capture equipment parameters on a continuous basis, providing a live feed of operational conditions. This data can feed into the models you developed to make predictions such as equipment failure. By analyzing trends in real-time data, CMMS can predict when equipment is likely to require maintenance, which will be important in maximizing operational efficiency.
Progressively make each maintenance activity CMMS-driven so that you can streamline condition-based monitoring, track spare parts, and plan maintenance activities in advance. In a way by incorporating CMMS in the decision-making framework, you will adopt a proactive maintenance approach. It will allow for timely interventions before a breakdown, reducing unplanned downtime.
Update Continuously
Regularly updating the predictive analytics model is essential for adapting to evolving operational conditions and changes in equipment behavior. Incorporating algorithms for failure prediction based on the latest maintenance data helps refine the model’s understanding of failure patterns. The continuous learning process trains the model to stay relevant and effective in predicting potential issues.
Use new maintenance data to seek valuable insights into emerging failure patterns. For instance, your CMMS may use random forests for equipment failures, so it must get updated at periodic intervals or at a time when an unexpected failure occurs. Similarly, new data will improve the accuracy of K-Means clustering that can group components based on the nature of failure or the function they perform.
Use the inputs from CMMS for continuous monitoring
We discussed team building in the preceding part. The roles you will define in this phase will come into the picture now in the monitoring process. Each stakeholder will use CMMS capabilities at the defined level to aid in decision-making.
Maintenance technicians will obtain insights into processes and use them on a regular basis to ensure smooth maintenance operations. Managers will extend their analysis further, going into the resource usage and allocation budget. The maintenance head will dig deeper and examine the overall efficiency of the operations and will offer input to framing newer strategies. The performance data will allow the maintenance department to set condition monitors and predict equipment behavior. With these insights, it would be able to deploy an action plan to reduce downtime, improve equipment reliability, conduct vibration analysis, reduce equipment failure, and streamline routine maintenance.
In this process, the maintenance team will track various KPIs (key performance indicators) such as:
- The idea of CMMS integration for improving maintenance performance is gaining currency. Using it in your predictive maintenance program will heighten your maintenance standards. With it, organizations can seamlessly transition from reactive to proactive maintenance practices.
The CMMS provider you choose bridges the gap between your intent to use the tool and executing the predictive maintenance strategy. If you are keen on it, start a predictive maintenance program today with FieldCircle, so that you can reap several CMMS benefits, including improved asset reliability, reduced downtime, and cost savings.