CMMS Software Integration: Challenges, Mistakes, and Best Practices
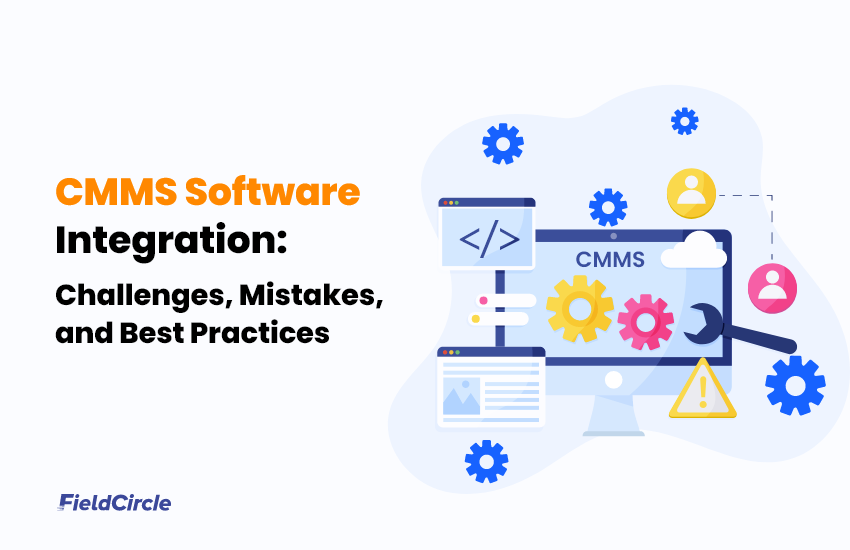
The importance of having the right tools and skills for a job is undeniable, and the same is true for CMMS software (Computerized Maintenance Management Systems) integration that helps organizations manage their maintenance tasks efficiently. CMMS software serves as a tool for effectively overseeing maintenance tasks within an organization. Its core functionalities encompass asset tracking, work order management, preventive maintenance scheduling, and inventory control.
Integrating CMMS software with other business systems, such as ERP (Enterprise Resource Planning) and SCADA (Supervisory Control and Data Acquisition), is a strategic move that can lead to significant efficiency gains. This integration enables real-time data exchange, which in turn improves decision-making and drives efficiency across maintenance operations.
However, despite its advantages, implementing the software at an enterprise level might not be simple. According to a publication by Medium, 70% of CMMS implementations fail often for the same reason. Organizations often underestimate the importance of proper planning and pre-implementation strategies when adopting new software, leading to unsuccessful CMMS adoption.
In this blog, we will, therefore, discuss the challenges associated with CMMS implementation along with the most common mistakes and best practices.
What is CMMS Software Integration?
CMMS Software Integration refers to the seamless connection between CMMS software and other business systems, such as ERP (Enterprise Resource Planning), SCADA (Supervisory Control and Data Acquisition), PLC (Programmable Logic Controller), and others. Its core purpose in modern maintenance management is to facilitate data sharing and process automation, ultimately enhancing the efficiency and effectiveness of maintenance operations.
The primary components and functionalities of CMMS software include:
- Asset Management – It tracks and manages assets throughout their lifecycle, including equipment, machinery, facilities, and infrastructure.
- Work Order Management – It creates, assigns, and tracks work orders for maintenance tasks, repairs, and inspections.
- Preventive Maintenance Scheduling – Plans and schedules routine maintenance activities to prevent equipment failures and downtime.
- Inventory Control – Manages inventory levels of spare parts, materials, and supplies required for maintenance tasks.
- Maintenance Analytics – Analyzes maintenance data to identify trends, optimize schedules, and improve maintenance processes.
- Data Synchronization
- Improved Visibility and Control
- Streamlined Processes
- Enhanced Reporting and Analytic
- Cost Savings
- Have you communicated CMMS implementation plans to executive leadership or the board?
- What percentage of maintenance processes will be mobile-accessible in your CMMS?
- Will you create a dedicated team or use the existing IT structure for CMMS integration?
- Are customer-facing CMMS modules web-enabled?
- Are vendor partners actively involved in CMMS integration?
- Have you assessed the timeline for CMMS integration?
- Have competitors integrated CMMS?
CMMS integration plays a critical role in streamlining maintenance operations and improving decision-making by providing comprehensive insights and enabling better coordination across various business functions. In other words, this integration involves establishing seamless connections between CMMS and other business systems. This integration allows for the exchange of data between different systems, enabling real-time information sharing and automation of processes. For example, integrating CMMS with ERP systems can ensure that maintenance activities are aligned with production schedules and financial workflows. Similarly, integration with SCADA or PLC systems enables direct access to equipment data for condition monitoring and predictive maintenance.
Understanding CMMS Needs and Objectives
Clearly defining needs and objectives before implementing a CMMS software integration is crucial for several reasons as follows:
1. Alignment with Business Goals
It ensures that the integration efforts are aligned with your organization’s broader goals and objectives. It will also clearly define what the organization aims to achieve through CMMS integration so that the integration process can be tailored to support these goals effectively.
2. Efficiency and Effectiveness
It helps in identifying specific pain points and challenges within the current maintenance management processes. This allows organizations to focus on integrating CMMS functionalities that directly address these challenges, leading to more efficient and effective maintenance operations.
3. Resource Allocation
Defining needs and objectives helps in determining the resources required for CMMS integration, including financial, technical, and human resources. It allows organizations to allocate resources effectively and ensure that the integration process stays within budget and timeline constraints.
4. Stakeholder Alignment
Clearly defined needs and objectives facilitate better communication and alignment among stakeholders involved in the integration process. It ensures that everyone understands the goals and expectations, reducing the likelihood of misunderstandings or conflicts during the implementation process.
5. Measurable Outcomes
Setting clear objectives enables organizations to measure the success of CMMS integration. By defining specific, measurable, achievable, relevant, and time-bound (SMART) objectives, organizations can track progress and evaluate the impact of integration on maintenance management processes and overall business performance. Establishing quantifiable metrics, such as percentage reduction in downtime or increase in equipment reliability, enables organizations to assess the effectiveness of integration on maintenance management processes and overall business performance. Additionally, SMART objectives ensure that integration goals are realistic and attainable within the constraints of resources, time, and capabilities.
Additionally, understanding the needs and objectives of the implementation is also essential for the successful integration of CMMS with other core business systems like ERP and SCADA, which play a critical role in enhancing the efficiency and effectiveness of maintenance management processes. Here are some reasons why:
Integration allows for seamless data exchange between CMMS and ERP/SCADA systems. This ensures that maintenance data, such as work orders, asset information, and inventory levels, are synchronized across all systems in real-time. As a result, maintenance teams have access to accurate and up-to-date information, enabling them to make informed decisions and respond promptly to maintenance needs.
Integration consolidates data from different systems to provide a unified view of maintenance operations. Maintenance managers can easily track assets, monitor equipment performance, and analyze maintenance trends across the organization. This enhanced visibility enables proactive maintenance planning and resource optimization, leading to improved asset reliability and reduced downtime.
Integrated systems streamline maintenance processes by automating tasks and workflows. For example, when a maintenance request is generated in the ERP system due to equipment failure, it can trigger an automatic work order creation in the CMMS system. This eliminates manual data entry and reduces the risk of errors, resulting in faster response times and increased operational efficiency.
Integration enables comprehensive reporting and analytics by combining maintenance data with other business metrics. Maintenance managers can generate custom reports and dashboards to track key performance indicators (KPIs), such as equipment uptime, maintenance costs, and compliance with regulatory standards. This insight allows for data-driven decision-making and continuous improvement of maintenance strategies.
By integrating CMMS with ERP systems, organizations can optimize inventory management and procurement processes. Maintenance teams can maintain optimal inventory levels, reduce stockouts, and minimize carrying costs. Additionally, integration helps in identifying cost-saving opportunities, such as predictive maintenance strategies and efficient resource allocation, ultimately leading to reduced maintenance expenses and improved profitability.
Benefits of CMMS Integration
CMMS integration offers a wide range of benefits, leveraging which integrated organizations can achieve operational excellence, reduce downtime, and drive continuous improvement in maintenance management practices. Here, we have listed some of the crucial benefits of CMMS integration:
1. Streamlined Processes
CMMS integration streamlines maintenance processes by connecting various systems across the organization. For example, integrating CMMS with ERP systems ensures that maintenance tasks are aligned with production schedules and financial workflows. Similarly, integration with SCADA systems allows maintenance teams to access equipment data for condition monitoring and predictive maintenance directly. The integration also minimizes manual efforts, reduces errors, and enhances overall process efficiency by automating tasks, facilitating data exchange, and improving communication between departments.
2. Enhanced Data Accuracy
Integrating CMMS with other business systems ensures real-time synchronization of data, leading to improved data accuracy and reliability. For instance, when a maintenance task is completed in the CMMS system, the updated information is automatically reflected in connected systems like ERP, ensuring consistency across the organization. This enables maintenance teams to make informed decisions based on up-to-date information, leading to better planning, scheduling, and execution of maintenance activities.
3. Improved Asset Management
CMMS integration enhances asset management by providing a centralized platform for tracking and managing assets throughout their lifecycle. Maintenance teams can more effectively monitor asset performance, track maintenance history, and schedule preventive maintenance tasks by integrating with asset tracking systems. This proactive approach helps identify potential issues before they escalate, extend asset lifespan, and minimize downtime, ultimately improving operational reliability and efficiency.
4. Optimized Inventory Control
Integration with inventory management systems enables real-time visibility into inventory levels, ensuring that maintenance teams have access to the right parts and supplies when needed. By maintaining optimal inventory levels, organizations can reduce stockouts, minimize carrying costs, and prevent disruptions to maintenance activities. Additionally, integration allows for automated inventory replenishment, ensuring that critical spare parts are replenished promptly to support maintenance operations.
5. Enhanced Reporting and Analytics
Integrated CMMS systems provide robust reporting and analytics capabilities, allowing organizations to track key performance indicators (KPIs), analyze maintenance trends, and identify areas for improvement. For example, maintenance managers can generate custom reports to track equipment uptime, maintenance costs, and compliance with regulatory standards. By leveraging actionable insights derived from data analysis, organizations can optimize maintenance strategies, allocate resources more effectively, and drive continuous improvement in maintenance operations.
6. Cost Savings
CMMS integration helps reduce maintenance costs through various means. It optimizes inventory control and aids organizations in minimizing carrying costs and reducing the risk of stockouts, resulting in cost savings. Proactive maintenance planning enabled by integration helps prevent costly breakdowns and extend asset lifespan, further reducing maintenance expenses. Additionally, improved operational efficiency and productivity achieved through streamlined processes and data-driven decision-making contribute to overall cost savings over time.
7. Compliance Adherence
Integration with regulatory compliance systems ensures that maintenance activities are aligned with industry standards and regulatory requirements. For example, integration with safety management systems allows organizations to track and manage safety-related maintenance tasks, ensuring compliance with safety regulations. Similarly, integration with environmental management systems enables organizations to monitor and report on environmental impacts of maintenance activities, ensuring compliance with environmental regulations. Organizations can mitigate risks, avoid penalties, and uphold their reputation in the industry by being compliant with legal and safety standards.
What Are The Challenges In CMMS Implementation?
Implementing a CMMS (Computerized Maintenance Management System) can be a complex process, and several challenges may arise during implementation. Here are some common challenges:
1. Migrating Data while Sticking to Accuracy
Migrating data from legacy systems to the new CMMS can be a complex task. For example, if the legacy data is inconsistent or contains errors, it may require extensive cleaning and standardization before it can be migrated. Additionally, mapping data fields from the old system to the new one requires careful planning to ensure that all relevant information is transferred accurately. Failure to maintain data accuracy during migration can result in incorrect or incomplete information in the CMMS, which can undermine its usefulness and reliability.
2. Ensuring System Compatibility at Each Stage
Integrating the CMMS with existing systems and technologies across the organization can be challenging. For instance, if the CMMS is not compatible with other software platforms or versions used within the organization, it may require custom integration solutions or middleware to facilitate data exchange. Ensuring compatibility at each stage of the integration process is essential to prevent data silos and ensure smooth communication between systems.
3. Identifying All Training Needs Before Integrating
Adequate training is crucial for users to utilize the CMMS effectively. For example, maintenance technicians may require training on how to create and manage work orders, while supervisors may need training on generating reports and analyzing maintenance data. Identifying all training needs beforehand ensures that users are equipped with the necessary skills to maximize the benefits of the CMMS and minimize the learning curve during implementation.
4. Process Integration
Integrating the CMMS into existing maintenance processes requires careful alignment and coordination. For instance, if maintenance workflows are manual or paper-based, transitioning to a digital CMMS may require redesigning processes to leverage automation and digital capabilities. Process integration involves mapping existing workflows to the new system, identifying bottlenecks or inefficiencies, and redesigning processes as needed to optimize efficiency and effectiveness.
5. Workflow Redesign
Implementing a CMMS often involves redesigning maintenance workflows to maximize the benefits of the new system. For example, if maintenance tasks are currently managed reactively, transitioning to a preventive maintenance approach may require redesigning workflows to prioritize preventive tasks and schedule routine inspections. Workflow redesign may also involve redefining roles and responsibilities within the maintenance team to ensure smooth implementation and adoption of the CMMS.
6. Adjusting Your Legacy System
Transitioning from legacy systems to a new CMMS can pose challenges, particularly if the legacy system is deeply ingrained in organizational processes. For instance, if employees are accustomed to using spreadsheets or paper-based forms for maintenance tracking, transitioning to a digital CMMS may require overcoming resistance to change and providing adequate support and training to facilitate adoption. Adjusting or retiring legacy systems may also involve migrating historical data and ensuring continuity of operations during the transition period.
7. Developing Change Readiness
Implementing a CMMS represents a significant change for the organization, and ensuring change readiness among stakeholders is crucial for success. For example, if employees are resistant to change or skeptical about the new system’s benefits, it may hinder adoption and acceptance. Developing change readiness involves communicating the new system’s benefits, addressing concerns or resistance, and fostering a culture of adaptability and continuous improvement to ensure a smooth transition and maximize the CMMS’s benefits.
What are the Possible Mistakes in CMMS software integration?
CMMS integration is susceptible to various mistakes that maintenance teams can commit. These can turn into operational hardships and long-term issues. As a result, for successful CMMS integration, steer clear of the mistakes discussed below:
1. Insufficient Planning and Preparation
When you rush into CMMS integration without thorough planning and preparation, you risk encountering various issues. For instance, inadequate stakeholder engagement means key voices might not be heard, unclear objectives can lead to confusion and misalignment, and a lack of a detailed implementation plan might result in oversights and missed opportunities for optimization. Without comprehensive planning, your organization may face delays, unexpected costs, and suboptimal outcomes that hinder the effectiveness of the CMMS.
2. Inadequate Data Migration and Validation
Neglecting proper data migration and validation during CMMS integration can result in significant problems for your organization. If you fail to clean, standardize, and validate data from legacy systems before migration, you risk introducing errors, inconsistencies, and data integrity issues into the new system. This can lead to unreliable information, incorrect analysis, and compromised decision-making, eventually undermining the value of the CMMS for managing maintenance activities effectively.
3.Ignoring System Compatibility
When you overlook system compatibility during CMMS integration, you set yourself up for integration challenges and inefficiencies. For example, incompatible software platforms or versions may hinder smooth data exchange and interoperability between systems, resulting in fragmented data and manual workarounds. Ignoring compatibility can limit the functionality and usability of the CMMS, making it harder for your teams to streamline maintenance processes and achieve desired outcomes efficiently.
4. Sidelining Regulatory Compliance
Failing to prioritize regulatory compliance during CMMS integration exposes you to significant risks. Overlooking compliance requirements related to data security, privacy, and reporting can lead to legal penalties, reputational damage, and operational disruptions. By sidestepping compliance considerations, you may also miss opportunities to enhance data governance, mitigate risks, and ensure accountability in maintenance operations, jeopardizing your organization’s credibility and sustainability.
5. Overlooking Asset Prioritization
Neglecting to prioritize assets appropriately during CMMS integration can have detrimental effects on your maintenance operations. If your maintenance management team fail to identify and prioritize critical assets based on their importance to operations and reliability, you risk allocating resources ineffectively and increasing the likelihood of downtime. Overlooking asset prioritization may result in missed opportunities to optimize maintenance strategies, improve asset performance, and maximize the return on investment in the CMMS.
6. Not Conducting a Pilot Phase
Skipping the pilot phase during CMMS integration deprives you of valuable insights and opportunities to address potential issues early on. By not testing system functionality, usability, and performance in a controlled environment, you risk encountering unexpected problems and resistance from users during full-scale deployment. Not conducting a pilot phase limits your team’s ability to validate assumptions, refine processes, and build confidence in the CMMS, increasing the likelihood of implementation challenges and dissatisfaction among stakeholders.
7. Overcomplicating the System
When you overcomplicate the CMMS system during integration, you create unnecessary complexity and barriers to adoption. For example, adding excessive features, customizations, or integrations can overwhelm users, increase implementation costs, and prolong the learning curve. Overcomplicating the system detracts from its intended purpose of simplifying maintenance management processes, making it harder for you to realize the full benefits of the CMMS and achieve your maintenance goals efficiently.
What are the best practices for the integration of Computer Maintenance Management Software?
The best practices we have suggested below can effectively integrate Computer Maintenance Management Software (CMMS) into your organization, optimize maintenance processes, and unleash the full benefits of the system.
1. Analyze Your Existing Systems
Conduct a comprehensive analysis of your current maintenance management systems, processes, and workflows. Identify all the systems involved in managing maintenance tasks, such as asset management software, work order systems, management tools. Evaluate the strengths and weaknesses of each system, and identify any gaps or inefficiencies in your current processes. This analysis will provide valuable insights into the specific challenges and requirements that CMMS integration needs to address, ensuring that the integration efforts are aligned with your organization’s goals and objectives.
2. Build a Coherent CMMS Integration Plan
Develop a detailed integration plan that outlines the objectives, scope, timeline, and resources required for CMMS integration. Clearly define the goals and desired outcomes of the integration process and break down the implementation into manageable tasks and milestones. Assign responsibilities to key stakeholders and establish clear communication channels to ensure coordination and collaboration throughout the integration process. A coherent integration plan will serve as a roadmap for the implementation, guiding decision-making and tracking progress toward achieving your integration goals.
3. Involve Every Stakeholder
Engage stakeholders from across the organization in the integration process to ensure their needs and perspectives are considered. Consult with maintenance teams, IT staff, department heads, and end-users to gather input and feedback on their requirements and expectations for CMMS integration. Solicit buy-in and support from stakeholders by clearly communicating the benefits and value of the CMMS and addressing any concerns or objections they may have. Involving stakeholders early on fosters a sense of ownership and commitment to the success of the integration project, increasing the likelihood of adoption and user satisfaction.
4. Adopt a Phased Approach to Integration
Implement CMMS integration in phases to minimize disruption to operations and manage risks effectively. Prioritize integration tasks based on their complexity and criticality and sequence them in a logical order to ensure smooth progress. Start with low-risk, high-impact integration activities that deliver immediate benefits to users, such as basic asset tracking or work order management. Gradually introduce more advanced functionality and integrations as your organization becomes familiar with the CMMS and gains confidence in its capabilities. A phased approach allows you to iterate and refine your integration strategy based on feedback and lessons learned, ensuring a successful and sustainable implementation.
5. Give Thought to Scalability and Growth
Consider the long-term scalability and growth potential of your CMMS integration strategy. Choose a scalable CMMS solution that can accommodate increasing data volumes, users, and business requirements as your organization grows. Evaluate the scalability of the CMMS architecture, database infrastructure, and integration capabilities to ensure they can support future expansion and evolution. Plan for scalability by designing flexible integration workflows and data models that can easily adapt to changing business needs and technological advancements. By future-proofing your CMMS integration strategy, you can minimize the need for costly rework and upgrades down the line, and ensure that your investment in the CMMS delivers lasting value to your organization.
6. Go for Workflow-Level and Not Database-Level Integration
Focus on integrating CMMS at the workflow level rather than attempting to integrate databases directly. Understand the existing maintenance workflows within your organization and design CMMS workflows that align with these processes. Customize the CMMS to support your unique maintenance requirements, such as asset tracking, work order management, and preventive maintenance scheduling. Map out the flow of data and information between CMMS and other systems and implement integration points at key workflow touchpoints to facilitate seamless data exchange and communication. By integrating at the workflow level, you can ensure that the CMMS complements your existing processes and workflows rather than disrupting them and maximizes user adoption and acceptance.
7. Have a Process to Prevent Data Duplication
Implement robust processes and controls to prevent data duplication and ensure data consistency across systems. Establish data governance policies and standards to define data ownership, quality, and integrity requirements. Develop data validation rules and checks to enforce consistency and accuracy when transferring data between CMMS and other systems. Implement data synchronization mechanisms to keep data synchronized in real-time or on a scheduled basis, minimizing the risk of duplicate or conflicting information. Regularly monitor and audit data quality to identify and address any issues promptly and provide training and support to users to ensure they understand their roles and responsibilities in maintaining data integrity. By having a process to prevent data duplication, you can maintain the reliability and accuracy of your data and ensure that your CMMS integration delivers accurate and actionable information to support decision-making and drive business outcomes.
Conclusion
Implementing a successful CMMS can be a challenging process, but with effective implementation, it can become a powerful database of maintenance-related data. This data can be utilized to implement best practices and identify opportunities for improved efficiency. Good software is a critical component of your maintenance and reliability strategy, significantly enhancing organizational performance now and in the future. Therefore, before you collaborate to make CMMS a part of your operational system, consider these questions first:
If you start with answers to these questions and follow the best practices we discussed, keeping in mind the possible challenges and mistakes, be assured your CMMS integration project will be a success.
Seek consultation from our experts to integrate a CMMS into your business processes and align with your niche operational needs. As a CMMS provider, we will persistently assist you along the integration journey and guide your maintenance team until it develops expertise in its use.