CMMS Integration With ERP System: Benefits, Challenges, and Solutions
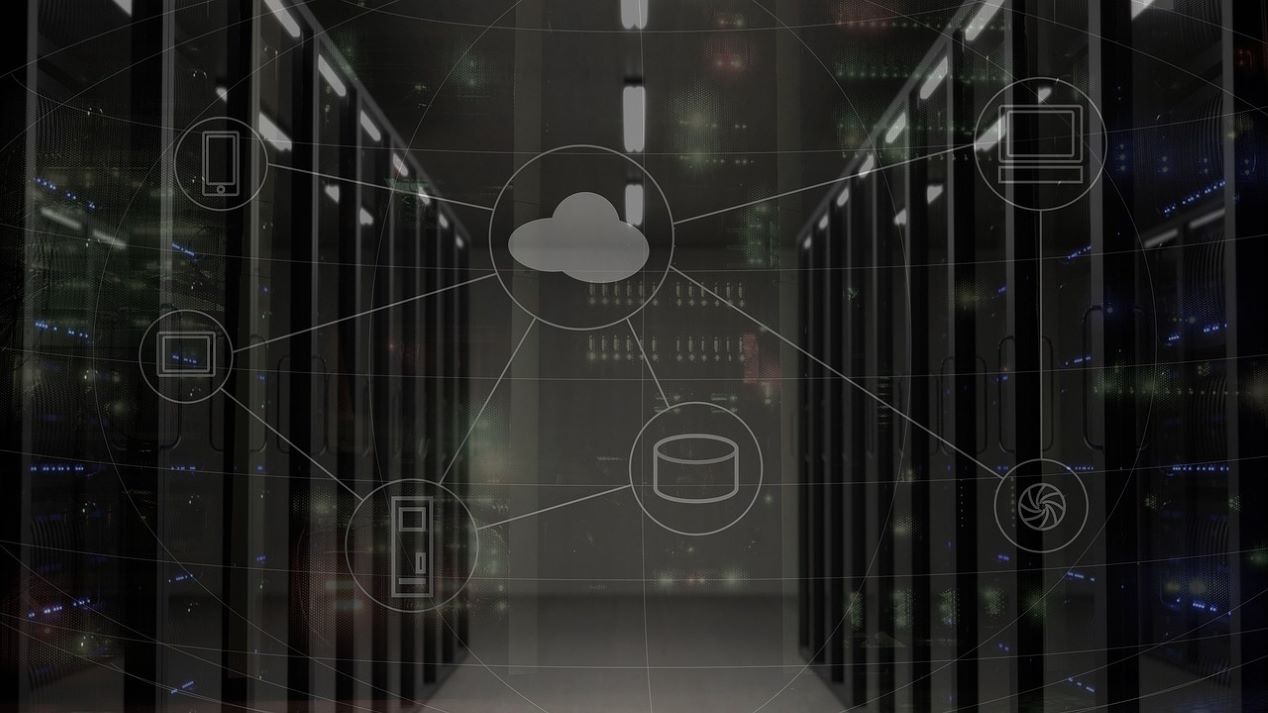
One of the essential queries that should be asked before making CMMS integration is, Is it valuable? Basically, integration is important for speeding up company procedures and making data analysis and reporting easier. To better understand your business processes, data can be shared and exchanged instantly and without delays between various software applications through integrations. First, what is CMMS integration?
CMMS integration is a process of enabling two or more software systems to communicate with one another by making shared data accessible to all systems and facilitating its exchange. Each system may read from or write to the other’s data during the data exchange. And without a doubt, the ERP system is the most crucial system to link CMMS software with.
Why Integration of CMMS and ERP?
CMMS and ERP systems are two different software programs that are designed to help manage a company’s business processes. CMMS stands for Computerized Maintenance Management System, and it is used for managing maintenance operations. It helps to track and manage the maintenance of assets and equipment in an organization, and streamlines maintenance activities. ERP stands for Enterprise Resource Planning and it is usually used to manage the entire scope of a business. It is a business management software that integrates all the business processes and data from various departments of a company.
Integration of CMMS with ERP is a way to improve the efficiency of your company’s maintenance operations, cut downtime and increase profit margins. It will also allow you to have more accurate records of your inventory, which can save you time when you need to order new items or find out what supplies you have in stock. Overall, effective integration holds the key to building a successful predictive maintenance program for the long-term.
If a CMMS software doesn’t work on accurate and up-to-date information, all of the investments made in its deployment and the overall business value it provides may be lost. The planning module of the computerized maintenance management system is a prime example, as it has the potential to significantly improve downtime optimization in production if implemented properly. However, if a CMMS maintenance software planning is based on inaccurate or out-of-date data, it will simply be erroneous. So it is necessary to integrate the computerized maintenance management system with ERP to get real-time data.
How smoothly does the CMMS and ERP Integration work?
CMMS and ERP integration is a process of linking the two systems together. This allows for seamless management of the changes that come from one system to the other. The two systems are linked through the use of workflows, which are automatic processes that trigger when specific events occur. The key is to make sure that the two systems communicate with one another and that all changes that happen in one system are reflected in the other.
At the time of CMMS integration, it is important to look at the integration process. How smoothly do the CMMS and ERP integration work? There are a few things to make sure of before you take the plunge. The first thing you need to make sure of is that your CMMS is compatible with your ERP. The next thing to make sure of is that you have the software and hardware to support the CMMS integration. The last thing to make sure of is that the integration team knows how to integrate the two systems.
The benefits of this integration are that it can reduce the time spent on data entry and increase efficiency in terms of workflow management. We will explore some of the challenges in CMMS and ERP integration.
When trying to integrate the CMMS and ERP systems, there are some challenges you need to overcome.
- How data is created and stored?
- How is it forwarded from one system to another?
- How is data managed?
- In which way the data is synchronized.
- How data is shared?
- And the last one is how data is accessed?
When you have a clear idea about these questions your integration will be smoother. Integration between CMMS and ERP can be seen as an investment, rather than an expense because it saves time and money in the long run.
What are the Benefits of CMMS integration with an ERP System?
Businesses can reap many benefits by integrating CMMS with ERP. For instance CMMS reporting improves maintenance management, and ERP brings the entire spectrum under a single umbrella. We dive into the important benefits, below.
Spare parts management
A faster spare parts inventory management procedure is the first and most unquestionable benefit that a CMMS/ERP software integration offers you. No longer do technicians need to double-enter spare part data or question its accuracy. To speed up operations, all crucial data is broadcast across the platforms.
Easier purchase orders
Each maintenance manager strives to speed up purchasing of a missing spare item. This could be a drawn-out, tedious process that involves multiple departments and calls for numerous approvals. A technician can easily speed up the process by designating a spare item as missing in the maintenance management software, which will then automatically generate, send, and notify all concerned employees of a purchase order in the enterprise resource planning software.
With computerized maintenance management systems and ERP integration, the management of purchase orders has become simpler than before. All you have to do is, create a purchase order in your CMMS software and transmit the data to the ERP as a purchase request. The integration will then sync the data automatically to update the pertinent quantities and cost data for simple inventory ordering.
Easy reporting and data accessibility
All employees now have access to a central information hub where they can use the knowledge necessary to make critical decisions thanks to the integration of asset management software and enterprise resource planning software.
Effectively manage historical data
Maintenance managers are aware of the data value in making choices. Data is used by managers to comprehend variables such as the typical response time and the number of open monthly work orders. But it might be challenging to obtain a full scope of data-backed information when distinct information is housed in separate systems.
A single reporting system with ERP and CMMS integration gives accessibility to all parties across departments. The management can access the facts they require to make executive choices about recruiting or budgets through this lone reporting point. The production team, meanwhile, can identify inefficiencies in technician productivity, information on asset downtime, and typical response times.
Improved internal communication
To maintain the smooth running of the organization, many departments interconnect. However, when trying to communicate with multiple systems, everything from research to accounting to production may suffer. ERP solutions make it possible for various divisions to efficiently communicate data about human resources, time management, and distribution planning. As a result of schedules, service statuses, and overtime hours recorded in the system, managers use a CMMS software to make decisions about scheduling technicians or backlogged repair orders.
Managers can use a single interface to make choices based on data from all departments by connecting the two. For instance, based on HR data, managers can immediately determine whether a technician qualifies for overtime and, if necessary, schedule someone for an emergency work order request. The numerous teams around the facility are more responsive as a result of improved data accessibility and the elimination of superfluous data.
Enhanced planning
In this scenario, managers and HR departments may accurately assess the competence of the technicians regardless of their educational background. They can accurately calculate the amount of time they have spent using any kind of equipment and the problems they have resolved. They can also remind staff members that they need to complete any required training or renew their licenses. Because of this, maintenance managers may better organize their team’s schedules and recruitment needs by using HR data. However, maintenance technicians are better able to comprehend their abilities, developments, and interventions.
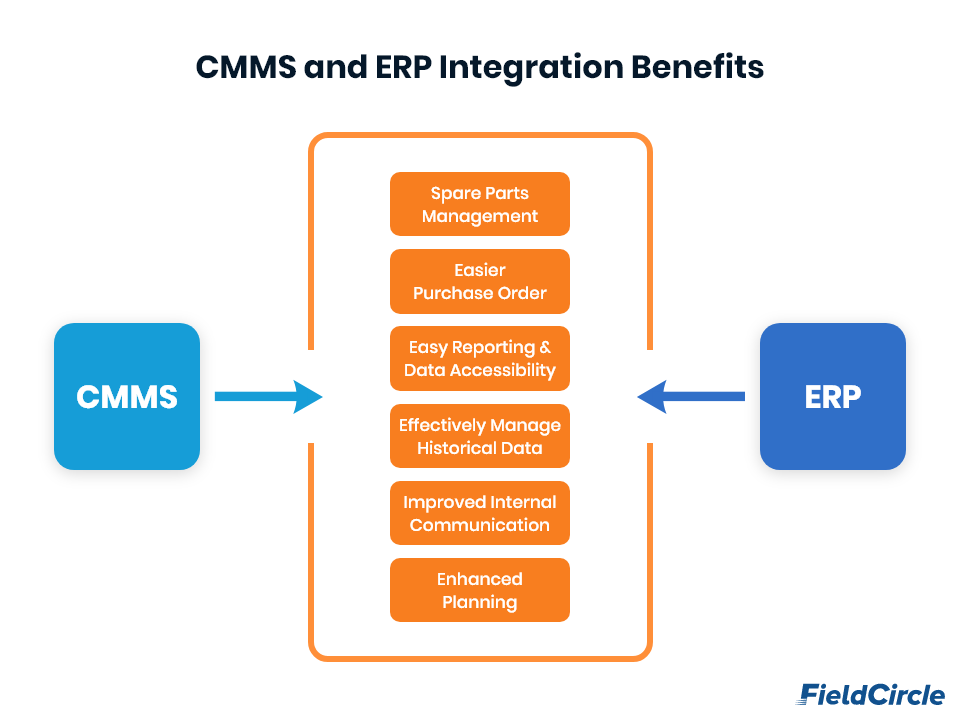
What are the Challenges in CMMS and ERP Integration and Their Solutions
Computerized Maintenance Management Systems (CMMS) integration with Enterprise Resource Planning (ERP) unfolds new possibilities of improvement, as we saw above. While the former focuses to bring transformation in maintenance, the latter is implemented with an objective of optimizing the supply chain management efforts. However, the integration between CMMS and ERP systems also comes with its share of obstacles. We take a closer look at these challenges that businesses may face and offer practical solutions to overcome them:
1. Data Standardization and Compatibility Issues
Integration becomes complicated when data structures between CMMS and ERP systems are misaligned. CMMS may utilize a more granular data model to track maintenance of equipment, while ERP systems operate on broader categorizations to manage enterprise-level functions.
The disparity can cause errors, misinterpretations, or even complete failures in syncing data. For instance, CMMS might log detailed preventive maintenance schedules, but if the ERP system doesn’t recognize such detail, financial forecasting or inventory management will be affected.
Solution:
Harmonizing data formats through middleware solutions or custom APIs proves effective. Additionally, mapping data points and agreeing on unified definitions during the planning phase averts these inconsistencies.
2. Conflicts During Real-Time Data Synchronization
Integrating systems to synchronize real-time data streams frequently leads to performance bottlenecks. Maintenance logs entered in CMMS, if not updated promptly in the ERP system, might lead to discrepancies in procurement or accounting records.
One such scenario is where delayed updates cause over-purchasing of spare parts and lead to the cascading consequences of such conflicts.
Solution:
Employing cloud-based synchronization tools with event-driven architectures resolves latency issues. Monitoring tools should also be deployed to detect and rectify synchronization errors before they proliferate.
3. Resistance in User Adoption
Even when technical aspects of integration are executed successfully, employees accustomed to standalone systems may resist adopting new changes where maintenance workflows get linked to ERP.
Maintenance teams working with CMMS might hesitate to engage with ERP-driven processes, perceiving them as time-consuming or irrelevant to their operations. This divide between operational and enterprise-level users disrupts integration benefits.
Solution:
Training programs tailored to highlight benefits for each team, coupled with regular feedback sessions, improve user confidence. Gamifying the learning process or incentivizing adoption also helps bridge workflow gaps.
4. Schema Inconsistencies
CMMS and ERP systems are built on distinct data architectures, which may lead to mismatches in data schemas. CMMS emphasizes specific data like maintenance history, equipment failure logs, and part-specific details.
In contrast, ERP systems aggregate high-level data such as asset cost, overall inventory, or depreciation schedules. A CMMS will store asset data using a unique identifier, while the ERP will use an entirely different naming convention or lack fields to store maintenance-specific metadata.
Solution:
Creating an intermediary layer, such as an Extract, Transform, Load (ETL) process, reconciles schema differences by reformatting, aggregating, or splitting data before synchronizing. A pre-deployment phase where both teams align on master data definitions avoids conflicts downstream.
5. Inadequate API Functionality
Most modern CMMS and ERP systems offer APIs for integration, but these APIs can lack the functionality to handle complex operations or data flows. So, a CMMS API might provide endpoints to retrieve work order data but omit critical fields like downtime analysis. ERP APIs might fail to accommodate dynamic updates needed for live inventory management.
One such scenario could be of a manufacturing plant trying to integrate its CMMS with ERP for inventory replenishment based on maintenance schedules. However, the API from the ERP system doesn’t support event-based triggers, leading to delays in ordering spare parts.
Solution:
Developing custom middleware that acts as an intelligent intermediary between CMMS and ERP allows the systems to communicate without relying entirely on native APIs. These middleware solutions introduce missing features such as event-driven triggers or advanced error handling.
6. Asset Hierarchy Misalignment
CMMS uses a detailed hierarchical structure for assets and tracks components within systems. ERP systems, on the other hand, treat assets as singular entities focused on financial and operational aspects.
A conflict arises when the CMMS reports maintenance needs for subcomponents, while the ERP lacks an equivalent field for such granularity. For instance, a CMMS flags a gearbox issue in a specific production machine, but the ERP logs data only at the machine level. Financial reports from the ERP overlook specific repair and maintenance costs, which ultimately leads to inaccurate budget allocations.
Solution:
Establish mapping rules between the CMMS hierarchy and ERP asset fields to properly consolidate granular data. For this, link subcomponents in CMMS to custom fields or tags in the ERP to maintain alignment.
7. Gap in Workflow Integration
CMMS and ERP systems operate on fundamentally different workflows. CMMS is task-oriented, focusing on maintenance work order management, technician assignment, and completion tracking of maintenance tasks. ERP systems prioritize enterprise-wide resource planning, which might conflict with the CMMS processes.
On the operational front, a maintenance manager uses the CMMS to issue an urgent work order, but the ERP flags it as unapproved due to budget constraints, which may delay repairs and escalate downtime.
Solution:
Introduce workflow orchestration tools that bridge CMMS and ERP approval processes and streamline maintenance task handling. Automate workflows to pre-approve maintenance actions for specific thresholds (e.g., costs under a pre-determined budget) and eliminate unnecessary delays.
8. Data Security Concerns in Cross-System Communication
Integrating CMMS and ERP creates a two-way data flow that must meet the security standards of both systems. Improper encryption, lack of secure authentication, or over-permissioned access introduces vulnerabilities.
Due to poor security measures, a CMMS user can gain access to ERP financial records due to improperly configured roles in the integration pipeline.
Solution:
Adopt secure communication protocols (OAuth 2.0 or SAML) for authentication and follow CMMS data security best practices. Role-based access control (RBAC) should be enforced at both systems, with regular audits of access logs for compliance.
Conclusion
The organization’s efficiency can be significantly improved by using an easy-to-use maintenance management program or a top-tier CMMS solution, which is extremely valuable not only from the perspectives of scale and efficiency but cost optimization as well. However, proper integration with enterprise systems, particularly ERP, will further improve the efficiency. Although it is technical, it requires many business decisions, and it is worthwhile to take and plan individually for a specific firm.
The advantages of CMMS integration will be proportional to how updated the information in the system is. As a result, we can only fully utilize the CMMS system’s capabilities if we consider and accurately map the processes in the environment.
And even if the entire concept might seem difficult to implement from a technical standpoint, many software solutions can address the issues at once, so it won’t be difficult. In order to attempt the initial question: Yes, it is valuable to integrate computerized maintenance management systems and ERP.