4 Types of Maintenance Strategies That You Must Adopt For Optimal Efficiency
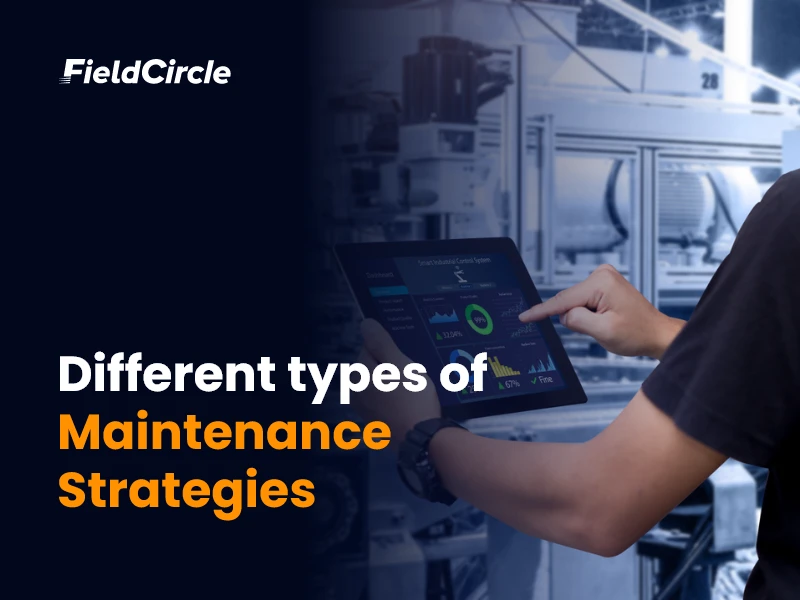
A structured approach to maintenance keeps assets in working order, prevents disruptions, and avoids excessive repair expenses. Depending on how equipment functions and how operations are structured, multiple maintenance strategies come into play.
Some businesses stick to preventive measures, conducting scheduled inspections and part replacements to reduce the risk of malfunction. Others take a predictive route, using real-time data and analytics to catch problems before they spiral out of control. Striking the right balance between maintenance costs and equipment availability determines operational efficiency.
Every approach has its strengths and weaknesses which makes it essential to weigh the options before locking in a strategy. Reactive maintenance, preventive maintenance, predictive maintenance, and corrective maintenance each serve a distinct purpose, and understanding their applications leads to smarter decision-making. The following sections break down these strategies and help understand their ideal use cases.
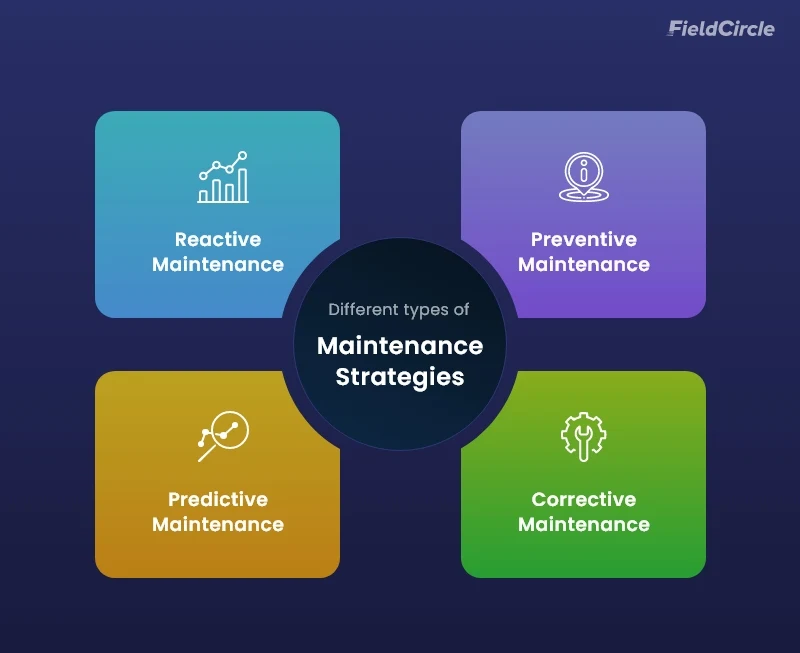
1. Reactive Maintenance
Reactive Maintenance, or breakdown maintenance, is a strategy in which maintenance is performed only after equipment or asset failure. It is used for non-critical assets where downtime has negligible impact and maintenance costs are low.
As an unstructured maintenance approach, this maintenance now is a thing of the past. Technicians fix equipment only after failures occur. The method was a default maintenance approach, where no other approach was available. Today, this approach is deliberately employed for non-critical tasks and suits industries relying on non-critical or easily replaceable equipment, such as light fixtures, small HVAC units, or non-essential machinery in environments where occasional breakdown minimizes production.
Key advantages of the reactive maintenance model are low maintenance costs, which avoid the upfront costs of scheduled maintenance, and simple implementation, which requires minimal planning or specialized tools. Other pros are immediate repairs for fixing or replacing the failed component for quick restoration and rapid functionality of affected equipment.
Meanwhile, the disadvantages include a high risk of unexpected disruptions and the potential for severe failures. However, it prolongs downtime and halts the production.
2. Preventive Maintenance
Also called scheduled maintenance, Preventive Maintenance refers to the maintenance strategy of performing regular inspections and maintenance tasks at predetermined intervals to prevent equipment failure, regardless of the asset’s condition. It includes routine checks for wear, damage, or performance issues, lubricating moving parts to reduce friction and wear, removing dirt, dust, or debris that may affect operations, fine-tuning equipment, and replacing consumable or aging parts before failure.
As a maintenance practice, preventive maintenance became prominent in the 20th century to combat the effects of machine wear and tear in industrial settings. Since it addresses potential issues early, preventive maintenance has become a staple in industries such as manufacturing, transportation, and facilities management. It suits assets with predictable wear patterns, such as conveyor belts, HVAC systems, and production machinery.
However, preventive maintenance involves regular inspections and servicing and requires higher maintenance costs. The challenge can be overcome easily by adopting a good preventive maintenance software which streamlines the process of implementing proactive maintenance strategies.
3. Predictive Maintenance
It is a data-driven strategy where equipment is monitored in real-time to predict failures and schedule maintenance at optimal times. It uses advanced techniques, such as IoT sensors, data analytics, and AI, to collect real-time vibration, temperature, and pressure data to analyze patterns and predict potential failures. Consequently, this proactive approach heavily depends on advanced technology, such as maintenance software, and expertise in data analysis.
Predictive maintenance is ideal for high-value, critical assets in sectors like aerospace, energy, and heavy equipment manufacturing, where even minor halt and delay impact massive operational and financial losses. It continuously tracks equipment performance, uses predictive algorithms to forecast issues, and plans interventions based on predicted needs.
By resolving issues before they impact operations, predictive maintenance helps minimize operational disruptions and streamline resource utilization. Predictive maintenance harnesses modern technologies to shift focus from traditional models to a condition-based maintenance, resource-efficient approach. By using a comprehensive maintenance application you can build a flawless predictive maintenance program and pave a way for long-term effectiveness.
4. Corrective Maintenance
Corrective Maintenance is fault-based maintenance that focuses on identifying and correcting potential issues before they result in equipment failure. Here the maintenance team inspects and monitors physical infrastructures to detect the root causes of faults, evaluate the extent of damage, and resolve or replace faulty components or parts before they become significant problems. It emphasizes continuous improvement and proactive actions to address faults, which are essential for quality control frameworks.
The fault-based maintenance is suitable for organizations in manufacturing and production settings where uptime and safety are crucial. It is common in systems where minimal downtime does not result in significant operational disruption and financial loss. This maintenance strategy strikes a balance between proactive strategies like preventive maintenance and reactive maintenance, providing an intermediate approach that proactively prevents issues while remaining responsive to emerging faults.
Corrective maintenance improves safety by minimizing the risk related to equipment malfunction and reduces long-term costs by helping avoid the higher costs associated with major failures and extended production halts. On the other hand, it demands skilled personnel for continuous monitoring, which increases operational complexity and requires significant initial investments. Corrective approaches also have higher immediate costs for emergency repairs and a high risk of repeated failures if the root causes are not accurately identified and resolved.
Steps to Develop an Effective Maintenance Strategy
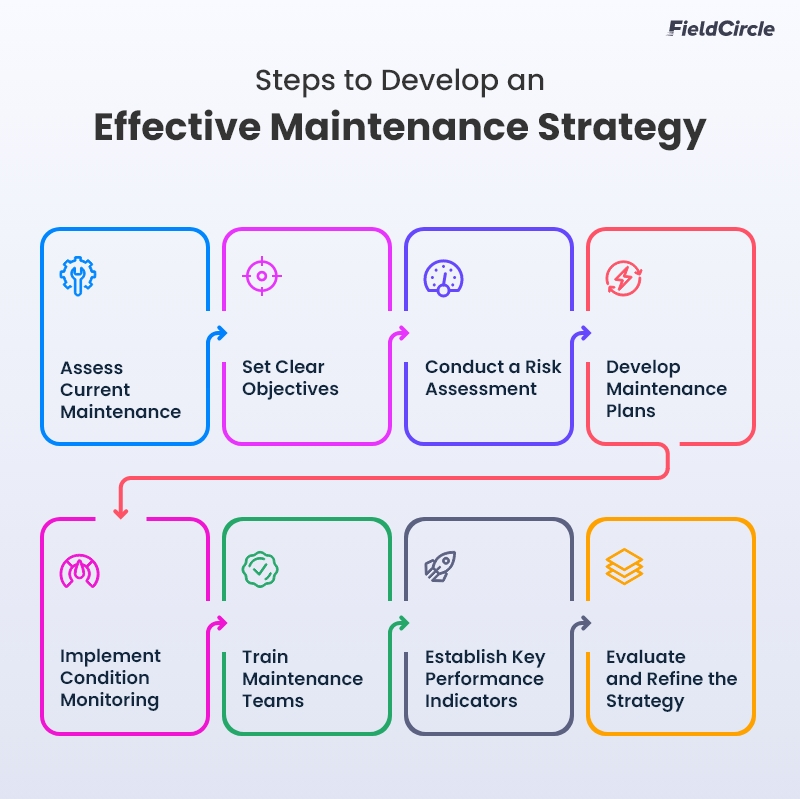
An effective maintenance strategy must offer optimal equipment performance while minimizing downtime and reducing maintenance costs.
Here are the 9 steps that organizations must follow to develop an effective maintenance strategy
- Assess Current Maintenance Practices
- Set Clear Objectives
- Conduct a Risk Assessment
- Develop Maintenance Plans
- Implement Condition Monitoring
- Train Maintenance Teams
- Establish Key Performance Indicators (KPIs)
- Implement a Maintenance Management System
- Evaluate and Refine the Strategy
Organizations should collect data related to equipment performance, failure rates, and costs and analyze past maintenance records to identify recurring issues and resource utilization patterns.
Organizations must set clear objectives and measurable goals to align the maintenance strategy with operational and business needs. It includes reducing downtime, optimizing resource utilization, minimizing maintenance costs, and more. Rather than keeping it vague, it must be clearly defined like ‘reducing downtime by 15% in 1 year’ or ‘minimizing maintenance costs by 20% in 6 months.
By conducting risk assessments, organizations identify critical assets and assess the risks associated with their failure. This is a critical step as it helps pinpoint assets with the highest operational impact and prioritize maintenance efforts effectively.
Maintenance teams must develop maintenance plans based on each asset’s criticality and operational requirements. The appropriate strategy can be predictive, preventive, reactive, or corrective maintenance. Organizations must create detailed schedules and standard operating procedures that address each asset’s unique needs.
Conduct a condition monitoring program by leveraging advanced technologies like sensors and IoT devices or conducting manual inspections to monitor the real-time health of critical assets. Incorporating real-time monitoring tools for predictive maintenance helps anticipate and prevent equipment failures.
Equip maintenance teams with the necessary skills and knowledge of new technologies, tools, maintenance practices, and safety protocols.Cross-training is important in maintenance as it builds a culture of proactiveness and continuous improvement.
Establish maintenance KPIs like Mean Time Between Failures (MTBF), Mean Time to Repair (MTTR), and Overall Equipment Effectiveness (OEE) to track the effectiveness of the maintenance strategy. Reviewing these metrics regularly allows organizations to monitor progress and identify improvement areas.
Implement a maintenance management system using a Computerized Maintenance Management System (CMMS) centralized maintenance data for seamless access and analysis. It automates maintenance scheduling, tracking, and reporting to streamline workflow, enhance efficiency, and enable informed decision-making.
Evaluate and refine the maintenance strategy in response to evolving operational demands and technological advancements to address gaps or inefficiencies and adapt the approach to meet changing requirements.
How to Choose the Right Maintenance Strategy?
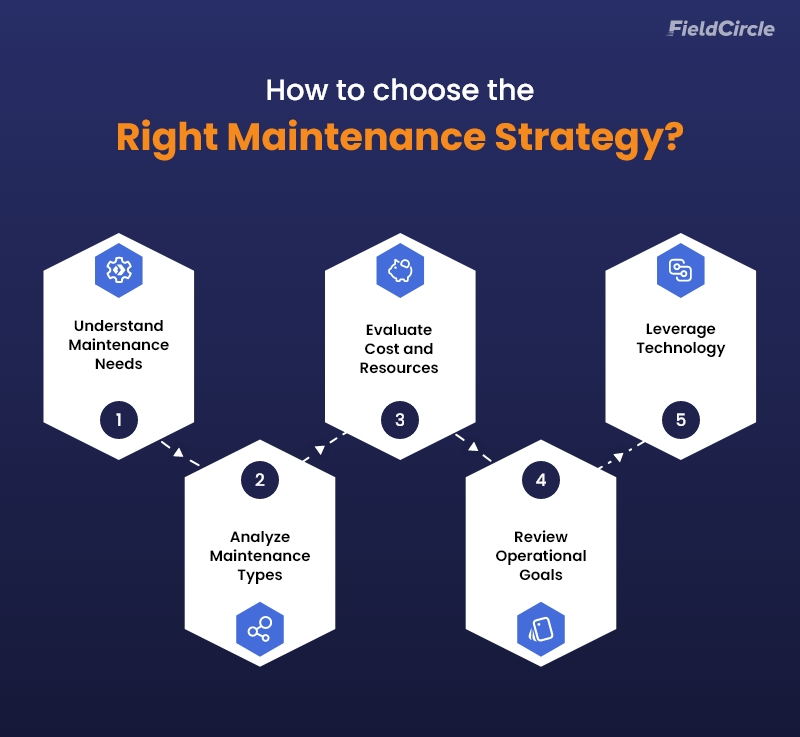
Choosing the right maintenance strategy requires a comprehensive understanding of asset criticality, failure patterns, available resources, and organizational goals. Aligning the chosen strategy with these factors and using modern technology allows businesses to optimize maintenance practices and streamline efficiency.
6 things to consider while choosing the right maintenance strategy are
- Understand Maintenance Needs
- Analyze maintenance Types
- Evaluate Cost and Resources
- Review Operational Goals
- Leverage Technology
- Measure Results
Consider each asset’s criticality, the impact of failure, and the operating environment. For example, assets with high safety or production significance need proactive care, while non-critical equipment can tolerate reactive maintenance.
Reactive maintenance is appropriate for low-priority assets, and predictive or preventive maintenance is best for critical systems. Knowing each strategy’s strengths and weaknesses lets you decide which aligns with your business goals.
Consider the initial investment in tools and training, ongoing maintenance costs, and the cost of equipment failure. Balancing these will help you find an effective and affordable plan.
Align your maintenance strategy with your organization’s broader goals, such as reducing production halts, compliance, and safety. How will the strategy contribute to productivity improvements, life cycle cost reduction, and long-term reliability so it supports your company’s purpose.
Tools such as IoT sensors, CMMS, and predictive analytics transform maintenance. These technologies allow real-time monitoring, data-driven decision-making, and scheduling, allowing you to predict and prevent failures and optimize resource use.
Track your key performance indicators (KPIs), such as MTBF, MTTR, and OEE, to see how the chosen strategy performs. Use these metrics to determine whether the strategy meets your operational goals and identify areas for improvement. Measuring results consistently will ensure that the strategy adapts to changing conditions and continues to deliver value.
Which is the Best Maintenance Strategy for your Business?
Choosing the right maintenance strategy depends on the specific needs and operational priorities of your industry. Below, we outline the best strategies for various industries and their applications, followed by commonly used approaches in different scenarios.
- Manufacturing: Preventive maintenance is the most effective for ensuring predictable performance and reducing unplanned downtime. It is ideal for managing equipment that requires consistent, reliable operation. Whereas, corrective maintenance addresses minor faults to maintain smooth workflows.
- Energy Sector: Predictive maintenance stands out for using real-time condition monitoring to prevent costly outages and optimize resource utilization. Condition-Based Maintenance (CBM) is a complementary approach for critical equipment that benefits from dynamic monitoring.
- Aerospace and Defense: Predictive maintenance ensures the safety and reliability of high-risk systems by identifying failure modes early. Also, corrective maintenance works as a backup to quickly address smaller, unexpected issues.
- Facilities Management: Preventive maintenance supports occupant safety and ensures the longevity of building systems through routine checks. Reactive maintenance is useful for non-critical components, such as lighting or small fixtures, where immediate repair isn’t essential.
- Automotive and Electronics: Corrective Maintenance efficiently addresses minor faults while keeping breakdowns minimal. On the other hand, reactive maintenance is a practical approach for managing low-priority failures or non-essential systems.
Which of these are Commonly Used Maintenance Strategies
- Preventive Maintenance: A cost-effective and straightforward approach to reducing unplanned production downtime. It is widely used in manufacturing, facilities management, and transportation sectors for maintaining consistent equipment performance.
- Predictive Maintenance: A proactive strategy that uses real-time data to predict and prevent failures. It is particularly suited for energy, aerospace, and heavy equipment manufacturing industries, where critical assets demand constant monitoring and timely intervention.