What is Preventive Maintenance Program: A Comprehensive Guide
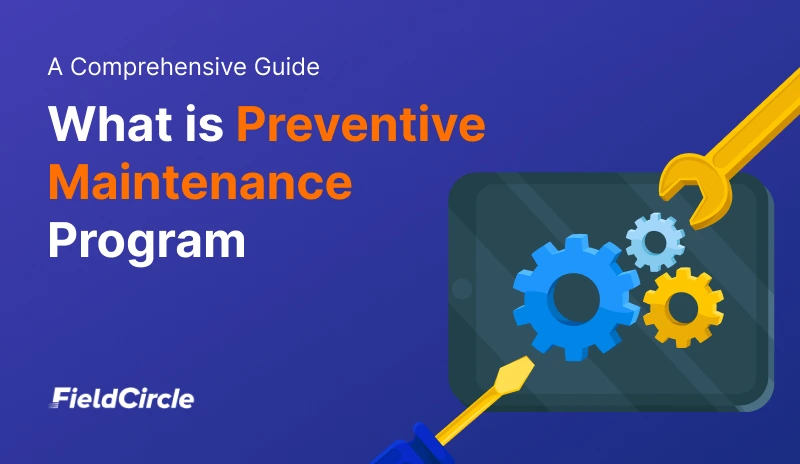
Preventive maintenance is a proactive approach to maintaining equipment and systems by performing regular inspections, servicing, and repairs to avoid unexpected failures. The phrase reflects a strategy aimed at ensuring machinery operates efficiently without the disruption of unplanned downtime.
Emerging in response to the high costs of reactive repairs, preventive maintenance gained prominence as industries sought to improve reliability and productivity during the mid-20th century.
The approach soon became a norm, especially in manufacturing, where operational efficiency is paramount. In fact, 88% of businesses in the manufacturing sector now prioritize preventive maintenance to avoid costly breakdowns and ensure smoother operations. Other industries, too, are following the suit.
Let’s dive into this comprehensive guide. What preventive maintenance entails, how it works, its various types, steps in building a preventive maintenance plan, the tools and technologies used to implement it, and its benefits and with this why it’s become a cornerstone of modern maintenance strategies
What is Preventive Maintenance
Preventive maintenance is a proactive approach to maintain equipment, systems, or infrastructure to ensure they operate efficiently and smoothly. It focuses on regularly scheduled inspections, servicing, and repairs aimed at keeping equipment and machinery in optimal working condition. Instead of waiting for breakdowns or malfunctions and addressing them later (reactive maintenance), maintenance tasks are planned in advance to identify and address potential issues before they escalate into major problems. Maintenance professionals attend to wear and tear well in time so that the complete equipment ecosystem continues to work uninterruptedly.
How Does Preventive Maintenance Work?
Preventive maintenance unfolds as a coordinated process that connects various stages through a unified approach. It relies on systematic steps to identify potential risks, schedule tasks, and carry out timely interventions, all aimed at maintaining equipment reliability. Each stage contributes to the overall goal by creating a cycle of consistent monitoring, execution, and evaluation. In this process, various tools and technologies such as preventive maintenance software play their part to maintain equipment and systems at their optimal performance levels. We discuss these elements in detail below.
Key Steps in Preventive Maintenance
A well-organized preventive maintenance process unfolds through a series of defined steps which are:
- Asset Inventory Analysis
- Schedule Development
- Task Assignment
- Execution
- Monitoring and Data Collection
The process begins with cataloging and analyzing all assets. Each piece of equipment is documented with its specifications, maintenance history, and operational role, which helps identify critical assets and their specific maintenance needs.
Based on the inventory analysis, a maintenance scheduling plan is created. Tasks are assigned specific intervals, such as daily, weekly, or monthly, depending on the asset’s usage and manufacturer recommendations.
Technicians are assigned specific tasks, ensuring the right expertise is applied. Clear instructions and guidelines are provided to make the process precise and efficient.
Technicians carry out scheduled tasks, which may include cleaning, lubricating, inspecting, or replacing parts. Procedures follow detailed steps outlined in standard operating protocols.
Sensors and manual inspections gather data during maintenance activities. The information is stored in a centralized system to track performance and refine future schedules.
Tools Used in Preventive Maintenance
To execute preventive maintenance effectively, organizations rely on a range of tools and technologies that support each step of the process. These tools are:
1. Computerized Maintenance Management Systems (CMMS)
A good CMMS platform will always be instrumental for managing schedules, assigning tasks, and maintaining records. They provide dashboards for monitoring progress and generating reports, streamlining the maintenance process.
2. Condition Monitoring Sensors
Real-time monitoring tools enhance precision in identifying issues:
- Vibration Sensors detect imbalances or misalignments in rotating machinery.
- Thermal Imaging Cameras identify overheating components.
- Ultrasonic Detectors locate leaks in pneumatic and hydraulic systems.
3. Diagnostic and Maintenance Tools
Technicians rely on various tools to execute tasks:
- Torque Wrenches for precise tightening.
- Laser Alignment Tools for calibrating mechanical components.
- Multimeters for testing electrical circuits.
Why is Preventive Maintenance Important
Preventive maintenance focuses on keeping systems operational and steps in before failures occur. So, it is a forward-thinking approach that helps businesses to maintain more stable and predictable operations, and spares them the inefficiency of constant disruptions.
We see how the approach is contrary to reactive maintenance which leaves organizations scrambling to fix breakdowns and leads to inconsistent operations and excessive costs. By regularly maintaining equipment, preventive maintenance avoids erratic spikes in repairs that reactive methods generate and which patch problems temporarily rather than addressing the root cause.
Types of Preventive Maintenance
There are 6 major types of preventive maintenance which are:
- Predictive maintenance
- Time-based maintenance
- Usage-based maintenance
- Condition-based maintenance
- Prescriptive maintenance
- Risk-based maintenance
Let’s dive into these different types of preventative maintenance that businesses can implement to improve operational efficiency and understand how each type serves a specific purpose, and addresses unique maintenance needs.
1. Predictive Maintenance (PdM)
Harnessing advanced analytics, predictive maintenance takes CBM a step further by forecasting potential failures before they occur. Using machine learning algorithms, historical data, and continuous condition monitoring, PdM predicts when equipment is likely to fail.
So, with PdM, you can plan maintenance activities in advance, minimize downtime and prolong the operational life of assets. It’s widely used in industries where equipment failure would be particularly costly, such as manufacturing or energy production. The sophistication of PdM means it often requires significant investment in predictive technologies and skilled personnel to interpret the data. You can build a predictive maintenance program with a CMMS configured to meet your needs.
2. Time-Based Maintenance (TBM)
Carrying out maintenance at predetermined intervals, time-based maintenance or calendar maintenance revolves around scheduling routine checkups regardless of the asset’s condition. Equipment is serviced periodically, whether it’s monthly, quarterly, or annually, depending on the manufacturer’s guidelines or organizational policies. One of the common examples of Time-Based maintenance is scheduled inspection of boilers or turbines in power plants.
TBM prevents issues that may not be immediately visible but could emerge from prolonged use, such as wear and tear. It is commonly used in environments where reliability of the machinery is important. Adhering to fixed schedules has its benefits as it reduces the likelihood of unexpected failures.
3. Usage-Based Maintenance (UBM)
Instead of relying on the passage of time, usage-based maintenance focuses on the actual utilization of an asset. Equipment maintenance is triggered by the amount of usage—such as hours in operation or number of cycles—rather than calendar days.
UBM works particularly well for machines that operate sporadically or the workloads of which vary significantly. Regular servicing is conducted after a set usage threshold is met, ensuring that maintenance aligns with how much the asset is being worked, which prevents the premature servicing that can be a drawback of time-based schedules.
4. Condition-Based Maintenance (CBM)
Condition-Based Maintenance is a type of maintenance that is performed only when specific indicators suggest that equipment performance is deteriorating. Condition-based maintenance is highly reliant on real-time data collection from sensors or manual inspections that track factors like temperature, vibration, or oil contamination. When these parameters deviate from acceptable ranges, action is taken.
As parts are replaced only when they show signs of wear or malfunction, CBM reduces unnecessary servicing while maximizing asset lifespan. It demands accurate monitoring tools and is typically applied to critical machinery where operational efficiency is key.
5. Prescriptive Maintenance
Prescriptive maintenance, also called action-oriented maintenance, builds on predictive strategies by not only anticipating failures but also suggesting specific measures to avoid them. It bases its decisions on insights gathered from the analysis of real-time data that the IoT ecosystem generates. Through these actionable insights, businesses can decide whether to repair, replace, or adjust a component. Prescriptive maintenance is highly beneficial in complex systems like power grids and aviation equipment.
The effectiveness of prescriptive maintenance depends on factors like data accuracy, smooth technology integration, and the sophistication of the equipment involved. While the initial investment in tools and systems can be high, the long-term benefits outweigh the costs. Its success hinges on combining the right technologies with a well-thought-out implementation strategy.
6. Risk-Based Maintenance (RBM)
Risk-based maintenance prioritizes assets for maintenance based on the level of risk they pose if they were to fail. Rather than treating all equipment equally, this approach evaluates the probability of failure and its potential impact on operations. High-risk assets—those that could cause major disruptions or safety hazards—are serviced more frequently, while low-risk ones may require less attention.
RBM is a type of maintenance where detailed risk assessments are performed, and factors such as asset criticality, operational environment, and historical failure rates are analyzed. It’s a strategic exercise which focuses on maintenance efforts where they’re needed most and thus optimizes resource allocation.
What are the Benefits of Preventive Maintenance?
Following are the benefits of preventive maintenance, which we further discuss in detail:
- Downtime reduction
- Extended asset lifespan
- Cost optimization
- Safety improvement
- Efficiency improvement
- Profitable budgeting
- Better resource mana
- Reliability enhancement
Let’s take a look at these notable gains that come when you implement a preventive maintenance program. They highlight how effective preventive maintenance provides greater control over system reliability and allows businesses to focus on growth without the worry of unforeseen complications.
1. Downtime Reduction
Preventive maintenance minimizes unexpected equipment failures by addressing potential issues before they occur, resulting in fewer unplanned shutdowns, keeping operations running smoothly. The ability to identify and rectify problems during scheduled maintenance allows companies to avoid the costly and time-consuming process of repairing breakdowns that could interrupt critical business functions.
2. Extended Asset Lifespan
Proactively addressing wear and tear through preventive maintenance keeps equipment in optimal working condition for longer periods. Routine maintenance checks and part replacements mitigate excessive deterioration, enabling machinery to operate efficiently beyond its expected lifespan. Eliminating the need for expensive replacements, it preserves the value of the investment.
3. Cost Savings
Regular maintenance reduces the likelihood of expensive emergency repairs or replacements by catching minor issues before they escalate into major problems. By investing in periodic servicing, businesses are able to significantly reduce long-term repair costs. Preventive maintenance is thus an economically sound strategy for maximizing asset performance without incurring large, unexpected expenses.
4. Safety Improvement
Preventive maintenance inspections and upkeep contribute to creating a safer work environment by reducing the risk of malfunctioning equipment that could lead to workplace accidents. Maintaining equipment at its best operating conditions helps in avoiding hazardous situations, protects employees from potential injuries and prevents liability issues related to safety breaches.
5. Efficiency Improvement
Well-maintained machinery operates more smoothly and with fewer interruptions, which is why more than 60% of businesses have been able to achieve higher productivity. Regular servicing optimizes performance, reduces energy consumption and extends the time between repair cycles. Consistent operational efficiency also enables the business to meet production targets more consistently, and leads to improvement in the overall performance.
6. Predictable Budgeting
When you use preventive maintenance strategies you can schedule and plan for maintenance costs rather than facing unpredictable repair bills. With a routine in place, financial forecasting becomes easier, and companies can allocate resources more efficiently without sudden disruptions from unexpected machinery breakdowns. Predictable costs help stabilize budgets and prevent financial strain.
7. Better Resource Management
Scheduling regular maintenance activities helps optimize the usage of both labor and equipment. By knowing when machinery will be offline, businesses can plan around these downtimes, maximizing the productivity of workers and minimizing idle time. When resources are allocated properly, it leads to smoother workflows and reduces the strain on maintenance personnel.
8. Reliability Enhancement
Consistent preventive maintenance makes equipment more dependable by keeping it in peak condition. With fewer unexpected breakdowns, machines operate consistently under various conditions, and improves the overall reliability of production processes. Reliability builds confidence in meeting operational demands, and reduces the risk of missed deadlines or production halts.
What are the Challenges of Preventive Maintenance?
Implementing preventive maintenance is fraught with some challenges. These are around:
- Equipment Age and Incompatibility
- Unforeseen Environmental Factors
- Lack of Organizational Buy-In
- Rapid Technological Obsolescence
- Over-Maintenance Risks
Unless and until managed rightly, these challenges can become difficult to tackle and result in significant roadblocks as we see below:
- Equipment Age and Incompatibility
- Unforeseen Environmental Factors
- Lack of Organizational Buy-In
- Rapid Technological Obsolescence
- Over-Maintenance Risks
Older equipment may not support the advanced monitoring technologies required for preventive maintenance. Retrofitting legacy systems to integrate with modern predictive tools is often impractical or extremely costly, leading to gaps in maintenance coverage.
External elements, such as extreme weather conditions, unpredictable operational environments, or sudden shifts in supply chain dynamics, can undermine even the best-laid maintenance plans. These factors often introduce variability that is difficult to predict or manage.
Resistance isn’t limited to frontline staff. Leadership or management might undervalue preventive maintenance, particularly in industries where short-term financial gains take precedence. The lack of support can cripple resource allocation and policy enforcement.
Preventive maintenance programs often depend on cutting-edge technology, but the rapid pace of technological change can render tools and systems obsolete before they deliver a return on investment. Balancing innovation with sustainability is a persistent challenge.
Ironically, excessive maintenance can lead to wear-and-tear, reduced operational life, or unnecessary downtime. Striking the perfect balance between proactive intervention and operational continuity requires a nuanced approach, which many organizations struggle to achieve.
What are the Future Trends in Preventive Maintenance
Following are the trends that are expected to evolve the way preventive maintenance is conducted, pushing beyond the technologies currently being implemented:
- Self -Healing Systems
- Digital Twins
- Blockchain
- Hyper-Automation
- Zero-Touch Models
- Sustainability
Maintenance professionals who want to create a preventive maintenance strategy for the long-term must incorporate these trends.
1. Self-Healing Systems
In the future, equipment could be designed with self-healing capabilities, where systems automatically detect wear or damage and repair themselves without human intervention. Advances in nanotechnology and material science could make this a reality, reducing the need for manual maintenance.
2. Digital Twins
While digital twins are already in use, future versions will be more sophisticated. Incorporating AI, future digital twins in maintenance could simulate real-time operational scenarios and predict not just maintenance needs but also how equipment might behave in various conditions, and optimize overall system performance.
3. Blockchain
Blockchain technology could emerge as a way to securely track and verify maintenance histories across equipment and fleets. The immutable record-keeping would increase transparency and trust in maintenance practices, especially in industries like aerospace, manufacturing, and heavy machinery.
4. Hyper-Automation
Combining AI, machine learning, robotic process automation (RPA), and other technologies, automation could take over maintenance significantly. Everything will be automated right from detecting potential failures to dispatching maintenance crews, managing inventories, and performing repairs autonomously.
5. Zero-Touch Models
The future may bring a “zero-touch” approach to preventive maintenance where intelligent machines perform maintenance checks and repairs entirely without human intervention. Such systems would rely on a mix of AI, robotics, and smart sensors, drastically reducing downtime and human error.
6. Sustainability
With a growing focus on sustainability, future maintenance strategies may prioritize energy-efficient operations and the reduction of waste in maintenance procedures. Equipment maintenance could be tied to environmental impact metrics, ensuring that machinery is not just operational but optimized for greener practices.
Areas of Preventive Maintenance
A comprehensive preventive maintenance plan covers the following maintenance activities:
- Equipment Maintenance
- Facility Maintenance
- Vehicle Maintenance
- IT Systems Maintenance
- Power Supply Maintenance
- Building Exterior Maintenance
- Energy Systems Maintenance
Let’s see how the upkeep of these elements results in smoother operations.
1. Equipment Maintenance
Regular cleaning and lubrication are the basic preventive maintenance tasks that keep the machinery operating smoothly. Inspections identify wear and tear early, while timely parts replacement helps extend the lifespan of equipment. By adhering to scheduled asset maintenance, organizations can reduce downtime and keep production lines running efficiently.
2. Facility Maintenance
Electrical systems, HVAC units, plumbing, and structural elements require continuous monitoring. Maintaining the health of these equipment is the goal of facility maintenance and inspections and servicing of these components prevent costly damage and outages. Focusing on the upkeep of infrastructure keeps a facility functioning safely and efficiently while supporting business operations.
3. Vehicle Maintenance
Routine inspections of engines, tires, brakes, and other critical components reduce the likelihood of mechanical failures. Adhering to manufacturer-specified maintenance schedules increases safety on the road, reduces wear, and prolongs the vehicle’s life cycle, making it reliable for long-term use.
4. IT Systems Maintenance
Regular updates and patches for software, operating systems, and hardware components are essential to prevent cyberattacks and system failures. Conducting routine backups and security checks helps minimize data loss and downtime, while monitoring system performance ensures that networks and servers run smoothly.
5. Power Supply Maintenance
Backup generators, batteries, and uninterruptible power supply (UPS) systems require regular testing to ensure that they will function correctly during power outages. Maintaining power systems reduces the risk of business disruptions and equipment damage due to sudden loss of electricity.
6. Building Exterior Maintenance
Roofs, windows, and exterior walls should be inspected for damage or leaks regularly. Preventing deterioration from weather conditions can help avoid costly repairs and structural issues that might disrupt operations or compromise safety.
7. Energy Systems Maintenance
Solar panels, wind turbines, and other energy-producing equipment require routine inspection and cleaning to ensure optimal energy output. Proper maintenance reduces the risk of energy inefficiency and costly repairs due to system malfunctions.
Checklist for Preventive Maintenance Program Implementation
Below, we’ve put together a detailed preventive maintenance checklist. Following these guidelines is essential to prolong equipment lifespan and reduce potential issues before they arise.
1. Inspect Equipment for Wear and Tear
- Look for any visible signs of damage, corrosion, or wear on mechanical parts.
- Check belts, gears, and bearings for proper alignment and tension.
2. Lubrication
- Ensure all moving parts are properly lubricated to reduce friction.
- Use manufacturer-recommended lubricants and adhere to specified intervals.
3. Test Electrical Connections
- Check all wiring, terminals, and electrical components for loose connections or damage.
- Inspect circuit breakers, fuses, and safety switches for proper functioning.
4. Clean Equipment and Surrounding Areas
- Remove dust, debris, and other contaminants that may interfere with equipment operation.
- Ensure air vents and filters are clear to prevent overheating.
5. Calibrate Instruments and Controls
- Regularly verify the accuracy of sensors, gauges, and meters.
- Adjust control settings to maintain optimal performance.
6. Check Safety Features
- Test emergency stop buttons and other safety devices.
- Inspect guards, shields, and warning labels to ensure they are in place and functional.
7. Replace Worn Components
- Proactively replace parts like filters, seals, and gaskets before failure occurs.
- Keep a log of replaced parts to track wear patterns.
8. Test Battery Systems
- Inspect battery connections, clean terminals, and check charge levels.
- Replace batteries as per the recommended cycle or if they show signs of deterioration.
9. Fluid Checks
- Verify fluid levels in equipment like hydraulic systems, coolants, and oils.
- Look for any leaks or contamination in the fluid reservoirs.
10. Software and Firmware Updates
- Ensure any computerized or digital equipment has up-to-date software and firmware.
- Backup important data before performing updates.
11. Verify Operational Performance
- Run a diagnostic test or performance check to ensure the equipment is operating at optimal levels.
- Listen for unusual noises or vibrations that may indicate underlying issues.
12. Review and Update Maintenance Logs
- As part of a preventive maintenance audit, it’s essential to document all maintenance tasks, noting any issues discovered and the corrective actions taken.
- Adjust the preventive maintenance schedule based on equipment performance data and manufacturer recommendations.
13. Check for Leaks
- Inspect hydraulic lines, valves, and pneumatic systems for leaks.
- Ensure seals and gaskets are intact in fluid-containing systems.
14. Check Environmental Conditions
- Monitor temperature, humidity, and ventilation around equipment that may be sensitive to environmental factors.
15. Inspect Alignment and Balance
- Check the alignment of rotating parts like shafts and pulleys to avoid excessive wear.
- Balance rotating equipment to prevent vibration damage.
Takeaway: Implement FieldCircle Preventive Maintenance Software
Implementing a preventive maintenance strategy becomes much simpler with the right software in place. Over 80% of companies have successfully streamlined their preventive maintenance work through a computerized maintenance management system (CMMS). By automating schedules, tracking asset performance, and reducing unexpected breakdowns, these systems revolutionize how businesses approach equipment upkeep.
A well-designed CMMS, such as FieldCircle CMMS, provides actionable insights that allow maintenance teams to shift from reactive to proactive maintenance. For organizations seeking to enhance reliability, minimize downtime, and improve efficiency, preventive maintenance software is an invaluable tool.