Robotics and Automation in Maintenance and Repair: A look at the Promising Future
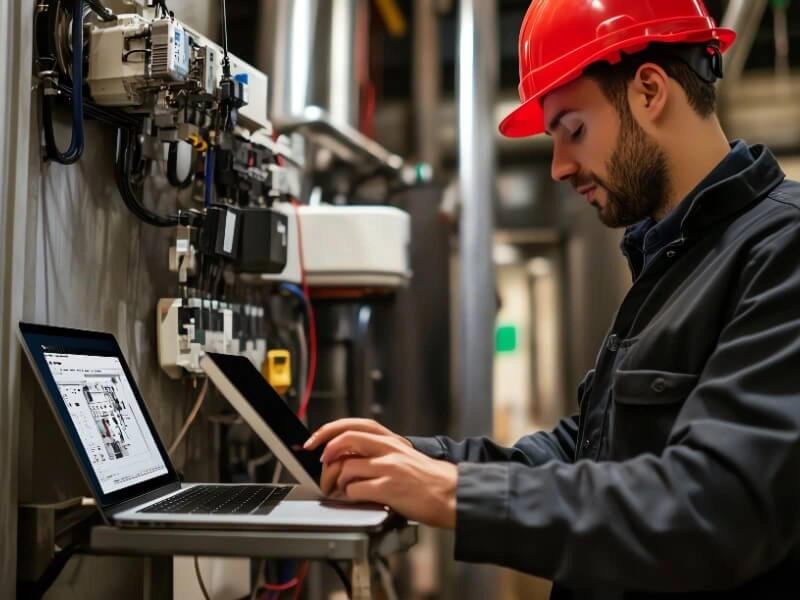
Robotics has been one favorite term in the business world for many years. But the recent developments in AI and machine learning have been propelling enterprises to pursue it more urgently. In areas like maintenance, where there are challenges beyond the scope of human capabilities, integration of robotics and automation offers an invaluable alternative.
Robotics: The Evolution
In the 1990s, pioneers like Stefano Nolfi employed genetic algorithms for autonomous refinement of physical structure and control strategies. Then Sergey Levine’s reinforcement learning studies showcased robots learning tasks through trial and error, adapting based on rewards. In industrial robotics, Peter Kopacek’s work on self-optimizing control strategies enhanced productivity and reduced energy consumption. Further, Marco Dorigo’s swarm robotics experiments highlighted collective adaptive behaviors. All these efforts culminated in the evolution of modern robotics that began surging, along with other many areas, in maintenance operations too.
Maintenance in new age: The move towards Robotics
The arrival of Artificial Intelligence (AI) into maintenance practices has given rise to a new era of predictive maintenance. This proactive maintenance strategy uses AI algorithms for analyzing vast datasets and offers excellent diagnostic measures, allowing for timely intervention.
Connected with these developments are Augmented Reality (AR) and Virtual Reality (VR). Enterprises are mulling the implementation of these technologies to obtain precise insights into the performance of their maintenance operations.
The evolution of robotic maintenance practices is linked with these advancements that are taking place rapidly. Currently, robotics in maintenance is not merely a futuristic concept but one of the key parts of the present. Its global market was valued at $4.23 billion in 2021. Remarkably, this figure is projected to surge to $10.05 billion by 2030 at the CAGR of 10.1% from 2022-2030. With 2.7 million robots in factories at present, the present state of robotics in maintenance mirrors an impressive deployment of robots.
Robotics: The promise
Understanding what robotics has to offer in the future is not just a matter of foresight but a necessity for maintenance professionals. The shift towards automation maintenance is more than a trend; it is a strategic move towards a future where maintenance is not just about fixing issues but optimizing maintenance activities with the assistance of cutting-edge robotic technologies. It is clear that robotics is steering maintenance into an era of unprecedented efficiency and will play an important role in the future.
Robotics Trends that will share the future of Maintenance and Repair
Emerging developments in robotics will allow robots to adapt to diverse tasks, diagnose issues autonomously, and optimize maintenance schedules. These cutting-edge robotic technologies that are evolving in form of:
Collaborative Robots (Cobots)
Collaborative robots, or cobots, will continue to gain popularity. These robots can work alongside human technicians, enhancing efficiency and safety. Cobots are designed to collaborate with humans in shared workspaces, helping in tasks that require precision or strength.
The dexterity and precision that cobots offer will make them invaluable for tasks such as fine-tuning delicate components or handling small parts that are challenging for human hands.
Cobots will continuously monitor equipment through sensors, detecting anomalies, and predicting potential failures with remarkable accuracy, thereby bringing transformation in predictive maintenance.
Additionally, as cobots can work in hazardous environments, from high temperatures to toxic substances, they will ensure safer maintenance practices. Cobots will also reduce downtime through swift and autonomous execution of routine tasks.
Swarm Robotics
Swarm robots excel in inspecting expansive areas and can perform repairs in complex cases, surpassing the efficiency of individual units. A concept currently under development, its implementation will improve the collaboration among robots allowing for simultaneous inspection and paving way for complex repairs.
As a collective approach, swarm robotics harnesses the power of distributed intelligences. With its synchronized teamwork, it presents a promising trajectory for optimizing equipment maintenance processes through enhanced speed, precision, and resource utilization.
Nano-Robotics for Microscopic Maintenance
Companies like Thermo Fisher Scientific are conducting research to take Nano-Robotics to the next stage. The results will be visible in maintenance, repair, and overhaul operations (MRO). These robots carry our maintenance processes at microscopic levels.
Their minuscule size allows access to confined spaces, ensuring thorough maintenance without disassembly. And so, they will improve the accuracy of detecting and rectifying faults with unparalleled accuracy. By operating at such a microscopic scale, Nano-Robotics will minimize the impact on surrounding components and optimize repair efficiency.
Self-Healing Materials and Robotic Patching
These robotics technologies enable autonomous identification and repair of minor damages. Specifically, self-healing materials possess intrinsic capabilities to mend structural flaws, which enhances durability.
Robotic patching systems, equipped with advanced sensors scan equipment surfaces, pinpointing issues. Then it applies patches precisely. Overall, the amalgamation of these two different robotic concepts offer a paradigm shift in maintenance which will usher in a proactive era for equipment repair and longevity.
Soft Robotics for Delicate Operations
Soft robotics are constructed with adaptable materials. Indeed, it is one of those robotics concepts that is set to revolutionize equipment maintenance. The lightweight and multifunctional nature of these robots, coupled with high elasticity and deformability, enables them to absorb energy and recover swiftly from physical impacts. This unique construction makes them ideal for delicate operations where precision is important.
In industries like aerospace, soft robots can streamline aircraft examinations, reducing maintenance time and enhancing adaptability to unpredictable space conditions. Their potential spans across industries, from electronics to medical applications, since they promise cost-effective and efficient maintenance.
Drone-based Maintenance Inspections
Companies like UPS are using drones to deliver spare parts to ground-based engineering crews at aviation hubs. Electric vertical take-off and landing (eVTOL) drones are already being employed for carrying out inspections and surveys of complex areas such as tanks, vessels, structures, and pipelines remotely. They can capture high-resolution images and videos, allowing for the detection of defects and damage in locations that are difficult for humans to access.
Likewise, drones are demonstrating their prowess in the inspection of confined spaces. This ability of drones to navigate isolated structures and confined spaces is making them particularly suitable for industries such as oil and gas, energy, and construction. So, drones are becoming an epitome of quick and efficient support.
Self-Optimizing Robotic Systems
Self-optimizing robots, rooted in cybernetics, have evolved through key research milestones. Recent applications, such as Pieter Abbeel’s deep reinforcement learning in robot locomotion, are opening new avenues in self-optimization. Such advancements indicate the potential of self-optimizing robots to autonomously enhance performance.
In time to come, these robots will be crucial for framing adaptive maintenance and repair strategies. They will make it easy to operate in dynamic and unpredictable environments, and help maintenance professionals to adjust strategies to changes in weather, equipment configurations, or the surrounding environment. Due to their versatility, they will perform optimally across varied conditions without compromising efficiency or precision.
Biological-Inspired Robotics
Bio-inspired robotics draw inspiration from nature and mimic the adaptability and problem-solving capabilities of living organisms. The development of a multifunctional robotic end-effector will turn out to be a significant leap in enhancing the efficiency of maintenance processes, particularly in hazardous underground mining environments. This has been highlighted in a research that shows how this robotic solution can automatically maintain reconfigurable vibrating screen (RVS) machines, and address the challenges of dangerous conditions.
This approach employs therblig and morphological methodologies to identify maintenance objectives and constraints. The resulting robotic end-effector integrates a worm-gear mechanism with hexagonal-shaped heads and an electric cylinder actuator module, performing functions such as gripping, ungrasping, loosening, bolting, unpinning, and hammering. The future paints a promising picture where bio-inspired robots will be important in industrial upkeep.
Underwater Robotics
Underwater robotics is transforming maintenance practices across industries, particularly in offshore oil and gas operations. These robots, also known as unmanned underwater vehicles (UUVs), are designed to operate underwater without the need for human intervention.
Particularly significant in the offshore oil and gas industry, these robots are expected to be extensively used for repair and maintenance in this sector along with its regular application in drilling. They are also employed for tasks such as underwater surveillance and environmental monitoring. The use of underwater robots in maintenance helps overcome the limitations of traditional methods and human divers, which is important especially from the viewpoint of improving safety.
Transform your Robotic Maintenance with a CMMS
The use of robotic technology is ushering in a new era of efficiency in maintenance, as the future speaks. And as robotics evolves, its application in equipment maintenance, diagnose and repair will undoubtedly redefine industrial efficiency and precision.
Integrating a Computerized Maintenance Management System (CMMS) is crucial in this paradigm shift. A CMMS enables a proactive approach, scheduling and automating routine maintenance tasks for robotic systems. As robotic maintenance are primarily chosen for their ability to work around the clock, it is with a CMMS that you can track if they are maintaining sustainable levels of performance.
Let our experts explain to you how you can get these long-term benefits through a FieldCircle CMMS software demo. Connect and know why you must rely on CMMS for adding value with robotics in your maintenance processes.