Maintenance in the Age of Automation: Challenges and Opportunities
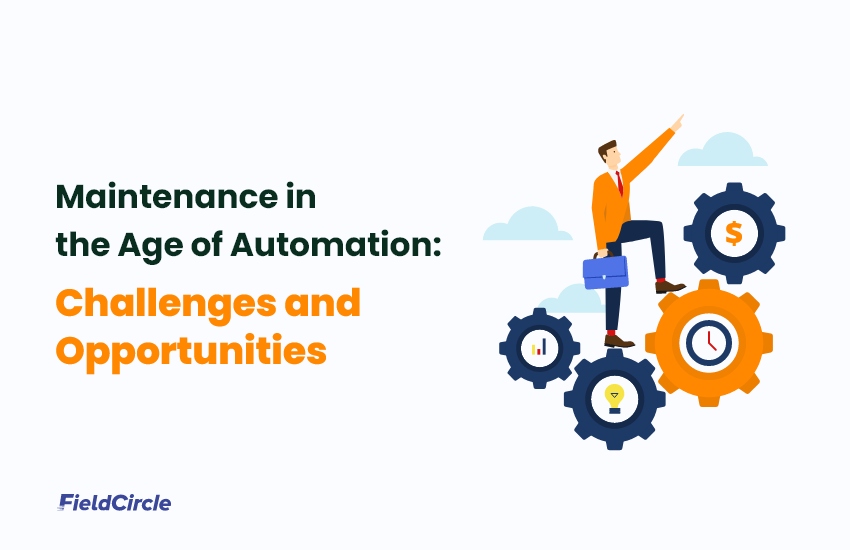
The arrival of the fourth industrial revolution has brought a new wave of transformation in maintenance. It has given way to Maintenance 4.0, a concept that heavily relies on automation.
For stalwarts such as Kone and Siemens, implementing automation for reengineering maintenance in their manufacturing processes and production system has been an ongoing journey. But it needn’t be the same for every enterprise, due to myriad challenges that automation brings.
By taking over the tough adoption process, enterprises can bring a massive transformation in their maintenance function. They can optimize the process of maintaining their complex systems and also augment human capabilities.
On one hand, there is an allure of using automation for building a state of the art maintenance framework, due to its potential benefits. On the other hand, maintenance leaders are aware of the fact that they must overcome barriers to secure advantages with automation in the Industry 4.0 environment.
Against this backdrop, we cover the challenges and opportunities that automation offers in maintenance and equip you with the readiness to strategically optimize your maintenance management systems.
What are the challenges in implementing automation in maintenance?
Automation is poised to change the way maintenance operations are conducted. But to achieve a breakthrough with it, you must overcome hurdles that lay in the path to its successful adoption. So, below we discuss major challenges that maintenance leaders typically encounter when implementing automation.
Building automation competence
The prospect of automation lures most maintenance professionals these days. However, the process requires investing significant resources (time and dollars) and efforts. You must assist your workforce in developing the necessary skills to effectively use and manage automated maintenance systems. You need dedicated support from specialized personnel, including automation engineers, artificial intelligence (AI), and data analysis experts.
From complex software and guidelines to a competent workforce, you need everything that an automation system requires. Apart from financial resources, you must build a culture of continuous learning, possible through regular training programs. All in all, you have to be investment-ready to erect a competent framework for implementing automation for managing your maintenance operations.
Managing complexities
Automation can bring complexity to the maintenance process, especially in two ways. Firstly, in adjusting to equipment variability and secondly, in maintaining reliability.
Adapting to equipment variability demands a flexible automation system capable of adjusting to diverse machinery specifications, configurations, and conditions. You need sophisticated sensor integration and control algorithms to streamline automation across a range of equipment types.
While maintaining reliability, you must address potential system failures, so as to ensure robust fault detection mechanisms and implement redundant systems to minimize downtime.
Balancing the need for adaptability with the imperative of reliability requires meticulous design, continuous monitoring, and timely updates to accommodate evolving maintenance requirements, which becomes a tough process altogether.
Handling Partial Dependence and Partial Independence
Even if automation is implemented for maintenance, it still requires some degree of human intervention. You cannot thus completely transfer the responsibility of managing maintenance tasks on the automation systems, which themselves will work under the supervision of an automation management team. You will have to closely watch if your automation systems are performing their function rightly or not.
Let’s take an example of manufacturing systems; a robotic assembly line may need humans to program specific tasks, adjust machinery, or replace worn-out components. If a robot malfunctions or a sensor requires recalibration, human expertise is crucial to diagnose the issue and implement corrective measures. Likewise, in the medical equipment industry, a fully automated medical imaging device may require manual calibration by skilled professionals for accurate and reliable results.
Building Rapport
The challenge we discussed previously, gives way to a connected challenge – establishing human-machine coordination.
As automated systems become more sophisticated, humans need to collaborate closely with machines for optimal performance. The collaboration spans tasks like programming, diagnostics, and troubleshooting. Establishing a harmonious human-machine rapport involves not only technical proficiency but also a deep understanding of the system’s intricacies. Here, human technicians must navigate complex interfaces, interpret data outputs, and communicate effectively with automated systems.
Moreover, the challenge extends to cultivating trust in automation. Humans must feel confident in the reliability of automated processes, especially when it comes to critical functions, say in precision manufacturing. Now, building such trust creates the need for streamlining communication, training staff, and building strong feedback mechanisms so that the team is fully equipped to make use of automated processes.
Building a Flexible Data-Value Chain
The implementation of automation systems in maintenance heavily relies on a robust data-value chain. It is integral to predictive maintenance that integrates real-time sensor data, historical records, and operational parameters. The challenge lies in orchestrating a seamless flow of data across the entire value chain.
Firstly, disparate data sources, varying formats, and inconsistent quality must be harmonized for accurate predictive models. Next, establishing interoperability among diverse systems is a technical hurdle, which requires standardized protocols. In terms of hardware, you need sensors, IoT devices, and data storage infrastructure, so as to manage large amounts of data.
Last but not least, the data-value chain must be resilient to evolving operational conditions to support automation to adapt to ongoing procedural changes.
Developing a Human Cyber-Physical System (H-CPS)
Automation gives rise to H-CPS, where people, machines, and computer technology all work together. However, managing it is no easy feat. One major issue is the concurrency and synchronization problem, where intricate interactions between humans, physical systems, and cyber technologies can make it tricky to keep everything in synchronization.
The interfaces between human operators and autonomous components present another hurdle. Designing H-CPS requires careful consideration of how humans interact with automated elements and the development of effective control strategies for systems. Similarly, modeling and specifying the requirements for H-CPS can be tough due to the need to incorporate the human factor and the complex interactions between physical and cyber components.
Beefing up Cybersecurity
Securing automated systems with strong cybersecurity mechanisms is an imperative because as you make things smarter, you open the door to more cyber risks. With automation, machines communicate with each other quite frequently, which creates more chances for cyber-attacks.
Without robust cybersecurity measures, there’s a real risk of data breaches, manipulation of automated processes, and disruption of critical functions. It’s akin to fortifying a building – without solid defenses, vulnerabilities increase, potentially undermining the entire automation effort.
Overcoming Resistance
Employees, accustomed to familiar workflows, may express concerns about job security, harbor distrust in automated systems, or exhibit reluctance towards learning new technologies. Addressing these emotional and psychological barriers is essential for successful automation adoption.
Due to these concerns, maintenance leadership can find it tough to shift from established workflows to automated processes. Finally, employee apprehensions cannot disappear in a day, and it takes time for them to ebb away.
Scaling across processes
As operations expand, diverse processes emerge, each with unique demands and intricacies. Implementing automation at scale necessitates addressing varying workflows, data sources, and system interfaces against operational expansion.
In this process, compatibility issues may arise. Further, coordination and synchronization become critical, which creates expectations of careful actions from planners to sustain efficiency.
What opportunities does Automation bring in Maintenance?
By building capabilities you can effortlessly overcome the challenges we saw. So, don’t be deterred by them. While there are challenges, there are opportunities, too. So, envision can capitalize on these opportunities and enjoy their benefits.
Smart Condition Monitoring
Automation has been a key lever in enabling enterprises to transition from preventive maintenance software to predictive maintenance systems. Offering remote monitoring capabilities to maintenance teams, across industries, this move can transform the character of condition monitoring across processes such as:
Fault Detection and Diagnostics: Automation enables real-time monitoring of equipment conditions, facilitating early fault detection and diagnostics. By leveraging sensors and data analytics, the system can identify abnormal patterns or deviations from normal operating conditions. As a result, technicians can swiftly respond with corrective actions before issues escalate.
Work Order Generation: Upon detecting potential faults or deviations, an automated system can generate work orders seamlessly. Due to this feature, maintenance teams receive timely and accurate information about the issues that require attention.
Vibration Analysis and Balancing: Vibration patterns can indicate potential imbalances or misalignments in rotating equipment. By integrating automated balancing systems, maintenance managers can address these issues promptly, thereby enhancing the reliability of assets. It will work as a part of a predictive maintenance strategy, where abnormal vibrations can be an early indicator of impending failures.
Thermal Imaging for Electrical Systems: Automation extends to the use of thermal imaging technology for monitoring electrical systems. An automated system can analyze thermal patterns in electrical components to identify potential issues such as overheating.
Battery Health Monitoring: Advanced sensors and automated analytics can continuously assess the condition of batteries in various devices and systems. With these systems, you can anticipate the need for battery replacements or maintenance based on the real-time health status, preventing unexpected downtime and disruptions.
Now, let’s look at some other industry-specific examples that cast light on how automation can be a boon in the monitoring process:
Monitoring and Control of HVAC Systems: Automated systems collect data on temperature, humidity, and air quality and feed this real-time information into a centralized control system. As a primary step that aids predictive maintenance, they help take corrective actions beforehand.
Conveyor Belt Tensioning: Integrated sensors or load cells provide real-time data on tension levels, providing input to automated systems to autonomously adjust the tension of conveyor belts. The predictive analytics algorithms get trained to anticipate tension changes based on historical data.
Corrosion Monitoring in Maritime Structures: Sensors provide real-time data on corrosion levels, which is transmitted to a central monitoring system. The data collection and analysis allow for early detection of corrosion, as algorithms identify trends and patterns that indicate potential corrosion-prone areas.
Advanced Robotics Streamlining Routine Operations
The integration of robotics into various facets of inspection and maintenance streamlines many routine processes such as:
Inspection: In the industrial sector, deploying robots for routine inspections of machinery and equipment reduces the need for human intervention in hazardous environments. Industrial robot maintenance ensures these robotic systems operate efficiently, preventing unexpected failures and optimizing performance. For instance, in the energy sector, robotic systems equipped with advanced imaging technologies can inspect turbine blades for defects and wear, ensuring seamless operations with minimal downtime.
Cleaning Systems: May it be any industry, facilities, often face challenges in maintaining cleanliness which impacts operational efficiency. Automated cleaning systems, driven by robotics, offer a solution. Robots can navigate complex spaces, execute cleaning tasks with precision, improve sanitization, and reduce time for the process. To give an example, robots can navigate solar arrays, remove dust and debris, and improve energy throughput through solar panels.
Pipeline Monitoring and Inspection: Robotic systems designed for pipeline inspection can navigate through intricate networks, detecting leaks, corrosion, or other anomalies.
Alignment in Conveyor Systems: Automated robotics can be employed to monitor and maintain the alignment of conveyor belts. By promptly correcting misalignments, these systems smooth material transport.
Efficient Lubrication and Greasing
Lubrication and Greasing is one elemental process in entire maintenance operations, as no equipment can ever function without lubrication and greasing. This is a periodic activity that can become a headache if technicians do not adhere to schedules, and can lead to upheavals in performance.
Automation brings a paradigm shift as it offers scheduled lubrication and greasing cycles based on real-time usage data, eliminating the inefficiencies associated with manual applications such as over or under-lubrication and greasing. The chances of premature bearing failure are thus remarkably brought down. The condition monitoring sensors provide real-time data on bearing temperature and vibration reinforcing the process of lubrication and greasing application.
Streamlined Calibration
Through automated testing and calibration, the efficiency and speed of these operations are significantly heightened. You achieve consistency in the calibration of measurement instruments, as the risk of errors is eliminated, and results are more reliable.
Automatic calibration and testing bring advantages such as scheduled calibration, remote calibration capabilities, and robust data logging. Scheduled calibration takes away the complexities of adhering to calibration timelines, while remote capabilities prove invaluable for geographically dispersed assets.
Energy Efficiency
By harnessing real-time data, automated systems optimize equipment performance, dynamically adjusting settings for peak energy efficiency. While minimizing operational costs, these systems also extend the lifespan of machinery, as they reduce the overall environmental impact.
The consistency in equipment operations is ascertained through intelligent adjustments based on current conditions. This is also one of the best maintenance practices, which can align with your sustainability and green management goals.
Improvement in Equipment TCO and EBITDA
Total Cost of Ownership (TCO) encapsulates all expenses associated with owning and operating equipment, extending beyond the initial purchase cost. Automation can reduce TCO by introducing efficiency measures in maintenance.
Predictive maintenance helps in the proactive identification of potential issues, facilitating scheduled maintenance and averting costly breakdowns. The maintenance costs are thus eliminated right away. Likewise, efficient energy usage curbs utility costs over the equipment’s lifecycle.
The reduction in TCO through automation translates into tangible benefits in EBITDA. Reduction in downtime, energy efficiency, and optimization of labor utilization frees up capital. Also, due to improvements in asset management, the revenue-generating potential of existing assets is maximized. All these factors potentially contribute to an increase in and positively impact EBITDA.
How a CMMS helps overcome automation challenges and secure opportunities
A computerized maintenance management system (CMMS) can be a one-stop maintenance solution to beating automation adoption woes for transforming maintenance processes and securing opportunities that it offers.
Implementing a CMMS software can thus be the first step in your automation program and offer future directions. By integrating it with other technologies, streamlining big data analytics, and assimilating it into the Industrial Internet of Things (IIoT), a CMMS will enable a smooth transition to fully automated workflows.
Learn from our experts how a CMMS acts as a bridge between human capabilities and intelligent systems. Using FieldCircle’s capabilities, you can harness the transformative potential of automated maintenance systems and capitalize on the opportunities they offer.