What Are Maintenance Costs? Insights, Strategies to Optimize Your Expenses, and More
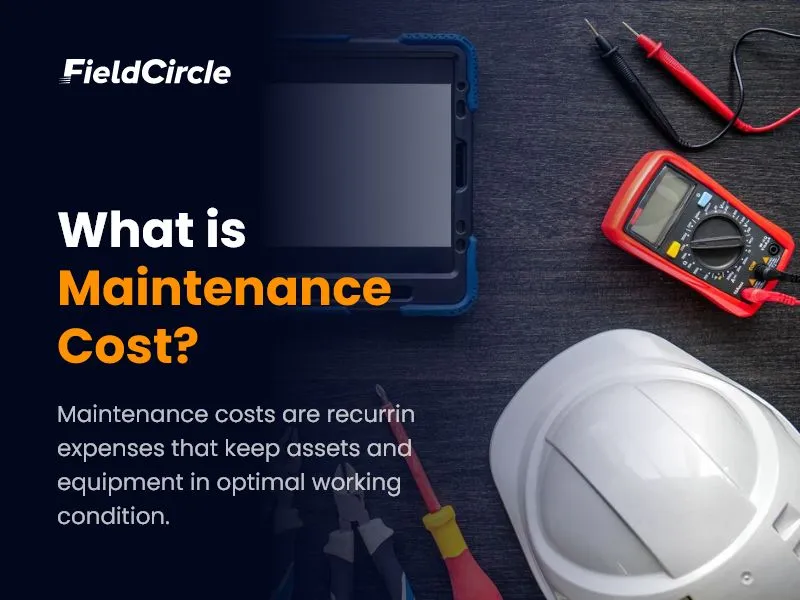
Maintenance costs are recurring expenses that ensure assets and equipment remain in optimal working condition. They remain in the background when businesses plan their budgets, yet they can account for a significant portion of overall expenditures.
Depending on the nature of the business, maintenance costs can range anywhere between 15% to 40% of the total operating costs—and in certain industries, even higher. They are thus a critical area of focus, as the financial impact of poorly managed maintenance can quickly spiral out of control.
Understanding the breakdown of these costs is essential, not just for day-to-day budgeting, but also for long-term business sustainability. On the contrary, failing to understand these expenses can potentially lead to costly disruptions and inefficiencies.
However, if you are aware about ins and outs of maintenance costs, you can successfully manage and control these expenses. The following discussion serves the purpose by discussing everything about maintenance costs, right from key components and stakeholders to the processes to calculate and optimize them.
What are the Key Components of Maintenance Cost?
Key components of maintenance cost are labor costs, material and spare parts expenses, equipment and tool expenses, overhead costs, and software maintenance vendor fees. These elements of maintenance management are crucial for effective budgeting and operational efficiency.
Labor Costs
Labor costs cover wages, salaries, benefits, overtime, training, and outsourced labor payments to technicians, engineers, maintenance managers, maintenance supervisors, as well as contractors for their expertise. They form a significant portion of the maintenance budget and encompass the human efforts necessary to perform maintenance activities. Efficient labor management ensures the timely completion of tasks, reducing the frequency and severity of unplanned breakdowns. This helps prevent expensive repairs and keep maintenance costs under control.
Material and Spare Parts
Material and spare parts expenses include the costs associated with replacing spare parts such as bearings and belts, raw materials, consumables such as lubricants, filters, adhesives, fasteners, and tools essential for maintaining machinery efficiency and keeping assets functional. Investment in tangible components helps keep spare parts inventory readily available, preventing prolonged downtime during equipment failure and helping maintenance activities proceed without delays. Proper inventory management decreases operational costs and inefficiencies.
Equipment and Tool Expenses
Equipment and tool expenses involve upkeep prices for diagnostic tools like thermal imaging cameras and vibration analyzers, general tools like hand tools, power tools, and precision instruments, and rental costs for leasing equipment during specific maintenance activities. Spending money on reliable equipment and tools enables accurate issue identification, reduces unnecessary repairs, and prevents costly breakdowns. It also reduces repair time and prevents errors caused by inadequate equipment. To maintain the equipment, implement a good equipment maintenance solution as it comes with several benefits for the maintenance team.
Overhead Costs
Overhead costs are indirect expenditures on utility bills like electricity, water, and heating, facility maintenance expenses for workshops and storage areas for tools and spare parts, salaries of support staff, and software licensing fees. They involve spending on everything essential to maintaining the facilities and infrastructure supporting maintenance activities. Neglecting these aspects results in inefficiencies, damaged equipment, and mismanaged schedules, increasing overall maintenance costs. Appropriate management of overhead costs ensures proper coordination, scheduling, and oversight while avoiding unexpected financial strain.
Software Maintenance Vendor
Software maintenance vendor fees include licensing costs, upgrades and update expenses, and vendor support costs for ongoing support, troubleshooting, maintenance, training services, and software customization. It manages software solutions like Computerized Maintenance Management Systems (CMMS) or Enterprise Resource Planning (ERP) tools to streamline maintenance planning, tracking, and reporting. Proper licensing, renewal, and software updates reduce human errors, minimize inefficiencies, enhance resource allocation, improve decision-making, forecast future maintenance needs, and ensure long-term savings.
Who Tracks Maintenance Costs?
Maintenance managers, finance department, facility manager, procurement department, operations manager, and maintenance technicians track maintenance costs. Each role is responsible for monitoring, managing, and optimizing the financial aspects of maintenance activities.
Maintenance Managers
Maintenance managers oversee all maintenance activities and ensure cost-effectiveness. They are responsible for planning and scheduling preventive maintenance to avoid unplanned expenses, managing labor, materials, and repairs budgets, and tracking performance via metrics like maintenance per cost and equipment downtime to identify inefficiencies. By balancing preventive and reactive maintenance, they aim to reduce unexpected expenses and allocate resources efficiently—demonstrating the clear preventive maintenance benefits in minimizing downtime, optimizing asset life, and improving operational stability.
Finance Department
Finance departments align maintenance activities with the organization’s overall financial strategy. They collaborate with other departments to allocate the optimal budget for maintenance, track expenses to ensure transparency and prevent overspending, and prepare a detailed financial report highlighting the ROI of maintenance efforts. Finance departments maintain financial discipline so maintenance costs do not overshoot and consequently impact profitability.
Facility Managers
Facility managers ensure the upkeep of physical infrastructures, including buildings, systems, and equipment. They are responsible for maintenance coordination, providing timely repairs, and implementing preventive maintenance software to streamline scheduling and tracking of maintenance activities. By leveraging such tools, they can efficiently monitor energy consumption to identify cost-saving opportunities and coordinate with external service providers for specialized maintenance tasks. As part of core facility manager responsibilities, their role is to minimize operational disruptions and reduce expenses associated with asset downtime and inefficient energy usage.
Procurement Department
Procurement departments handle the acquisition of tools, materials, and maintenance services. They select suppliers and negotiate contracts to secure reliable and cost-effective vendors. They manage inventory to ensure optimal spare parts and equipment stock without overstocking. Their role also includes analyzing market trends to compare costs and choosing the best maintenance supplies deals. Efficient procurement avoids overpricing, eliminates delays in acquiring materials, and minimizes waste from excess inventory.
Operation Managers
Operation managers bridge maintenance activities and production goals. Their responsibilities include aligning maintenance schedules to minimize disruption, ensuring adequate resource allocation for operations and maintenance, identifying potential risks, and coordinating with maintenance teams to resolve them proactively. They prioritize maintenance tasks that impact production efficiency, helping to reduce losses because of production halts and missed deadlines.
Maintenance Technicians
Maintenance technicians execute maintenance activities by performing preventive and corrective maintenance tasks. They inspect and identify issues early, report them to management, and ensure proper maintenance of tools and equipment for efficient operations. Their role is to improve equipment reliability and prevent costly failures through timely interventions for repairs and maintenance. They are responsible for providing accurate, on-field data that feeds into cost-tracking mechanisms.
What are the Tools Used for Tracking?
CMMS (Computerized Maintenance Management Systems) and ERP (Enterprise Resource Planning) systems are tools for tracking maintenance costs. CMMS tracks, manages, and analyzes maintenance activities and costs through a centralized platform. It includes work order management, cost tracking, inventory management, and reporting. ERP integrates maintenance data with broader organizational functions like finance, procurement, and inventory. It enables cross-departmental visibility, tracking maintenance costs alongside overall business expenses.
How Are Maintenance Costs Calculated?
Maintenance costs are calculated using historical data, predictive analysis tools, and maintenance management software. Historical data provides records of past maintenance expenses, such as labour hours and spare parts usage, which help identify trends and predict recurring maintenance expenses. Predictive analysis tools utilize advanced technologies like IoT sensors and machine learning to estimate costs based on current asset conditions, reducing unexpected failures and aligning maintenance with real-time asset performance. Maintenance management software, such as CMMS or ERP systems, automates tracking and forecasting labor, materials, and downtime expenses.
Here are the metrics vital for calculating maintenance costs
- Consider expenditures regarding assets, including purchase, operation, maintenance, and disposal—collectively known as the total cost of ownership (TCO). This comprehensive view is especially applicable for high-value equipment industries like manufacturing and healthcare. TCO is calculated using the formula:
- Cost per Asset/Unit: Measures the average price of maintaining a single asset or unit. It helps compare the maintenance efficiency of different assets or equipment types.
- Mean Time to Repair (MTTR): This measures the time it takes to repair and restore an asset to operational status. It indicates quicker repairs, lower costs, and reduced downtime.
- Maintenance, Repair, and Operation (MRO): Include labor, spare parts, and consumables used in maintenance activities. It provides a comprehensive view of direct maintenance expenses, helping organizations manage inventories and budgets effectively.
TCO = Initial Cost + Maintenance Costs + Operating Costs – Residual Value
Cost per Asset/Unit = Total Maintenance Costs / Number of Assets
MTTR = Total Repair Time / Number of Repairs
How to Optimize Maintenance Costs?
Optimizing maintenance costs requires streamlining operations using maintenance software, analyzing asset performance data, establishing relevant KPIs, enhancing resource utilization, and leveraging technology to improve efficiency. Strategies such as lean maintenance and autonomous maintenance reduce waste, empower employees, and enhance maintenance practices for improved maintenance management and cost.
Below are 9 effective strategies to achieve cost optimization
- Implement a Maintenance Management System
- Track Preventive vs. Reactive Maintenance
- Monitor Asset Performance
- Use Key Performance Indicators (KPIs)
- Optimize Spare Parts Inventory
- Adopt Condition-Based Maintenance
- Streamline Work Order Processes
- Leverage Reporting and Analytics
- Encourage Staff Training
Implementing a Maintenance Management System optimizes maintenance costs by improving real-time visibility into maintenance operations and reducing errors caused by fragmented information. It offers a single platform for all maintenance data. It improves inter-department communication and makes the tracking, scheduling, and planning of maintenance, labor hours, and material usage easier.
Tracking preventive vs. reactive maintenance helps reduce expensive emergency repairs and unexpected breakdowns. Monitoring the ratio of scheduled, proactive maintenance to unscheduled emergency maintenance provides actual data that can be evaluated for better maintenance planning. It helps distinguish and categorize maintenance tasks according to their nature and impact on operations.
Monitoring asset performance contributes to cost reduction by identifying inefficiencies early and avoiding over-servicing. Using IoT sensors to monitor metrics like temperature, vibration, and runtime helps adjust maintenance schedules based on wear and tear trends. Such an approach not only prevents unwanted repairs but also minimizes expenses associated with major breakdowns.
Using KPIs optimizes maintenance costs by providing quantifiable results of maintenance strategies and highlighting improvement areas. Establishing relevant maintenance KPIs to get measurable insights into maintenance performance is essential. Reviewing performance indicators regularly helps identify cost trends, track progress, and adjust strategies effectively.
Optimizing spare parts inventory reduces maintenance costs by preventing delays in repairs due to shortages or unavailability of spare parts. A well-managed spare parts inventory tracks, schedules, monitors, plans, and manages part usage patterns using maintenance software for correct stocking and avoiding overstocking to prevent excess storage expenses.
Adopting condition-based maintenance optimizes maintenance costs by scheduling tasks based on real-time equipment needs, avoiding unnecessary interventions. Organizations use this maintenance strategy to make maintenance decisions based on actual asset conditions using sensors and IoT technology rather than fixed scheduling, reducing unnecessary maintenance tasks and related expenses.
Streamlining work order processes improves maintenance costs by enhancing resource allocation and reducing time wastage. It also provides clarity when prioritizing maintenance tasks. Simplifying work orders tracks labor hours and allocates resources efficiently to prevent bottlenecks. This ensures proper and prompt task completion and increases workforce efficiency.
Leveraging reporting and analytics reduces maintenance costs by identifying inefficiencies and enabling data-driven decisions for continuous improvements. Detailed reports and analytics offer actionable insights into high-cost areas and recurring issues. This information helps adjust strategies and improve efficiency.
Encouraging staff training optimizes maintenance costs by preventing avoidable equipment damage and improving the efficiency of routine tasks. Training employees on proper equipment usage, basic maintenance tasks, and emergency response procedures helps reduce downtime and cuts costs related to frequent repair works.
What is the Difference between Maintenance Costs and Capital Expenses?
Maintenance costs are the recurring expenses necessary to keep assets operational, whereas Capital Expenses (CapEx) are one-time investments made to improve an asset’s condition.
Maintenance costs include regularly repairing, servicing, and sustaining existing operations to preserve operational efficiency. Examples are repairing equipment, routine servicing, replacing worn-out parts, and so on. These activities are treated as operational expenses (OPEX) and are expensed immediately. Funds spent on maintenance works preserve the asset condition and provide reliability and longevity but do not enhance its value.
On the other hand, Capital expenses include the amount spent to acquire, upgrade, or improve assets for the organization’s long-term benefit. Examples are purchasing new machinery, constructing facilities, upgrading technology, etc. These sporadic costs are treated as capital expenditures (CAPEX) that depreciate over time. These activities focus on increasing asset value, productivity, and lifespan.
To clarify the point, maintenance costs include replacing worn-out conveyor belts to keep them operational, while capital expenses involve purchasing a new conveyor to improve production speed and increase overall capability.
What are the benefits of Optimizing Maintenance Costs?
The benefits of optimizing maintenance costs range from reduced expenses, increased equipment lifespan, and energy savings to better budget control and adherence to industry regulations. These benefits improve equipment performance, increase production capability, and support long-term sustainability.
Top 8 benefits of optimizing maintenance costs are
- Reduced Expenses
- Increased Equipment Longevity
- Improved Operational Efficiency
- Energy Savings
- Enhanced Safety
- Better Budget Control
- Data-Driven Decisions
- Regulatory Compliance
Optimizing maintenance costs reduces expenses by minimizing emergency breakdowns and eliminating unnecessary repairs and servicing. It significantly lowers repair, labor, and replacement expenses. Using proactive planning allows organizations to intervene at the right time, avoiding expensive reactive measures and cutting expenditures between 18 and 25%.
Regular and optimized maintenance extends the lifespan of assets by minimizing tears and wear, reducing the risk of breakdowns. This helps maintain operational efficiency and prevent premature damage, delaying the need for expensive replacements, reducing downtime, and maximizing asset ROI.
Optimizing maintenance costs provides regular and efficient maintenance that reduces equipment failures, unplanned outages, and operational disruption. It enhances equipment reliability, improves resource utilization, and ensures sustainable operations for improved workflow, contributing to business profitability and competitiveness.
Well-maintained equipment and tools reduce energy consumption by operating machinery at peak efficiency, lowering utility costs, and enhancing overall operational efficiency. For example, using chilled water pumps in the HVAC system of a cleanroom in a high-tech manufacturing environment increased energy savings by 53%. Regular upkeep, such as cleaning, lubricating, and identifying and fixing leaks, insulation issues, or faulty systems, minimizes unnecessary energy use.
Regular maintenance ensures timely repairs to minimize risks of accidents and equipment failures, creating a safer working environment. Predictive maintenance identifies potential issues early and addresses them to prevent costly incidents. For instance, Schindler Group conducted regular safety audits and logged safety hazards from 20 to 1,200 annually. A well-maintained safety system protects employees and infrastructure from damage and avoids additional expenses.
Optimizing maintenance costs provides accurate cost tracking for real-time expense monitoring, cost transparency breaking down labor, parts, and service expenses, and improves resource allocation for critical maintenance needs. For example, a mid-sized aerospace equipment manufacturer negotiated better terms with suppliers and decreased its procurement costs by 15%. Organizations can efficiently spend their budget, avoid surprises, and enhance financial stability.
With improved maintenance costs, organizations use data-driven records to refine maintenance strategies and prioritize investments. They track real-time performance metrics to optimize asset utilization and maintenance schedules, reduce unplanned downtime, repair costs, and waste, and ensure the highest ROI from maintenance efforts.
Consistent maintenance reduces fines and legal risks by ensuring compliance with industry regulations like OSHA and ISO. For instance, manufacturing companies violating the Clean Air Act under the Environmental, social, and governance (ESG) regulation face fines of up to $446,000 per violation. Regular upkeep helps meet safety inspections and certifications, as well as emission and waste management standards, and prevent accidents that lead to legal consequences.
Optimize Maintenance Cost with FieldCircle Maintenance Management Software
Built keeping in view each industry’s requirements, FieldCircle’s maintenance management software is a one-stop solution for managing and controlling costs and adhering to budget. With our outstanding features, you can track every single cost element with the utmost perfection.
A demo from our experts will give you a detailed idea as to how our tool actually works and regulates the maintenance cost. We will take you through various scenarios and offer practical insights as to how you can track and monitor different costs and also how you can keep a check on them through a combination of the features of our tool and the right approaches.