How To Develop Effective Maintenance Supervisors For Operational Success
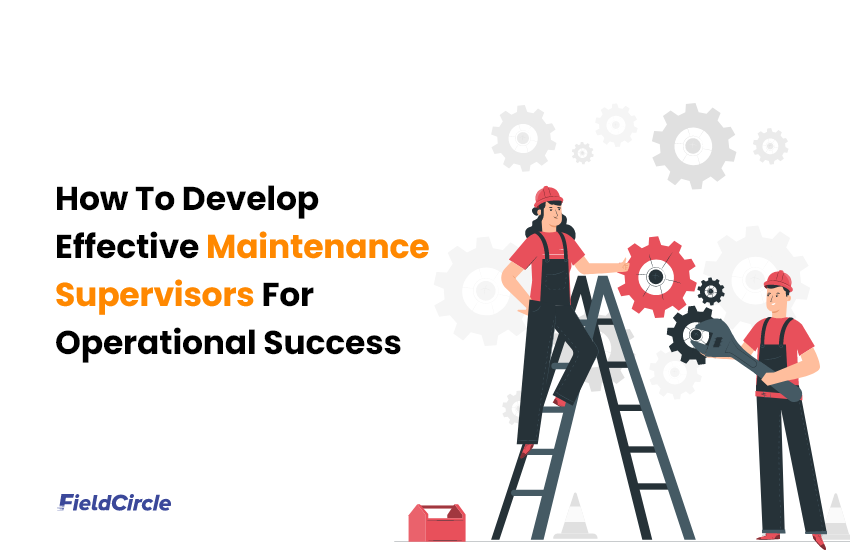
“A leader is best when people barely know he exists. When his work is done, and his aim fulfilled, they will say: “we did it ourselves,” are the wise words of Lao Tzu.
Even in maintenance operations, when workflows function smoothly, technicians say we did it.
No one can even doubt the role of technicians, but behind the curtain is a supervisor who keeps relentlessly following every process and person, monitoring and managing every activity, dotting the i’s and crossing the t’s.
Maintenance supervisors are architects of operational success, as their leadership and supervision skills are the driving force behind a well-functioning team and operations. They shape the trajectory of your maintenance processes and take it in a positive direction.
As frontline staff members, supervisors are pivotal as they serve as a bridge between top management and technicians.
Building effective supervisors is a nuanced task that goes beyond the management of routine tasks. Your supervisors must exhibit varied capabilities and involve themselves in people and processes actively. This translates into the challenge of ensuring that they possess necessary technical and management skills that align with your organizational goals.
As you might find yourself stuck as to what course to follow to build great supervisors, we offer these valuable tips.
Steps to Develop and Have the Best Supervisors in Your Maintenance Team
Supervisory powers are important in maintenance management as they dictate the efficiency of operations. New supervisors and managers entering your team must grasp the necessary skill sets while existing ones must be made aware of balancing authority with collaboration and made to adapt to emerging trends. Against this backdrop, follow these steps to have the top supervision talent and build a resilient and high-performing maintenance team.
Build a Joint Vision
When all your supervisors are on the same page they work as a unified force and align their efforts with a shared commitment towards enhancing operational efficiency. Clarity of purpose allows them to direct their energies and delegate tasks and responsibilities in the most optimum manner.
A clear and concise mission that reflects the organization’s values and objectives related to maintenance activities promotes collaboration and minimizes misunderstandings. It becomes easier to prioritize tasks, allocate resources efficiently, and make decisions that align with the overall maintenance strategy.
Understanding these objectives is essential for effective shift planning. Supervisors should be able to analyze and anticipate the unique challenges and tasks associated with each shift. Only by aligning the purpose with shift-specific objectives, they can develop targeted plans that address the particular maintenance needs during that time frame.
For instance, a night shift may prioritize preventive maintenance tasks to minimize disruptions during the day when production is at its peak. On the other hand, a day shift may focus on addressing immediate equipment issues to support ongoing operations.
Empower with a Proactive Approach
Traditionally, the focus was primarily on preventive maintenance, which involved scheduled inspections and repairs to forestall potential issues. However, predictive maintenance has been replacing it as leaders are adopting proactive maintenance strategies.
As PWC has brought forward, predictive maintenance decreases costs by 12%, extends the lifetime of an aging asset by 20%, and reduces safety, health, environmental, and quality risks by 14%. So it has become one of the must-have skills for today’s maintenance supervisors.
Equip your supervisors with capabilities to harness predictive maintenance technologies such as sensors, data analytics, and machine learning to foresee equipment failures so that they can precisely plan and minimize downtime. Adeptness in predictive maintenance not only optimizes asset performance but also goes hand in hand with the idea of data-driven decision-making.
Create a mandate for Industrial Hygiene
Supervisors act as the linchpin between management directives and frontline workers, which necessitates them to be well-versed in workplace health and safety practices. It can help in proactively identifying and mitigating potential risks and is necessary to build an environment where employees are cognizant of potential hazards. Moreover, supervisors should be trained in translating complex safety guidelines into actionable directives for their teams.
At least in facilities management, nearly 27% of managers covered in a survey do not think that employees are aware of potential hazards and how to report any risk. This gap can be bridged by supervisors who should be held accountable to ensure good health and safe conditions for workers in every operational activity.
Smooth the way for Guideline Acquaintance
Professionals with strong adherence to norms exhibit exemplary supervisor skills, showcasing their ability to manage and lead a team within legal and ethical frameworks. However, technicalities involved in these regulations, ranging from equipment maintenance procedures to safety protocols, demand comprehension, and implementation prowess.
The specific standards relevant to supervisory responsibilities will depend on the industry, the nature of the business, and the types of equipment and systems involved. In general, you should guide your maintenance supervisors to be thorough with:
– Occupational Safety and Health Administration (OSHA) Standards: Covers various aspects of workplace safety, including hazard communication, machine guarding, and personal protective equipment.
– National Electrical Code (NEC): Governs electrical installation and maintenance practices to ensure the safety of electrical systems.
– Environmental Protection Agency (EPA) Guidelines: Encompasses regulations for environmental compliance, addressing issues such as waste disposal and emissions control.
– Industry-Specific Certifications: Supervisors should be familiar with certifications relevant to their specific industry, covering specialized safety and maintenance protocols.
– ISO Standards: Denotes international standards that provide guidelines for quality management, environmental practices, and occupational health and safety.
– NFPA (National Fire Protection Association) Codes: Addresses fire prevention and protection measures to ensure the safety of personnel and facilities.
– Ergonomics Standards: Offers guidelines for designing workspaces and tasks to optimize human well-being and overall system performance.
– Building Codes: Provides applicable local or national building codes that dictate construction and maintenance requirements for structures.
– ANSI (American National Standards Institute) Standards: Covers a wide range of topics including safety, performance, and testing criteria for various products and systems.
– FDA (Food and Drug Administration) Regulations: This applies especially in industries involved in the production of pharmaceuticals, food, or medical devices.
Familiarity with these standards equips supervisors with the necessary tools to cultivate a culture of compliance, enhancing both operational efficiency and the overall safety of the workforce.
Instill Brain Twisting and Teasing Brilliance
Problem-solving and critical thinking skills are indispensable for every supervisor in maintenance due to the dynamic nature of operations. In scenarios where a critical piece of machinery unexpectedly malfunctions, the supervisor should swiftly diagnose the issue, weighing various potential causes. For instance, if a production line grinds to a halt due to an unidentified problem, the ability to analyze the situation critically enables in promptly identifying the root cause.
Moreover, in preventive maintenance planning, problem-solving skills come into the picture. The supervisor needs to anticipate potential issues and develop strategies to mitigate risks before they disrupt operations. The ability to solve problems and think critically comes into play during scheduling optimization, evaluating different maintenance strategies, and weighing the costs and benefits to optimize the performance and longevity of equipment. If we talk about resource management, managers with strong problem-solving and critical thinking abilities can efficiently allocate manpower and resources.
As Machine Lubrication mentions, your supervisors should divide problem-solving into these four levels so that they can address a maintenance problem with the right approach:
– Immediate Reaction: Address the problem when it arises and subsequently disregard it until its recurrence.
– Adaptation: Learn to coexist with the problem by making adjustments to accommodate its symptoms.
– Anticipation: Tackle the underlying causes of the problem through the application of preventive techniques.
– Proactive Approach: Change the conditions that gave rise to the problem initially, emphasizing a forward-thinking and preventive stance.
With these categories, your supervisors will guide the maintenance teams with the most appropriate course of action applicable for a given situation.
Empower with a CMMS
Equipping maintenance supervisors with a Computerized Maintenance Management System (CMMS) is essential for building new-age smart supervision skills.
In the first place, excellent CMMS software acts as a centralized platform for supervisors, and they can organize and manage work orders, asset information, and preventive maintenance schedules with ease. Next, the maintenance software improves coordination and cooperation among maintenance teams through real-time communication features and its mobile-friendly nature.
Supervisors can assign tasks, track progress, and communicate with team members seamlessly, promoting collaboration and swift issue resolution. So, irrespective of where members are positioned at the moment, they can connect with a member and engage in discussion. Thanks to mobile CMMS capabilities!
Most importantly, CMMS analytics features empower supervisors with data-driven insights. They can analyze historical maintenance data to identify patterns, optimize workflows, and make informed decisions. Invariably, adopting a CMMS has become the most basic criterion for building predictive maintenance capabilities, conducting proactive interventions, and preventing costly breakdowns.
Let them be watchful of Mannerisms and Etiquette
The foremost area where the professional demeanor should manifest in your supervisors is work ethic. When supervisors act with honesty, they bring transparency to processes. The entailing effect is reflected in integrity which paves the way for reliability in operations and sets the standard of a commitment to quality work.
Supervisors must also excel in allocating time efficiently so that they can respond to equipment breakdowns well in time and adhere to preventive maintenance schedules.
Equally important is their ability to harness team potential. As maintenance is a team effort, teamwork must be optimized. However, this happens when supervisors understand the collaborative nature of the work and allocate tasks based on individual strengths. So, through teamwork, supervisors can foster a sense of shared responsibility, where each team member contributes effectively to the collective goals.
Lastly, conflicts inevitably arise in any workplace. Good supervisors demonstrate the right skills to resolve conflicts for better outcomes. They not only address issues promptly but also maintain team cohesion, which is critical for continuous maintenance operations.
Watch like a hawk
Employ daily scoreboards and dashboards to understand how your supervisors are performing against the set thresholds for various key performance indicators (KPIs). With visual analytics, you will be able to quickly identify trends, bottlenecks, and areas where they need improvement. Include KPIs around these areas in your dashboards and promptly monitor them:
– Work Order Completion Rate: The percentage of assigned maintenance tasks completed within the scheduled timeframe will indicate the ability to manage workflow efficiently.
– Downtime Reduction: Tracks the reduction in equipment downtime under the management of the supervisor, reflecting her/his effectiveness in preventive maintenance and rapid response to breakdowns.
– Resource Utilization: It evaluates how effectively resources (human, equipment, and materials) are utilized by the maintenance team under the direction of the supervisor.
– Safety Compliance: Monitors adherence to safety protocols and the number of safety incidents, showcasing the commitment to maintaining a safe working environment.
– Training and Development: Measures the progress of maintenance team members in terms of skills development and certifications, indicating the role’s importance in fostering a skilled workforce.
– Budget Adherence: Assesses the supervisor’s ability to manage maintenance activities within the allocated budget, demonstrating financial responsibility.
– Equipment Reliability: Tracks improvements in equipment reliability and longevity, showcasing the supervisor’s effectiveness in implementing preventive maintenance strategies.
Make use of the insights obtained from these tools and provide feedback constructively on areas requiring improvement. In this way, you will align your employee performance with organizational goals, which will benefit your maintenance process.
Sustain Perpetual Development
Enabled by technological revolutions and domain-specific research, the maintenance field is undergoing rapid changes. Enterprises are capitalizing on concepts such as artificial intelligence and Digital Twin to reengineer their maintenance operations.
In the wake of this transformation, training your supervisors with knowledge and skills for applying the latest trends becomes an important agenda. Training can be vital to equip maintenance personnel with the skills needed to operate and maintain sophisticated equipment.
Along with technical skills, behavioral and communication skills, too, matter. To keep each of your members in the supervision team at the same level, you must conduct workshops on soft skills. Even the qualities of problem solving and critical thinking we talked about earlier will require professional training as not all supervisors will have the same natural ability to pursue and apply them. But with the help of training, you can attain the required levels of perfection in the needed skills in each of your supervisors.
Make them Promote Dialogue
Your maintenance team might comprise people from different ethnic backgrounds; they might come from different geographies. The supervisors must take due care in respecting the diversity existing in the workplace so that each member feels equally valued.
With diversity existing in a team, how well your supervisors handle the barriers caused by cultural differences determines overall success. They must demonstrate effective communication and interpersonal skills so that people find it easy to reach them.
A good supervisor always acts as a coach and mentor to staff rather than positioning himself as a snobbish manager. By doing so, he creates a work environment, where talent is nurtured. Such an open culture keeps improving the productivity of maintenance technicians and helps in talent retention. Make sure that they exhibit these people skills. At the end of the day, the ability to communicate effectively, and show empathy and support are indispensable traits for successful supervision.
Equip to deal with upheavals
Unforeseen equipment failures and other emergencies can disrupt maintenance operations and jeopardize safety. Hence the need to equip your supervisors with emergency response capabilities.
You can enable your supervisors to remain one step ahead by training them about incorporating a computerized maintenance management system (CMMS) in their emergency response framework.
A CMMS will keep them abreast of the overall functioning of the maintenance operations and alert them well in advance about probable issues. The tool will offer them reminders about conducting the next audits and if a particular piece of equipment is about to go down. From efficiency to monitoring hazards, a maintenance management software can be their go-to choice for mitigating risks.
Wrapping Up
The role of supervisor is constantly evolving from a mere position that manages tasks and performs supervision. As a part of maintenance leadership, the ability to supervise is becoming important from a strategic viewpoint.
Today’s supervisors are tasked with not just managing day-to-day maintenance activities, but their performance KPIs are linked to monetary benefits. In accordance with the addition of responsibilities, the supervisor role has begun bearing more accountability and must offer skills and performance that enhance your maintenance ROI.
As we spoke, adopting a maintenance management application can be a great step in this process. With tools such as FieldCircle CMMS, you can take your maintenance supervision capabilities to the next level.