Cross-Training Your Maintenance Team: Strategies and Benefits
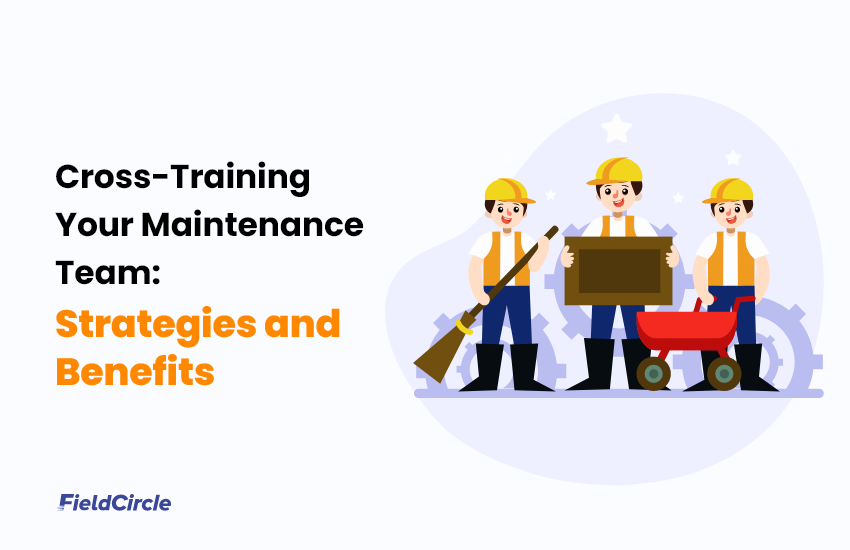
Today’s maintenance leaders have a penchant for being versatile. One prominent reason behind it is the rapid penetration of technologies in maintenance. It is quite evident how Industry 4.0 is making the adoption of IoT, predictive maintenance and automation commonplace in most industries. These forces are shaping business processes in manners hitherto unimagined.
In the wake of these changes – which nobody knows how fast will translate into unexpected realities – the need to be well-versed across functions and practices has become clearer. The solution to counter this challenge, which is still unfolding, lies in cross-training.
So, to become future-ready, and demonstrate adeptness in managing evolving maintenance operations, cross-training has become a powerful mechanism and invincible tool. Its viability in today’s maintenance management is justified by its efficacy in equipping teams with capabilities to manage complex software interfaces, participate in the application of AI and data analytics, and secure digitally-driven systems from cybersecurity threats. Moreover, it aims to bring out maintenance staff from their traditional isolated role, often looked at as taciturn, and enthuse them to communicate and collaborate across functions.
In a nutshell, cross-training is not just a need but one key practice that is not a choice but an obligation for today’s maintenance functions. We look at the strategies to cross-train your maintenance employees and empower them with diverse skills, and then move to the benefits you will derive as a result.
What is Cross-Training and What is its significance?
Cross-training is the process of training employees to perform tasks and responsibilities outside their primary job roles to build versatility and improve operational flexibility. It equips employees with diverse skills, allowing them to step into various roles when needed ensuring operational continuity during absences or workload spikes. This approach fosters teamwork, enhances employee engagement, and develops a more adaptable workforce. By reducing dependency on specific individuals, it also strengthens organizational resilience.
How to Craft a Cross-Training Program For Maintenance: Strategies to adopt for Cross-Training employees?
Creating a cross-training program for maintenance staff is a strategic way to enhance workforce flexibility, improve efficiency, and ensure smooth operations. By equipping employees with knowledge in multiple areas, such as HVAC, plumbing, electrical systems, and general repair, organizations can minimize downtime and optimize resource utilization. This guide outlines effective strategies to develop a robust cross-training program, from assessing skills to evaluating outcomes.
1. Assess Skills and Roles
To create a successful cross-training program, it’s essential to first assess the current skills and roles within your facility maintenance team. Identify key areas of expertise, such as HVAC, electrical work, plumbing, and general repairs. Evaluate each team member’s strengths and skill gaps to pinpoint where additional training is needed. For example, if several employees excel in HVAC but lack knowledge of electrical systems, prioritize electrical training modules to address this gap. This foundational assessment ensures that your program targets the most critical areas for improvement.
2. Set Clear Objectives
A well-structured program requires clear and measurable objectives. Define what you want to achieve, such as reducing equipment downtime, improving efficiency, or creating more scheduling flexibility. Setting goals like these allows you to measure the program’s success over time. Additionally, outline expected outcomes, such as smoother operations during staff absences or enhanced collaboration among team members. For instance, a cross-trained team can step in during emergencies without disrupting workflow, leading to better resource allocation.
3. Create a Structured Training Plan
Developing a structured training plan is key to ensuring consistent learning outcomes. Divide the program into manageable modules, with each module focusing on a specific skill or area of maintenance. Include hands-on training opportunities, such as role rotations, where employees can gain real-world experience in different tasks. Pair this with a mentorship program by assigning experienced employees to guide less-experienced colleagues. For example, a senior plumber could mentor a technician in advanced repair techniques, fostering both skill development and team collaboration.
4. Utilize Diverse Learning Methods
Incorporate a mix of learning methods to keep training engaging and effective. Interactive workshops can encourage employees to work together and solve practical maintenance problems. Supplement this with online resources, such as video tutorials and manuals, for flexible, self-paced learning. Job shadowing is another effective tool, allowing employees to observe and learn from peers performing specialized tasks. For example, a technician could shadow an HVAC specialist to gain insights into equipment troubleshooting.
5. Monitor Progress and Provide Feedback
Regularly monitoring progress ensures that the training program delivers the desired results. Use tools like a cross-training matrix to track skill acquisition and identify remaining gaps. Assess employees’ progress through practical evaluations, quizzes, or supervisor observations. Provide constructive feedback to reinforce strengths and address areas for improvement. For example, if an employee is struggling with electrical troubleshooting, offer targeted support or additional training resources to help them succeed.
6. Encourage Knowledge Sharing
Fostering a culture of knowledge sharing is critical for sustaining the benefits of cross-training. Encourage peer learning by organizing team meetings where employees can exchange insights and best practices. Create internal documentation, such as step-by-step guides or procedure manuals, to serve as reference material for all team members. For instance, documenting standard HVAC troubleshooting techniques ensures consistent application across the team.
7. Offer Incentives for Participation
Motivate employees to fully engage in the cross-training program by offering meaningful incentives. Recognize their efforts through bonuses, certificates, or public acknowledgment during team meetings. Additionally, highlight how cross-training can contribute to career growth. Employees who acquire new skills are more likely to be considered for promotions or leadership roles, which can inspire them to invest in their own development.
8. Assess the Impact
Finally, measure the program’s overall impact by tracking performance metrics, such as response times to maintenance issues, equipment reliability, and employee satisfaction. Use this data to evaluate the program’s success and identify areas for improvement. For example, if the program has reduced downtime but not improved team collaboration, consider introducing more team-based training exercises. Continuously refining the program ensures it remains aligned with the organization’s evolving needs.
What are the Benefits of Cross-Training for your Maintenance Team?
Establishing harmonized cross-functional collaboration and making maintenance personnel understand the nitty-gritty of the other sides of the business are primary goals of cross-training. This process brings several improvements that reflect across:
-
Root Cause Analysis Proficiency
Identifying the root causes of issues in maintenance operations is a cross-functional task, where team members from different teams have to arrive and analyze the situation. Cross-training streamlines the process of implementing and employing methods like failure mode and effects analysis (FMEA), to address underlying issues and prevent recurring problems. So, teams can systematically analyze equipment failures and take note of establishing a guideline that won’t lead to the issue in the future.
-
Predictive Maintenance Implementation
With procedural and technical knowledge, maintenance personnel can apply their skills to implement condition monitoring, IoT sensors, and predictive analytics. Proactive identification of potential failures and the scheduling of maintenance activities before critical issues arise will be two important outcomes of the action.
-
Integration of Reliability-Centered Maintenance (RCM)
RCM rests on a systematic analysis of critical components and their failure modes, guiding maintenance decisions based on risk and criticality. Cross-trained professionals can effectively implement reliability-centered maintenance methodologies and sustain asset reliability.
-
Streamlined Procurement
Maintenance professionals by offering accurate insights into equipment specifications and requirements will optimize procurement efforts. They will thus minimize the lead time for procuring the required spare parts and be the key to sustaining optimum levels in the spare part inventory.
-
Efficient Data Management for Analytics
Technical cross-training enhances data literacy among maintenance staff. This proficiency is crucial for leveraging data analytics in maintenance management. Teams can efficiently collect, analyze, and interpret data to make informed decisions, driving continuous improvement in maintenance strategies and overall operational productivity.
-
Integrated Health and Safety Protocols
Health and safety don’t form a special function but a responsibility within a function. Technically, maintenance supervisors and managers well-versed and adept in OHS (organizational health and safety) standards mitigate the risk of accidents or incidents, which will have broader implications for the entire organization.
-
Optimized Energy Consumption
Minimizing energy utilization is one pressing urgency that every team has to address without fail, as enterprises strive to cut down unnecessary energy usage and adopt green measures. Cross-training includes an understanding of energy consumption patterns related to maintenance activities and creating roadways for energy efficiency improvements surrounding cost reductions.
It’s Time you Implement Cross-Training
Implementing cross-training programs for maintenance not only addresses immediate skill gaps but also contributes to the long-term resilience of organizations. It standardizes the maintenance workflow and builds an ideal work environment as bottlenecks associated with isolated teams are eliminated. By cultivating adaptable teams capable of seamlessly navigating industry changes, maintenance practices evolve with the demands of the future.
As organizations strive for success, implementing cross-training becomes a strategic investment in workforce versatility and collaborative problem-solving. We encourage you to consider integrating these strategies within your team, fostering a culture of continuous learning and adaptability. Even adopting tools like maintenance management software is one part of this process. Know how it works by speaking with our experts.