What is Maintenance Management?
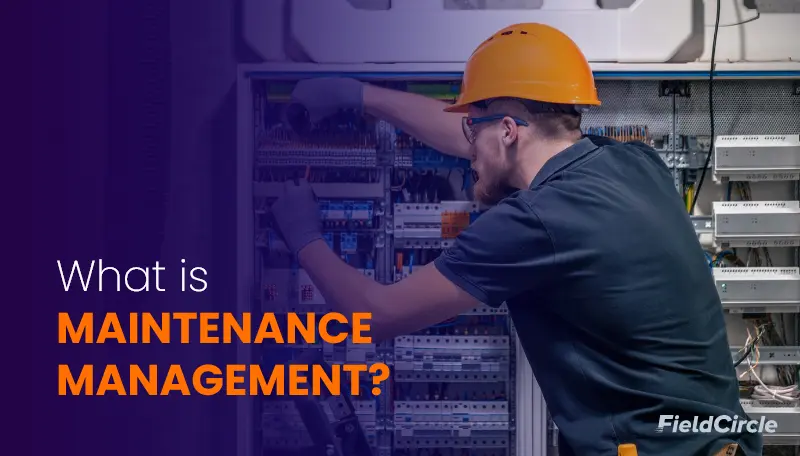
Maintenance management is the organized process of planning, executing, and overseeing maintenance activities to ensure the optimal performance, reliability, and safety of assets. It involves planning service schedules, managing work orders, tracking asset conditions, and analyzing performance data to reduce downtime and prolong asset life. Most organizations use maintenance software, such as a CMMS, to automate these processes, improve visibility, and centralize task execution across teams.
The purpose of maintenance management goes beyond routine repairs. Its core objectives include minimizing equipment failures, controlling maintenance costs, improving workplace safety, and ensuring compliance with industry standards. These goals are met through a range of strategies, including reactive, preventive, predictive, and reliability-centered maintenance. When these processes are poorly managed, organizations face significant consequences such as operational delays, increased repair costs, non-compliance risks, safety hazards, and faster asset deterioration.
To manage maintenance effectively, businesses must also understand their broader scope and operational challenges. This includes asset tracking, cost control, inventory management, and aligning maintenance with production schedules. Many organizations struggle with issues such as limited budgets, workforce shortages, outdated systems, and poor communication. Overcoming these obstacles requires adopting best practices like choosing the right maintenance strategy, setting clear KPIs, maintaining accurate records, and integrating maintenance activities with daily operations. A well-structured maintenance management system helps create a resilient, efficient, and data-driven maintenance environment.
Why is Maintenance Management Important?
Maintenance management is essential for ensuring the performance, reliability, and safety of equipment, facilities, and infrastructure. By applying scheduled and condition-based strategies, it reduces downtime, extends asset lifespan, lowers repair costs, and improves workplace safety. Industries like manufacturing, healthcare, utilities, and transportation depend on it to maintain productivity, meet compliance standards, and operate efficiently.
The following 7 factors highlight why maintenance management is fundamental to operational success:
What are the Objectives of Maintenance management?
The core objectives of maintenance management are to minimize downtime, extend asset lifespan, reduce maintenance costs, and improve operational efficiency. These priorities keep systems reliable and productive across their lifecycle. It also focuses on ensuring safety and compliance, using resources effectively, and enabling informed decisions through performance data. Together, these objectives help organizations maintain control, reduce risk, and align maintenance with business goals.
1. Minimize Downtime
Downtime reduction is a high-impact objective, particularly in manufacturing lines and logistics hubs where every minute of delay affects throughput and revenue. Maintenance management reduces such downtime through systematic preventive maintenance schedules, predictive diagnostics like thermal imaging for electrical panels, and emergency SOPs for critical asset failures. For example, an automotive plant that performs daily conveyor belt checks has reported a 15-20% improvement in overall equipment effectiveness (OEE). These actions ensure higher uptime, stabilize production targets, and reduce the mean time to repair (MTTR) across asset categories.
2. Extend Asset Lifespan
Asset longevity hinges on structured maintenance protocols and real-time performance monitoring. Organizations that conduct quarterly vibration analysis on rotating machinery or use telemetry data for fleet management significantly delay equipment degradation. For instance, oil and gas operators use SCADA (Supervisory Control and Data Acquisition) systems to optimize pipeline valve servicing intervals, preventing stress-induced failures. Accurate service logs and adherence to OEM-recommended intervals extend the usable life of machinery by 25–40%, cutting early capital replacement and maximizing return on investment.
3. Optimize Maintenance Costs
Cost optimization in maintenance operations requires smart budgeting, data-backed prioritization, and waste elimination. Maintenance management enables this by combining CMMS-driven cost tracking, failure rate analysis, and prioritization of critical assets for service. For example, a logistics firm using this structured approach for its forklifts reduced emergency repair costs by 30% while also cutting unnecessary inventory. With a centralized view of service history and cost allocation, budgeting becomes predictable, and decisions become resource-conscious.
4. Enhance Operational Efficiency
Operational efficiency increases when maintenance is synchronized with production, minimizing downtime and avoiding scheduling conflicts. By aligning maintenance with production cycles and using predictive alerts, plants can perform necessary service without interrupting output. High-volume industries like food processing leverage sensor data to time maintenance during routine cleaning, ensuring minimal disruption. For example, a bottling plant uses automated pressure sensor alerts to service fillers while keeping the line running. Integrating this data into ERP systems enables smarter resource planning, streamlines workflows, and reduces energy waste from uncoordinated operations.
5. Ensure Safety and Compliance
Safety and compliance objectives are mandatory in sectors where regulatory oversight and risk exposure are high, such as pharmaceuticals and aviation. Maintenance management supports these priorities by documenting all inspection activities, enforcing digital SOPs, and integrating compliance workflows into audit-ready platforms like CMMS. As reported in a case study published in Accreditation and Quality Assurance, a biopharma facility using electronic SOPs tied to CMMS audit trails can reduce audit deviations by 50%. Regular training, lockout/tagout enforcement, and scheduled safety drills minimize injury risk and help organizations meet ISO 9001 and OSHA 1910 standards consistently.
6. Improve Resource Utilization
Effective resource utilization ensures that tools, technicians, and materials are used to their full potential without overload or downtime. Through centralized work order management, skill-based task assignment, and RFID-integrated inventory management, maintenance management enables precise deployment of both human and material resources. For example, a hospital uses CMMS to assign biomedical staff based on real-time workload and asset criticality, ensuring ICU devices are prioritized. This approach reduces idle labor, prevents overuse of non-critical tools, and maintains system readiness.
7. Facilitate Better Decision-Making
Maintenance management plays a pivotal role in enabling strategic decision-making by providing access to comprehensive performance data and trend analysis. Through CMMS dashboards, organizations can monitor commonly used metrics such as Mean Time Between Failures (MTBF), Mean Time to Repair (MTTR), and maintenance cost per asset. These insights help identify chronic issues, evaluate technician performance, and forecast budget needs. At a packaging facility, leaders used downtime analytics to reallocate capital from low-yield machines to higher-performing units. By basing decisions on actionable data, maintenance teams can fine-tune preventive strategies, align resources effectively, and plan long-term investments with greater accuracy.
What are the Different Types of Maintenance?
The main types of maintenance are reactive, preventive, predictive, and reliability-centered maintenance, each designed to support asset performance and minimize failures based on specific operational needs. Reactive maintenance addresses issues after failure, preventive maintenance schedules interventions before breakdowns, predictive maintenance uses condition-monitoring tools to forecast faults, and reliability-centered maintenance prioritizes tasks based on asset criticality and failure impact. Understanding these types helps organizations reduce downtime, manage maintenance costs, and extend asset lifespan.
Reactive maintenance
Addressing issues only after failure occurs defines the core principle of reactive maintenance. It is typically used for non-critical, low-cost items where interruptions pose minimal risk to operations, such as replacing worn-out light switches or damaged furniture. While simple to implement, reactive maintenance often leads to increased operational disruptions due to its unplanned nature. The lack of foresight results in higher costs for emergency repairs and spare parts. This strategy is most suitable when downtime is acceptable, but it offers little control over maintenance spending and asset reliability.
Preventive maintenance
A widely adopted strategy in asset-heavy operations is preventive maintenance, which revolves around performing regular inspections and servicing based on predefined schedules. These intervals can be time-based, like monthly HVAC checks, or usage-based, such as oil changes every 3,000 miles. By addressing wear and tear before it leads to breakdowns, preventive maintenance reduces emergency repairs and promotes long-term equipment stability. It is a reliable and cost-effective method for managing predictable maintenance tasks across various sectors, from transportation fleets to commercial facilities.
Predictive maintenance
Modern facilities increasingly rely on predictive maintenance to fine-tune maintenance schedules based on actual equipment condition. This approach uses IoT-enabled sensors and data analytics to monitor real-time performance indicators, allowing organizations to predict failures with greater accuracy. Metrics like vibration analysis or temperature fluctuation help determine the optimal time for maintenance, minimizing unnecessary interventions. Although the initial investment in technology can be high, predictive maintenance improves resource allocation, reduces unexpected failures, and extends the operational lifespan of high-value assets.
Reliability-centered maintenance
In safety-critical industries, reliability-centered maintenance plays a key role by aligning maintenance efforts with asset reliability and operational importance. It involves analyzing failure modes and their consequences to determine which tasks are essential for maintaining functionality. This data-driven method helps prioritize high-risk components, ensuring resources are directed where they deliver the most impact. Reliability-centered maintenance supports organizations in balancing cost efficiency with system uptime and safety compliance, particularly in sectors like aviation, energy, and healthcare.
What Are the Consequences of Poor Maintenance Management?
Poor maintenance management results in longer equipment downtimes, escalating repair expenses, compromised workplace safety, and shortened asset life. It also increases the risk of compliance failures and disrupts productivity across operations. These outcomes collectively hinder operational stability and can lead to significant financial and reputational damage.
Below are the 6 major consequences of poor maintenance management.
- Increased Downtime
- Higher Costs
- Safety Hazards
- Reduced Asset Lifespan
- Non-Compliance Issues
- Decreased Productivity
- Increased Downtime:
Frequent equipment failures and unplanned service interruptions are direct results of inadequate maintenance, leading to prolonged downtime and operational bottlenecks. These delays reduce productive hours, impact service delivery timelines, and frustrate customers. In high-output environments, idle machinery not only lowers throughput but also drives reactive repair costs. According to IBM, unplanned downtime costs 35% more per minute than planned downtime, making it a major threat to revenue stability.
- Higher Costs:
Poor maintenance strategies lead to a cycle of reactive repairs and inefficient spending. Repeated breakdowns inflate the need for emergency services, which are often billed at premium rates. A Statista report indicates that maintenance budgets can reach up to 20% of a company’s operating budget, especially when preventive planning is absent. Delays in identifying underlying equipment issues contribute to prolonged downtime and unnecessary replacement of parts. Additionally, inefficient use of labor and poor inventory control further drive up costs, straining overall operational budgets and cutting into margins.
- Safety Hazards:
Neglecting routine maintenance increases the likelihood of sudden equipment failure, exposing workers to significant safety risks. Faulty machines, unserviced pressure systems, or worn electrical components can cause serious injuries or fatalities. These accidents can damage infrastructure and lead to operational shutdowns. Legal liabilities from safety lapses may result in lawsuits, compensation payouts, and regulatory penalties. The Health & Safety Executive reports that workplace-related injuries cost the UK economy £18.8 billion annually, underscoring the high financial and reputational risks of compromised safety standards.
- Reduced Asset Lifespan:
Without scheduled servicing and condition monitoring, equipment experiences rapid deterioration. Components wear out faster, leading to more frequent malfunctions and breakdowns. As a result, assets are retired prematurely, increasing capital replacement cycles and depreciation rates. CQ’s research shows that neglected maintenance can reduce asset value up to 20% faster than assets that are routinely maintained. The decline in equipment reliability also limits worker productivity and increases the likelihood of recurring operational disruptions.
- Non-Compliance Issues:
In industries governed by strict regulations, poor maintenance practices often lead to non-compliance with safety, environmental, and operational standards. Failure to conduct inspections or maintain accurate service records can result in fines, license revocations, or even forced shutdowns. For example, BP Products North America was fined $21.3 million by OSHA for serious safety violations. Beyond financial penalties, non-compliance damages stakeholder trust and tarnishes brand credibility, especially in sectors like healthcare, energy, and manufacturing, where reputational integrity is critical.
- Decreased Productivity:
Unreliable equipment performance directly affects worker output and process consistency. Frequent malfunctions cause disruptions in workflow, forcing staff to pause operations or switch tasks inefficiently. Deloitte estimates that maintenance-related breakdowns can reduce productivity by 5% to 20%, depending on asset criticality. This not only delays service delivery but also weakens employee morale and increases overtime costs. In fast-paced environments, such delays compromise service levels, hurt customer satisfaction, and reduce the capacity to scale operations effectively.
What is the Scope of Maintenance Management?
The scope of maintenance management includes asset management, work order handling, budget control, inventory oversight, compliance assurance, and integration with operations. These six core areas define how maintenance activities are planned, executed, and aligned with broader business objectives. A structured approach to these functions helps organizations improve uptime, extend equipment life, control costs, and meet regulatory requirements.
The 6 common scopes of maintenance management are given below.
- Asset Management
- Work Order Management
- Budget and Cost Control
- Inventory Management
- Compliance and Safety Management
- Integration with Operations
1. Asset Management
At the core of long-term equipment reliability and cost efficiency lies asset management, which oversees the tracking, performance monitoring, and lifecycle planning of all physical assets. Using asset management capabilities in CMMS, organizations can build detailed asset registries, schedule condition-based inspections, and determine optimal replacement timelines. For instance, utility firms use QR-coded tracking to monitor transformers and automate service schedules based on usage data. This approach ensures consistent uptime, smarter capital planning, and reduced asset-related failures.
2. Work Order Management
Smooth execution of maintenance activities depends heavily on work order management, which organizes how tasks are created, assigned, prioritized, and completed. Through work order management software, teams can manage workflows dynamically, enabling swift assignment of technicians based on skill, location, and urgency while capturing real-time updates. For example, in a high-traffic airport facility, mobile-enabled work orders allow HVAC servicing to be routed and resolved without manual coordination. This improves response times, enhances accountability, and streamlines task resolution
3. Budget and Cost Control
Financial sustainability in maintenance programs is anchored by budget and cost control, which track how labor, materials, and service expenses are allocated. Leveraging APM tools, teams can analyze cost per asset, identify recurring expense patterns, and forecast future repair or replacement needs. For example, a logistics provider reduced fuel system repair costs by 18% after analyzing failure frequency and shifting to predictive maintenance. This data-driven visibility supports better financial planning and ensures high-value return on maintenance investments.
4. Inventory management
Behind every responsive maintenance operation is inventory management, responsible for ensuring tools and parts are available when and where they are needed. Integrated with CMMS, inventory systems help monitor usage trends, trigger automated restocking, and prevent supply disruptions. In assembly-line manufacturing, RFID-tagged storerooms help track real-time part movement and availability. By maintaining balanced stock levels and reducing part shortages, inventory management supports continuous operations and cost-effective spare utilization.
5. Compliance and Safety Management
Maintaining operational integrity and meeting regulatory requirements depends on compliance and safety management, which governs how inspections, hazard controls, and standards enforcement are executed. CMMS platforms with compliance modules document every safety task, generate audit trails, and ensure adherence to frameworks like ISO 45001 or OSHA 1910. For instance, chemical plants rely on digitized checklists to validate safety valve inspections and avoid hazardous leaks. These systems protect both personnel and the organization from fines, incidents, and reputational damage.
6. Integration with Operations
To maximize operational uptime and reduce service conflicts, integration with operations aligns maintenance planning with production workflows. Collaboration between maintenance and operational teams enables shared scheduling, synchronized job execution, and real-time visibility into asset status through linked CMMS and ERP platforms. For example, in continuous processing plants, maintenance is timed with process cooldowns to avoid production delays. This unified approach reduces disruption, enhances efficiency, and fosters cross-functional alignment.
What are the Challenges in Maintenance Management?
Maintenance management faces several challenges that hinder its efficiency, ranging from labor shortages and limited budgets to outdated practices and poor communication. These obstacles can disrupt maintenance workflows, increase downtime, and prevent organizations from achieving performance, safety, and cost-control targets. Addressing these issues requires strategic investment in technology, training, and cross-functional alignment.
- Lack of Skilled Labor:
One of the most persistent barriers in maintenance operations is the lack of skilled labor, which directly affects task quality, service timelines, and overall equipment reliability. Many teams struggle to keep up with evolving systems due to limited training and technical gaps. For instance, facilities using building automation often face service delays because few technicians are proficient in digital interfaces. Investing in workforce development and using CMMS platforms to standardize workflows helps close these knowledge gaps and reduce technician overload.
- Insufficient Budget:
Financial limitations represent a significant challenge in implementing effective maintenance strategies, particularly when preventive and predictive models require upfront investment. A restricted budget often delays servicing, increases reactive repairs, and reduces long-term cost efficiency. For instance, a manufacturing unit postponing pump overhauls due to budget cuts saw system failures escalate operating costs by 20%. Tools like FieldCircle Maintenance Software can help monitor maintenance spending and support better financial planning to prioritize critical asset care.
- Outdated Processes:
Sticking with outdated maintenance processes, such as manual logs and disconnected task planning, undermines service accuracy and slows down operations. These issues grow over time, particularly in organizations scaling equipment volume without digital support. For example, a facility still relying on paper checklists for generator servicing struggled with data loss and compliance gaps during internal audits. Moving to a CMMS or EAM system enables digital task tracking, error reduction, and better long-term decision-making.
- Inefficient Communication:
Disjointed communication between teams is one of the most underrecognized challenges in maintenance management, yet it has far-reaching consequences. Without shared visibility into task schedules or priorities, teams risk duplicate work or missed service opportunities. A utilities firm, for instance, reported service delays after field technicians were dispatched without awareness of simultaneous system diagnostics already underway. Communication-integrated CMMS tools enable live updates, role clarity, and better coordination between maintenance and operations teams.
What Are the Best Practices for Effective Maintenance Management?
The best practices for effective maintenance management include applying the right maintenance strategies, building capable teams, adopting management software, tracking key performance indicators, documenting activities accurately, aligning with operations, and pursuing continuous improvement. These practices ensure that maintenance efforts are structured, proactive, and aligned with both operational needs and strategic goals.
- Implement appropriate maintenance strategies
- Set up an effective team
- Utilize maintenance management software
- Establish maintenance KPIs
- Maintain accurate documentation
- Integrate maintenance with operations
- Commit to continuous improvement
1. Implement Appropriate Maintenance Strategies
Selecting the right maintenance strategy is essential for balancing reliability, cost, and asset performance. Organizations should assess asset criticality, usage patterns, and failure history to determine whether preventive, predictive, or corrective methods are most effective. In many cases, a combined approach offers the best balance between immediate needs and long-term goals. Regular review and optimization of strategies ensure alignment with evolving operational demands. The main maintenance strategies include
- Preventive Maintenance: Regularly schedules inspections and repairs to prevent equipment failure.
- Predictive Maintenance: Use data and condition monitoring to anticipate and address potential issues.
- Corrective Maintenance: Resolves issues after they occur, suitable for non-critical assets.
2. Set Up an Effective Team
Building a capable and responsive maintenance team is key to executing tasks efficiently and safely. Setting up an effective team involves defining roles, assigning tasks based on technical expertise, and providing regular training. In facilities with rotating shifts, having role-based schedules ensures that no critical system is left unattended. Organizations often use skill matrices to map technician capabilities and assign work orders accordingly. This structured team setup improves service quality, accountability, and interdepartmental collaboration.
3. Utilize Maintenance Management Software
Using centralized tools like CMMS and EAM is essential to streamline task execution and asset oversight. When organizations utilize maintenance management software, they gain real-time visibility into equipment health, work order status, inventory levels, and service history. For example, CMMS can automate scheduling for HVAC servicing, send mobile alerts to technicians, and log completion data. These capabilities reduce manual tracking, enhance data accuracy, and support better decision-making across departments.
4. Establish Maintenance KPIs
Tracking and analyzing performance metrics is crucial to optimizing maintenance processes over time. Establishing maintenance KPIs such as Mean Time Between Failures (MTBF), Mean Time to Repair (MTTR), and asset availability helps identify inefficiencies and areas for improvement. Dashboards can visualize these indicators and highlight patterns, like a spike in repair frequency on specific machines, prompting preventive actions. Consistent KPI monitoring supports strategic planning, cost control, and service standardization.
5. Maintain Accurate Documentation
Effective maintenance programs rely heavily on accurate documentation to ensure traceability, compliance, and consistent service quality. Capturing real-time updates in digital work orders, inspection logs, and service reports allows teams to track performance history and verify task completion. In highly regulated industries, missing documentation can lead to audit failures or fines. CMMS streamlines audits by organizing maintenance records in a centralized platform, making it easier to demonstrate compliance and operational accountability.
6. Integrate Maintenance with Operations
Achieving seamless service delivery across departments requires organizations to integrate maintenance with operations. Scheduling maintenance around production cycles, shift changes, or downtime windows reduces conflicts and prevents service interruptions. For example, scheduling maintenance during line changeovers in packaging plants avoids output delays and improves overall system throughput. Shared systems like CMMS-ERP integrations help teams align resources and communicate schedules in real time, supporting uninterrupted operations.
7. Commit to Continuous Improvement
Long-term maintenance success depends on the willingness to adapt and evolve. Organizations must commit to continuous improvement by analyzing past performance, reviewing service feedback, and testing new tools or methods. Monthly reviews of maintenance KPIs, combined with team input, help refine SOPs and asset prioritization. Some companies adopt lean maintenance principles or reliability-centered practices to fine-tune their strategies over time, ensuring sustained operational value.
How to Get Started with Maintenance Management Software?
To get started with maintenance management software, organizations must first choose a platform that aligns with their operational goals, asset complexity, and service workflows. Selecting the right software is critical to maximizing maintenance efficiency, reducing downtime, and ensuring long-term asset reliability. A powerful solution like FieldCircle provides a complete suite of features, including work order management, asset maintenance and tracking, and preventive maintenance scheduling, all designed to streamline operations and improve service delivery.
FieldCircle’s maintenance software is especially well-suited for businesses in the field service industry, offering mobile accessibility, technician-based scheduling, and real-time task visibility. By consolidating maintenance activities into a centralized digital system, FieldCircle enables faster response times, better resource coordination, and full operational transparency across field and facility-based teams.