What is Maintenance Software? Everything You Should Know
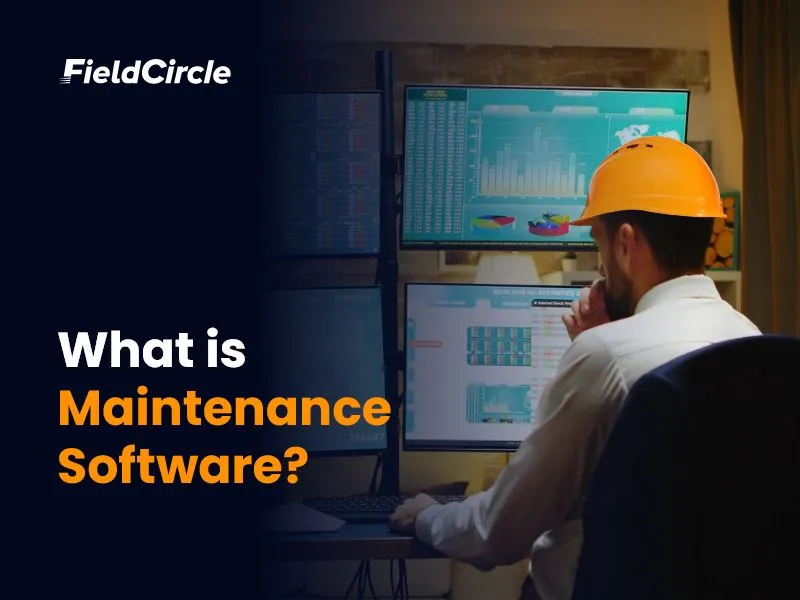
Maintenance software is a digital tool designed to plan, track, and manage maintenance activities for physical assets, equipment, or facilities. It helps maintenance managers, technicians, and operations teams automate tasks like preventive maintenance scheduling, work order management, inventory tracking, and compliance reporting to reduce downtime and extend asset lifespan.
There are different types of maintenance software, such as CMMS (Computerized Maintenance Management Systems) for general maintenance, EAM (Enterprise Asset Management) for enterprise-level asset control, and fleet maintenance tools for managing vehicle upkeep. These systems provide real-time data, improve maintenance efficiency, and ensure regulatory readiness across industries like manufacturing, transportation, and utilities.
By centralizing asset data, maintenance software automates key workflows across the organization. It registers each asset with service details and triggers work orders based on time, usage, or sensor input. Technicians receive alerts, complete tasks via mobile or desktop apps, and update the system in real time. This creates a continuous feedback loop that supports timely maintenance, accurate record-keeping, and improved equipment reliability.
What are the Objectives of Using Maintenance Software?
The 6 main objectives of using maintenance software in your system are stated below.
- Help reduce downtime
- Control maintenance expenses
- Plan preventive maintenance
- Monitor safety and compliance
- Manage people and process
- Organize reports and information
1. Help Reduce Downtime
Maintenance software helps reduce downtime by streamlining maintenance workflow and automating task scheduling. It provides real-time equipment tracking to monitor equipment status, detect issues early, and respond quickly to prevent failures and reduce repair delays. Through preventive and predictive maintenance, maintenance software helps avoid wear and tear and extend asset lifespan. As a result, it minimizes disruptions through preventive actions and boosts production efficiency.
2. Control Maintenance Expenses
Through proactive alerts and scheduled maintenance tasks, a maintenance application minimizes costly emergency repairs and downtime. Efficient scheduling and task automation optimize workflow processes to reduce overtime and unnecessary labor expenses. Using maintenance software, organizations can track warranties for timely claims, reducing repair costs and overhead expenses. It further optimizes inventory management to prevent overstocking of equipment and parts. Businesses thus need to purchase only essential spare parts, which helps minimize procurement and inventory costs and reduces storage.
3. Plan Preventive Maintenance
The process of planning becomes much more streamlined with maintenance software. Coupled with IoT-enabled sensors, it tracks equipment conditions continuously and makes it easy to schedule maintenance based on real-time data. The software creates automated triggers to send real-time alerts for maintenance tasks. It notifies the maintenance team to make a timely intervention based on predefined thresholds, such as temperature, pressure, or vibration levels, and maintenance performance metrics, like Mean Time Between Failures (MTBF) or energy efficiency rates. Also, it helps standardize procedures through checklists to ensure consistency and accuracy across all maintenance tasks.
4. Monitor Safety and Compliance
Organizations can easily track incidents using maintenance software to document and analyze safety patterns and address recurring issues effectively. The software uses automated checks to centralize compliance-related data, making it easy to verify industry regulations and legal standards. It also simplifies permit and audit management for seamless compliance. To that end, it organizes all necessary documents in a single accessible location, reducing operational delays and the risk of penalties.
5. Manage People and Process
Maintenance software manages people and processes by automating maintenance scheduling, task assignments, and resource allocation for efficient operations. It helps technicians organize assets, equipment, and documents to maintain asset information and maintenance records for easy access and management. With integrated collaboration tools, such as shared task boards, real-time messaging systems, and centralized document repositories, maintenance teams can communicate effectively and ensure cross-team collaboration for streamlined workflow.
6. Organize Reports and Information
Maintenance software organizes reports and information to generate automated maintenance and performance reports effectively. It monitors KPIs such as Mean Time to Repair (MTTR) and Mean Time Between Failures (MTBF) to evaluate production efficiency and outcomes. By maintaining detailed records of asset performance and maintenance, the software assists organizations in optimizing maintenance activities. Interactive real-time dashboards allow maintenance managers and supervisors to get instant insights into operation and equipment status.
What Features Should a Good Maintenance Software Have?
A good maintenance software should have these 10 key features.
- Work Order Management
- Asset Management
- Preventive Maintenance Scheduling
- Mobile Accessibility
- User-Friendly Interface
- Inventory and Spare Parts Management
- Integration Capabilities
- Compliance and Safety Management
- Reporting and Analytics
- Field Maintenance Management
1. Work Order Management
Work order management automates and digitizes work order creation by creating, tracking, and scheduling recurring tasks instantly with detailed task descriptions specific to dedicated team members. Generally speaking, traditional work order management relied on manual methods using pen, paper, and spreadsheets, which were prone to errors, delays, and inefficiencies. As against this, maintenance software streamlines the work order database for easy access to information, reducing delays, improving accountability, minimizing downtime, and controlling maintenance costs.
2. Asset Management
Tracking and managing assets through a centralized platform, asset management provides real-time data regarding asset specification, location, and usage. Asset management becomes more streamline with asset management capabilities in maintenance software that allow organizations to track performance. Preventive maintenance software includes inventory integration that provides detailed asset insights, helping maintenance managers and executives manage inventory, work orders, and schedule maintenance.
3. Preventive Maintenance Scheduling
Preventive maintenance scheduling via maintenance software automates task planning for recurring maintenance. It uses IoT-enabled sensors and data analytics to create automated triggers that send alerts for maintenance tasks based on thresholds like temperature, vibration, and water level. Maintenance technicians benefit from customizable schedules based on equipment needs and get auto-reminders and notifications for due tasks.
4. Mobile Accessibility
Mobile accessibility is another essential feature of maintenance software that helps create work orders, schedule maintenance, and access records from mobile devices. With this flexibility, maintenance technicians and supervisors can access task details, update work orders and log activity, schedule maintenance, and communicate with teams from anywhere. It also helps ensure seamless operations and increases overall responsiveness, making operations faster.
5. User-Friendly Interface
A maintenance software must have a good UI, as it makes navigation easy for all users. The interface should have clear drop-down menus and search functionality for seamless operation. Through intuitive dashboards, forms, and templates, maintenance software simplifies the workflow for creating and managing tasks and helps users access critical data quickly. To make the software more user-oriented, it should have customizable layouts and role-based access.
6. Inventory and Spare Parts Management
Another very important feature is inventory and spare parts management which provides organizations with a centralized database with detailed specifications and stock levels of parts and tools. It facilitates tracking inventory usage and stock location and helps automate the reordering schedule. Maintenance technicians receive real-time stock updates and low-stock alerts on maintenance software, reducing delays caused by a part shortage or unavailability. With a clear record of parts, maintenance software minimizes costs by avoiding overstocking or unnecessary purchases.
7. Integration Capabilities
There are various tools with which maintenance software must seamlessly integrate. A good maintenance software comes with strong integration capabilities and connects with external systems, such as enterprise resource planning (ERP), IoT devices, and analytics tools, to provide unified data management. Integration maintains a proper data flow and synchronization among integrated systems in real time for a consistent and seamless workflow and optimizes time by reducing manual data entry and enhances efficiency.
8. Compliance and Safety Management
A maintenance software provides a repository with all the necessary safety protocols, compliance checklists, and audit schedules through maintenance software. It automates tracking safety protocols and regulatory changes, documents incidents and corrective actions and manages permits and audits for compliance readiness. This minimizes operational disruptions caused by non-compliance and saves costs by reducing penalties. It also helps create a safer workspace.
9. Reporting and Analytics
Reporting and analytics are essential features of any maintenance tool. It must provide detailed reports on KPIs like Mean Time Between Failures (MTBF) and real-time maintenance costs through analytics dashboards. Maintenance software helps generate customized reports for asset performance and maintenance activities, finalize and share reports with stakeholders for review, and automate periodic reporting for timely insights. Through actionable insights, maintenance managers and supervisors can track progress and identify patterns and efficiencies to make quick and informed decisions.
10. Field Maintenance Management
In the context of field maintenance management, maintenance software provides mobile tools for field technicians to generate, assign, monitor, and dispatch field maintenance activities efficiently. It comes with GPS tracking and offline functionality that help delegate tasks to nearby field service teams, even with limited connectivity. This enhances response times, reduces downtime, improves resource allocation, and streamlines workflows and real-time communication for better productivity.
What Are the Different Types Of Maintenance Software?
Types of maintenance software range from simple maintenance work process management to complex systems that handle tasks beyond workflow management, like CMMS, EAM, APM, ERP, etc.
The 9 types of maintenance software are:
General Maintenance Software:
- Computerized Maintenance Management System (CMMS)
- Enterprise Asset Management (EAM) Software
- Work Order Management Software
- Asset Performance Management (APM) Software
- Enterprise Resource Planning (ERP) Software
Industry-specific Maintenance Software
- Field Service Management Software
- Aircraft Maintenance Software
- Fleet Management Software
- Facility Maintenance Software
- Computerized Maintenance Management System (CMMS):
- Enterprise Asset Management (EAM) Software:
- Work Order Management Software:
- Asset Performance Management (APM) Software:
- Enterprise Resource Planning (ERP) Software:
- Field Service Management Software:
- Aircraft Maintenance Software:
- Fleet Management Software:
- Facility Maintenance Software:
CMMS is a maintenance software that automates and streamlines the maintenance process. It helps maintenance teams manage work orders, schedule preventive maintenance, track assets, manage inventory, and organize detailed asset history. With a centralized maintenance data system, computerized maintenance management system (CMMS) optimizes equipment performance and lifespan, minimizes downtime and maintenance costs, and ensures safety and regulatory standard compliance, making it ideal for manufacturing plants, healthcare facilities, and utility industries. CMMS also streamlines audit processes and thereby assists in meeting compliances and regulatory requirements.
Providing comprehensive solutions for managing the lifecycle of physical assets across multiple locations, an EAM software application includes everything from planning, tracking, acquiring, optimizing, executing, and operating to maintaining, complying, and disposing of assets. Managing every facet of the physical assets allows EAM to maximize asset reliability and efficiency, reduce TCO, and enhance compliance and sustainability practices. This software best suits large enterprises like transportation, manufacturing, healthcare, and utilities.
Work order management software assists maintenance teams to create, assign, prioritize, schedule, and track work orders. It simplifies maintenance and operational tasks and helps businesses manage and track work orders to the end. It provides an automated system that replaces manual effort, improving task organization and overall productivity. Suitable for service-based SMBs, the software enhances communication and ensures timely completion of maintenance activities.
For monitoring, analyzing, and optimizing physical asset performance, you need asset performance management software. It uses predictive analytics, IoT data, and condition monitoring to prevent equipment failures and improve operational efficiency, asset performance, and reliability. It also reduces unplanned downtime and maintenance costs and provides data-driven insights for informed decision-making. APM is crucial for manufacturing and utilities, where equipment reliability is essential for productivity.
ERP software provides a unified system that integrates maintenance management with various business functions, including maintenance, finance, supply chain, sales, operations, and human resources. It supports scheduling, asset tracking, and resource planning to automate business processes for efficient resource allocation, cost control, and optimal performance. Organizations like manufacturing, construction, and logistics with diverse operations and centralized management needs require ERP software.
Also, there are maintenance software that are designed to support specific industries like:
A field service management software manages maintenance operations related to field service management. It includes scheduling, dispatching, tracking, and optimizing work orders for field technicians on customer sites or remote locations. Further, field service application helps monitor job progress, manage customer information, and manage field-based assets through GPS tracking, mobile access, and real-time updates. Suitable for telecom, HVAC, and utility industries, FSM software streamlines field operations and improves communication between field teams and office staff.
Aircraft Maintenance Software manages aviation-specific maintenance activities, focusing on operational demands and adhering to strict regulatory standards. It includes managing maintenance tracking, work orders, parts inventory, and inspection scheduling. The software provides real-time updates on maintenance works, integration with regulatory databases, and detailed audit reporting to ensure proper resource utilization and operational cost reduction. Dedicated to airlines, aviation maintenance organizations, and aircraft manufacturers, this software offers efficient maintenance planning to minimize aircraft downtime.
Logistics, transportation, delivery services, and rental companies use Fleet Management Software to monitor and maintain vehicles, such as trucks, buses, and delivery vans. It includes scheduling maintenance, tracking fuel usage, managing driver data, and adhering to necessary regulations. In further evaluation, the software integrates GPS and telematics to provide real-time vehicle condition and location insights. All these features are dedicated to optimizing vehicle performance, reducing maintenance costs, minimizing downtime, and enhancing operational efficiency.
For maintenance operations in property management, facilities including hospitals, schools, and large office complexes use facility maintenance software applications to efficiently manage building systems and infrastructures. For maintenance operations in property management, facilities including hospitals, schools, and large office complexes use facility maintenance software applications to efficiently manage building systems and infrastructures. It includes HVAC, lighting, plumbing, and workspace optimization. Whether it’s a property manager or a facility technician on the ground, the software allows organizations to manage work orders, schedule routine inspections, and track facility asset conditions. Doing so ensures safety, functionality, and energy efficiency in facilities while limiting operational costs.
Who Uses Maintenance Software?
Maintenance software is used by organizations with physical assets requiring regular maintenance. It is used in various industries, including healthcare, retail, manufacturing, utilities, and field service. Maintenance managers, supervisors, and technicians use maintenance software to track, plan, and schedule maintenance tasks of equipment.
What are Industry examples of Maintenance Applications?
The top 8 industry examples of maintenance applications are:
Healthcare
Generally speaking, healthcare sectors, including hospitals, diagnostic centers, pharmaceuticals, and laboratories, require maintenance software to ensure proper functionality and compliance of medical equipment and infrastructures. Maintenance software for healthcare helps manage and maintain medical device calibration, HVAC systems in clean rooms, and emergency power backups to minimize downtime and uninterrupted service delivery. One of the best ways to use maintenance software in the healthcare sector is to automate equipment maintenance schedules, track asset history, and maintain compliance with HIPAA, FDA, and ISO requirements.
Hospitality
Maintenance software for the hospitality industry focuses on achieving guest satisfaction and operational efficiency through timely resolution of issues associated with HVAC systems and elevators, proper maintenance of kitchen equipment, pool maintenance, communication systems, and other utilities. Since HVAC systems offer numerous benefits, hotels, restaurants, resorts, event venues, and the food and beverages sector rely on them. They require continuous operation of critical HVAC systems to offer a great ambiance and ensure guest comfort and joy. Best practices for software maintenance in the hospitality industry involve preventive maintenance scheduling, inventory tracking, and compliance management.
Retail
In the retail industry, the maintenance application helps supermarkets, shopping malls, standalone stores, and warehouses maintain their facilities and equipment for better customer experience, which can bring more profits. Some key components crucial for the retail sector include managing refrigeration systems, lighting, point-of-sale (POS) systems, security systems, HVAC, and display fixtures. One of the best ways to achieve asset reliability, energy efficiency, and enhanced customer experience using maintenance software is by integrating preventive maintenance scheduling, energy tracking, and asset lifecycle management.
Manufacturing Plants
Manufacturing industries like automotive, steel, cement, and textile plants, use maintenance software primarily to enhance operational efficiency by minimizing downtime, complying with industry-specific safety and quality regulations, and managing asset lifecycles to extend their lifespans and reduce repair costs. Best practices for using maintenance in manufacturing plants involve preventing downtime and increasing productivity by tracking asset performance, scheduling predictive maintenance for assembly lines, conveyor systems, and specialized machinery, and managing spare parts inventory.
Utilities
Utility industries like oil and gas and mining, use maintenance software to achieve service reliability through continuous utility delivery without interruptions. One of the best uses of maintenance software is to maintain transformers, substations, and grid infrastructures. The software also ensures the functionality of pumps, pipelines, and treatment facilities and monitors pipeline integrity and storage systems to prevent costly failures and maintain top performance and production.
Education
Schools, colleges, and universities use maintenance software to manage facilities, provide seamless communication between students and maintenance staff, and ensure a safe and conducive learning environment. The software allows the educational sector to maintain critical infrastructure like HVAC, lighting, and IT systems cost-effectively. It also optimizes maintenance budgets by scheduling timely repairs, which extends asset life. One of the best ways of using maintenance software for education is to follow preventive maintenance scheduling, inventory tracking, and compliance management to ensure safety and asset reliability.
Finance
In the finance industry, maintenance software guarantees complete system uptime by continuously providing financial services and ensuring the seamless operation of infrastructure and IT systems. Applications for banks, insurance firms, and stock exchanges involve managing ATM networks, backup power systems, and HVAC in server rooms for uninterrupted operations. A best practice for using maintenance software for the finance sector is implementing preventive maintenance schedules and tracking assets to enhance uptime with minimum delays.
Field Service
The field service industry, including HVAC, cleaning services, landscaping, construction, plumbing, and zoo maintenance, utilizes maintenance software to manage remote operations efficiently by dispatching real-time updates. One of the best ways to use maintenance software for field service is to optimize routes, manage mobile trucks, and track inventory for on-site repairs. It also includes using GPS-enabled features to assign tasks to nearby field technicians for faster response times and remote access of work orders for seamless operation.
Who Accesses Maintenance Software?
Maintenance managers, supervisors, technicians, inventory managers, and executives use maintenance software to plan, track, and schedule maintenance activities for equipment and physical assets. They also create work orders, monitor repairs, and review asset history.
Maintenance Managers
From planning and scheduling preventive maintenance, conducting inspections, and developing maintenance strategies to monitoring team and asset performance and managing a team of maintenance technicians, maintenance managers use maintenance software to administer the entire maintenance process. They are responsible for aligning maintenance with organizational goals. For example, a maintenance manager uses maintenance software to track and prepare a report on equipment downtime and operational costs to make data-driven decisions and optimize maintenance efficiency.
Maintenance Supervisors
A maintenance supervisor oversees daily maintenance activities and coordinates between management and maintenance technicians to ensure the overall repair works of systems and machinery for smooth operations. Their role includes assigning task orders, monitoring and reporting tasks, managing resources, ensuring quality control, and maintaining compliance with safety protocols. Skilled maintenance supervisors use maintenance software to schedule and assign tasks to maintenance technicians and monitor progress to ensure everything is completed on time.
Maintenance Technicians
Maintenance tasks, such as repairing, inspecting, installing, and maintaining equipment, systems, and buildings are performed by maintenance technicians through maintenance software. These works include electrical, plumbing, HVAC, and general maintenance. For example, a maintenance technician uses maintenance software to see work orders, track progress, and maintain maintenance activity records. It helps them perform routine checks, conduct repair works, and troubleshoot malfunctions to enhance uptime and boost production productivity.
Inventory Managers
Monitoring inventory levels, stocking and tracking critical parts, ordering spare parts and tools, maintaining part usage and location records, and optimizing inventory levels to reduce storage and inventory costs are key tasks performed by inventory managers with maintenance software. They are responsible for maintaining a proper supply of parts and equipment to support and streamline maintenance activities. An inventory manager uses maintenance software to track inventory supply and receive alerts for shortages so they can buy required inventory items in time to avoid operational disruptions.
Executives
They are responsible for making high-level decisions by analyzing KPIs like maintenance costs, asset utilization, and downtime metrics. They determine whether maintenance strategies meet organizational goals and evaluate the ROI of maintenance activities to prepare for future investments. For example, maintenance software can help CEOs set strategic priorities, CFOs monitor maintenance budgets, analyze cost savings, and allocate investments, and COOs align maintenance processes with performance objectives to support long-term goals and achieve operational efficiency.
What are the Challenges of Implementing Maintenance Software?
The challenges of implementing maintenance software can arise from organizational culture, cost of implementation, lack of training, or adaptability issues.
6 common challenges that occur while implementing maintenance software are given below.
- Employees Resistance to Change
- High Initial Cost
- Data Migration Issues
- Customization and Scalability Challenges
- Inadequate Training
- User Adoption Issues
Employees with little to no knowledge of maintenance software and its benefits may hesitate to use it. Their unfamiliarity and skepticism during the implementation phase can delay the entire process, leading to inefficiency and reduced productivity. To change employees’ resistance to change, it is necessary to offer hands-on demonstrations of maintenance software. The benefits, like reduced workload and improved efficiency, must be emphasized and clearly communicated. Their concerns must be appropriately addressed, and necessary support must be provided.
The high upfront costs of setting up maintenance software and integrating it with the existing system can strain an organization’s budget, especially SMBs. It can make stakeholders wary about long-term value and delay adoption. Organizations with doubts about their decision must start with tailored, scalable solutions and add features over time as needed. They must be given a clear picture of long-term ROI, highlighting how the software can reduce downtime, save costs, and increase productivity.
Issues can arise during the transition of historical data from legacy systems like spreadsheets and old software to new maintenance software. Incomplete data or incompatible data formats can make the process more complex and error-prone, leading to inaccuracies, loss of critical information, and an extended implementation period. To ensure a smooth data migration process, it is essential to conduct a detailed data audit to clean and organize existing records. Using an automated migration tool and planning a phased migration can help validate extracted data and maintain reliability.
While setting up maintenance software, it might not meet all organizational goals and may fail to scale as the business grows. This limits the effectiveness of software and increases operational costs and delays. Therefore, organizations must evaluate the features, customization options, and scalability options before implementation and choose the one that aligns with their business objectives.
When the training phase is rushed, and the functionality of maintenance software is not adequately addressed to the employees, it impacts the effectiveness of the software. This can lead to underutilization of the software, increased inefficiency, and failure to meet expected outcomes. To mitigate these issues, employee training must be rushed, and a comprehensive role-based onboarding process must be initiated. Employees should be offered continuous learning opportunities through webinars, in-app tutorials, and mentoring.
After implementing maintenance software, users might find it challenging to adapt to the new system and consider it complex and overwhelming. This approach can slow the transition, cause underutilization of software, and result in a low adaptation rate. It can also reduce inefficiency and ROI. To make the adoption process smooth, users must be provided with a user-friendly interface that makes it easy to use the new maintenance software. They must also be offered ongoing training and support to minimize complexity and assist in seamless integration with the existing system.
How FieldCircle Aligns with Modern Maintenance Needs?
FieldCircle Maintenance Software is a comprehensive maintenance software with features like work order management, asset maintenance and tracking, and preventive maintenance scheduling catered towards modern maintenance needs.
The intuitive and user-friendly interface, integration capabilities, and mobile accessibility provided by our tool make it suitable for every maintenance-heavy business. With FieldCircle, businesses can analyze real-time asset data to streamline maintenance processes, bring down costs, and enhance productivity.