A Brief History of CMMS and How It Changed the Maintenance Management?
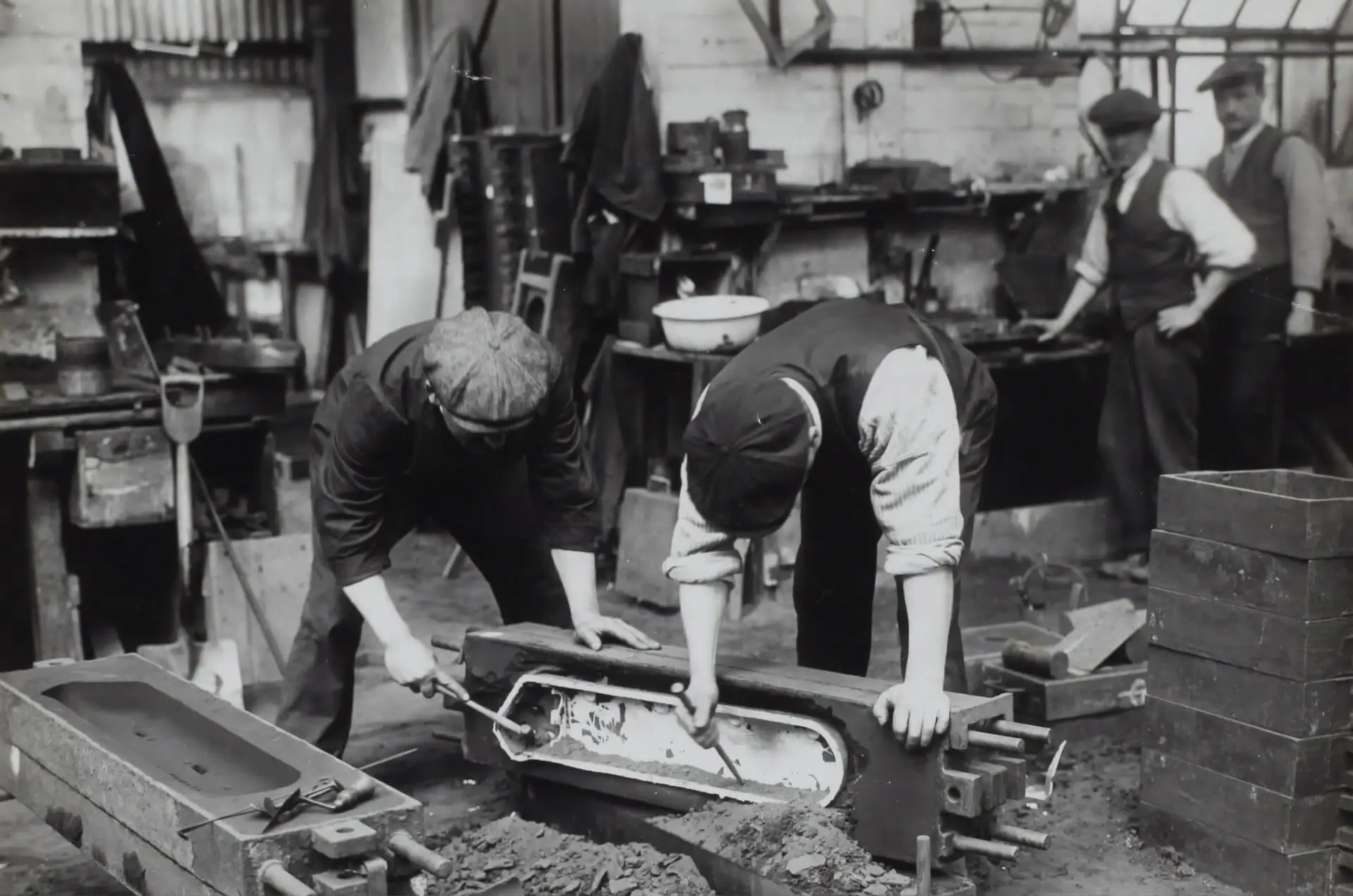
The brief history of CMMS unveils the rapid growth of accessibility and performance of maintenance management. The solution has become the standard software in many developing industries today; believe it or not, it is a 50 years old concept.
Different Generations of CMMS Development
CMMS has been around since the early generation of computers. In the 1960s, the first generation of maintenance solutions used punch cards running on IBM mainframe computers. The earlier version of this application was limited in usage and the expertise needed to run fundamental work orders. This system attracted large companies and government organizations to manage their service operations.
In the late 1960s, punch cards were replaced by computer terminals. The evolution of mainframe computers made the solution available to many organizations, but still, it is limited to large companies and government organizations who could afford the tool.
After the introduction of minicomputers in the late 1970s, service management evolved with increased capabilities allowing medium and large-sized industries that use CMMS. From the late 1980s to the early 2000s, the technological advancement of the personal computer paved the way for the growth of this platform.
The expanded ability to connect the PCs with the local area networks widened the usage of tool capabilities. After the 1990s, expressly, from 2000, we saw the tremendous evolution of the internet and cloud to drive maintenance. This is how the history of CMMS evolved and got its most significant breakthrough that could be available anywhere in the world with internet access.
This solution has come through the service operation in each industry, moving from the purchase or support model to the SaaS model. After the introduction of the fourth industrial revolution in 2010, computer networking capabilities emerged. When wireless and cellular technologies came, cloud-based solution was established. This is where the on-premise application model is replaced with the cloud-based one. With industry 4.0 technology, mobile service solutions have become commonplace, with IoT and AI as their significant contributors. This makes it more possible for users to place work orders, track progress, and order parts remotely.
Maintenance Management: Before and After CMMS
As businesses develop in size and complexity, managers feel pressured to handle the trends and demands. As a result, they are looking to operate smarter and wiser. This means the companies aim for a high return on investment, resulting from better time management, reduced cost, labor management, and extending the equipment life to improve operations. Businesses realize that management with paper and pencil shortfalls them in obtaining goals. Let’s look at management before and after CMMS overview and how they changed small and medium-scale industries.
Many companies started adopting management solutions after the development of computerized management applications. A CMMS can monitor and track the inventory, generate work orders with accurate reports, and, most importantly, provide preventive maintenance of the required assets.
The preventive maintenance approach provides the scheduled equipment checks, a valued aspect of the service program. Companies prefer to use it rather than a reactive approach. The reactive approach is addressed only when problems arise. This results in unexpected shutdowns and equipment failures.
Traditional maintenance management
Before the evolution of management solutions, maintenance management occurs through the manual spreadsheet method. This provides the limited ability to store data, and the manual input takes more time to process.
No real-time tracking
They cannot maintain the specific needs of the manufacturers, such as real-time data about the progress, tracking work orders, ordering parts and access to multiple users, and so on.
Reduced productivity
As the traditional method cannot alert or remind about the operation, the manager must do every function, including the routine check.
With these constraints, time, costs, resources, and staff allocations are done as needed, but this will not provide revenue to the company. The preventive program significantly reduces equipment breakdown and improves the equipment’s performance. This is where the traditional program fails.
The Perspective About the History of CMMS
The core functionalities and capabilities of robust maintenance management software mainly had stayed the same from earlier. The prominence of work orders, parts, assets, and acquisition has always been in the solution. The improvement happened in the aspects of reporting, analysis, and in mobile-based solutions. The future of such will be easier and more powerful with digital transformation. Augmented reality(AR) and virtual reality(VR) for service solutions will be implemented in the upcoming years.
We are simply moving away from reactive to preventive methods. Improved data types of usage metrics and conditions of the assets help to become more predictive. Now the application is more intelligent and accurate in managing operations. With the continuous development of technology, using artificial intelligence (AI) and machine learning (ML) gives more perspective to maintenance.
The Revamping Responsibilities of the Maintenance team
The role of the team has changed from every perspective. They are responsible for the development and success of the organization. The team, supported by platforms like computerized management solutions, uses a proactive approach to increase efficiency, reducing downtime, team safety, and inventory management in CMMS.
This proactive approach, empowered by the evolution of CMMS, allows managers to effectively prepare the factory for potential challenges and meet the demands of the industry.
CMMS: Preventive and Predictive
At last, introducing preventive management enhances facility management by making it possible to have regular checks on all the equipment. This avoids the disturbance and downtime to the manufacturer’s production cycle. All these developments made the tool more attractive to all types of industries. Predictive maintenance influences the IoT, where everything is monitored and connected.
Maintenance management
The service management program now differs from the spreadsheet or paper users in the early versions.
Automation
Once the platform is implemented, the tool automates all the operations by scheduling work order flows and tasks. The technicians are no longer holding paper records about works and parts orders. All these can be accessed with a single tap of the system, and the communications are done digitally.
Mobile CMMS
Accessing the application through mobile devices with camera and scanning capabilities provides real-time data to work wherever they are. This saves time and reduces errors.
Customization
The great benefit of today’s CMMS is the ability to adapt to the organization rather than the organization having to adapt to the platform. This means the application meets the requirements of every individual’s business, whether small or large, with different requirements. They can also change for the organization’s needs as they improve and reformulate.
Changes happen everywhere. The marketplace and economy allow the program to be raised as a management solution. The management approaches changed before and after the CMMS introduction. It is visible how this solution helps thousands of organizations make precise service operations with more profits.