What is Industrial Maintenance?
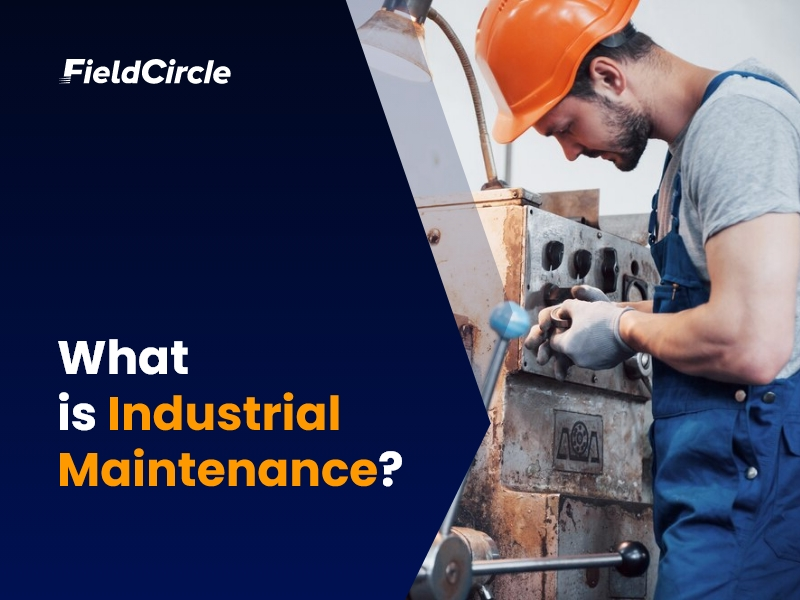
Industrial maintenance is the routine practice of maintaining and repairing equipment, machinery, and facilities used in industrial settings, such as manufacturing plants, power plants, and other production or utility facilities.
To interpret as per American Society for Maintenance and Reliability Professionals (SMRP), industrial maintenance is “the practice of protecting, controlling, and extending the life of physical assets to maximize their reliability, performance, and return on investment.”
Industrial maintenance is thus important to every equipment-heavy industry. May it be aerospace, manufacturing, energy, and oil and gas, industrial maintenance is a key function to sustain operational continuity and maintain safety. Due to its rising significance, the industrial maintenance market is expected to reach $85.8 billion by 2031 from $49 billion in 2021, with a CAGR of 5.6%.
However, the efficiency of industrial maintenance hinges on a multitude of factors, including skilled human resources, robust processes, and the integration of cutting-edge technology.
Given the vast scope of industrial maintenance, this blog aims to explore its various dimensions comprehensively. From different types of maintenance strategies to implementation scenarios across industries, we delve into various elements surrounding industrial maintenance.
Types of Industrial Maintenance Strategies
An industrial maintenance strategy caters to the unique needs and conditions of industrial equipment. Moreover, each strategy targets specifics of the maintenance operations. As a result, a comprehensive maintenance plan will be based on the following industrial maintenance approaches:
- Preventive Maintenance
- Predictive Mainteanance
- Corrective Maintenance
- Condition-based Maintenance
- Reliability-centered Maintenance
Let’s understand what these various types of industrial maintenance strategies mean.
-
Preventive Maintenance
Preventive maintenance is a proactive maintenance strategy where the maintenance team carries out scheduled inspections, servicing, and part replacements to prevent equipment failures. It relies on predetermined maintenance intervals or usage metrics to determine when maintenance activities should occur. Based on the patterns depicted by the maintenance metrics, the maintenance teams take necessary actions.
Maintenance activities are typically performed when the equipment is still operational and not exhibiting any signs of failure. The goal is to identify and address potential issues before they escalate into costly breakdowns. Lubrication, calibration, and component replacements are common operations carried out in the process.
As a part of preventive maintenance, in the manufacturing industry, industrial maintenance technicians regularly check conveyor belts for the right tension and alignment and lubricate machine bearings and motors so that there is no wear and tear.
-
Predictive Maintenance
This maintenance process rests on the power of AI-based predictive algorithms that harnesses power of data to predict equipment failures. The algorithms take real-time data from IoT sensors and monitoring systems installed on machinery and provide inputs to maintenance professionals through their results.
Predictive maintenance algorithms are particularly important as it detects early signs of wear, deterioration, or impending failure, and creates scope for maintenance teams to act in time. As a result, the maintenance function can achieve significant savings.
Monitoring the vibration levels of turbines to detect bearing faults in the power generation industry and using thermal imaging cameras for identifying overheating components in electrical substations, indicating potential failures are some ways predictive maintenance are applied. You can easily build a predictive maintenance program using a CMMS i.e. computerized maintenance management system.
-
Corrective Maintenance
Corrective maintenance is the process of addressing equipment failures reactively, usually after a breakdown has occurred. As a reactive maintenance strategy it helps diagnose the root cause of the failure and restores the functionality. This is a maintenance strategy executed on an as-needed basis and is unplanned, which is why it may also result in downtime and incur costs for repair.
In addition to addressing immediate issues, corrective maintenance also provides valuable insights into potential system weaknesses. For instance, maintenance teams are able to identify recurring failures or parts prone to malfunction, and use these insights to make informed decisions about upgrading components or refining their system design.
-
Condition-Based Maintenance
In condition-based maintenance, the maintenance team continuously monitors equipment condition and determines maintenance needs accordingly. A maintenance ecosystem comprising sensors and other monitoring devices is built to collect data on parameters such as temperature, vibration, and fluid levels. The data is then analyzed to identify deviations from normal operating conditions, to identify potential issues.
So, in an automobile manufacturing unit, maintenance workers will monitor the vibration levels of rotating machinery to monitor the function of the bearing. Similarly, in a data center, temperature and humidity sensors can be used to identify hot spots or airflow problems to check if equipment is overheating. Implementing condition-based maintenance strategy is one great way to reduce unnecessary maintenance costs and minimize the risk of unexpected equipment failures.
-
Reliability-Centered Maintenance (RCM)
Reliability is one of the important trends in maintenance digitization, which has given rise to ideas like reliability-centred maintenance. Based on reliability engineering, Reliability-centered maintenance (RCM) focuses on optimizing the reliability of critical assets.
In RCM, maintenance professionals identify the functions of each asset, determine the potential failure modes that can affect those functions, and select appropriate maintenance tasks to mitigate the risk of failure. RCM carries out equipment upkeep activities at the right time, using the most cost-effective methods, to maximize asset performance and minimize downtime.
RCM is common in high-stake industries such as aerospace. In an aircraft maintenance program, RCM gives insights on the critical functions of an engine such as its thrust and stability. Teams can analyze potential failure modes, such as turbine blade erosion and fuel system leaks and take actions for preventing these failures. So, the applicability of RCM extends beyond maintenance as it also exercises its importance in bringing safety to operations.
How To Create an Industrial Maintenance Strategy?
To create a robust industrial maintenance strategy that maximizes equipment performance and reliability, organizations can follow a structured process that combines various maintenance strategies. Here’s an enhanced breakdown of how to improve this process:
- Collect Downtime Data: Gather detailed downtime data and record instances of equipment failures, repair times, and associated costs. The information will help quantify the impact of downtime on production efficiency.
- Analyze Maintenance Value: This is like a what-if analysis where you calculate maintenance value by assessing the cost savings that you can achieve and revenue impact you can make through maintenance.
- Optimize Operational Variables: Identify areas for operational improvement to enhance maintenance productivity and reduce downtime, and thus improve the uptime. Fine-tuning every essential process, including equipment utilization, maintenance scheduling, and resource allocation.
- Utilize Advanced Tools: Implement predictive maintenance technologies like sensors and historical data analysis to forecast failures and prevent breakdowns. Leverage a computerized maintenance management system (CMMS) to track equipment history, schedule preventive maintenance tasks, and analyze maintenance data.
- Engage Machine Operators: Involve operators in basic maintenance tasks post-predictive maintenance implementation to ensure equipment longevity. Operators can lend their hand in routine inspections, minor repairs, and help apply a collaborative maintenance approach.
- Implement RCM Principles: Combine predictive, preventive, and proactive maintenance practices to minimize downtime and optimize equipment lifespan. Through cross-functional collaboration and ongoing evaluation, prioritize critical assets, analyze failure modes, and select maintenance tasks based on risk assessment.
What Are The Benefits of Industrial Maintenance?
Industrial maintenance comes with multiple benefits around equipment reliability, equipment lifespan, efficiency, downtime, product quality, compliance, and planning. Let’s understand these benefits, as discussed below:
-
Equipment Reliability and Safety
A staggering 97% of companies have experienced improvement in equipment reliability using predictive maintenance. By consistently keeping equipment in a perfect condition, maintenance sustains the flow of output from each machine in the entire operation. When the equipment is reliable, operators are assured of safety. So, a well-maintained forklift will work for a longer duration and also won’t pose any threats to its operators.
-
Improves Equipment Lifespan
Comprehensive maintenance strategies, including preventive measures like cleaning and parts replacement, increase machinery lifespan by 20%-40%, as timely repairs prevent wear and tear, and maximize equipment investment returns.
-
Improves Efficiency
The implementation of a preventive maintenance plan, service request totals dropped by an average of 13.4%, and 60% improvement in the average time to complete AC work orders. By maintaining machinery at peak efficiency, maintenance ensures faster and more reliable production processes, as proactive interventions assure uninterrupted operations.
-
Minimizes Downtime
Predictive and condition-based maintenance techniques anticipate potential issues, allowing proactive interventions and preventing downtime by 30%-50%. Real-time monitoring of equipment health identifies anomalies, which gives maintenance teams enough room to schedule interventions before failures occur, bringing down the unplanned downtime and ensuring operational continuity.
-
Maintains Product Quality
Industrial maintenance upholds product quality by ensuring that a piece of equipment operates within specified parameters. When maintenance personnel adhere to maintenance schedules and recommended practices, they naturally minimize the risk of product defects and deviations.
-
Facilitates Compliance
Adherence to maintenance schedules and safety protocols prevents violations and associated penalties. So, when organizations maintain equipment in the right state they carry out operations within the boundary of regulatory parameters, thereby upholding legal obligations surrounding workplace safety and environmental responsibility.
-
Aids in Financial Planning
Structured maintenance programs make maintenance costs predictable, aids financial planning, and optimizes budgetary allocation. In this process, preventative maintenance schedules minimizes the risk of sudden equipment failures and thus equipment operation becomes more efficient, thereby reducing the overall maintenance expenditures.
What Industries Rely on Industrial Maintenance?
Equipment-heavy industries like manufacturing strive to sustain service levels consistently. Maintenance is a key part of the service delivery framework. Since we have seen the viability of industrial maintenance in general, let’s proceed to know how it adds value across various industries.
- Food: Regular maintenance of meat grinders, slicers, dough mixers, and ovens by cleaning and calibration is a key process to keep operations streamlined.
- Refineries: Maintenance of pumps, valves, reactors, and distillation towers in an oil refinery.
- Energy: Wind turbines, gearboxes, reactor coolant pumps, and steam generators are maintained regularly.
- Construction: To adhere with the plan, tower cranes, hoists, asphalt pavers, and rollers are maintained for structural integrity.
- Automotive: Maintenance of robotic welders and conveyors in an automotive assembly is a regular activity in the automotive industry.
- Aerospace: Jet engines and avionics systems at an aircraft maintenance facility are regularly maintained for diagnostic testing and component overhaul.
- Manufacturing: Maintenance of surface mount machines, reflow ovens at an electronics manufacturing and maintenance of tablet presses and encapsulation machines are some common examples in the industry.
Common Industrial Maintenance Professionals
Due to the complex nature of the task, the industrial maintenance process comprises a diverse range of tasks and responsibilities, demanding the presence of these different types of professionals so that the maintenance strategy can be implemented in a holistic manner.
-
Industrial Engineer
The roles and responsibilities of industrial engineers are centered around optimizing production processes and systems to maximize efficiency and minimize waste. Bringing practical exposure to and relevant qualifications in industrial engineering, they apply the latest theories and principles to design and refine production systems.
-
Maintenance Planner / Maintenance Schedulers
They come at top in the hierarchy of the maintenance department, and collaborate with the top management to build strategy for overall maintenance operations. Building a holistic plan for maintenance operations, they build the budget for maintenance while considering the overall resource requirement.
-
Maintenance Manager / Maintenance Supervisor
These are senior team members in the maintenance department who oversee the team of maintenance technicians. Acting as an interface between maintenance planners and maintenance technicians, they facilitate the implementation of the outlined maintenance strategy.
-
Maintenance Technician
Performing one the most important industrial maintenance jobs – that of directly resolving maintenance issues, industrial maintenance mechanics bring hands-on expertise in repairing, maintaining, and troubleshooting industrial machinery and equipment and play a key role in ensuring smooth operation of manufacturing and processing plants.
-
Automation Specialist
With the increasing use of automation in industrial maintenance, the presence of automation experts is becoming fundamental to designing, implementing, and maintaining automated systems for improved equipment health monitoring, issue diagnosis, and maintenance process optimization.
-
Reliability Specialists
As specialists, they focus on improving asset reliability through data analysis, failure mode and effects analysis (FMEA), and reliability-centered maintenance (RCM) techniques. They execute the key process of identifying potential failure modes, develop strategies to mitigate risks, and implement predictive maintenance programs to anticipate and prevent equipment failures.
Certifications and Training of Industrial Maintenance
By serving as invaluable tools for validating expertise, ensuring adherence to quality standards, the following certifications play a pivotal role in industrial maintenance.
- Certified Maintenance and Reliability Professional (CMRP)
- International Maintenance Institute (IMI) Certification
- Certified Maintenance and Reliability Technician (CMRT)
- Certified Plant Maintenance Manager (CPMM)
- ISA Certified Automation Professional (CAP)
Businesses with industrial maintenance as a key function must invest in these certifications. Below we explain more about their relevance in the sector:
-
Certified Maintenance and Reliability Professional (CMRP)
Improving equipment efficiency and reducing operational risks are crucial in industrial maintenance, and CMRP certification validates expertise in these areas. Recognized worldwide, it demonstrates proficiency in asset management, reliability engineering, and maintenance optimization. Professionals with this credential are equipped to implement cost-effective strategies that minimize downtime and extend asset life cycles.
-
International Maintenance Institute (IMI) Certification
A broad understanding of maintenance principles across industries is essential for ensuring reliability in industrial operations. IMI Certification highlights a professional’s ability to manage preventive maintenance, diagnose equipment failures, and implement long-term reliability strategies. It serves as proof of competence in industrial maintenance, helping professionals reduce unplanned downtime and improve operational efficiency.
-
Certified Maintenance and Reliability Technician (CMRT)
Technicians responsible for industrial maintenance must possess strong troubleshooting skills and in-depth knowledge of equipment reliability. CMRT certification validates these abilities, ensuring professionals can handle repairs, identify failure patterns, and maintain physical assets effectively. Industries that rely on uninterrupted operations benefit greatly from certified technicians who can prevent costly breakdowns and extend equipment longevity.
-
Certified Plant Maintenance Manager (CPMM)
Managing maintenance operations in industrial plants requires leadership, strategic planning, and technical expertise. CPMM certification provides professionals with the necessary skills to optimize maintenance programs, improve resource allocation, and implement proactive maintenance strategies. Those holding this certification can significantly enhance plant productivity by reducing equipment failures and streamlining maintenance processes.
-
ISA Certified Automation Professional (CAP)
Automation plays a critical role in industrial maintenance, making CAP certification valuable for professionals working with control systems. Covering system design, implementation, and maintenance, it ensures that automated processes function efficiently with minimal disruptions. By earning this credential, professionals can enhance system reliability, reduce maintenance costs, and contribute to the seamless operation of industrial automation.
To Wrap Up
Undoubtedly, industrial maintenance is the cornerstone of operational success in modern industries. While this was a fair knowledge delivery, remember that the adoption of advanced technologies like Computerized Maintenance Management Systems (CMMS) will bring immense improvements in your maintenance processes and asset performance.
So, as a business seeking to optimize its maintenance operations, connect with us to have a cutting-edge CMMS solution specifically tailored to meet your business’s diverse needs. By embracing the power of technology through a CMMS, you will be able to build and implement an infallible maintenance strategy.