How to Prepare a Maintenance Budget Flawlessly: A Detailed Guide with Template
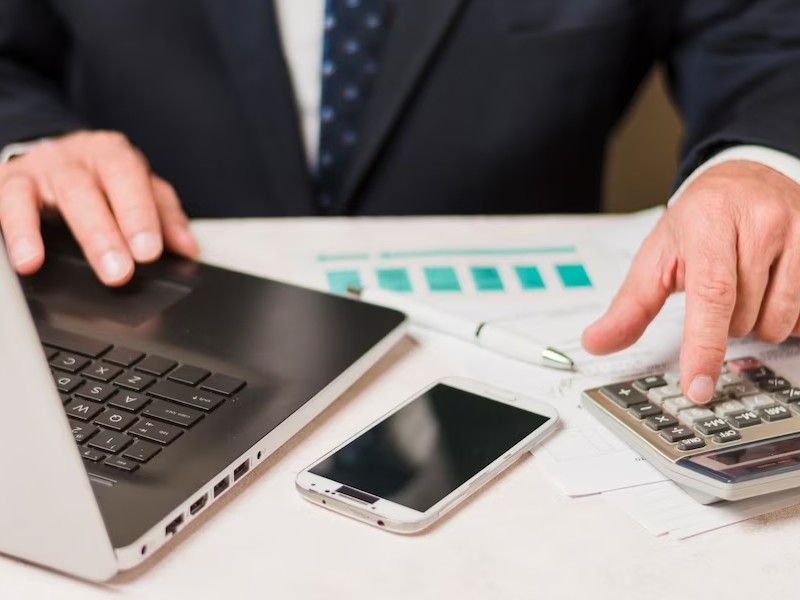
You start planning your maintenance budget, only to face challenges right from the start leading to confusion, overwhelm and frustration. This is why most facilities directors and facilities CFOs find setting up and preparing a facilities maintenance budget the most daunting task.
While issues like missed entries of important expenses like replacement parts or specialized tools when planning your budget can lead to budget problems and equipment failures later, being overly cautious and setting aside too much money for maintenance can mean wasting resources that could be used elsewhere.
It’s like choosing the most important pieces of the puzzle. You must consider how long each piece will last and the impact if it breaks down.
And unexpected breakdowns or urgent repairs can strain your budget, leaving less money for planned maintenance.
So, how do you plan for such events? How do you prepare a maintenance budget for your facility that can help you achieve your operations goal while not putting pressure on resources?
In this post, we will take you through a step-by-step guide on how to prepare a maintenance budget and the maintenance budgeting best practices that you should follow. Before that we will shed light on the idea of maintenance budgeting and its importance. This will act as your trusty roadmap to budgeting success. At the end of the post, we have also provided a free downloadable maintenance budget planning template that will help you explore how to calculate maintenance budget. You may download it and play around. Let’s dive in.
What is Maintenance Budgeting?
Maintenance budgeting is the process of allocating planned financial resources for scheduled maintenance and inspection of equipment, infrastructure, and facilities within a defined fiscal cycle. It lays out clear spending priorities, supports structured planning, and sticks to predefined operational timelines and standards.
Why is Maintenance Budgeting Important?
Maintenance budgeting holds the reins when it comes to financial discipline in maintenance and inspection operations. It sets a clear boundary for expenditure. Organizations can assign the right amount of funds without going overboard or cutting corners. It is a hallmark of a good organization to have a planned maintenance budget for managing costs effectively, and those with structured budgets report fewer unexpected failures.
With a defined budget in place, maintenance and inspection tasks follow a structured course. There is no arbitrary spending as there is optimal allocation of resources, which is why businesses get the job done without burning a hole in their pocket. A practical maintenance budget example would be allocating fixed quarterly funds for routine maintenance inspections while reserving a separate contingency amount for emergency repairs, so that there is predictable and balanced spending throughout the year.
Use Equipment Cost as Your Baseline:
One of the less obvious facets of maintenance cost is equipment cost, which involves everything from spare parts to brand-new assets.
When considering equipment cost, you should also factor in the expenses associated with servicing the equipment, whether done by your maintenance team or the equipment vendor.
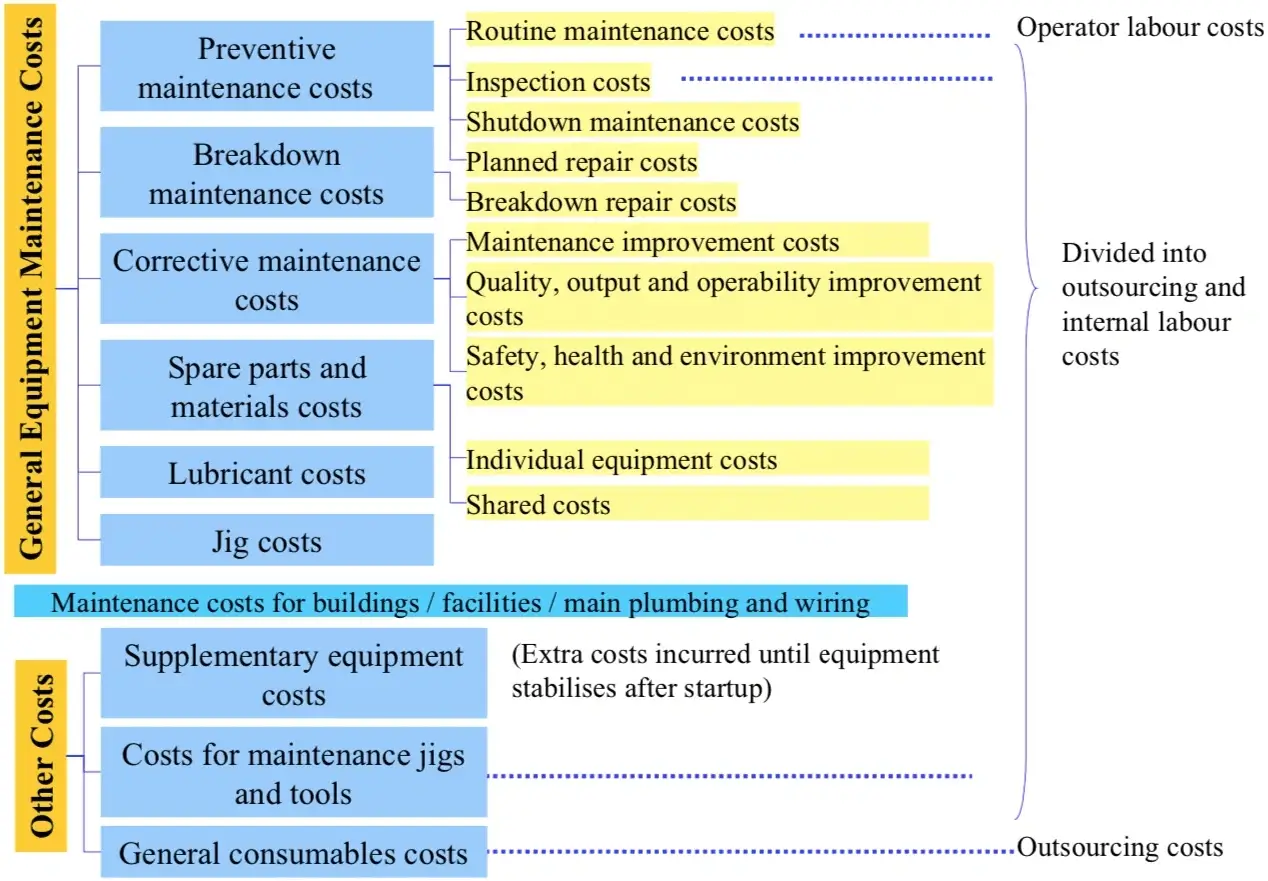
Source: LearnManufacturing
It’s a critical aspect of budgeting.
One way to quantify equipment cost is by comparing maintenance cost (MC) to the replacement asset value (RAV) of your equipment, expressed as a percentage (%RAV). In this case maintenance cost vs replacement asset value analysis becomes important.
Note*: The world-class standard for %RAV falls from 2% to 5%, as per Baker Hughes study. This percentage allows maintenance planners to estimate the required funds for equipment maintenance, ensuring it remains within a reasonable proportion of the asset’s value.
By utilizing %RAV as a guideline, you can gauge the appropriate allocation of funds for upkeep of the equipment. Keeping maintenance costs within the recommended range helps prevent overspending and ensures a balanced budget.
Assess Equipment Installation and Construction Expenses:
So, imagine you’re standing there, scratching your head, trying to figure out how much dough you should shell out for construction costs.
It’s like solving a financial puzzle but with a twist.
You’ve got to gauge how much installation and construction your facility actually tackles. Are you in the “moving offices and installing shiny new equipment” club? Or are you more of a “steady as she goes, minimal changes” kind of manager?
Here’s the deal: The more changes and upgrades your facility undergoes, the higher the costs.
But understanding this crucial puzzle piece helps you see the bigger picture. For instance, if you have a dedicated team of eight individuals who work 12-hour shifts five days a week, you’ll likely encounter overtime situations that require additional compensation. But what if you had a larger team, say, 12 people?
In that case, you can minimize overtime and reduce the money you’ll need to allocate for construction maintenance costs.
Gather the Right Information!
Let’s say you’re managing a facility with various assets, and you’re tasked with setting up a maintenance budget. You review the CMMS reports and discover that a particular HVAC system has required frequent repairs over the past year. The CMMS data shows that it has generated ten work orders costing $8,000.
Armed with this information, you can identify a pattern and understand the maintenance needs of that specific asset.
Considering that data, you can allocate a portion of your budget towards preventive measures for the HVAC system, such as regular maintenance and component replacements, to reduce future breakdowns and associated costs.
The CMMS helps you estimate the expenses more accurately and supports your decision to prioritize proactive maintenance for critical assets.
As Robert Peffen from ManagementResources Group summarized, “One of the most effective ways to control the maintenance budget is to identify and eliminate recurring reliability and maintenance problems. To accomplish this, the data on maintenance work performed must be collected and analyzed. The identified “bad actors” should be ranked according to the severity of impact to the business. ” It is here that tools like CMMS can prove quite useful.
Get Your Ratios Right For Resource Allocation
You know, every industry has its own set of standards when it comes to labor, inventory, and materials ratios. It’s like a secret recipe for success! But don’t worry if you’re not familiar with these ratios yet. A quick Google search can be a real lifesaver!
Let’s say you’re running a restaurant. In the restaurant industry, the labor, inventory, and materials ratios can vary depending on the type of establishment.
For instance, a fast-food joint might have a 30% to 40% labor ratio, meaning that around 30% to 40% of the total expenses go towards paying the staff. On the other hand, a fine dining restaurant might allocate a higher percentage, say 45% to 50%, to ensure top-notch service.
When it comes to inventory, let’s consider a bakery. They follow a 20% to 25% ratio for materials, meaning that roughly 20% to 25% of their expenses are dedicated to purchasing ingredients like flour, sugar, and butter. On the other hand, a tech company manufacturing computer hardware might have a lower materials ratio, around 10% to 15%, as its primary focus is on costly electronic components.
Once you’ve got the industry standard ratios, it’s time to do a little digging. Look at your budgets from the past few years and see if you’re exceeding those ratios. If you are, it’s time to shake things up a bit. By making some changes, you can boost your profit margins and cut maintenance costs.
But remember, every industry has its own considerations. Each industry has its unique set of standards, practices, and ratios that determine the ideal balance of resources and costs.
For example, a high-speed manufacturing plant might aim for a labor and materials ratio 50:50. On the other hand, a custodial business may lean more towards 85% labor and 15% materials. It’s all about finding the right rhythm for your work.
And here’s a little tip for you when it comes to materials and inventory. Not all buildings need special inventory requirements. Take, for instance, an elementary school — no need for regular turnover of inventory there. Instead, vendors can simply deliver materials as they’re needed.
Now, let’s get down to hiring and labor costs. It’s time to determine how much you’ll spend on your fantastic workforce. First things first, you need to know the direct labor rate. That’s the amount you’ll pay your workers, excluding fringes and benefits.
Next up, we have the ever-elusive fringe benefits. These sneaky costs can be quite hefty, usually averaging 30 to 40 percent of the base salary. But if your company isn’t big on fancy benefits, you can expect that percentage to drop to around 22 to 25 percent.
Finally, don’t forget about overhead costs. This includes supervision, managers, office supplies, computers, and good ol’ payroll. It all adds up.
Plot And Present Your Maintenance Budget Journey
Designing and presenting your comprehensive building facility maintenance budget planning is no easy task, but it’s essential for the success of your facility. Take a moment to consider the insights provided in the diagram below. It’s like a roadmap that connects different elements and helps you navigate through the budgeting process.
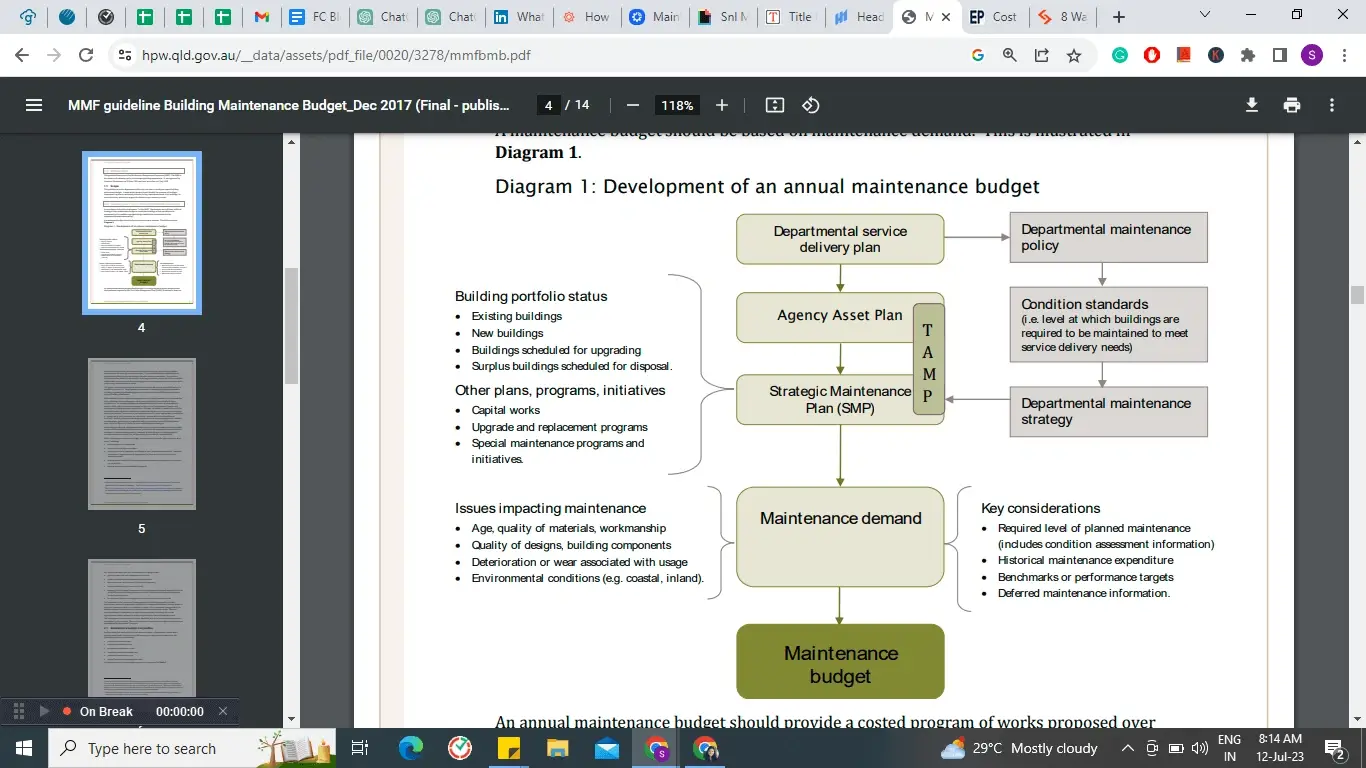
Source: Maintenance Management Framework Queensland Government
As you develop your budget, think about how it aligns with your departmental service delivery plan, asset strategic plan, and the condition standards you aim to maintain. Remember, it’s not just about numbers; it’s about meeting your facility’s needs and ensuring its long-term sustainability.
Now, let’s talk about presenting that budget. And here’s where the power of budgeting for maintenance comes into play. You can simplify the entire process by utilizing a maintenance budget template within a computerized maintenance management system (CMMS).
Imagine yourself in front of your stakeholders, armed with a good CMMS software that simplifies data management. With the help of the CMMS-generated reports, you can paint a clear picture of maintenance needs, cost trends, and the impact of your proposed budget allocations. It’s like having solid evidence to back up your decisions.
But don’t forget the human element. Communication is key. Tailor your message to different audiences, showing them how the budget aligns with their interests and priorities. Engage them throughout the presentation, creating a sense of collaboration and ownership.
Track Your Budget to Stay on Course!
Tracking and monitoring your maintenance budget is crucial to ensure compliance and make necessary adjustments. Most times leaders don’t know what’s consuming the maintenance budget and thus, as a maintenance manager, facility manager, or operations manager, it’s essential to establish effective systems for expense tracking and maintain flexibility in budget management.
While putting together a carefully crafted maintenance budget, you might have often realized that ensuring compliance without tracking expenses is challenging. Establishing a system for expense tracking allows you to keep tabs on where your budget is being utilized, identify any deviations, and ensure that expenses align with the allocated funds.
The power of regular budget review cannot be underestimated. By monitoring budget deviations, you gain valuable insights into how well your budget is performing. It helps you identify areas of overspending or underspending, enabling you to take corrective actions and make informed decisions for future budget cycles.
Flexibility is key in budget management, especially when needs and priorities change. By staying adaptable, you can adjust your budget when unforeseen circumstances arise, or new opportunities emerge. This flexibility ensures that your budget remains relevant and responsive to the evolving needs of your facility or organization.
Consider implementing a Computerized Maintenance Management System (CMMS) to streamline these processes. A CMMS can automate data collection, simplify expense tracking, and provide real-time insights into your budget’s performance. By leveraging the power of a CMMS, you can efficiently track and monitor your maintenance budget, ensuring compliance and making informed adjustments as needed.
Leave Room for Changes!
When prepping your budget, let’s not forget one super important step: leaving room for changes. Why?
Life has a funny way of throwing curveballs at us, and maintenance is no exception!
For instance, consider a scenario where with an initial capital of $300 million. A portion of this funding, $100 million, was specifically allocated for refurbishing the bank’s headquarters building. As part of the renovation, exquisite marble was installed on the walls, resulting in a beautiful and seemingly perfect outcome.
However, the bank’s managing director later expressed dissatisfaction with the chosen marble and decided to have it completely replaced. Naturally, this unexpected change incurred substantial costs.
Examples like this highlight the importance of anticipating and accounting for such changes when developing a budget for maintenance.
By leaving room for changes in your maintenance budget, you can ensure you have the resources available to address unforeseen circumstances, modifications, or updates that may arise during the maintenance process. This flexibility allows for effective budget management and enables you to respond promptly to evolving needs, ultimately promoting overall efficiency and success in your maintenance operations.
Embrace Technology
As a maintenance, facility, or operations manager; you know the challenges of managing budgets effectively while juggling numerous responsibilities.
Imagine this scenario: you’re tasked with creating a maintenance budget, but you’re overwhelmed with manual data collection, scattered spreadsheets, and time-consuming analysis.
That’s where technology comes in. You can streamline your budgeting for maintenance and unlock valuable insights by harnessing the power of best facility maintenance software,
With a computerized maintenance management system (CMMS), you can automate data collection, track maintenance activities, and capture costs. No more digging through piles of paperwork or struggling to compile information from various sources. The software does the heavy lifting, saving you time and effort.
But the real magic happens when you leverage the data generated by the CMMS. You can analyze historical maintenance information, identify trends, and make data-driven decisions. Understanding past performance allows you to optimize your budget allocations and prioritize maintenance activities more effectively.
Furthermore, technology empowers you to collaborate seamlessly with your team and stakeholders. You can easily share budget information, track progress, and align everyone toward common goals. This fosters transparency and accountability, creating a more collaborative environment for budget planning and execution.
Please Sell It to the C-Suite.
As a facility manager, you know that presenting the facility maintenance budget to the C-suite can be a daunting task. It’s crucial to convey its value, justify costs, and highlight the benefits in a relatable and introspective manner.
Let’s explore how you can gain the support of the C-suite by showcasing your thorough preparation, contingency planning, and linking the budget to tangible workplace outcomes.
- Emphasize Value and Benefits:
Reflect on how well-maintained facilities positively impact your team’s productivity, their sense of safety, and, ultimately, customer satisfaction. You can demonstrate the importance of allocating resources to maintenance by showcasing these benefits.
- Justify Costs:
And here’s the heart of it all: justify your allocations. Explain how your budget decisions will optimize maintenance activities, improve equipment reliability, and enhance operational efficiency. By demonstrating the value and impact of your budget, you’re not just crunching numbers – you’re building a strong alliance with your stakeholders.
- Thorough Preparation and Contingencies:
Share your meticulous approach to maintenance budget preparation. Highlight how you have analyzed historical maintenance data, identified trends, and used this information to forecast future expenses accurately. Emphasize your inclusion of a contingency fund to handle unexpected repairs and emergencies, showcasing your preparedness.
- Link Budget to Workplace Outcomes:
Connect the dots between the maintenance budget and the tangible outcomes it brings to the workplace. Reflect on how well-maintained facilities enhance employee morale, increase operational efficiency, and ultimately contribute to the company’s profitability. Help the C-suite envision the positive impact on their bottom line.
- Track and Communicate Results:
Again, put yourself in the C-suite’s shoes and recognize their need for transparency and accountability. Commit to regular reporting, sharing actual expenses, progress made towards maintenance goals, and any deviations from the budget. Show them you are a responsible steward of resources and a reliable communicator.
Streamline your Maintenance Budget Planning with FieldCircle
Budget is a key tool for maintenance cost management and when it comes to facility budgeting, there’s no one-size-fits-all strategy. It all depends on your facility’s unique needs and your company’s budget capacity. While guidelines can provide direction, the final numbers and budgets are yours.
Collecting relevant data may take time, but it’s worth the effort. Establishing and testing your budgeting process might require adding tools like a CMMS system or specialized software. Once your systems are in place, the benefits will extend for years.
Implementing tools like FieldCircle streamlines your maintenance processes and optimize your budget. By prioritizing preventive maintenance, regular inspections, and leveraging modern technologies, you can enhance performance, extend asset lifespan, and ultimately save costs in the long term.
So, let’s embrace the power of budgeting for maintenance and ensure the efficient operation of your facility for years to come.