What’s Eating Your Facility’s Budget: 15 Things that You Shouldn’t Overlook
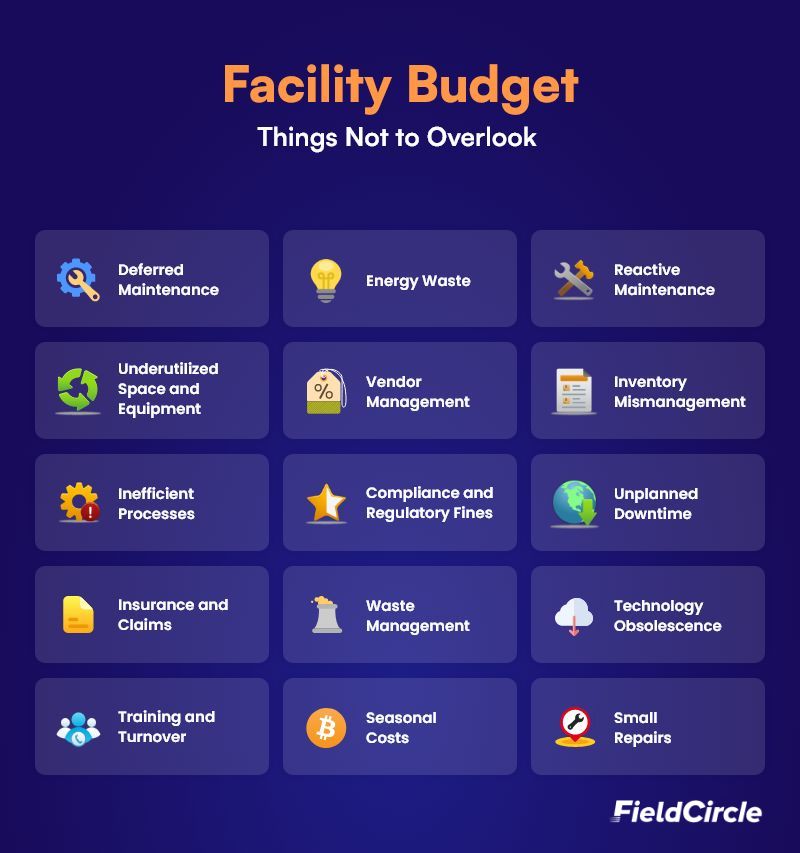
A budget is a key financial tool for any facility, guiding it towards financial stability through planning, reviewing, and adjusting revenue and expense streams.
However, facility budgets can face unexpected hits due to various factors that don’t always appear on the radar. These hidden or less obvious areas can silently consume the maintenance budget. They disrupt the balance by creating a self-perpetuating cycle where emergency and unplanned costs drive up the total cost of ownership (TCO) and leave facility managers caught unprepared.
It’s relatively easier to optimize things if the teams have clarity of what’s consuming their facility’s maintenance budget, where are the leaks and what to optimize but things become trickier when they don’t have visibility of these aspects.
FieldCircle is used by leading organizations and maintenance professionals and in the course of our engagement and conversation with them, we have identified these hidden areas in facility management practices that can take a toll and consume facility budgets and why facility managers must be proactive about them. Let’s jump in.
1. Deferred Maintenance
Postponing maintenance due to budget constraints can lead to higher repair costs over time. What may seem like savings in the short term can result in costly emergency repairs or equipment replacements later on, and consume your maintenance budget.
Denver International Airport is a classic example of how deferring maintenance can come with costs. With poor facility maintenance practices, the airport has struggled with a backlog of over 7,000 maintenance tasks. A city audit revealed that this neglect has resulted in out-of-order escalators and other equipment failures and impacted passenger flow and overall airport functionality.
A research found that early actions can cut maintenance expenses by over 50%.
On the other hand, deferring it can make facility costs balloon four to five times. In general, the consequences of neglecting timely maintenance takes a heavy toll on the budget for facility maintenance. The potential solution lies in making regular maintenance and repair a thumb rule – one of the important strategies to reduce maintenance costs.
2. Energy Waste
Inefficient energy usage—such as outdated HVAC systems, poor insulation, or lighting left on in unused spaces—can gradually increase utility costs. Around 40 to 60 percent of energy in commercial buildings is consumed by Heating, Ventilation, and Air Conditioning (HVAC) alone. Improper use of these ecosystems leads to excessive energy waste, especially in older or non-maintained facilities.
According to the U.S. Environmental Protection Agency, 30% of the energy used in commercial buildings is wasted. The consequences include higher utility bills, which can be particularly burdensome for businesses operating on tight margins, which forces the budget to swell.
Further, small inefficiencies add up, especially in large facilities, and often need regular energy audits and energy management systems. Operating machines at suboptimal levels will slowly deteriorate the system performance and, in the absence of audits, will never be captured until it turns into a significant failure.
3. Reactive Rather Than Preventive Maintenance
Reactive maintenance, or addressing issues only when they become critical, tends to be more costly than preventive maintenance. It costs anywhere between 20 and 40 percent higher than preventive maintenance. The reasons are obvious: Facilities will face higher labor costs, have to deal with emergency part orders, and experience downtime—all of this will be disruptive and costly.
Ideally, a facility should spend at most 20 percent on reactive maintenance because reactive work will involve more than meets the eye. A breakdown is associated with reactive maintenance. It means there is downtime, associated activities in the facilities have come to a halt—overall, it is a loss that adds to your maintenance budget. The costs will also add due to the non-availability of spare parts and overtime of technicians. These are some compelling facts about why you must prioritize preventive maintenance.
Facilities that adopt reliable preventive maintenance software build efficient maintenance practices. Such software offers real-time insights that help maintenance teams identify issues well in advance and successfully optimize maintenance costs. Such tools are great companions in facilities’ ongoing maintenance efforts.
4. Underutilized Space and Equipment
When planning a budget, space and equipment utilization are key areas to look at. Paying for unused or underused spaces and equipment can be a hidden drain. For example, keeping an entire building wing operational despite low occupancy rates increases cleaning, maintenance, and utility costs without offering corresponding value.
The commercial space rent differs from location to location in the US. However, an average of USD 37 to USD 40 can be expected per square foot. Considering an office space of 20,000 square feet, with around 20 to 40 percent unutilized space, the waste will be between USD 148 thousand to USD 320 thousand.
Substantial unused areas lead to overestimations of space needs and higher ownership costs. The same goes for equipment. There are categories of underutilized equipment: idle, obsolete, and scrap. Failing to identify the state of your equipment will incur unnecessarily high costs. You can strategize space management with a facility software and justify what you are paying for.
5. Vendor and Supplier Management
When contracts are not properly negotiated or reviewed, organizations risk being locked into unfavorable terms. Vendors may introduce hidden fees or unclear pricing, making it difficult for facilities to forecast expenses accurately. These unforeseen charges can catch facility managers off guard and stretch budgets beyond what was originally planned. Conducting vendor reference checks is thus crucial.
Using multiple vendors for similar services without consolidating contracts can also waste resources. Facilities miss out on opportunities to secure better deals or bulk discounts, resulting in higher operational costs. Sometimes, failing to compare vendor pricing regularly leaves organizations paying inflated rates for routine services.
As contracts progress without regular reviews, cost creep becomes a common issue. Small, overlooked charges slowly accumulate and erode budgets. The financial strain creates unnecessary risks, including business continuity concerns, and damages a company’s reputation if vendor issues go unaddressed. The solution lies in constantly monitoring vendor performance using standard facility vendor performance metrics to ascertain that your vendors are delivering as promised.
6. Inventory Mismanagement
Keeping too much on hand without properly tracking what’s used creates hidden costs that add up quickly. Items like HVAC parts, cleaning supplies, and electrical components can sit in a warehouse for years, degrading or becoming obsolete but still taking up space.
When something is stockpiled but goes unused, it’s essentially money-tied up with no return and impacts cash flow. It’s worth noting that nearly 10% of what facilities purchase ends up just sitting on shelves indefinitely. This can equate to millions of dollars in unused resources in large organizations.
On the flip side, running out of essential materials like air filters or electrical relays brings its own set of issues. Facilities teams will pay a premium for last-minute restocks, express shipping fees, or temporary fixes to keep systems running until the right parts arrive. When facilities need a replacement part urgently, there’s little time to look for the best price, and rush orders usually cost significantly more than regular purchases.
7. Inefficient Processes and Manual Work
Using outdated, labor-intensive tasks like data entry, scheduling, and reporting drains valuable work hours unnecessarily. Facilities still using these manual methods miss opportunities to shift workers to more strategic roles. When left unchecked, manual processes can drain 25% of revenue annually, creating a long-term financial impact.
Manual systems also lack transparency and accountability. Tasks performed by such processes don’t leave a clear record, making it challenging to identify responsible parties when mistakes and issues occur. Managers struggle to track employee progress effectively, which results in more errors and reduced productivity.
Investing in robust facilities management software provides a powerful solution to eliminate unnecessary labor hours tied to manual tasks like data entry, scheduling, and reporting. Over time, the reduction in labor costs achieved through such tools contributes to a significant cost saving.
8. Compliance and Regulatory Fines
Henry Ford once said, “If you need a machine and don’t buy it, then you will ultimately find that you have paid for it and don’t have it.” When we relate this to compliance, the cost and risk of non-compliance can easily outweigh the cost of investing in compliance efforts.
A facility must meet numerous regulations, ranging from building code requirements to geography-specific norms related to material handling and other safety, environmental, and accessibility standards. Overlooking these requirements can lead to hefty fines, costly retrofits, reputational damages, and legal expenses if regulations are breached—significantly increasing the total cost of ownership over time.
Facilities that ignore the importance of proactive compliance end up paying for compliance, like what happened with Walmart in 2013. Reportedly, one of the biggest retailers in the world, violated the Federal Insecticide, Fungicide, and Rodenticide Act (FIFRA) by failing to handle hazardous waste and was fined more than $81 Million.
9. Unplanned Downtime
Unplanned interruptions in facility operations significantly impact financial resources. When production or work comes to a halt due to unexpected failures, the immediate loss is compounded by delays throughout the entire workflow. For example, a critical piece of machinery breaking down can halt downstream processes, leading to various disruptions. These delays may cause supply chain bottlenecks, which take weeks to resolve and may further extend the time it takes to meet customer demands.
The costs associated with fixing unplanned issues escalate quickly. Expedited parts and labor to get the facility back online often comes at a premium, adding extra expenses. Downtimes due to such interruptions can cost a facility up to $260,000 per hour, reflecting the significant financial burden placed on operations. Findings reveal, industrial manufacturers lose an estimated $50 billion annually due to such interruptions. Equipment failure accounts for 42 percent of this unplanned downtime.
Downtime can lead to lost productivity or even lost revenue, especially in production facilities. Unplanned equipment failures often require expedited parts or labor costs and disrupt facility operations.
10. Insurance Premiums and Liability Claims
Unaddressed safety hazards or inadequate risk management can increase insurance premiums or lead to liability claims from incidents on-site. Liabilities from claims put a strain on a facility’s cash flow, notably when multiple claims are filed at once or when large settlements are necessary.
When it comes to property damage, if a facility has a $150,000 deductible and experiences $200,000 in damages, it must cover the first $150,000 out of pocket before insurance takes effect. Such deductible requirements lead to substantial immediate costs and affect budget planning.
The best way is to start by making modest investments in safety practices as this could reduce the financial pressures significantly over time. This way by mitigating on-site risks, facilities lower the chances of costly claims, which, over time, will potentially lead to fewer incidents.
Additionally, facilities need to consider both reported claims and those yet to be filed i.e. Incurred But Not Reported (IBNR) claims, when assessing their liabilities. They must reserve funds for incidents that have taken place but haven’t yet been submitted to the insurer.
11. Waste Management and Recycling Fees
Mismanaged waste disposal or failure to comply with local recycling regulations can incur additional fees. Efficient waste sorting and disposal practices can reduce costs and sometimes even generate revenue from recyclable materials.
This is especially critical in industries like healthcare, where waste has to be responsibly disposed of. In healthcare, handling hazardous waste can cost up to per kilogram, while non-hazardous waste disposal costs around $1.14 per kilogram.
When healthcare facilities don’t monitor waste production or lack a recycling program, they generate massive volumes of waste, leading to millions of dollars in disposal expenses. Across the industry, many facilities spend more than necessary on waste management, with total excess costs estimated at approximately $4 to $7 billion. So, if you are about to create a budget, be sure to consider how you will manage your waste.
12. Technology Obsolescence
Outdated technology creates significant financial strain for facilities, largely because it requires more maintenance and support to keep it running. These systems break down frequently, and when they do, the lack of manufacturer support often means paying premium rates for specialized troubleshooting. Recovery services for these systems may not be cheap, and these costs can add up quickly and drain funds that might be better spent elsewhere.
Obsolete equipment also slows down operations, limiting productivity and reducing potential revenue. Facilities that cling to outdated technology may miss out on efficiencies that competitors take advantage of with newer systems.
A study shows how facilities burdened with outdated tech generally see about 2.9% slower profit growth over five years than peers in the same field. Over a few years, these operational lags became evident in lower revenue streams and hindered growth. Looking at your existing technology setup can greatly help when creating a facility management budget. Identify areas where there are opportunities to implement technology and automate mundane operations.
13. Employee Training and Turnover
Insufficient training for facility staff can lead to errors, accidents, and higher turnover rates, each with its costs. Poorly trained employees can unintentionally trigger penalties. In fact, OSHA violations stemming from inadequate training can cost up to $136,532 per violation, a hefty price for skipping training essentials.
Employees should be well-versed in safety protocols, environmental standards, industry compliance, and the latest technology and maintenance practices. Covering all these bases means facilities teams are prepared to handle shifts in industry practices and equipment upgrades without missing a beat.
To overcome training hassles, facilities must set aside funds for investing in ongoing training and development. Training should be one of the essential facility maintenance objectives and span all critical areas needed for effective facility management, so that teams stay updated with the latest advancements and industry standards. Facilities should outsource training to experts to build programs faster that groom new recruits into honed facility managers.
14. Seasonal or Climate-Related Costs
Seasonal variations and uncertainties caused by climate change pose unique challenges for facility managers. In the US, where hurricanes are among the most destructive natural disasters, commercial properties alone account for approximately $9 billion in hurricane-related losses each year. Further, around 730 hundred commercial properties are at the risk of flood damage. The cost of repairing structures is expected to increase by 25% from 2022 to 2052 as findings have shown. Such unexpected events require immediate action and resources and can catch facilities off guard.
While there are costs brought by damage, there are costs required to repair that damage. Research from Deloitte highlights just how serious these costs are becoming. Their findings reveal that insurance premiums for commercial buildings are rising sharply, with average monthly rates projected to increase from $2,726 in 2023 to $4,890 by 2030. In high-risk states, these costs could nearly double, and are expected to reach $6,062 per building per month by 2030.
15. Overlooking Small Repairs
Small maintenance issues, like fixing leaky faucets or sealing drafty windows, seem minor at first glance, but they contribute significantly to financial waste if left unattended and end up consuming your maintenance budget.
A dripping faucet might take a plumber $300 to fix, and can gradually raise water bills by hundreds of dollars each year. Likewise, failing to address a piping issue may result in replacement costs that surpass $16,000 in larger properties.
Allocating a maintenance fund between 1% and 4% of a property’s value aids in managing recurring maintenance. If a property is valued at $500,000, it would ideally have $5,000 to $20,000 set aside annually. In this way, when minor repairs are consistently addressed, they prevent higher expenses and you can sustain the value of the property for the long term.
Takeaway
Remaining vigilant and nipping problems in the bud are facility managers’ best steps to stay on top of their budgets. Gaining continuous visibility into spending and monitoring how even small factors affect the bottom line are essential facility management practices for higher margins that lead to smarter, more controlled spending.
Top management must be committed to making its staff adept in technology, which can bring costs down dramatically across many areas. Adopt a facility management software to improve overall facility management and a comprehensive CMMS software to build a solid preventive maintenance program and cut maintenance costs. All these actions will lead to optimum budgeting and minimal spending for unintended activities.