What is Facilities Maintenance Management?
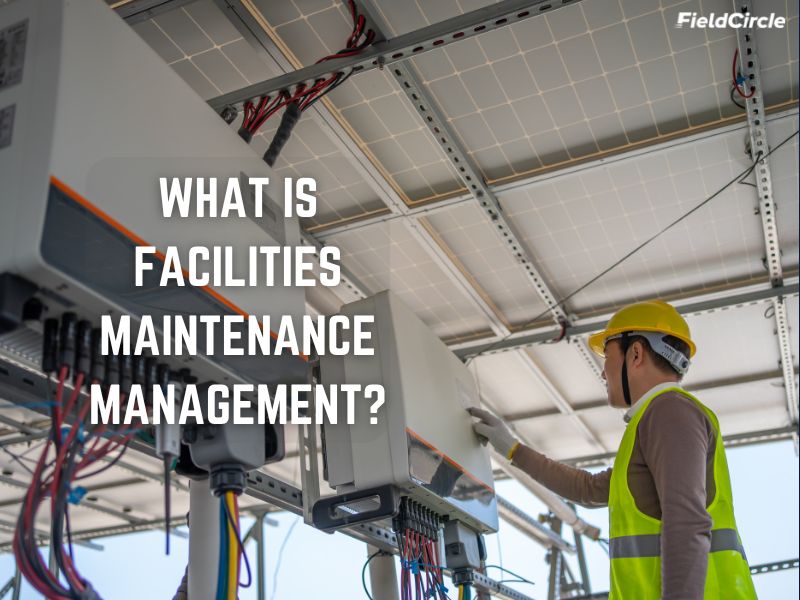
Facility maintenance is an umbrella term covering all essential maintenance tasks both inside and outside commercial buildings. It includes maintaining equipment, building systems, infrastructure, and the surrounding space. Embracing a proactive stance, facility maintenance integrates preventive, corrective, and predictive strategies, effectively optimizing resources while cultivating a safe and efficient operational environment. Let’s explore more about this key area in facilities management.
Facilities management is an intrinsic part of every enterprise these days, regardless of industry or size. From multinational corporations to small businesses, the effective management of facilities is integral to supporting core operations.
Central to the successful functioning of any facility is the process of maintenance. Whether it’s a commercial office space, a manufacturing plant, or a healthcare facility, maintenance plays a pivotal role in ensuring the longevity, safety, and operational efficiency of physical assets. What industrial maintenance is to heavy industries, facilities maintenance is to facilities. Without proper maintenance protocols in place, facilities are susceptible to a myriad of issues ranging from equipment breakdowns and safety hazards to deterioration of infrastructure.
A study from the University of Connecticut and Syracuse University found that keeping up with maintenance can increase a property’s value by about 1 percent each year. That one percent can go a long way for businesses. Further, water damage which can result in mold growth can lower a property’s value by around 3 percent. However, with scheduled maintenance, such damages can be prevented and instead of encountering depreciation, organizations can sustain the value of their property.
So, maintenance keeps facilities in good shape and aids in realizing the goal of facilities management. By implementing proactive maintenance strategies, organizations can preemptively address potential issues before they escalate, thereby minimizing downtime and disruptions to operations. It extends the lifespan of equipment and infrastructure, preserves the value of assets over time, and improves the return on investment (ROI).
Effective maintenance practices are also essential for regulatory compliance and risk management. In industries such as healthcare, manufacturing, and hospitality, businesses have to operate within a strict regulatory framework. Maintenance helps facilities mitigate the risk of accidents and work in accordance with industry regulations and best practices, and thus avoid liabilities and legal consequences.
Moreover, in an era where sustainability is increasingly prioritized, maintenance plays a crucial role in promoting environmental responsibility. By adopting green maintenance practices, such as energy-efficient processes, waste reduction initiatives, and eco-friendly materials, organizations can successfully minimize their environmental footprint while simultaneously lowering operating costs and enhancing brand reputation.
In this blog, we provide comprehensive coverage of every aspect of facilities maintenance essential for effective facility management. Whether you’re a facility manager seeking to enhance operational efficiency or a business owner looking to maximize the value of your facility, the information covered here will serve as your guide for defining a successful future facility maintenance roadmap.
Primary Objective of Facilities Maintenance Management
The primary objectives of facilities maintenance revolve around a broad spectrum of activities tailored to maintain the performance of the facility, focusing on:
Achieving Operational Excellence
Facilities maintenance aims to keep all physical assets and infrastructure functioning smoothly. This it does through regular inspections and repairs that help prevent breakdowns and interruptions in operations. By addressing issues proactively, facilities can minimize downtime and maintain continuous productivity.
Building a Safe Environment
Another key objective is to ensure the safety of occupants and users of the facilities. A safe environment is essential to protect the well-being of employees, visitors, and the community. Maintenance tasks include inspecting and repairing safety features such as fire suppression systems, emergency exits, electrical wiring, and structural integrity.
Ensuring Asset Longevity
Facilities maintenance seeks to maximize the lifespan of assets and infrastructure. By implementing preventive maintenance measures, such as routine inspections, cleaning, lubrication, and minor repairs, facilities mitigate wear and tear, and prolong the life of equipment and buildings. As a result, organizations can avoid premature replacements and reduce long-term costs.
Continuously Enhancing Efficiency
Maintenance activities focus on optimizing the performance of HVAC systems, equipment, and utilities to reduce energy consumption and operating costs. As part of facility management best practices, regular maintenance ensures that equipment operates at peak efficiency, enabling facilities to achieve higher operational ROI.
Maintaining Consistent Levels of Occupant Comfort and Satisfaction
Maintaining a comfortable and conducive environment for occupants is also a priority, which is achieved by regulating indoor air quality, temperature, and lighting levels to create a productive and pleasant workspace.
Taking Timely Corrective Actions
Facilities maintenance involves responding to issues and emergencies in a timely manner. By building efficient plans, organizing, and executing maintenance tasks, facility maintenance managers address problems promptly and prevent further damage. The maintenance process entails taking swift corrective actions to minimize disruptions and maintain operational continuity.
Types of Maintenance in Facility Management
Facility management encompasses a broad range of maintenance activities designed to ensure the functionality, comfort, safety, and efficiency of a built environment. These maintenance activities are typically carried out in form of these three types of facility maintenance processes:
Preventive Maintenance
Preventive Maintenance is a proactive approach to maintenance, where maintenance professionals take steps to prevent the occurrence of problems. There is an established schedule of regular inspections, servicing, and part replacements that the maintenance team follows to avert equipment failures and keep operations smooth. Understanding the different types of Preventive maintenance, such as time-based, usage-based, and predictive maintenance, helps organizations tailor their maintenance plans effectively. Implementing a comprehensive checklist for equipment and facility areas based on industry standards and manufacturer recommendations is one key aspect of this approach.
Through scheduled inspections, the maintenance team detects signs of wear or potential issues before they escalate. In this process, facility managers follow a detailed checklist to carry out the maintenance tasks. This approach highlights several preventive maintenance benefits, such as reduced downtime, cost savings, and extended equipment life. For instance, in commercial buildings, HVAC units undergo routine servicing like cleaning coils and replacing filters to maintain optimal performance and indoor air quality. Next, prompt inspection and repair of roof leaks to prevent water damage is conducted to offer comfort to tenants and preserve property value.
Corrective Maintenance
Maintenance procedures that are carried out post occurrence of issues in the facilities operations for addressing equipment failures or malfunctions fall under this category. The maintenance team responds to requests, and addresses the problems. Fixing leaks, unclogging drains, repairing broken pipes, or addressing issues with water pressure are common corrective maintenance plumbing activities carried out in real estate. This is also known as reactive maintenance strategy
The maintenance team gauges the urgency and the impact of the identified problem and determines the resources required to deal with it. They record the details of maintenance tasks, including the nature of the issue, actions taken, materials used, using this as an input for preventive actions. One key step here is to verify that the issue is fully resolved and that no further immediate attention is required. By serving as input for preventing failures, corrective maintenance helps in reducing unplanned downtime.
Predictive Maintenance
With the rise of artificial intelligence and IoT, maintenance has changed significantly. The shift has occurred from preventive maintenance to predictive maintenance, where maintenance teams use predictive analytics to determine probable occurrences of malfunctioning and take action in time. Maintenance teams make use of IoT sensors to monitor equipment performance and health in real-time, and analyze data trends to predict equipment failures.
As many as 83% of organizations have improved their reliability using predictive maintenance, with a potential reduction in equipment maintenance costs by 10-40%. With these benefits, maintenance teams are more focussed on capitalizing the power of predictive power rather than relying on the traditional preventive or corrective approach. Bringing several improvements in the maintenance process, predictive maintenance helps build a long-term maintenance strategy.
Key Components of Facilities Maintenance Management
Let’s look at major components of facilities maintenance. These are in fact clusters of elements of process types that are similar in nature. By looking at facilities maintenance in this manner, facilities managers can systematically address each maintenance need.
Building Maintenance
The importance of building maintenance lies in its ability to prevent deterioration, prolong the lifespan of the structure, and maintain a safe working environment for occupants. Care and preservation of a structure’s physical integrity and functionality is what all it covers.
Maintenance teams regularly carry out inspection and repairing of building exteriors, roofs, walls, windows, and doors. They address issues caused by cracks, leaks, weather damage, and structural weaknesses. The purpose is to keep the structure of the commercial or residential buildings sound, resilient against environmental upheavals, and aesthetically appealing.
Property Maintenance
Routine cleaning of communal spaces is essential to maintain hygiene and overall cleanliness. Termed as property maintenance, it includes scheduling regular cleaning of lobbies, hallways, elevators, and other shared areas.
Maintenance activities that revolve around inspections and upkeep of outdoor areas and cover tasks such as landscaping and maintaining external structures fall under property maintenance. So, from mowing lawns, trimming hedges, repairing pavement cracks, and repainting parking lot lines, to maintaining parking lots and walkways, property maintenance deals with all similar activities. Going further, Managing waste disposal and recycling systems efficiently is also part of property maintenance. Teams will carry out sorting, collection, and disposal of waste and material recycling to remain environmentally sustainable.
Equipment Maintenance
From pumps, security systems to vacuum cleaners and floor scrubbers, there is an endless list of equipment that a facility will have. These equipment must undergo regular maintenance so that they keep working sustainably and deliver the output on a constant basis. Equipment maintenance makes this possible.
There is a set course of action that the maintenance team will follow for equipment maintenance. Using a combination of preventive, corrective and predictive maintenance, the team aims for zero downtime. Well-maintained equipment operates more reliably and efficiently, and leads to higher productivity and higher-quality outputs. With the right equipment strategy, businesses successfully extend the lifespan of their assets and improve the maintenance ROI.
Specialized Maintenance
Specialized maintenance tasks require expertise in specific areas or systems within a facility. Engaging certified facility managers and technicians paves the way for high-quality maintenance. Certifications like Certified Maintenance and Reliability Professional (CMRP) and Certified Maintenance Manager (CMM) provide expertise in maintenance planning, reliability-centered maintenance, and asset management.
Additionally, certifications in electrical maintenance (e.g., Certified Electrical Safety Compliance Professional – CESCP), HVAC/R (e.g., North American Technician Excellence – NATE), welding inspection (e.g., Certified Welding Inspector – CWI), and building operations (e.g. Certified Building Operator – CBO) equip maintenance teams with specialized skills. The role of professionals with these specialized certifications becomes evident in niche scenarios.
Facility Management And Maintenance
Facility maintenance and Facility management even though are closely related serves distinct roles within the broader context of ensuring the functionality and efficiency of built environments.
Facility maintenance is primarily concerned with the physical upkeep of buildings and equipment, focusing on tasks such as repairs, cleaning, and preventive measures to prolong the life of assets and ensure operational functionality. It is a critical aspect that directly impacts the safety, and reliability of the physical environment.
On the other hand, Facility management encompasses a wider scope, integrating people, place, process, and technology to enhance the overall quality of life and productivity of the core business. Facility Management typically involves strategic planning, real estate management, emergency preparedness, environmental sustainability, and financial management, in addition to maintenance activities.
Facility Maintenance Management acts as a bridge between these two areas, focusing on maintaining a facility’s physical assets within the broader objectives of Facility Management. It strategically aligns maintenance tasks with organizational goals, compliance standards, and sustainability efforts.
Job Roles in the Facility Maintenance Management
Multiple stakeholders across different hierarchies are involved in the process of carrying out the process of facility maintenance. The key job roles in this process comprise:
- Facility Manager
- Maintenance Manager
- Facility Maintenance Technician
- Maintenance Planner/Scheduler
At the helm of the hierarchy, the facility manager wields authority over strategic planning, budget allocation, and overall management of personnel. The responsibilities of this role span across areas, right from overseeing all activities to liaising with external contractors.
Among the key qualities of a good facility manager are the ability to set the department’s direction and priorities, serve as the linchpin in overall functionality, and balance operational demands with budgetary constraints to maintain efficiency.
Positioned directly beneath the Facility Manager, the Maintenance Manager assumes leadership in executing day-to-day maintenance operations. The responsibilities encompass supervising maintenance staff, coordinating repair tasks, and devising comprehensive maintenance plans.
With a keen focus on optimizing resources, maintenance managers implement preventive, corrective, and predictive maintenance programs to mitigate risks and enhance equipment longevity. They serve as liaisons between the facility manager and maintenance technicians, translating strategic directives into actionable plans while assuring accountability and efficiency within the maintenance department.
Within the facility maintenance hierarchy, the facility maintenance technician embodies hands-on expertise essential for the operational integrity of the facility. They work under the guidance of maintenance managers or supervisors, and undertake a diverse array of tasks, from routine inspections to emergency repairs.
Technicians are frontline workforce who execute the responsibilities that encompass troubleshooting mechanical and electrical systems, conducting preventive maintenance, and swiftly addressing maintenance requests to minimize downtime.
Maintenance planning and scheduling is one special role in the maintenance team that optimizes workflow and resource allocation. By devising result-oriented maintenance plans, they translate strategic objectives into handsome outcomes.
Maintenance planners and schedules give meticulous attention to detail and gather information on maintenance tasks, using it as an input to build the plans. They serve as architects of efficiency, balancing competing priorities coming up with the best combination of activities.
Importance of Facility Maintenance Management
Without an iota of doubt, facilities maintenance management is an indispensable process in the entire facilities management. The reasons explained below cast more light on its importance and expose the benefits of facility maintenance:
- Ensures operational efficiency
- Enhances safety
- Extends asset lifespan
- Facilitates compliance with legal and regulatory requirements
Effective maintenance ensures that all building functions, from HVAC systems to essential equipment, operate smoothly. By preemptively addressing potential issues through routine inspections and upkeep, businesses can minimize disruptions and maintain uninterrupted operations.
Regular inspections and repairs uphold safety standards and ensure compliance with regulations, building codes, and fire safety codes established by local fire departments. By maintaining buildings and equipment to meet safety codes, facility maintenance management protects occupants and workers from potential hazards. Adhering to regulations is a key step to mitigate legal risks, avoiding fines and penalties associated with non-compliance.
Maintenance strategies, such as preventive and predictive measures, extend the lifespan of assets. By identifying and addressing issues early, businesses reduce the need for costly replacements and repairs, thereby optimizing the performance and durability of assets, and thus improving asset portfolio.
Facility maintenance management plays a crucial role in mitigating operational risks. By addressing potential hazards and adheres to necessary compliances and guidelines such as Environmental Protection Agency (EPA) regulations for environmental protection and Americans with Disabilities Act (ADA).
Challenges in Facility Maintenance Management
Facility Maintenance Management (FMM) is fraught with complexities that bring before facilities maintenance staff the onerous challenges of:
- Keeping Up with Technological Advancements
- Ensuring Regulatory Compliance and Safety Standards
- Addressing Aging Infrastructure and Deferred Maintenance
- Optimizing Maintenance Operations and Workforce Management
Embracing new technologies like Building Automation Systems and IoT devices promises efficiency gains, but integrating them with existing systems is complex and expensive. You need to impart constant training for facility maintenance workers to help them harness these tools effectively, which can result in pressure to keep up with the ever-evolving technology.
There are regulations at local, state, and federal levels and managing compliances at various levels is a daunting process. As any slip-ups can risk the safety of occupants, it can come with severe legal repercussions and threaten the image of organization.
For dealing with aging infrastructure and a backlog of maintenance tasks you must plug multiple gaps. Additionally, retrofitting and upgrading facilities to modern facility standards demand significant resources and careful planning. All this you have to manage, all while trying to prioritize critical maintenance needs amidst limited budgets.
To strike the right balance between routine maintenance, emergency repairs, and workforce management, maintenance teams have to juggle with many things. These are some of the core facilities management challenges, where teams must navigate a resource-intensive exercise while constantly confronting competing priorities and limited resources.
Technology Used in Facility Management Maintenance
Businesses are growing increasingly tech-intensive, bringing diverse tools and technologies to continuously improve their maintenance operations by integrating cutting-edge technology. Major technologies that are bringing revolution in facilities maintenance include:
Facility Management Software (FMS)
Facility Management Software (FMS) serves as the centralized digital hub for managing all activities of facilities maintenance, thereby streamlining planning, execution, and monitoring of maintenance activities. Serving as a dedicated facility maintenance software, it’s an essential tool for facilities maintenance managers seeking to optimize operations and maintain high standards of asset management and upkeep. Depending on the size, scope, and needs of the organization, there are different facility management software options available, each offering a unique combination of tools and features. Some of the key features of the software include:
- Monitoring critical assets, right from HVAC systems to electrical infrastructures.
- Creating, assigning, and tracking maintenance work orders, thus aiding in timely repairs.
- Maintaining a real-time ledger of maintenance supplies and parts.
- Managing vendor contracts and interactions.
- Generating comprehensive reports and analytics, thus providing insights into maintenance trends and performance metrics—an essential capability for staying ahead of evolving facilities management trends and making data-driven decisions.
- Enabling space allocation, room booking, occupancy tracking
- Monitoring energy consumption and associated costs.
Building Automation Systems (BAS)
Building Automation Systems (BAS) automate the control of building systems like lighting, heating, ventilation, and air conditioning (HVAC), enhancing operational efficiency and occupant comfort. As a key component of an automated facility management system, BAS offers important features such as:
- Ability to automatically adjust settings based on occupancy and usage patterns.
- Facilitates the integration of various building systems onto a single platform.
- Provides remote access and control capabilities.
- Remote capability to troubleshoot issues.
Internet of Things (IoT) and Smart Sensors
By offering an unprecedented level of connectivity, data collection, and analytics, IoT and smart sensors represent a transformative approach to facilities maintenance. They perform several key functions including:
Features:
- Continuously monitoring building systems, equipment, and environmental conditions in real-time, providing a constant stream of data, thus detecting changes in equipment conditions, and assisting in remote diagnostics and troubleshooting of equipment issues.
- Monitoring energy consumption patterns and identify opportunities for optimization, such as adjusting HVAC settings based on occupancy levels or scheduling equipment operation during off-peak hours.
- Detect anomalies in real-time and generate alerts or notifications to maintenance teams.
- Integrate with existing building automation systems (BAS) and other facility management software platforms, enabling centralized control, monitoring.
- Monitor environmental conditions such as temperature, humidity, air quality, and occupancy levels, and optimize indoor environmental quality.
Mobile Maintenance Applications
Mobile apps revolutionize how maintenance requests are reported, tracked, and resolved, enabling seamless communication between facility managers, technicians, and occupants. They bring transformation to the maintenance process by offering:
- Remote real-time access to maintenance data, work orders, and schedules.
- Offline functionality that allows users to access and update data even when they are not connected to the internet.
- Capability to capture photos or videos of equipment issues, damage, or completed work directly within the app, providing visual documentation for reference and record-keeping purposes.
- Capability to access predefined task checklists, standard operating procedures (SOPs), or maintenance manuals directly from the app.
Predictive Analytics and Artificial Intelligence (AI)
AI and predictive analytics harness historical data and machine learning algorithms to forecast future maintenance needs, transforming the approach to facilities maintenance from reactive to predictive. It assists the maintenance process by helping:
- Analyze patterns and trends to predict equipment failures.
- Determine the optimal maintenance schedule based on data-driven insights.
- Continuously improve predictive accuracy and refine maintenance strategies over time.
Geographic Information System (GIS)
GIS technology offers spatial insights into facility management, enabling the visualization and analysis of physical assets across different locations, which is especially important for organizations with multiple facilities. Geographical Information Systems:
- Map out the geographic distribution of assets, aiding in strategic planning and resource allocation.
- Assess the impact of location on maintenance needs and planning, optimizing routes for maintenance crews and identifying areas prone to issues.
- Optimize maintenance routes for technicians by analyzing asset locations, work orders, and traffic conditions to determine the most efficient route for completing maintenance tasks.
- GIS applies spatial analysis techniques, such as hotspot analysis, proximity analysis, and spatial clustering, to help identify areas with high maintenance needs.
- GIS integrates environmental data, such as terrain, land use, and environmental hazards, with maintenance data to assess the impact of environmental factors on maintenance operations.
To Wrap Up
We took you to every corner of facilities maintenance management. Equipped with this insight, you can take appropriate action to bring positive changes in your facilities maintenance operations.
One thing we get to see is that innovation and a forward-thinking approach are not merely options but imperatives in the pursuit of optimal facility performance and sustainability. So, by harnessing cutting-edge technologies such as computer-aided facility management (CAFM) software and computer maintenance management system (CMMS) organizations can elevate their maintenance practices.