9 Effective Strategies To Cut Costs in Facility Maintenance
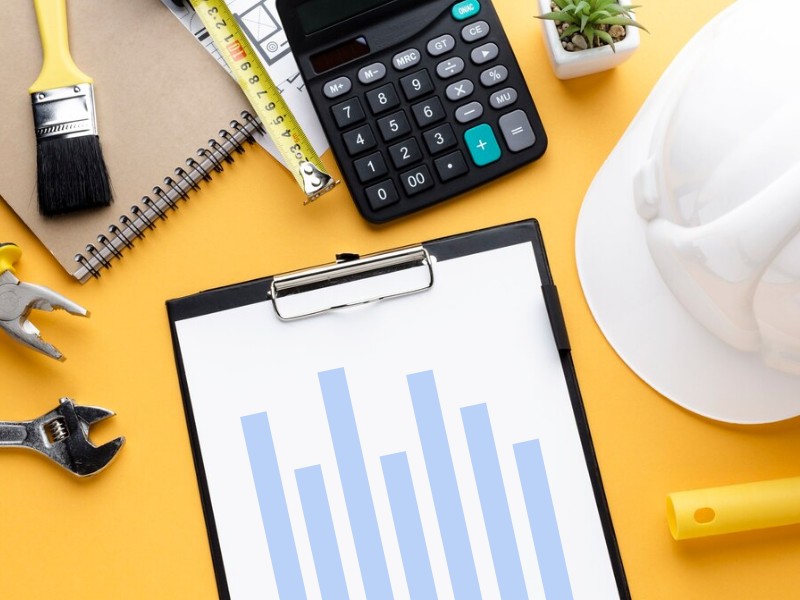
Managing a facility is like walking a tightrope, balancing quality and costs delicately. As a facility leader, you face the challenge of juggling maintenance budgets and finding ways to make them more manageable, including how to keep the facility maintenance costs minimum, which becomes more challenging if you don’t have the right blend of experience, open perspective and a well-rounded approach.
You’re no stranger to the constant pressure of reducing costs. The higher-ups demand a cost cut within a strict time limit, usually around 4-5% within 3-6 months.
But here’s the catch: nobody knows the ideal maintenance cost due to the uncertainties involved. The dependance on so many factors leads to an unpredictability that keeps operations and facility managers worried.
Surprisingly, nearly 50% of those costs are classified as “waste,” according to the ARC Advisory Group.
While slashing maintenance spending in half overnight is an unrealistic expectation, reducing costs by 20% over a period is an achievable goal.
In this blog, we’ll delve into practical strategies and ideas on how to reduce facilities management cost that leaders have followed and benefitted from- some short term while others can be implemented over long term.
Short-Term Initiatives and Quick Fixes to Reduce Facility Maintenance Costs
When it comes to reducing building maintenance costs, one of Sa key question to consider is how can we improve facility maintenance? Organizations can benefit significantly from implementing short-term initiatives and quick wins that address this concern. Let’s check out those actions.
– Create A Crew That Nails Tasks!
When reducing costs, many organizations may consider cutting the number of employees or eliminating specific planning tasks.
However, it’s essential to recognize that reducing staff without addressing underlying inefficiencies will not lead to significant cost savings. It can often have the opposite effect, impacting morale and overall productivity.
Managers must prioritize empowering their staff to reduce costs and improve efficiency.
Maintaining a highly skilled and motivated team ensures smooth operations and helps avoid the substantial costs associated with turnover.
Studies by ShifteLearning have shown that rehiring expenses typically represent 12% of a business’s total expenses, with up to 40% for firms with high turnover rates. The financial impact of turnover is further evidenced when nearly 70% of organizations reported negative financial implications due to recruiting, hiring, and training replacement employees. The overtime work of existing employees until the vacant position is filled adds to the cost burden.
A well-trained team requires less time waiting for instructions or assistance and minimizes the need for rework by other team members. To identify where to focus your training efforts, analyze your team’s key performance indicators (KPIs) and leverage a facility planning software like FieldCircle for reporting dashboard for valuable insights on improvement areas.
Key points:
- Technical training: Equip your teams with the necessary skills for repairing equipment and performing preventive approach tasks effectively.
- Cultivate a maintenance culture: Foster an environment that values proper practices and encourages collaboration among team members.
- Save time and resources: Well-trained teams require less assistance, reducing downtime and increasing productivity.
- Analyze KPIs: Review your team’s key performance indicators to identify areas that need improvement and prioritize training accordingly.
- Leverage space planning solution: Utilize reporting dashboards to gain insights into your team’s training needs and make informed decisions.
By implementing these cost management strategies in facility and investing in the training and development of your crew, you can create a highly efficient team that reduces operational expenses and contributes to your property’s long-term success.
Balance Your Stocks to Save Your Stacks
The importance of efficient inventory and spare parts planning cannot be overstated. In fact, in 2020 alone, the cost of inventory distortion amounted to a staggering US$1.8 trillion, according to IHL Services.
This figure highlights the issue’s magnitude and underscores the need for proactive measures to optimize inventory control.
Think about it this way: Have you ever found yourself in a situation where you desperately needed a specific part for a repair, only to discover that it’s nowhere to be found? It’s frustrating, time-consuming, and can cost your property a pretty penny. But adequate inventory and spare parts planning can save the day!
When you effectively manage your inventory, you can significantly reduce inventory costs by 10% by eliminating stockouts and overstocks, as per the Retail Vision Study by Zebra.
Having a well-managed inventory means striking the perfect balance between supply and demand. It ensures you have the right amount of spare parts and materials, eliminating the risk of being caught off guard when equipment or machinery breaks down.
– Do Building Energy Makeover
Have you ever considered how facilities operations costs can affect energy efficiency?
The answer lies in various ways, some of which may be simpler than you think. It could be as straightforward as recommending and implementing energy-saving light bulbs, enhancing insulation on windows and walls, and making small yet impactful changes within your facilities.
We know what you might think: these upgrades require an initial investment. And you’re right.
However, viewing them as long-term investments that pay off over time is essential, considering that approximately 35% of a building’s energy costs are attributed to lighting alone, as the Environmental Protection Agency (EPA) highlighted. Just imagine the potential for reducing that slice of your overall costs by simply switching to energy-saving bulbs.
Here’s where it gets even better. There are a lot of powerful tools for reducing facilities maintenance costs by introducing measures to monitor and track energy usage. The data you gather can guide you in making informed decisions that lead to cost savings. These measures enhance the longevity and performance of your assets and pave the way for a more efficient operation.
But it doesn’t stop there. There’s a growing emphasis on environmental consciousness, and embracing energy efficiency can bring additional benefits. By taking a firmer stance in this area, your businesses and employees may become eligible for tax cuts and other incentives, creating a win-win situation for your finances and commitment to sustainability.
Medium and Long-term Initiatives to Reduce Facility Operations Costs
Organizations seeking to reduce costs can employ long-term initiatives offering sustainable solutions. These initiatives can help companies achieve long-lasting facilities operations cost savings. Organizations can enhance the efficiency and effectiveness of their processes by implementing strategies and adopting these tips to reduce maintenance costs.
– A Stitch in Time Saves Nine!
Have you ever heard the saying, “An ounce of prevention is worth a pound of cure”? Well, it holds when it comes to maintenance.
Taking a proactive approach and implementing preventive care can be a game-changer for your building’s overall performance and cost planning. Let’s explore how it can revolutionize your operations practices.
Preventive approach is all about staying ahead of the game. Instead of waiting for something to break down or malfunction, you take proactive measures to keep your equipment and systems in shape. By identifying critical equipment and systems that demand regular attention, you can prevent costly breakdowns, extend their lifespan, and improve efficiency.
Strategies for reducing maintenance costs through Preventive Maintenance:
One key element in implementing proactive approach is using reliable facility scheduling software to create a well-structured maintenance schedule. This schedule outlines when and how each equipment or system should be inspected, cleaned, and serviced. By following a consistent preventive schedule, you can ensure that all necessary tasks are completed on time, reducing the risk of unexpected failures and costly repairs.
Step | Description | Example |
Identify Critical Equipment | Determine essential equipment requiring maintenance to prevent breakdowns. | Identify the high-traffic elevators that need regular inspections and lubrication to prevent expensive downtime. |
Determine Tasks | Specify tasks required for optimal conditions. | Create a task list for monthly filter replacement in HVAC units to maintain airflow and energy efficiency, reducing the need for costly repairs. |
Set Frequency and Intervals | Define task frequencies based on recommendations. | Schedule quarterly equipment calibration to ensure accurate readings and avoid costly measurement errors in laboratory equipment. |
Assign Responsibility | Allocate tasks to staff or contractors. | Assign an in-house technician to conduct routine lubrication and inspection of manufacturing machinery, minimizing wear and tear and avoiding expensive breakdowns. |
Create a Schedule | Develop a calendar or system to track tasks. | Utilize planning platform like FieldCircle to create a digital schedule that sends automated reminders for preventive approach tasks, ensuring timely completion. |
Regularly Review and Update | Assess effectiveness and make adjustments. | Analyze records and feedback to identify patterns and optimize the schedule, reducing unnecessary tasks and streamlining the process. |
You can significantly reduce costs across various areas by following these steps and customizing the preventive method schedule to your building’s specific needs.
– Let the Data Speak!
Just think about the staggering average hourly downtime costs reported by facilities like yours – between $301,000 and $400,000, as per Statista. Inefficiency comes at a hefty price.
Predictive analytics emerges as a powerful tool to combat equipment inefficiencies and minimize the cost of facilities management. You can enhance equipment effectiveness and significantly reduce costs by leveraging data-driven insights.
Predictive analytics can produce impressive results in operations. As reported by BirlaSoft, it can contribute to a 30% reduction in costs and a 25% improvement in unplanned downtime.
Through predictive analytics, you gain the ability to detect early warning signs of equipment failure, enabling proactive method interventions that prevent costly breakdowns. Analyzing historical data, performance metrics, and other relevant information allows you to identify patterns and trends that provide valuable cost-cutting clues. If you’re wondering how do you optimize building maintenance costs, predictive analytics is an essential tool to consider.
By harnessing the power of predictive analytics, you can optimize schedules, allocate resources efficiently, and address needs before they escalate into significant issues. This saves money, minimizes disruption to operations, and maximizes equipment uptime.
– Leave It to the Pros!
As a manager, you have a lot on your plate. But what if I tell you there’s a way to lighten the load and reduce maintenance time? It’s called outsourcing. You can tap their specialized skills and experience by delegating tasks to external experts.
Outsourcing offers several advantages. You gain access to a pool of skilled professionals dedicated to specific tasks, ensuring higher quality work and faster turnaround times. It also leads to significant cost savings. Companies can save up to 30% on costs by outsourcing non-core tasks, as per Deloitte’s 2021 Global Shared Services and outsourcing Survey Report. Instead of hiring and training an in-house team for every task, you pay for the specific services you need when you need them.
To identify tasks suitable for outsourcing, assess your in-house team’s skills and resources. Focus on tasks outside their expertise or those that are time-consuming. Janitorial services, landscaping, or specialized equipment repairs are commonly outsourced tasks.
To effectively manage outsourced services, establish clear communication and expectations. Define your requirements and desired outcomes, and regularly review their performance.
– Dodge Costly Detours and Unexpected Breakdowns
Managing facilities requires a long-term approach, much like planning a journey.
Regarding assets, it’s not just about fixing things when they break; it’s about considering the costs throughout their lifespan. For example, invest in a new HVAC system for your property. Sure, it’s a significant expense upfront, but there’s more to it. That system has a lifespan; it’ll need service and replacement over time.
To tackle this, you need an asset planning plan – a roadmap for your assets. It helps you anticipate service costs, allocate funds for replacements, and prioritize spending. A clear plan lets you make informed decisions and avoid unexpected financial burdens.
Aberdeen Group’s study shows that organizations implementing asset lifecycle planning can reduce costs by up to 22%. That’s real money saved!
So, as a manager or startup founder, think long-term. Develop an asset planning plan, prioritize service and replacements, and witness decreased costs. It’s an investment that pays off.
– Forge Strong Partnerships
As a manager, building strong partnerships and collaborating with suppliers and service providers can be a game-changer for reducing costs and maximizing value. Developing strong partnerships with suppliers and service providers is vital.
As per Harvard Business Review, you can negotiate favorable contracts and pricing by fostering collaborative relationships, resulting in up to 10% savings on supplies or discounted rates for equipment repairs.
Another beneficial approach is a vendor-managed inventory (VMI), where suppliers monitor and replenish your stock.
By embracing partnerships and collaboration, managers can tap expertise, negotiate better contracts, explore innovative inventory planning solutions, and achieve significant cost reductions.
– Set Targets and Crush Them
Suppose you discover that your average monthly cost per square foot is $1.50 while the industry standard is $1.00. This realization motivates you to explore ways to align your costs with the benchmark, such as renegotiating vendor contracts or investing in energy-efficient equipment.
Tracking and benchmarking costs give you the power to take control of your facility management budget. You can make informed decisions and allocate resources more effectively by identifying cost-saving opportunities and implementing a targeted facilities management cost reduction strategy.
Here’s how you can utilize tracking and benchmarking, along with operations software, to reduce costs:
- Utilize a platform to track and manage activities efficiently.
- Define key performance indicators (KPIs) aligned with cost-saving goals and track them consistently.
- Set realistic performance targets based on industry benchmarks and historical data.
- Collect and analyze data to identify trends, outliers, and areas for improvement.
- Identify specific cost-saving opportunities, such as recurring issues or excessive spending on spare parts.
- Optimize preventive approach schedules using the capabilities of maintenance software.
Conclusion
Regarding costs, a little knowledge can go a long way. Businesses can significantly reduce their financial burden by understanding the factors contributing to these expenses and implementing the right cost reduction strategy.
It’s crucial to realize that maintenance isn’t just about fixing things when they break; it’s about proactive planning, regular inspections, and preventive measures. Embracing a holistic approach that focuses on preventive methods, energy efficiency, and vendor management can lead to substantial savings in the long run.
So, whether you’re a small business or a large corporation, having cost control is an intelligent investment that will benefit your bottom line and allow you to allocate resources to other essential areas of your operations.
Get in touch to implement the right strategies and software for cost control, ensuring smooth operations.