The Intersection of Quality Assurance and Maintenance
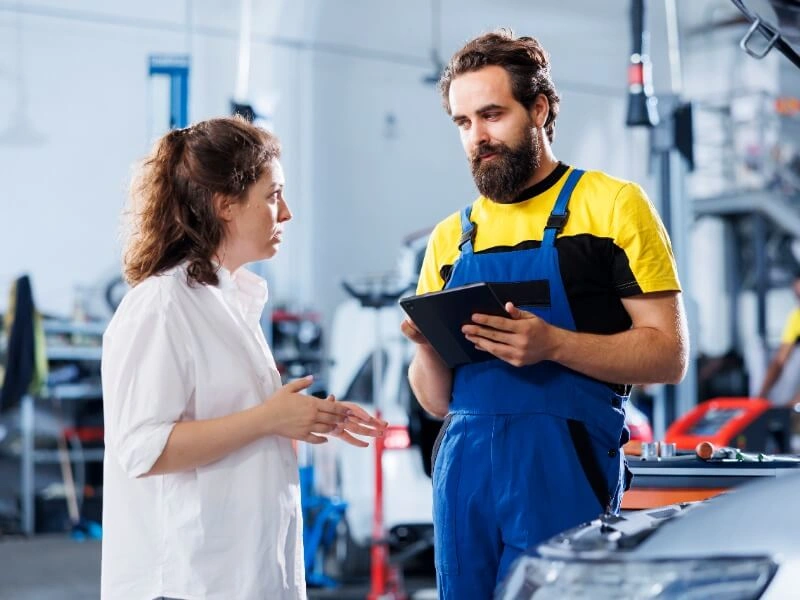
Maintenance and quality assurance are two cardinal processes in organizations with heavy equipment setup. They work as two different units in the overall value chain. The former focuses on improving equipment reliability and reducing downtime to make equipment and machinery deliver the best in a consistent manner. The latter, aiming to build products that meet accepted standards.
Despite their separate relevance they are related, with maintenance dictating the terms of quality assurance, though implicitly. Maintenance and quality management along with safety achieves a cohesive and effective operational environment. Organizations that consider them as two components on the same plane, always get the upper hand. We move and analyze this relation more closely.
Quality Assurance: Tightening the Bolts for Business Success
Quality assurance (QA) is a key process in every industry. Since it directly affects the business success, businesses cannot approach it with a lackadaisical attitude. They must concentrate resources and inspect all processes that lead to QA to achieve the quality outcomes.
Technically quality assurance is the systematic process of checking and evaluating products, services, or processes to ensure that they meet predefined standards and specifications. The primary goal of quality assurance is to identify and rectify defects or deviations from the established criteria, ultimately ensuring that the final output meets the desired level of quality.
What does Quality Assurance involve?
Quality assurance process will vary from industry to industry. Typically, here are the steps that go into building a QA process:
- Establishing Standards and Specifications: You define the criteria and requirements that a product or service must meet. This process sets the benchmarks for quality, ensuring that the end result aligns with predefined expectations. Standards and specifications serve as the foundation for subsequent quality assurance activities and evaluations.
- Sampling and Testing: Quality management team examines a representative subset of a larger batch. Testing methods may include visual assurance, measurements, material testing, and more, depending on the nature of the product or service.
- Documentation: This includes recording standards, assurance results, corrective actions taken, and any other relevant information. Documentation provides a basis for traceability and continuous improvement.
- Application of Statistical Methods: Statistical methods such as statistical process control (SPC) are employed to monitor and control the production process. These methods help identify trends, patterns, and variations that could impact product quality.
- Root Cause Analysis: In the event of defects or deviations, quality inspectors often conduct root cause analysis to determine the underlying reasons for the issues. Addressing the root cause is crucial to preventing future occurrences.
As quality management is an industry-specific process, let’s see how it is carried out in various industries.
Industry | Area | Scenario |
Manufacturing | Using Six Sigma methodologies to minimize defects. | Reducing variations in the production process to achieve high-quality outputs. |
Construction | Conducting tests on concrete mixes. | Testing concrete samples for compressive strength and adherence to project specifications. |
Agriculture | Utilizing precision farming technologies. | Implementing GPS-guided tractors for accurate seeding and planting in agriculture. |
Mining | Implementing real-time monitoring systems on mining equipment. | Monitoring equipment health parameters to predict and prevent breakdowns. |
Oil and Gas | Implementing strict quality control measures during pipeline construction. | Ensuring weld quality and coating integrity in oil and gas pipelines. |
Energy Generation | Conducting performance tests on turbines. | Dynamometer testing of wind turbine generators to verify their power output and performance. |
Transportation | Implementing thorough aircraft maintenance checks. | Regular inspection, repair, and replacement of aircraft components to ensure airworthiness. |
Healthcare | Validating the performance and safety of medical devices. | Conducting usability testing and validation of a new medical imaging device before market release. |
Telecommunications | Conducting regular security audits for telecommunication networks. | Penetration testing to identify and address vulnerabilities in network infrastructure. |
Aviation | Rigorous testing and validation of avionics systems. | Conducting avionics tests to verify the accuracy and reliability of navigation, communication, and monitoring systems. |
Automotive | Conducting comprehensive crash tests on vehicles. | Performing frontal, side-impact, and rollover tests to assess a vehicle’s crashworthiness. |
Chemical | Validating batch processes in chemical manufacturing. | Verifying the quality of each batch of pharmaceuticals through detailed testing and documentation. |
Water Treatment | Regularly testing chlorine residuals in water treatment. | Ensuring adequate chlorine levels to eliminate harmful microorganisms in drinking water. |
Textile | Conducting quality tests on fabrics. | Inspecting textile materials for defects and ensuring they meet specified quality standards. |
Food and Beverage | Implementing metal detection systems. | Using metal detectors to identify and remove metal contaminants from food products. |
Maintenance: A Precursor to Quality Assurance
“Be a yardstick of quality. Some people aren’t used to an environment where excellence is expected,” once remarked Steve Jobs. In the industries we looked at in the preceding part, maintenance is a key process to build an environment of excellence.
So, quality assurance is directly proportional to maintenance, as the effectiveness of the latter directly influences the outcomes of the former. Poor maintenance operations will lead to suboptimal product quality. Conversely, efficient maintenance practices will enhance the accuracy and reliability of quality assurance.
Maintenance ensures that equipment and machinery are in optimal condition, minimizing the likelihood of defects in the manufacturing process. Well-maintained machinery is less prone to breakdowns and malfunctions, leading to a more consistent production process. This, in turn, contributes to the production of higher-quality products.
Analyzing the Correlation
Regular maintenance prevents wear and tear on equipment, reducing the chances of deviations from product specifications.
In manufacturing, for instance, precision machinery and production lines are the backbone of the production process. Regular maintenance of these machines ensures that they operate within specified tolerances, minimizing the risk of unexpected breakdowns.
The correlation between maintenance and quality assurance becomes evident when considering the impact of equipment failure on product quality. If a key manufacturing component fails due to inadequate maintenance, it can introduce defects into the production process, compromising the quality of the final product.
In the oil and gas industry, where the stakes are high due to the potential environmental and safety risks, the correlation between maintenance and quality assurance is even more pronounced. Pipelines, storage tanks, and drilling equipment are subjected to harsh conditions and must be maintained meticulously to prevent leaks and spills. Inefficient maintenance can lead to inaccurate readings, making it challenging to assess the structural integrity of pipelines or the condition of storage tanks accurately. We have experiences such as the Deepwater Horizon oil spill, where an equipment malfunctioning was one reason for the catastrophic failure that resulted in severe environmental consequences.
In aeronautics, precision instruments, avionics, and structural components must undergo routine maintenance to ensure they meet stringent safety standards. Quality assurance processes, such as Non-Destructive Testing (NDT) methods, rely on the assumption that the equipment being tested is in optimal condition. Any oversight in maintenance could compromise the accuracy of these assurances, potentially leading to undetected flaws in critical aircraft components.
Regulatory norms bridging the gap
Adherence to standards and norms builds a link between maintenance and QA. So, in spite of working as two disconnected processes, they build one single process aimed to achieve consistent quality output. For instance, in
- Manufacturing adherence to quality standards such as ISO 9001 requires a systematic approach to maintenance to ensure that equipment is capable of consistently producing conforming products.
- Oil and gas regulatory frameworks such as API standards prescribe maintenance practices to guarantee the integrity of infrastructure.
- Aeronautics, organizations like the Federal Aviation Administration (FAA), enforces rigorous maintenance and assurance protocols outlined in documents like the Aircraft Maintenance Manual (AMM) to ensure airworthiness.
How businesses have reaped results
As we stressed about the inseparability of maintenance and quality assurance, we elaborate more with results achieved by recognized names. For instance, Delta Air Lines implemented a proactive maintenance strategy using advanced analytics and real-time monitoring of aircraft components. They began regularly inspecting and maintaining their fleet, ascertaining optimal condition of the aircraft during scheduled checks. The outcome was fewer in-flight issues and higher level of safety.
Deutsche Bahn has implemented a condition-based maintenance system for its train fleet. By monitoring the condition of train components, such as wheels, brakes, and engines, in real-time, they can schedule maintenance activities more efficiently. Likewise, Shell has been using predictive maintenance technologies, such as sensors and data analytics, to monitor the condition of equipment in real-time. By minimizing downtime and reducing the risk of equipment failures, they have enhanced the overall quality of operations.
Maintenance for Quality: Some Steps to Initiate
Across industries, here are some actions in maintenance that can be taken to witness direct positive impact of maintenance on quality.
Industry | Maintenance Operations for Quality Outcomes |
Manufacturing | Calibrate and quality-check production equipment consistently. Focus on continuous improvement by analyzing defect patterns and optimizing maintenance processes. |
Construction | Prioritize structural integrity checks and safety protocols. Schedule routine maintenance for construction vehicles and tools. |
Agriculture | Utilize precision farming technologies for real-time equipment monitoring. Conduct seasonal equipment inspections and maintain irrigation systems. |
Mining | Implement condition monitoring technologies for mining equipment. Focus on effective lubrication management and conveyor system maintenance. |
Oil and Gas | Regularly inspect pipelines, rigs, and processing facilities. Implement corrosion control measures and emergency response plans. |
Energy Generation | Implement condition-based monitoring of critical components. Prioritize maintenance tasks based on reliability analysis. Integrate protocols for uninterrupted energy generation. |
Transportation | Utilize advanced fleet management systems for real-time tracking. Conduct regular vehicle inspections and adhere to scheduled maintenance. |
Healthcare | Regularly calibrate and maintain medical devices. Implement asset management systems for healthcare equipment. Integrate infection control measures into maintenance activities. |
Telecommunications | Regularly monitor and maintain telecommunications networks. Implement redundancy measures for continuous network availability. Conduct regular inspections of antennas and transmission lines. |
Aviation | Conduct routine inspections of aircraft components. Plan and perform overhauls of critical components. Utilize flight data analysis for predictive maintenance. |
Automotive | Conduct routine inspections of vehicles during manufacturing. Implement predictive maintenance for production line equipment. Ensure rigorous quality checks at each stage of vehicle assembly. |
Chemical | Prioritize safe practices for handling hazardous materials. Utilize process monitoring technologies to identify deviations. |
Water Treatment | Conduct thorough inspections of water treatment plants. Utilize preventive maintenance software to schedule and track maintenance activities for pumps and filtration systems, ensuring timely servicing and reducing unexpected failures. Adhere to water quality standards and regulations in maintenance processes by leveraging data-driven insights and automated maintenance workflows. |
Textile | Conduct routine inspections of textile manufacturing equipment. Implement preventive maintenance for dyeing machines. Ensure quality checks in weaving processes. |
Food and Beverage | Conduct routine inspections of production lines. Calibrate cooking and cooling equipment for consistent product quality. |
The Role of Metrics
Here are various quality assurance metrics that businesses must monitor to get an idea about the efficiency of maintenance. By monitoring these metrics and understanding their relationship with maintenance efficiency, businesses can proactively address maintenance issues.
Quality Assurance Metric | Impact of Poor Maintenance | How to trace back to identify issues in maintenance |
Defect Rate | Increased defects in products or services due to unreliable equipment and processes. | Analyze defect patterns to identify equipment or process points that require maintenance. |
Non-Conformance Rate | Higher deviation from established standards due to inadequate maintenance. | Investigate non-conformance instances to identify maintenance-related root causes. |
Customer Complaints | More product or service issues leading to an increase in customer complaints. | Link customer complaints to specific equipment or process failures requiring maintenance. |
Productivity Loss | Unplanned downtime affecting productivity metrics (e.g., OEE, efficiency ratios). | Track downtime events and correlate them with maintenance records to identify causes. |
Cost of Quality | Increased expenses related to defect prevention, detection, and correction. | Examine cost breakdowns to identify areas where poor maintenance contributes to higher costs. |
Process Capability | Reduced stability and capability of manufacturing processes due to poor maintenance. | Monitor process variability and correlate it with maintenance records to address issues. |
Regulatory Compliance | Non-compliance with quality standards and regulations due to poor maintenance. | Audit maintenance processes and correlate findings with regulatory compliance metrics. |
Customer Satisfaction Index | Subpar products or services affecting customer satisfaction scores. | Link customer feedback to maintenance-related issues, focusing on improving satisfaction. |
Time-to-Market | Delays in product delivery caused by equipment breakdowns or process disruptions. | Analyze maintenance-related downtime and delays to streamline processes and reduce time-to-market. |
Audit Findings | Findings during audits resulting from poor maintenance practices. | Conduct internal audits on maintenance processes and address identified issues promptly. |
How a CMMS can enhance quality inspections through improvement in maintenance
One key element in achieving and maintaining high-quality standards is an efficient and effective maintenance strategy. A Computerized Maintenance Management System (CMMS) emerges as a crucial tool that not only streamlines maintenance processes but significantly contributes to enhancing quality inspections. From maximizing asset utilization for downtime reduction to maximizing warranty coverage, it offers manifold benefits.
With its various features, a CMMS aids in scheduled maintenance, keeping equipment and processes ever efficient. So, the maintenance software offers you a proactive approach that diminishes the likelihood of unexpected breakdowns, eliminating scope for detrimental effects on product quality.
We recommend you to connect with our experts to align FieldCircle CMMS with your quality assurance process and realize significant improvements.