The Ultimate Preventive Maintenance Checklist Guide
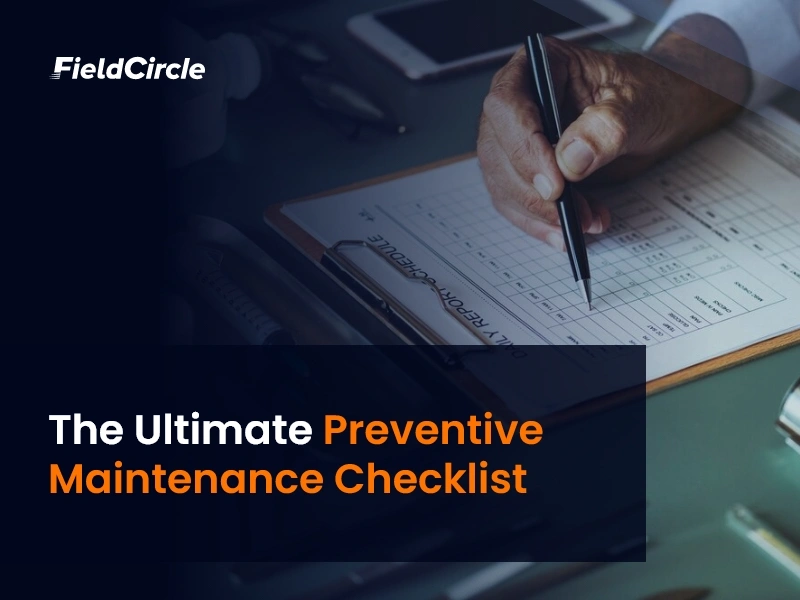
Checklists have long been the go-to tool for keeping things organized and running smoothly. There’s something to be said for the sense of control they provide—knowing you won’t forget a single task as you tick them off one by one. It’s a simple yet powerful way to keep things in check, no matter the scope of the work at hand.
When it comes to preventive maintenance, checklists become even more important. They act as a safety net, because they help catch potential problems before they snowball into bigger issues.
A solid maintenance checklist ensures that nothing slips through the cracks. You get a clearer picture of what needs to be done and when, avoiding last-minute scrambles.
In this comprehensive guide, we cover everything about preventive maintenance checklists – from their types, guidelines to build them, equipment-specific checklists, and common maintenance procedures to the process to build them.
What is a Preventive Maintenance Checklist?
A preventive maintenance checklist is a structured list of tasks and procedures that technicians or operators use to routinely service equipment. It outlines specific actions, such as cleaning, lubrication, and inspections, to be performed at set intervals. It serves not only as a guide for maintenance teams but also as a record-keeping tool that documents the condition of equipment over time.
Preventive Maintenance Pre-Checklist
Following are the four key elements that are precursors and fundamental to any maintenance checklist. Establish discipline in these four areas to eliminate avoidable errors and bring structure into day-to-day tasks:
-
Equipment and Asset Identification
Every piece of equipment must have a unique identifier. Labels, tags, serial numbers, or barcodes leave no room for ambiguity. Classification helps in assigning responsibility, planning inspections, and triggering replacements when needed. A structured register with clear asset descriptions, categories, and physical conditions keeps teams grounded.
-
Documentation (Locate and Create)
Existing documents should be easy to retrieve—whether manuals, technical specs, or previous maintenance logs. Where documents don’t exist, they must be created to fill gaps. Accuracy in documentation leaves no space for confusion, especially during troubleshooting or replacement. Storage locations, access methods, and update cycles must be fixed.
-
Tools and Supplies Readiness
Missing or misplaced tools can delay entire shifts. Every wrench, meter, valve, or cartridge must be tracked. Stocks should be replenished before reaching low thresholds. All tools must meet safety standards and operate without defects. The right tools, in the right place, at the right time—nothing less should be accepted.
-
Redefine or Verify KPIs
Outdated KPIs waste time. They either measure irrelevant outputs or hide performance gaps. Maintenance key performance indicators must reflect real operations—cycle time, repair frequency, downtime hours, mean time between failures. Each metric must point to measurable action. Precision matters. Guesswork has no place in operational performance.
What Are the Types of Preventive Maintenance Checklists and Tasks?
Preventive maintenance checklists are essential tools used to keep equipment and systems running smoothly. They consist of a series of tasks that help identify potential issues before they escalate. Following are the step-by-step checklists that businesses must follow to stay ahead of maintenance needs:
1. Preventive Maintenance for Buildings & Facilities
Following are the types of preventive maintenance checklists specifically designed for buildings and facilities. These checklists cover essential tasks to keep the overall structure and environment in good condition:
-
Building Maintenance Checklist
A building maintenance checklist handles routine tasks such as inspecting structural elements and checking systems like plumbing and HVAC to keep the facility in working order.
-
Commercial Facilities Maintenance Checklist
This checklist focuses on maintaining the operational systems in commercial facilities, including electrical systems, lighting, and safety equipment.
-
Apartments and Condos Maintenance Checklist
For apartments and condos, the checklist tracks the upkeep of both private and common spaces, including plumbing, landscaping, and structural elements.
-
Hotels Maintenance Checklist
Hotel maintenance checklists cover a range of tasks such as inspecting guest areas, kitchens, and public spaces to ensure functionality and cleanliness.
-
Hotel Rooms Maintenance Checklist
Hotel room checklists address individual tasks for each room, such as checking furniture, fixtures, and amenities to maintain guest comfort.
-
Food Safety Maintenance Checklist
A food safety maintenance checklist is essential for maintaining hygiene, monitoring storage conditions, inspecting kitchen equipment, and maintaining cleanliness standards to prevent contamination.
2. Preventive Maintenance for Building Infrastructure
These are the types of preventative maintenance checklists for building infrastructure. They tasks focus on the key systems that support the building’s daily operations and ensure long-term stability:
-
HVAC Maintenance Checklist
The HVAC checklist focuses on checking air filters, cleaning ducts, and inspecting system performance to keep air circulation optimal.
-
Plumbing System Maintenance Checklist
A plumbing checklist covers inspections of pipes, faucets, and drains, spotting leaks or blockages before they lead to problems.
-
Electrical Equipment Maintenance Checklist
This checklist tracks preventive maintenance tasks such as inspecting wiring, connections, and power supplies to prevent equipment malfunctions.
-
Electrical Motor Maintenance Checklist
The electrical motor checklist includes checks on motor alignment, lubrication, and testing to maintain smooth operation.
-
Electrical Panel Maintenance Checklist
An electrical panel checklist tracks tasks like inspecting circuit breakers and wiring to maintain electrical safety and prevent faults.
-
Generators (Diesel) Maintenance Checklist
The diesel generator checklist covers fuel checks, oil changes, and performance tests to keep the system ready for power supply in emergencies.
-
Emergency Lighting Maintenance Checklist
The emergency lighting preventive maintenance checklist ensures emergency lighting systems are tested and functioning properly during power failures or emergencies.
-
Fire Protection Maintenance Checklist
Fire protection tasks include inspecting extinguishers, sprinklers, and alarms to keep systems prepared for use in case of fire.
-
Fire Alarm System Maintenance Checklist
The fire alarm checklist tracks inspections of sensors, batteries, and connections to confirm the system is ready for use during a fire.
-
Security System Maintenance Checklist
This checklist covers tasks like checking cameras, testing alarms, and calibrating systems to maintain overall security in the facility.
-
Elevator Maintenance Checklist
Elevator tasks include inspecting cables, control systems, and safety features to keep the elevator operating safely and efficiently.
-
Building Interior Maintenance Checklist
Interior maintenance covers inspections of walls, flooring, and HVAC systems, making sure they remain in good condition for a safe environment.
-
Building Exterior Maintenance Checklist
Exterior maintenance tasks focus on checking windows, facades, and roofs for damage, ensuring the building’s structural integrity.
3. Preventive Maintenance for Machine & Equipment
The following types of preventive maintenance checklists are tailored for machines and equipment. These checklists address the necessary tasks to keep equipment running efficiently and avoid unexpected breakdowns:
-
Pumps and Motors Maintenance Checklist
Key tasks here include inspecting seals, checking bearings, and monitoring belt conditions to avoid unplanned disruptions.
-
Valves Maintenance Checklist
The checklist covers thorough checks of seals and lubricating moving parts while making sure no leaks occur in the system.
-
Air Compressor Maintenance Checklist
Focusing on the air filters, pressure levels, and hose conditions, the air compressor preventive maintenance checklist helps maintain the compressor’s operational reliability.
-
Gearbox Maintenance Checklist
It’s all about gear inspection, lubrication checks, and verifying the alignment, keeping the gearbox in top shape and preventing unexpected failures.
-
Exhaust Fan Maintenance Checklist
Regular blade cleaning, motor performance checks, and duct inspections make this checklist an essential for maintaining the exhaust system.
-
Hydraulic Press Maintenance Checklist
The checklist focuses on checking oil levels, inspecting hydraulic components, and testing pressure gauges to ensure smooth operation.
-
Overhead Crane Maintenance Checklist
Key tasks include checking cables, hoists, and motor conditions to keep overhead cranes functioning properly.
-
Forklift Maintenance Checklist
The forklift maintenance checklist is used for inspecting tire pressure, hydraulic systems, and battery levels to prev0ent any downtime or issues.
-
Conveyor Maintenance Checklist
A routine check of belts, rollers, and motors, making sure the conveyor system operates smoothly without blockages or mechanical issues.
-
Welding Machine Maintenance Checklist
The checklist checks on electrode conditions, machine settings, and cable inspections to maintain the welding machine’s dependability.
-
Lathe and Milling Machine Maintenance Checklist
This one tracks cutting tool wear, lubricates moving parts, and checks alignment to maintain the precision and longevity of machining equipment.
-
CNC Machines Maintenance Checklist
The checklist ensures software functionality, moving parts lubrication, and mechanical component inspections to keep CNC machines operating smoothly.
-
Laboratory Equipment Maintenance Checklist
Calibration, part cleaning, and regular maintenance checks are essential as this checklist assists in performing diligently.
-
Filling Machine Maintenance Checklist
The filling machine preventive maintenance checklist focuses on checking filling levels, nozzle cleanliness, and control systems to make sure the filling process stays consistent and efficient.
-
Kitchen Equipment Maintenance Checklist
Based on the type of equipment in the kitchen, this checklist helps inspect appliances, clean vents, and check safety features regularly.
4. Preventive Maintenance for Vehicles
Discussed below are the various types of preventive maintenance checklists for vehicles. These checklists guide the tasks required to maintain vehicles in optimal condition, reducing the chances of mechanical failures:
-
Trucks Maintenance Checklist
The truck preventive maintenance checklist covers a range of tasks, including checking tire pressure and tread condition, inspecting fluid levels such as oil, coolant, and brake fluid, and performing brake system checks.
-
Diesel Trucks Maintenance Checklist
Key tasks in this checklist include inspecting the fuel system for leaks or blockages, checking the exhaust system for damage or excessive wear, testing engine performance and diagnostics.
-
Semi-Trucks Maintenance Checklist
The semi-truck checklist focuses on inspecting tire condition and pressure, checking brake pads and systems for wear, ensuring proper fluid levels, and verifying the condition of the lighting system.
-
Tractor Trailers Maintenance Checklist
It is used in the inspection of the trailer’s suspension system, checking for damage to lights and wiring, assessing hitch connections for wear, and verifying that the braking system is fully operational, including trailer brakes and emergency brake systems.
How to Create an Effective Preventive Maintenance Checklist?
To create an efficient preventive maintenance checklist, you need to follow a step-by-step process which we discuss in detail below:
-
Identify Equipment and Asset
Begin by listing all assets and equipment maintenance needs. This can include machinery, vehicles, electrical systems, HVAC units, or plumbing installations. Each item should be detailed by its specific make, model, and serial number.
-
Classify Equipment by Function or Department
Group equipment according to its function, department, or operational role. For instance, separate HVAC systems from mechanical equipment or office machinery to streamline maintenance scheduling.
-
Refer to Manufacturer Guidelines
Consult the manufacturer’s manual for each asset. These documents provide essential technical specifications and recommended maintenance intervals for components like belts, filters, or lubrication points.
-
Incorporate Safety Codes and Regulations
Identify relevant safety codes, industry standards, and local regulations that apply to each piece of equipment. These may include electrical codes, fire safety regulations, or environmental protection requirements that directly affect maintenance tasks.
-
Examine Historical Maintenance Logs and Failure Records
Review historical data to identify recurring issues, past failures, or areas with frequent maintenance needs. This helps in prioritizing tasks that require more frequent attention or specific repairs.
-
Define Maintenance Tasks
For each piece of equipment, define the maintenance tasks based on the manufacturer’s recommendations, safety standards, and failure records. These tasks could include checking fluid levels, cleaning filters, inspecting wiring, or testing sensors.
-
Set Individual Task Intervals for Each Checklist Item
Assign specific time intervals for each maintenance task, such as weekly, monthly, or quarterly. Refer to historical logs and manufacturer guidelines for the most accurate interval determination.
-
Use CMMS for Checklist Management
Implement a computerized maintenance management system (CMMS) to track tasks, set reminders, and manage work orders. The system will automatically schedule maintenance and alert staff to upcoming tasks based on defined intervals.
-
Assign Responsibility for Each Maintenance Task
Designate maintenance personnel responsible for each maintenance task. Ensure clear accountability for each item on the checklist, whether it’s an internal technician or an external service provider.
-
Test the Checklist on a Small Scale
Before finalizing, test the checklist on a few items or equipment to verify that tasks are feasible within the set intervals and that the equipment operates correctly after maintenance.
-
Get Feedback From Maintenance Technicians and Supervisors
Gather feedback from maintenance technicians and maintenance supervisors about the checklist’s practicality and clarity. Their insights will help refine task intervals, add missing tasks, or adjust responsibilities.
-
Finalize and Document the Checklist
After testing and refining, finalize the checklist and document it in a standard format. Ensure that each task is clearly listed with assigned responsibilities and set intervals, and store the checklist in a centralized, easily accessible location.
What Are the Benefits of Preventive Maintenance Checklist?
Following are the key benefits of preventive maintenance checklist that explain how they unlock potential improvements that have a direct impact on operational performance:
-
Better Resource Allocation
Preventive maintenance allows businesses to allocate resources more effectively by reducing sudden repair costs. Knowing exactly when maintenance is required helps in scheduling repairs without disrupting other operations, leading to more controlled and efficient use of time and money.
-
Extended Equipment Life
Regular maintenance prevents overuse and avoids wear that shortens the lifespan of equipment. By addressing issues before they escalate, machines function longer and more reliably, pushing back the need for expensive replacements and offering better value over time.
-
Improved Safety Record
Routine checks reduce the risk of equipment malfunctions that could cause accidents.
Identifying and fixing small issues before they escalate ensures a safer working environment, which not only protects employees but also prevents costly insurance claims and liability issues.
-
Optimized Production Flow
Preventive maintenance eliminates unplanned downtimes, which often disrupt production schedules. Keeping systems in peak condition allows operations to run smoother, reducing delays and maximizing production capacity without unexpected stoppages or the need for last-minute fixes.
-
Reduced Unforeseen Failures
A well-structured preventive maintenance schedule targets issues before they cause major breakdowns. This proactive approach significantly lowers the chances of unexpected equipment failures that could halt operations, minimizing the financial and operational impact of unplanned repairs.
-
Cost-Effective Maintenance
Routine checks and minor repairs prevent costly major repairs by addressing smaller issues early, keeping maintenance costs low. Preventive maintenance reduces the likelihood of catastrophic failures, ensuring that maintenance budgets remain more predictable and manageable, without the financial strain of emergency fixes.
What Are the Most Common Preventive Maintenance Challenges and How to Solve Them?
A preventive maintenance process is fraught with many challenges. Below we discuss the major challenges often faced by maintenance professionals. Each of them follows a potential solution to overcome that particular challenge:
-
Inconsistent Maintenance Schedules
One of the most frequent hurdles businesses face in preventive maintenance is sticking to maintenance schedules. When tasks are missed or delayed, equipment can fail unexpectedly, resulting in costly downtime. To avoid this, companies can use a Computerized Maintenance Management System (CMMS). Such a system automates the process, sending reminders and ensuring that all maintenance activities are completed as planned.
-
Lack of Skilled Workforce
When there aren’t enough trained technicians available, maintenance tasks can suffer in quality and timeliness. As a result, equipment may not be properly cared for, leading to increased wear and tear. To tackle this issue, organizations should invest in employee training to boost team capabilities. In addition, hiring specialized contractors for specific tasks can fill any skill gaps when needed.
-
Limited Resources and Budget Constraints
Many businesses struggle with allocating enough funds to cover both routine and emergency maintenance needs. However, by identifying critical equipment and prioritizing its upkeep, companies can make better use of their limited resources. Another approach is to negotiate bulk discounts with suppliers or explore cost-effective preventive maintenance plans to ensure essential assets remain in top condition without overspending.
-
Failure to Track Maintenance History
Without a detailed record of past maintenance work, businesses risk repeating the same mistakes or missing patterns that could prevent future issues. A simple solution is to establish a maintenance tracking system. This enables businesses to monitor the frequency of repairs and anticipate upcoming maintenance needs based on historical data, allowing for more informed decisions and smoother operations.
-
Over-Reliance on Reactive Maintenance
Reactive maintenance makes you wait for equipment to fail before addressing maintenance often results in costly repairs and extended downtime. A shift toward preventive maintenance is key. By scheduling regular inspections and using automated scheduling tools, businesses can proactively maintain equipment, avoiding the costs and disruptions caused by reactive repairs.
How to Customize Preventive Maintenance Templates for Your Facility?
Customizing preventive maintenance (PM) templates starts by identifying the equipment and systems that need regular upkeep, such as machinery, HVAC, and safety devices. Each asset requires specific tasks and maintenance intervals, like lubrication or filter cleaning. Defining these details helps create a template that matches your facility’s needs.
Focus on listing tasks with clear instructions and adding sections for PM checklists, documentation, and measurements. This ensures that the template is practical, easy to follow, and adaptable to all maintenance requirements.
Can You Use These Templates with a CMMS System?
Yes, preventive maintenance templates can be used with a Computerized Maintenance Management System (CMMS). By integrating customized templates, you can automate work orders, track tasks, and monitor compliance, all within a centralized system. By using custom templates within the CMMS, you assign tasks to the right personnel, store documentation, and gain real-time insights into asset performance and task completion.
Using Fieldcircle CMMS to Streamline Preventive Maintenance Checklist
A maintenance management software plays a critical role in organizing and tracking maintenance activities and building a preventive maintenance program. Some features to look for in such software include:
- Work order management: Easily create and track maintenance tasks.
- Asset tracking: Monitor the condition and performance of each piece of equipment.
- Reporting and analytics: Generate reports that provide insights into maintenance performance and equipment reliability.
Equipped with all latest capabilities, FieldCircle CMMS software easily integrates with sensors and IoT devices, comes with AI/ML functions, allowing real-time monitoring and predictive analysis of equipment health. Moreover, it offers various templates for various processes in the entire maintenance life cycle. Get in touch with our team for effortless integration of checklists in the preventive maintenance process.