Field Service Technician: Responsibilities, Skills, Qualifications, Prospects and Best Practices
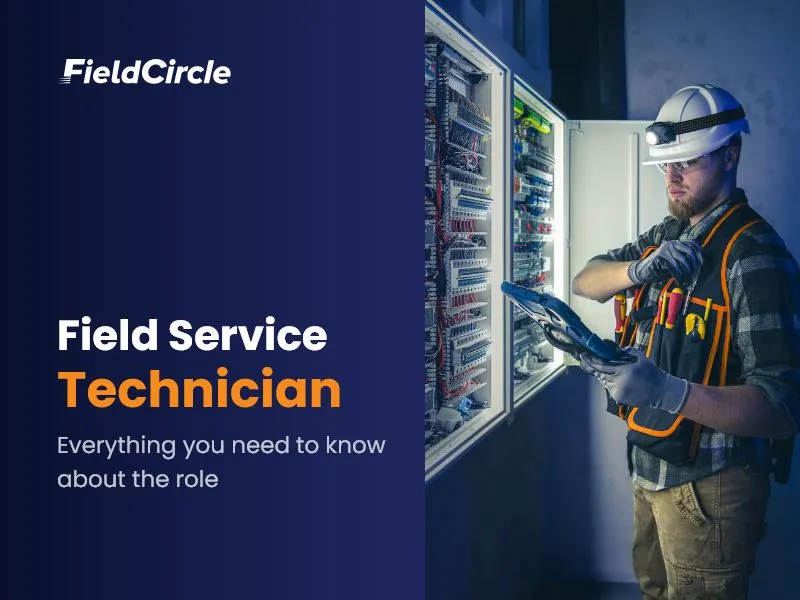
As businesses rely on technology more than ever, the demand for field technicians remains high. With a hands-on approach to maintaining and repairing equipment, field technicians are key to business success in many industries.
The role calls for a unique combination of on-the-job problem-solving skills, technical know-how, and the ability to work independently. These technicians often face situations where immediate solutions are necessary, without the luxury of time to consult their team. The demanding nature of the job requires them to bring to the table a broad skill set to tackle an array of challenges on the spot.
Understand in detail about responsibilities, skills, qualifications, and job prospects for field technicians, as we cover all these dimensions. We’ll also highlight the best practices that can make or break success in this fast-paced profession.
What is a Field Service Technician?
A field technician is a specialized professional responsible for installing, maintaining, and troubleshooting equipment directly at customer sites or in field settings. They bring expertise to addressing issues in equipment in real-time under less-than-ideal conditions. In this process, technicians handle everything right from installing new systems to diagnosing malfunctioning equipment.
What are the Key Responsibilities of a Field Service Technician?
In their work to keeping every piece of equipment constantly operating and delivering optimal performance, field technicians have to fulfill various responsibilities, which include:
- Routine Maintenance and Repairs
- Installation of Equipment
- Troubleshooting and Diagnostics
- Customer Interaction and Service
- Documentation and Reporting
- Ensuring Compliance with Safety Standards
A large part of field technicians go in routine maintenance. May it be manufacturing and utilities, in any industry routine maintenance operations are essential for consistent functioning equipment.
In routine tasks, field technicians carry out regular inspections, lubricate parts, replace filters, and identify components nearing the end of their lifespan. They follow a schedule to catch issues and prevent them from developing into significant technical problems.
Installation takes place when new equipment arrives. Field technicians install hardware or machinery according to specific technical requirements and industry standards. This is a complex and critical process, where they have to bring the right technical expertise as per the nature and function of the equipment.
In the installation operations, field technicians work closely with stakeholders, which could be team members from other key functions such as mechanical engineering, electrical engineering, quality assurance, etc. in case of enterprise equipment installation or customers in case of home appliances so that installations align with the expectations.
In all the field service processes, troubleshooting is a key process that a technician has to perform when the equipment malfunctions. Here, field technicians have to quickly identify the problem, analyze symptoms, and develop an effective solution.
For instance, when an HVAC unit fails to cool adequately, field technicians visit the site, methodically examine the system’s components—compressors, condensers, and refrigerant levels—and isolate the issue.
Field technicians work directly with clients, answer questions and explain technical information in clear, accessible language. These interactions are Important to driving customer engagement in field service, and requires an approachable demeanor, and patience, apart from strong technical skills.
Technicians need to maintain professionalism to ensure that every experience is positive and help build customer trust and loyalty. Embracing a service mindset not only aids in smooth troubleshooting but also enhances communication, strengthens client relationships, and contributes to repeat business and referrals.
Every task in field operations is recorded as part of the process protocol and for future reference. Field technicians must meticulously maintain precise records of each service call. They need to document all work performed, including repairs made, parts replaced, and also observations about the equipment’s condition.
With perfect documentation, technicians are easily able to recall previous work on a system, provide clients with a clear service history, and easily track job progress. Record-keeping by technicians is of particular importance in regulated industries, where documentation is scrutinized in audits.
While field technicians perform the operations, they have to keep an eye on sticking to norms and regulations, which is a non-negotiable aspect in field operations. They must follow all industry-specific guidelines to protect themselves, coworkers, and customers and to install the equipment or fix the issue as per the norms.
One common scenario that explains the importance of compliances is how electrical field technicians wear insulated gloves and adhere to lockout/tagout (LOTO) procedures to prevent accidental equipment activation during repairs. When field staff follow safety compliance they operate in a risk-less environment and keep on-site dangers at bay.
Essential Skills for Field Service Technicians
Strong understanding of the equipment functioning and tool usage, problem-solving ability, along with strong communication are the skills that a field technician must possess to successfully execute field operations. As practices are rapidly evolving and new approaches are emerging, field technicians must embrace new skills to remain relevant and carry out operations according to the latest standards.
1. Technical Proficiency
Field technicians need a strong foundation in technical knowledge, including the specific workings of equipment and machinery in their industry as well as familiarity with field service software. Only a technically proficient field professional can rightly diagnose, repair, and maintain equipment. Technicians must be adept at quickly interpreting technical manuals and diagrams and implementing the standards in the operations. Below are key skills expected of field professionals on the technical front.
- Understanding of Tools and Equipment
- Knowledge of Relevant Software and Systems
- Problem-Solving
Field technicians handle various tools daily, from basic wrenches and screwdrivers to advanced diagnostic devices. They must know how to and when to use these tools as each tool serves a specific purpose. Technicians must also understand equipment calibration, measurement tolerances, and maintain the tool set to perform the job without interruptions.
With industries increasingly relying on digital solutions, field technicians must know how to use various software systems used by the organization for field operations management; they must quickly adapt to new technologies. For instance, a business might be using a computerized maintenance management system (CMMS), so it is an imperative that each technician is familiar with using CMMS for maintenance operations. They must know each feature of the software, including scheduling, reporting, and inventory management works for their task.
Each field service issue comes with its own set of challenges. There are times when field technicians have to use their estimation abilities and critical issues require them to go to the root cause of the problem. They must remain vigilant of the insights that various field service metrics offer. All this calls for strong problem solving skills required to tackle unexpected challenges daily.
2. Other Important Skills and Abilities
Apart from technical skills, a field technician has to possess and demonstrate a range of skills and abilities which are important to succeed in their role as a field professional. These are:
- Communication Skills
- Time Management and Organization
- Physical Stamina and Dexterity
- Customer Service Orientation
Soft skills are essential like any other skills for field technicians. They must articulate complex information in a way that clients understand without feeling overwhelmed. As a result, effective communication is key for explaining technical issues to clients and collaborating with colleagues.
Good communication isn’t restricted just to communicating with stakeholders but also important for documenting the work and coordinating the workforce dispatch and scheduling process. The technician must meticulously note the findings as any mistake may convey wrong information to the technician who will use the documentation as a reference.
A day for a field technician typically involves several appointments across different locations. Balancing multiple tasks within tight schedules requires excellent time management and organizational abilities.
Technicians must know how to prioritize tasks and maintain clear records, meet deadlines and handle unexpected calls without compromising service quality.
The physically demanding nature of the job means field technicians should have good stamina and dexterity. They have to climb ladders, handle heavy equipment, maneuver in confined spaces, and so they must be in good physical shape.
Physical endurance directly impacts productivity and job satisfaction, as technicians who can handle physical challenges perform more effectively.
Clients expect courtesy, respect, and patience from technicians, especially in stressful situations where equipment has failed. So, in a way, field technicians embody the company’s values on the ground by bringing exceptional customer service skills.
By understanding client concerns, addressing issues efficiently, and providing a positive service experience, technicians contribute to customer satisfaction and retention. It is important to remember that while the right skills elevate customer satisfaction, on the reverse, wrong technician habits harm customer experience.
What Industry Should Hire a Field Service Technician?
When thinking about which industries should hire a field service technician, it’s important to understand how these technicians serve businesses on the ground. Field service technicians bring the hands-on skills needed to maintain, repair, and install equipment right and following are some industries to which they are important:
- Manufacturing
- Healthcare
- Telecommunications
- Energy
- HVAC
- Retailers
- Construction
- Automotive
- Aerospace
- Mining
Technicians are in the thick of manufacturing, repairing and maintaining everything from assembly lines to production robots. Their presence is important when something goes wrong. Instead of a halt in production, they fix the problem swiftly, and get operations back on track quickly.
In healthcare, from imaging machines to life-support systems, every piece of equipment needs to be up to scratch. Field service technicians are the ones who ensure that medical devices are regularly maintained and repaired, ensuring that hospitals, clinics, and healthcare centers operate without equipment failures interrupting patient care.
Technicians travel to different sites – from cell towers to data centers – to install, repair, and maintain essential systems. With constant demands on the network, they keep everything from wireless connections to broadband networks running without interruption.
Keeping the lights on isn’t as easy as flipping a switch. Field service technicians in energy and utilities ensure that everything from power plants to water pipelines is in working order. Their work has a direct impact on everyday life, ensuring that homes and businesses remain powered and connected.
When your heating or air conditioning system goes out, you call an expert. Technicians in HVAC are essential to keeping people comfortable, whether it’s repairing a furnace in the middle of winter or fixing an air conditioning unit during a heatwave.
Retailers who sell home appliances and consumer electronics depend on field service technicians to handle everything from installation to repairs. When a customer buys a washing machine, refrigerator, or television, they expect it to work right out of the box. If it doesn’t, a technician steps in to troubleshoot and fix the issue.
Heavy equipment in construction needs constant attention, and when something breaks, it’s up to a technician to get it back on track. Whether it’s a crane, bulldozer, or excavator, field service technicians maintain and repair the machinery that’s the heart of any construction project.
Whether it’s fixing a broken-down car on the side of the road or maintaining a fleet of trucks, field technicians are the ones who provide on-site repairs or maintenance. These technicians offer convenience and reliability, and keep cars and trucks on the move and businesses running smoothly.
The industry relies on complex machinery and technology to keep planes and spacecraft flying safely. Field service technicians in this sector are responsible for performing checks, making repairs, and upgrading parts on aircraft to ensure they stay in top working condition.
Technicians are needed on-site to maintain and repair the heavy-duty equipment – operating in harsh conditions – used for extracting resources. They help avoid costly downtime by ensuring that drilling rigs, bulldozers, and conveyor systems are up and running without fail.
What Qualifications Are Expected from a Field Service Technician?
The qualifications for a field technician can vary depending on the industry and specific job requirements. However, below are the general qualifications expected from a field technician:
- Educational Background
- Vocational Training or Technical School
A high school diploma or GED serves as the foundation for many field service technician roles. However, some positions demand more specialized education. For example, a technician working with complex electronics might need an associate degree in electronics technology or a certification in electrical systems.
Technicians handling IT services are often required to hold a degree in information technology or complete certifications like CompTIA A+ or Network+. Alongside, having expertise in using predictive analytics for field service improvement is always a plus. Mechanical service technicians, on the other hand, typically need training in mechanical engineering or related fields.
To stay ahead, technicians should pursue additional education, such as online courses or certifications, from reputable platforms like Coursera or edX. Taking these steps helps build a stronger skillset and opens doors to higher-level positions..
Technicians are expected to pursue additional training through vocational programs or technical schools, where they gain hands-on experience with industry-specific tools and machinery. In fact, training is an important step to building a great field service brand and must be positively looked at by both businesses as well as technicians.
What are the Certifications Required for a Field Service Technician?
Following are the certifications that will give field technicians an edge and enhance their capabilities. We divide these certifications in two categories which are:
- Industry-Specific Certifications
Along with technical expertise and experience, the following certifications attest to the capability of field technicians:
- CompTIA A+
- NATE (North American Technician Excellence)
- ASE (Automotive Service Excellence)
- Certified Electronics Technician (CET)
- HVAC Excellence Certification
- National Institute for Certification in Engineering Technologies (NICET)
- EPA Section 608 Certification
- Certified Fiber Optic Technician (CFOT)
- Safety Certifications (e.g., OSHA)
Occupational safety and health standards must be known and followed by technicians on the field. The following safety certifications prove invaluable in this regard across industries:
- OSHA 10-Hour or 30-Hour Certification
- American Red Cross First Aid/CPR/AED
- NEBOSH (National Examination Board in Occupational Safety and Health)
- IOSH (Institution of Occupational Safety and Health)
- Confined Space Entry and Rescue
- HAZWOPER (Hazardous Waste Operations and Emergency Response)
- NFPA 70E (National Fire Protection Association)
- Fire Safety and Emergency Response
- Scaffold User Training
- ISO 14001 (Environmental Management Systems)
- EPA (Environmental Protection Agency) Certifications
- OSHA Forklift Certification
- PPE Awareness Training
- Ongoing Training and Professional Development
The field technician role constantly evolves, with new technologies and methodologies emerging. Technicians must pursue ongoing training to stay competitive and deliver top-quality service. Employers often provide access to workshops, online courses, or in-house training sessions, encouraging technicians to keep their skills sharp.
Job Levels and Positions
Job levels and positions in field service progress based on experience, expertise, and responsibilities. There are numerous job opportunities available in the area. Below are the common technician job levels and positions for field technicians:
- Entry-Level Positions
- Mid-Level and Senior Positions
- Opportunities for Specialization
These roles are ideal for recent graduates and individuals with limited experience. The positions focus on basic installations, routine maintenance, and assisting experienced technicians.
As technicians gain experience, they qualify for mid-level and senior roles that involve complex diagnostics, client management, and oversight of junior staff. At senior positions, technicians lead projects, contribute to process improvements, and manage the field service function. Those who venture into sales have to achieve targets as defined by standard field service sales KPIs.
There are numerous opportunities to specialize in field service, and technicians should develop expertise in a niche area. For instance, a technician should specialize in medical equipment, fiber optics, or renewable energy systems.
Field Services Technician Salary
Field Service Technician salaries vary widely based on experience level, job role, and geographic location. The demand for skilled technicians is high, resulting in competitive salaries. Indeed.com lists more than 13,000 opportunities, while LinkedIn features over 11,000 openings for field service technicians.
As per the Bureau of labor statistics, in 2023, for professionals working in installation, maintenance, and repair occupations, $53,920 was the median annual salary higher than that of in other groups.
The international field service engineer salaries, as per ZipRecruiter, range from $36,500 to $105,000 with the average salary being $71,220. If we talk in general, below are the estimates for the US based on multiple sources:
Role |
Average Annual Salary |
Source |
Field Service Technician I |
$48,000 – $50,000 |
PayScale |
Field Technician Engineer |
$70,000 |
Glassdoor |
Senior Field Service Engineer |
$92,000 |
ZipRecruiter |
Regional Service Technician |
$61,000 |
Indeed |
Best Practices for Field Technicians
Field technicians face a diverse range of environments and challenges in their day-to-day work. To navigate these challenges, along with using previous experience, it is important for technicians to adhere to the following best practices so that the job is done right, safely, and efficiently.
- Stay Updated with Industry Trends
- Maintain High Standards of Safety
- Be an Effective Communicator
- Possess Strong Problem-Solving Skills
- Keep Accurate and Detailed Records
- Emphasize Preventative Maintenance
- Be Digital Savvy
- Be Customer-focussed
Continuous learning is a trait of strong field service professionals. Technicians should consistently follow industry news, attend workshops, and participate in professional groups to stay informed on trends and innovations. They must know how field service contracts work and be updated about the ongoing changes.
While adhering to established procedures like using protective gear is one key criteria for remaining safety compliant, field technicians should also use software to improve safety, by tracking various safety metrics. Safety protocols not only reduce accident risks but also reflect professionalism, which instills client confidence.
There are various stakeholders in field service, including clients, colleagues, and vendors. Field technicians must maintain open communication channels with all of them to remain clear about expectations, provide updates, and address questions or concerns.
Technicians are encouraged to adopt structured problem-solving methods to address issues systematically. They must ensure efficient implementation of the right techniques to solve the problems perfectly.
Maintaining comprehensive records benefits all parties involved. Detailed logs ensure that service history is accessible, enabling technicians to make informed decisions in future visits.
Preventive maintenance extends the lifespan of equipment and reduces the likelihood of emergencies. By prioritizing regular check-ups, field technicians help clients save money and achieve long-term reliability in their systems.
As most team members operate remotely from diverse locations, strong digital acumen becomes a default requirement for field technicians. They must know how to use the power of data visualization for better decision-making. When using a field service app, they must know how to use each of its features so that operations take place smoothly.
Sustaining relations with customers is a key responsibility on the shoulders of field technicians. They must understand the importance of customer feedback in field service and know how to use it to improvise service levels. Ultimately customer retention rests on the quality of service they deliver.
Conclusion
As industries evolve and become more reliant on specialized technologies, the demand for skilled field technicians grows. Businesses must focus on developing their technicians to handle the increasing complexity of systems. They must focus on developing their field service team to handle the increasing complexity of systems.
Finally, businesses must understand the value of this role and invest in their job growth. With technology becoming increasingly central to business success, this role is expected to assume new dimensions which businesses must embrace proactively.