Top Reasons Maintenance Backlogs Spiral Out of Control (and How Leaders Optimize Them)
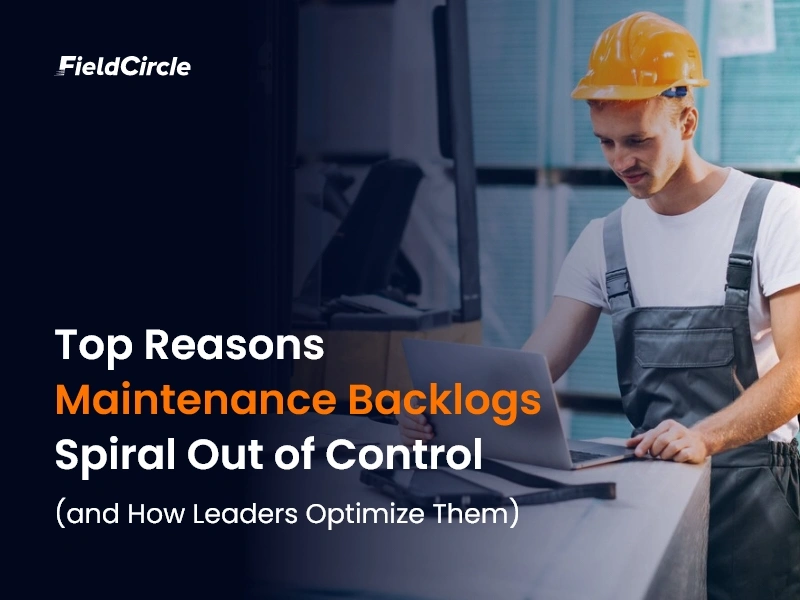
Many maintenance leaders grapple with a growing wave of overdue tasks that threaten schedules, budgets, and operational reliability.
According to reports, 82% of companies experience unplanned downtime that interferes with planned maintenance. The impact is anything but small—annual losses in manufacturing due to such disruptions have been estimated at a staggering $50 billion.
Ideally, a maintenance backlog should equal about 2–3 weeks of work. Anything beyond four weeks is a sign that the process is veering off track. Once it surpasses that threshold, teams often find themselves on the brink, facing higher costs, more frequent breakdowns, and operational chaos.
Let’s explore the most common reasons maintenance backlogs grow out of control and the proven strategies that high-performing leaders use to regain control and keep things running smoothly.
1. Chronic Resource Constraints (Labor and Budget Shortfalls)
A lack of resources—whether it’s people, skills, or budget—is one of the most common culprits for growing maintenance backlogs. With ongoing labor shortages, many teams are stretched thin, leading to employees becoming overburdened, which in turn increases the likelihood of delays.
According to reports, the U.S. manufacturing sector alone could see up to 2.1 million job vacancies by 2030, and maintenance technicians are among the hardest to recruit. On top of labor shortages, budget constraints force companies to cut corners on preventive maintenance (PM) and equipment reliability programs.
Maintenance can account for anywhere between 20% to 50% of an enterprise’s operating budget. But still it can be one of the first areas targeted for cost reduction. The combination of resource shortfalls leads to deferred work, which then compounds over time and creates a growing backlog.
How Leaders Optimize:
- Cross-train technicians across different equipment types to maintain staffing flexibility.
- Partner with trade schools and apprenticeship programs to build a skilled talent pipeline.
- Empower operators with basic maintenance tasks to reduce reliance on specialized technicians.
- Outsource non-core tasks to free up in-house resources for critical maintenance.
- Quantify deferred maintenance costs to secure additional resources and justify ROI.
2. Reactive Maintenance and the Firefighting Cycle
Many organizations fall into a reactive maintenance trap, constantly addressing breakdowns and emergency repairs instead of proactive, planned tasks. When a company relies too heavily on reactive maintenance, the focus shifts away from preventive measures, which are often the first tasks to get delayed when emergencies arise.
While nearly 90% of manufacturers claim to have a preventive maintenance program in place in their plants, only 38% of their assets are typically covered by such plans. This discrepancy means the majority of assets continue to run until failure, contributing to an inefficient and costly reactive cycle.
How Leaders Optimize:
- Set clear goals to increase the ratio of planned-to-unplanned maintenance, prioritizing preventive tasks.
- Negotiate scheduled downtime with production departments to minimize disruptions while performing maintenance.
- Invest in predictive maintenance technologies to monitor equipment and predict failures before they occur.
- Establish separate teams for emergency and planned tasks, ensuring routine maintenance isn’t neglected during crises.
- Use root cause analysis to address recurring breakdowns and reduce unplanned maintenance.
3. Poor Planning, Prioritization, and Tracking Processes
Many teams still rely on outdated systems—whiteboards, sticky notes, or email chains—to track and manage work orders. Such informal systems make it easy for tasks to get lost or mis-prioritized.
Without standardized procedures, maintenance tasks can become delayed, rescheduled multiple times, or missed entirely.
The lack of efficient planning and prioritization exacerbates the backlog problem, as does the tendency for scheduling inefficiencies that lead to uneven workloads.
How Leaders Optimize:
- Invest in a computerized maintenance management system (CMMS) or enterprise asset management i.e. EAM platform to centralize tracking, scheduling, and prioritization for better visibility.
- Use priority codes (Critical, High, Medium, Low) to assign tasks based on urgency and importance.
- Involve technicians in creating priority criteria to ensure practical experience is considered in task prioritization.
- Hold weekly planning meetings to reassess and reallocate tasks for effective resource deployment.
- Track work order aging and backlog size to provide clear progress updates and identify areas needing attention.
- Segment the backlog into categories (Plannable, Planned, Ready to Execute) to make the workload more manageable.
4. Inadequate Spare Parts and Materials Availability
Without the right parts, technicians cannot complete work orders on time, and tasks are marked as “awaiting parts,” which may stretch for days or even weeks. Poor inventory management, coupled with budget restrictions that discourage stockpiling essential parts.
In wake of these issues, maintenance teams struggle to balance maintaining sufficient stock while avoiding overstocking due to financial limitations. A “just-in-time” strategy might reduce costs, but it becomes problematic when parts are in high demand or difficult to obtain in a timely manner.
Global supply chain disruptions have only worsened these challenges. With rising shipping costs, extended lead times, and shortages of raw materials, accessing critical parts on time has become increasingly difficult.
How Leaders Optimize:
- Maintain critical spares inventory and set up automated reordering systems to avoid stock shortages.
- Use a CMMS to track part consumption, lead times, and stock levels for better inventory visibility.
- Build relationships with multiple suppliers to ensure backup options are available when needed.
- Categorize inventory into fast-moving, critical, and long-lead items to prioritize stocking decisions.
- Schedule preventive maintenance around parts availability, considering lead times for critical components.
- Create emergency kits with frequently failing components to ensure technicians are always prepared.
5. Lack of Leadership Alignment and Support
When top management fails to recognize the value of maintenance, support for the function often declines. Without leadership backing, maintenance becomes an afterthought, and critical resources—such as staffing, budget, and strategic focus—are withheld. The lack of support undermines the effectiveness of maintenance teams.
Additionally, when leadership sets unrealistic targets or focuses too heavily on short-term production goals, it detracts from the long-term health of assets. In such cases, preventive maintenance is deprioritized in favor of immediate production demands, which lead to more frequent equipment failures..
When the importance of preventive work is overlooked, reactive maintenance becomes more common, creating a vicious cycle of escalating issues. A lack of strategic alignment further hinders the development of a proactive maintenance culture, making backlog management even more difficult.
How Leaders Optimize:
- Translate technical metrics into business impacts, like downtime costs and lost throughput, to communicate maintenance’s importance.
- Use visual dashboards to highlight maintenance’s role in uptime and ROI, showcasing its strategic value.
- Align KPIs across departments (e.g., MTTR, OEE, downtime) to ensure maintenance goals support production and business objectives.
- Incorporate maintenance input in capital planning and scheduling to anticipate resource needs and prioritize work effectively.
- Champion a reliability culture across the organization, emphasizing maintenance as a key component of operational success.
6. Inefficient Communication and Workflows
A poorly managed communication process often results in critical details being lost or misinterpreted. Without clear communication, tasks may be duplicated, ownership becomes unclear, and deadlines are missed.
When information isn’t accurately passed on, technicians do not have the full context of an issue, which leads to repeated work or errors. The lack of clarity directly impacts efficiency and contributes to delays in resolving problems.
Handoffs between shifts or teams are another potential weak point in the workflow. When these transitions are not carefully managed, important information can be overlooked, which causes inefficiencies or misunderstandings. As maintenance teams work across multiple shifts or departments, these communication gaps can become significant sources of delays, and compound the backlog issue.
How Leaders Optimize:
- Standardize work requests and reporting forms to capture and transmit all relevant information effectively.
- Adopt mobile maintenance apps for real-time updates and seamless communication between field and office teams.
- Conduct shift handover meetings or use digital logs to provide incoming teams with full context of ongoing work.
- Develop clear SOPs and checklists for routine tasks to ensure consistency and smooth task transitions.
- Involve stakeholders early in planning to align departments and reduce delays from misunderstandings or shifting priorities.
7. Lack of Skill Diversity and Knowledge Retention
Even with an adequate team size, skill gaps can limit the completion of certain tasks. Many maintenance departments rely heavily on a few senior technicians who have extensive knowledge of legacy systems.
The loss of experienced personnel doesn’t just affect knowledge transfer—it also disrupts the ability to handle complex systems efficiently. Senior technicians often manage critical or specialized tasks, and without proper succession planning or documentation, their departure can stall progress. The knowledge drain intensifies the backlog as the team struggles to manage the increased workload.
Newer technicians, who may be less familiar with advanced or legacy equipment, face a steep learning curve. Without comprehensive training, their ability to tackle complex issues is limited, which slows down the maintenance process. As a result, the backlog continues to grow, as these technicians require more time to resolve problems that experienced staff could address more quickly.
How Leaders Optimize:
- Invest in training programs focusing on both technical skills and cross-training across asset types.
- Build a skills matrix to visualize team capabilities, identify gaps, and plan future training.
- Establish mentorship programs to allow experienced workers to share knowledge with junior technicians.
- Document procedures and lessons learned in the computerized maintenance management system application to prevent knowledge loss when key personnel leave.
- Rotate technicians through different areas or asset types to create a flexible and adaptable workforce.
8. Poorly Defined Maintenance Scope and Responsibilities
When teams aren’t sure who is responsible for certain tasks, valuable time is spent debating or clarifying ownership. The misalignment results in duplicated efforts or incomplete work.
Without clear boundaries between maintenance and production roles, tasks may be handled inefficiently, as each team will assume the other is responsible. There are errors and the time is wasted, and critical work gets overlooked or delayed. Such confusion strains resources.
The absence of defined responsibilities also leads to missed deadlines and delayed progress. As teams overlap in their duties or misunderstand the scope of work, tasks are either postponed or inadequately addressed. The resulting inefficiencies create a cycle of delays that becomes harder to manage over time.
How Leaders Optimize:
- Clearly document roles and responsibilities in collaboration with all stakeholders to eliminate ambiguity.
- Use maintenance responsibility matrices and RACI charts to provide visual clarity on roles.
- Conduct joint training sessions between maintenance and production teams to foster shared understanding.
- Align scope definitions with KPIs to promote accountability and efficiency.
9. Unreliable Work Request Intake
If maintenance requests are not submitted properly, including the relevant details and priority level, planners end up wasting time collecting missing information. Without complete and accurate details, they may also misjudge the urgency of tasks, only resulting in unnecessary delays in work assignment.
When requests lack clarity, planners are forced to seek repeated clarifications, as it consumes valuable time that could be better spent addressing the actual maintenance tasks. As a result, the planning process becomes disjointed, causing delays in scheduling and extending the time needed to resolve issues.
Moreover, incorrect or incomplete maintenance requests lead to work being misprioritized, further disrupting the workflow. If the urgency of a task is not properly communicated, critical issues might be postponed in favor of less important work.
How Leaders Optimize:
- Standardize the work request format by implementing digital portals with mandatory fields like asset ID and fault description.
- Train non-maintenance personnel on proper request submission to eliminate upstream inefficiencies.
- Audit requests periodically for completeness and quality to reinforce standards and improve turnaround times.
10. Ineffective Use of Data and Analytics
Without meaningful insights into backlog trends, asset performance, and technician efficiency, leaders struggle to make informed decisions. They cannot identify root causes of delays or inefficiencies.
While maintenance teams might collect data in vast amounts, absence of the right tools or expertise to transform this information into useful insights will keep the business in the backseat. Also, decision-makers are overwhelmed with raw data but unable to extract the key patterns or trends that can drive improvements. The data overload makes it harder to focus on areas that need attention.
Additionally, without clear visibility into performance metrics, leaders are unable to track progress or measure the effectiveness of current strategies. Without accurate insights into technician performance or asset health, identifying areas for improvement becomes a challenge.
How Leaders Optimize:
- Use dashboards and reports to track backlog aging, recurring failures, and PM compliance rates.
- Leverage analytics tools to predict asset failures and identify resource wastage.
- Prioritize actionable KPIs and update them weekly to drive continuous improvement.
- Hold regular performance review meetings based on data to foster accountability and transparency.
11. Unreliable or Outdated Asset Data
Backlogs also stem from inaccurate or outdated asset registers, missing maintenance histories, or incomplete bills of materials. Absence of these details misguide technicians, which leads to errors in parts ordering, tool allocation, or estimating job duration.
Incorrect or missing critical asset information disrupts the entire maintenance operations. In such a case, technicians end up with the wrong parts or tools, causing them to waste valuable time reworking tasks or waiting for the correct components. These mistakes compound inefficiencies throughout the workflow.
Inaccurate asset data also impacts job scheduling and prioritization of maintenance tasks. Without accurate maintenance histories, technicians overlook recurring issues or misjudge the urgency of certain tasks.
How Leaders Optimize:
- Invest in periodic asset audits to validate records and update key data fields like location and condition.
- Integrate sensors or IoT devices to automate condition data collection and enable real-time health monitoring.
- Encourage field technicians to validate and update asset data during every work order execution, fostering continuous improvement.
- Set up a structured hierarchy within the CMMS and attach digital schematics or manuals for better planning and fewer surprises in the field.
12. Deferred Capital Investment in Equipment
When aging equipment is kept in service beyond its economic life, maintenance demands escalate quickly. The backlog fills up with recurring failures, emergency repairs, and more complex fixes.
Additionally, management’s reluctance to replace or refurbish outdated assets leads to throwing good money after bad. Instead of investing in long-term solutions, resources are spent on short-term fixes, which don’t address the root cause of the problem.
Technicians find themselves stuck constantly dealing with temporary fixes, which often fail again shortly after completion. The approach prolongs the backlog, as each failure demands additional attention. The inability to modernize or replace aging equipment results in escalating maintenance costs which makes it harder to stay on top of routine maintenance.
How Leaders Optimize:
- Quantify long-term costs of aging equipment, including downtime, labor hours, and lost productivity, to influence capital planning.
- Use lifecycle costing models to build stronger business cases for asset renewal.
- Prioritize preventive strategies on newer equipment to slow deterioration and prevent backlog shifts.
- Align with finance and engineering to develop a long-term asset replacement roadmap, smoothing out investment decisions.
13. Inflexible Maintenance Schedules and Rigid Workflows
Strictly adhering to time-based schedules without considering asset conditions or actual workload can lead to significant inefficiencies. In such circumstances, maintenance teams end up performing unnecessary preventive maintenance (PM) tasks simply to meet schedule targets, while more urgent jobs accumulate.
When schedules are rigid and don’t factor in the real-time needs of assets, technicians are forced to follow prescribed routines even when they’re not necessary.
An over-reliance on inflexible workflows also limits the team’s ability to adapt to unexpected changes. Whether due to sudden equipment failures, unplanned downtime, or urgent requests, the inability to shift priorities quickly results in delays.
How Leaders Optimize:
- Implement condition-based and predictive maintenance to prioritize tasks based on actual asset wear or performance indicators.
- Adopt dynamic planning that adapts to real-time conditions, technician availability, and changing production priorities.
- Create flexible workflows that allow for task reallocation or bundling (e.g., performing several PMs on adjacent equipment in one visit) to clear the backlog faster.
Takeaway
A maintenance software becomes essential if you are aiming to take backlog management to a whole new level. By providing a centralized platform to track, prioritize, and allocate resources effectively, it leaves no task slipping through the cracks. To stay on top of things, implement FieldCircle and there will be no scope for backlogs to derail your operational goals.