What is a Preventive Maintenance Schedule? 8 Steps to Create a PM Schedule
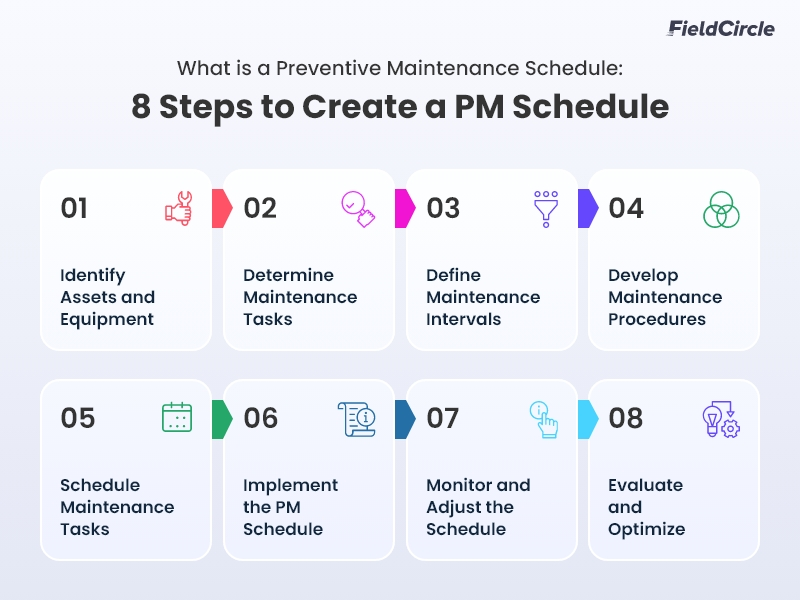
Preventive maintenance scheduling is the process of setting up a structured maintenance plan where tasks are performed routinely at fixed times, rather than reacting to problems as they arise. The main aim of the strategy is tomaintain the equipment in peak condition ever. It is a key part of preventive maintenance strategy and determines how maintenance teams execute their preventive maintenance plans to sustain the maintenance efficiency.
A solid preventive maintenance plan integrates both fixed preventive maintenance schedule and floating preventive maintenance schedule.
Fixed schedules consist of time-based tasks, such as monthly inspections and quarterly filter changes, ensuring routine upkeep.
On the other hand, floating schedules adjust based on the actual condition or usage of the equipment, like scheduling an oil change after a certain number of operating hours.
We help you delve into the concept of preventive maintenance schedule by exploring its significance and outlining practical steps to create a successful maintenance schedule.
What Is Preventive Maintenance?
Preventive maintenance (PM) is a process in which routine maintenance tasks are performed on equipment or assets to avoid unexpected failures and reduce downtime.
Unlike reactive maintenance, which focuses on fixing problems after they occur, preventive maintenance comprises conducting scheduled inspections, repairs, and part replacements to keep assets running smoothly and extend their operational lifespan.
An important part of the entire preventive maintenance program, its ultimate goal is to minimize the risk of unplanned breakdowns, optimize asset performance, and reduce long-term maintenance costs.
8 Steps to Create a Preventive Maintenance Schedule
Creating an effective preventive maintenance plan and schedule is a systematic process that requires thorough planning and attention to detail. Let’s walk through the steps necessary to develop an effective PM schedule for any organization.
1. Identify Assets and Equipment
The first step in creating a preventive maintenance schedule is to compile a comprehensive list of all assets and equipment that require regular maintenance. This is vital for knowing what to track and maintain. Businesses have a variety of equipment with different maintenance needs, so it’s important to categorize them effectively. Grouping assets based on their type, importance to operations, and maintenance requirements allows maintenance teams to prioritize tasks and focus on high-impact areas.
In manufacturing, equipment is grouped by categories such as electrical systems, hydraulic machines, and conveyor belts. Each group will have different maintenance needs. While some equipment will require weekly lubrication, others will only need quarterly inspections. By identifying and categorizing assets, maintenance personnel are thus able develop a more focused and manageable PM schedule.
It’s also important to consider the criticality of each asset. Equipment that plays a key role in production should be at the top of the priority list. For instance, Ford Motor has experienced challenges with its critical production robots. These robots are key to their assembly lines, so maintaining them at frequent intervals has become a high priority. Failure to maintain these robots has previously resulted in production delays.
2. Determine Maintenance Tasks
Once assets have been identified and categorized, the next step is to determine the specific maintenance tasks required for each. This involves reviewing maintenance manuals provided by equipment manufacturers and analyzing past maintenance records to pinpoint common issues. Maintenance manuals typically provide recommended tasks such as replacing parts, checking fluid levels, or conducting inspections. These should serve as the foundation for your maintenance task list.
Past maintenance records offer valuable insights into recurring problems or frequently failing components. If a particular machine frequently experiences belt wear, adding a task to inspect and replace the belt regularly helps prevent future breakdowns.
Compliance with industry regulations and standards is also essential during this step. Certain industries, such as aviation and healthcare, are heavily regulated, and failure to adhere to these standards lead to costly fines or safety risks. In these cases, maintenance tasks should align with regulatory guidelines to avoid any non-compliance issues. Companies like Delta Airlines rely heavily on maintenance manuals and historical maintenance data to guide their maintenance schedules.
In the healthcare sector, diagnostic imaging equipment like MRI machines requires strict preventative maintenance to remain in compliance with health standards. Following manufacturer recommendations and regulatory requirements helps avoid safety violations and equipment failures that can affect patient care.
3. Define Maintenance Intervals
The timing of maintenance tasks is just as important as the tasks themselves. Determining appropriate maintenance intervals requires analyzing how frequently equipment is used, the working conditions it’s exposed to, and its past performance. Machines that run 24/7 will require more frequent checks than equipment that is used occasionally.
Maintenance intervals are based on time, such as weekly, monthly, or quarterly checks. In other cases, intervals depend on usage. Maintenance will be scheduled after a specific number of operational hours or miles traveled. In transportation, fleet managers typically set intervals for vehicle maintenance based on mileage. A trucking company will schedule oil changes every 10,000 miles and tire inspections every 25,000 miles to ensure vehicles remain roadworthy.
In industries such as manufacturing, maintenance schedules will also be based on certain conditions, such as vibration levels or temperature. Monitoring equipment conditions through sensors enables maintenance teams to identify potential issues before they lead to breakdowns. If a sensor detects abnormal vibration in a machine, the PM schedule triggers an inspection to address the issue before it escalates.
Defining maintenance intervals based on equipment usage and condition data helps reduce unnecessary maintenance while keeping assets in peak condition.
4. Develop Maintenance Procedures
Maintenance tasks must be carried out according to standardized procedures to ensure consistency and accuracy. Detailed procedures for each task are critical to ensure maintenance personnel know exactly what steps to follow and how to perform tasks correctly.
Each procedure should include a clear list of required tools and materials, which ensures technicians are well-prepared before starting the task. Replacing an air filter on an HVAC unit will require specific tools such as a wrench and replacement filter. By listing these items in the maintenance procedure, teams save time and avoid disruptions during maintenance activities.
In addition to the step-by-step instructions, safety precautions and protocols should be incorporated into each procedure. Working on heavy machinery or electrical systems comes with inherent risks, so outlining safety steps such as turning off power sources or using protective gear is essential. Procedures should be written in a way that’s easy to follow, using plain language and avoiding unnecessary jargon.
At Tesla’s manufacturing plant, their industrial robot maintenance procedure for handling robotic arms includes specific steps for safely de-energizing the machines before technicians begin working. This structured approach not only enhances worker safety but also reduces downtime, ensuring improved overall maintenance efficiency.
5. Schedule Maintenance Tasks
Once maintenance tasks and procedures have been defined, they need to be distributed across a calendar to create a working schedule. Create a floating preventive maintenance schedule to avoid overwhelming the maintenance team or disrupting operations. Using a calendar allows teams to plan ahead and allocate resources efficiently.
Many organizations use computerized systems like computerized maintenance management system (CMMS) to handle scheduling. A CMMS automates the scheduling process by sending reminders when maintenance tasks are due and assigning them to the appropriate team members. These systems also track maintenance history and generate reports that allow maintenance managers to review completed tasks and identify trends.
Personnel availability and expertise are key factors in scheduling. Tasks should be assigned based on team members’ skills and availability. A task that requires electrical expertise should be assigned to a technician with the necessary qualifications. If maintenance teams are small, rotating shifts and scheduling tasks during off-hours helps minimize disruptions to production.
For instance, in leading businesses, the team uses a CMMS system that automates the scheduling of routine maintenance tasks for its bottling machines. The system notifies technicians when tasks such as lubrication and part replacements are due, and it tracks the history of repairs and replacements. Such a system helps in significantly reducing downtime and maintaining efficiency in its production lines.
6. Implement the PM Schedule
After the schedule has been finalized, the next step is implementation. Maintenance staff and other relevant personnel should be informed about the new schedule, their responsibilities, and any changes to their daily tasks. Clear communication ensures that everyone is aware of upcoming maintenance activities and knows what is expected of them.
Training is also a key component of implementing a preventive maintenance schedule. Even experienced technicians benefit from refresher training on specific procedures, tools, and safety protocols. Proper training minimizes the risk of errors during maintenance activities and helps maintain a safe working environment.
Documentation is another important part of implementation. Maintenance teams should document all completed maintenance tasks, including details such as the date of completion, any parts replaced, and any issues encountered. For organizations such as The U.S. Army Corps of Engineers, PM Schedule helps meticulously maintain heavy-duty machinery and infrastructure across the country.
7. Monitor and Adjust the Schedule
A preventive maintenance schedule is not set in stone; it requires ongoing monitoring and adjustment to remain effective. Periodic reviews of the schedule help identify areas for improvement. If certain equipment rarely experiences issues, maintenance intervals will be extended to reduce unnecessary tasks. Conversely, equipment that shows signs of wear more frequently will require more regular attention.
Gathering feedback from maintenance staff and equipment operators provides valuable insights into how well the schedule is working. Maintenance teams are on the front lines, so they are well-positioned to identify any inefficiencies or gaps in the schedule.
In organizations like Amazon, after implementing their preventive maintenance system in their fulfillment centers, the maintenance team will regularly analyze feedback from workers operating the automated robots. If certain robots require more frequent checks due to wear on specific components, the team will adjust their PM schedule and implement shorter intervals for these robots.
8. Evaluate and Optimize
The final step in maintaining a successful preventive maintenance schedule is continuous evaluation and optimization. Organizations should track key performance indicators (KPIs) such as equipment uptime, maintenance costs, and failure rates to assess the schedule’s effectiveness. By analyzing these metrics, maintenance teams are able to identify areas where improvements are needed.
Tracking equipment uptime helps identify whether the PM schedule is successfully preventing downtime. If equipment failure rates remain high despite regular maintenance, further investigation will be necessary to pinpoint the root cause and adjust the schedule accordingly.
Data-driven decision-making is critical to optimizing a PM schedule. Analyzing data trends, such as which equipment requires the most maintenance, helps maintenance teams focus their efforts where they are most needed. It also enables them to fine-tune maintenance intervals, procedures, and resource allocation for better results. In a hi-tech industry like semiconductor, this is a critical step.
Tools and Resources Required for Preventive Maintenance
- Computerized Maintenance Management System (CMMS)
- Enterprise Asset Management (EAM) Software
- Maintenance Scheduling Templates
- Checklists
- Condition Monitoring Sensors
- Mobile Maintenance Applications
- Preventive Maintenance Scheduling Software
- Barcoding and RFID Systems
A CMMS software is one of the most comprehensive tools for preventive maintenance scheduling. It allows for automation of scheduling, tracking of maintenance activities, and easy access to asset histories. CMMS tools are essential for organizations managing large amounts of equipment, as they help organize tasks, assign work orders, and monitor maintenance performance metrics.
EAM software focuses on managing the entire lifecycle of physical assets, from acquisition to disposal. It includes scheduling maintenance tasks, tracking costs, and integrating with other systems like procurement and inventory management. An asset management software is ideal for large enterprises with multiple facilities.
Templates serve as a guide for creating maintenance schedules. These tools include predefined sections for tasks, intervals, and safety checks, making it easier to organize preventive maintenance activities. Templates are particularly useful for standardizing procedures across teams and assets.
Checklists help ensure that each preventive maintenance task is completed thoroughly. These lists outline step-by-step procedures for inspecting, cleaning, and servicing equipment. Using preventive maintenance checklists reduces the risk of missing important tasks and improves consistency across maintenance efforts.
Sensors track the real-time performance of equipment by measuring variables like vibration, temperature, and pressure. These tools are essential for predictive maintenance, triggering maintenance when equipment conditions exceed predefined thresholds, thereby helping to prevent breakdowns before they occur.
Mobile apps designed for maintenance personnel allow technicians to access schedules, maintenance work orders, and asset information on-the-go. These tools enable real-time updates, remote reporting of completed tasks, and easier communication among team members, improving efficiency in preventive maintenance tasks.
Specialized scheduling tools help organize preventive tasks by allocating resources, setting up recurring maintenance tasks, and ensuring maintenance happens at the right intervals. These tools integrate with CMMS or EAM systems to ensure smooth workflow across teams.
These tools simplify asset tracking and management, ensuring maintenance teams are able to quickly locate equipment and its service history. Barcodes and RFID tags link assets to their maintenance records, allowing for more efficient scheduling and updates to asset information.
Conclusion
Along with a solid preventive maintenance schedule you also need to create a culture of responsibility and care within your organization. You need to prioritize safety and approach with a proactive mindset which shifts maintenance from a last-minute scramble to a seamless part of daily operations.
When teams take ownership of their maintenance routines, they not only keep machinery running smoothly but also minimize disruptions and stress during busy periods. In the end, investing in a thoughtful preventive maintenance strategy pays off. All you need is a comprehensive preventive maintenance software.