10 Steps to Create a Preventive Maintenance Plan In 2025
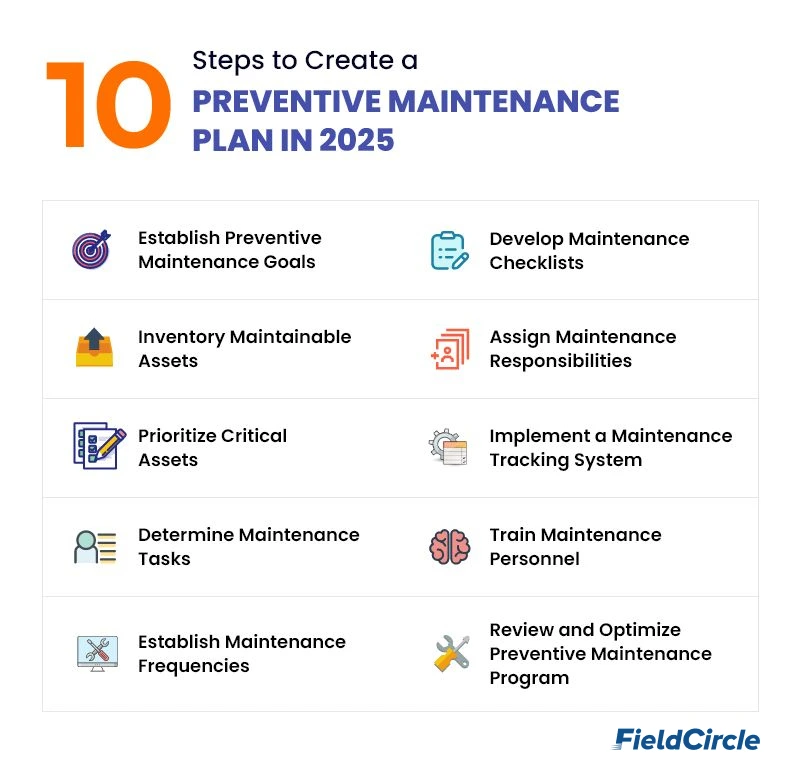
Preventive maintenance is the backbone of keeping equipment in good working order and avoiding costly disruptions for any business that relies on machinery. It is a smart maintenance approach to keep things running smoothly.
Unexpected breakdowns throw daily operations off track if not addressed in time and hit productivity and profits hard. That’s why having a well-thought-out plan in place isn’t just useful—it’s a necessity.
Creating an effective preventive maintenance plan requires setting clear objectives, identifying key assets, and staying on top of regular maintenance tasks, along with many other considerations. Each step needs scrupulous attention to keep small issues from turning into major setbacks.
We discuss more about the preventive maintenance plan and a series of well-defined steps to create it and successfully lay the groundwork for your Preventive Maintenance strategy.
What is a Preventive Maintenance Plan?
A Preventive Maintenance Plan (PMP) is a strategy that focuses on the regular upkeep and inspection of equipment, machinery, and infrastructure to prevent breakdowns and ensure operational efficiency. Rather than waiting for a failure to occur, businesses use PMPs to maintain their assets, save money, and avoid unexpected downtime.
The plans involve systematic planning, timely interventions, and the use of data to predict future maintenance needs. PMPs are highly valued across industries, from manufacturing to healthcare, because they increase reliability, extend the lifespan of equipment, and improve safety standards.
What are the 10 Steps to Create a Preventive Maintenance Plan?
Below, we discuss the 10 steps to create a preventive maintenance plan that will keep your operations running smoothly.
1. Establish Preventive Maintenance Goals
Before diving into the specifics of the plan, you must first set clear, measurable objectives. Your goals must be tailored to the nature of your operations, asset types, and even maintenance budget. Goals guide every action in the preventive maintenance plan and allow you to assess whether the plan is delivering desired results.
For instance, a production plant may aim to increase its overall equipment effectiveness (OEE) by reducing unplanned downtime by 15% over the next year. Another important goal is reducing maintenance costs by streamlining the maintenance process and minimizing emergency repairs.
When setting these goals, it is vital to keep them specific and actionable. Broad goals like “reduce downtime” or “improve efficiency” lack direction and are hard to measure. A more effective goal would be “reduce downtime of the conveyor system by 10% by the end of the next quarter by scheduling routine lubrication and inspections.” Notice how such a goal is not only specific but also linked to a timeframe and key tasks.
Additionally, consider aligning your preventive maintenance objectives with broader organizational goals. If your company’s primary goal is to reduce operational costs, your maintenance goals should reflect this by focusing on cost-effective strategies such as predictive maintenance or condition-based monitoring.
2. Inventory Maintainable Assets
Once your goals are set, the next logical step is to identify all assets that require preventive maintenance. This inventory acts as the foundation of your plan, ensuring that no equipment, no matter how small, slips through the cracks.
To start, walk through your facility, systematically documenting each piece of machinery or equipment. Include essential information such as make, model, serial numbers, location, age, and maintenance history. Some organizations use asset tags or barcodes to simplify this process, making it easier to track individual assets later on. This is possible with a custom equipment maintenance solution.
Be comprehensive during this step—don’t overlook support systems like HVAC, plumbing, or even office equipment that plays a role in overall productivity. For example, a malfunctioning air conditioning unit will not bring a production line to a halt, but it will create uncomfortable working conditions that hinder performance or lead to employee health issues.
By having a detailed list of all your assets, it becomes easier to schedule maintenance, order spare parts, and ensure timely replacements when necessary. This will ultimately prevent gaps in your maintenance plan and reduce the risk of unexpected equipment failure.
3. Prioritize Critical Assets
While every asset deserves attention, some are more essential to operations than others. Prioritizing these critical assets is a key part of preventive maintenance planning achieved through the right maintenance scheduling. Without this step, you risk devoting resources to less important assets while ignoring those that are mission-critical.
To decide which assets should be given priority, assess their impact on daily operations, costs associated with their failure, and the potential safety risks if they malfunction. Start by asking questions like, “If this asset were to fail, what would be the consequences?” and “How expensive would it be to repair or replace this asset?”
For instance, in a manufacturing plant, the production line’s motor is a part of critical equipment because its failure will halt the entire production process, leading to significant downtime and financial loss. On the other hand, a backup generator that’s rarely used may be lower on the list. Additionally, consider the age of the asset—older equipment is typically more prone to breakdowns and may require more frequent maintenance.
You will also have to factor in repair costs, time to procure spare parts, and safety implications when prioritizing assets. Once you have your list of critical assets, you’ll want to allocate more time and resources to maintaining these.
4. Determine Maintenance Tasks
With your prioritized assets in hand, it’s time to outline the specific tasks needed to maintain each one. These tasks are the building blocks of your preventive maintenance plan, and they should be detailed enough to guide your maintenance team through each step.
Some tasks are fairly standard—oil changes, belt replacements, and filter cleanings—but others will need to be tailored to the specific equipment and its operating conditions. Consider consulting your equipment manuals or the manufacturer’s recommendations to ensure your task list is accurate and complete. However, don’t limit yourself to what’s in the manual. Real-life conditions, usage patterns, and historical performance data may suggest that additional tasks or checks are required.
For example, the regular cleaning of the air filters in an HVAC system is a common preventive maintenance task, but in a factory with high dust levels, you will need to increase the frequency of these cleanings. Similarly, in a fleet management operation, tire rotations or brake inspections will be key tasks for vehicles, but you may also want to include specific tasks that address the unique wear-and-tear patterns based on driving conditions or load weights.
Once your tasks are established, break them down into specific actions with step-by-step instructions. This way, maintenance personnel will have a clear and consistent approach to each job, minimizing human error and ensuring all preventive maintenance work is done correctly.
5. Establish Maintenance Frequencies
Determining how often preventive maintenance tasks should be performed is balancing act operational demands with asset longevity. Scheduled too frequently, and you will end up over-maintaining your equipment and wasting resources; scheduled too sparsely, and you risk asset failure or reduced efficiency.
The best starting point is the manufacturer’s recommendations. Many manufacturers provide maintenance schedules in their manuals, offering guidance on the ideal timeframes for servicing. For example, an air compressor needs its filters changed every 6 months, while a conveyor belt only needs to be inspected annually.
However, real-world factors influence maintenance frequencies. If a machine is used in a particularly harsh environment or operates around the clock, it will need servicing more frequently than the manual suggests. Historical data also offers insights—if records show that a particular asset tends to break down after six months, you will have to set your maintenance intervals accordingly to avoid those breakdowns.
To simplify things, you will have to categorize your maintenance tasks into daily, weekly, monthly, and annual checklists. For instance, daily tasks will include inspecting fluid levels or checking for visible damage, while more thorough inspections or part replacements will have to be done on a quarterly or yearly basis.
6. Develop Maintenance Checklists
Checklists are a simple but highly effective way to ensure that each maintenance task is completed thoroughly and consistently. They are a hallmark of strong and smart maintenance processes. A well-constructed checklist leaves no room for ambiguity, allowing maintenance personnel to go through each step without missing any important details.
When creating these checklists, focus on clarity. Break down complex tasks into smaller, manageable steps, and use clear language to guide the person performing the task. For instance, if the task is to replace an air filter, include the exact steps: turn off the machine, locate the filter housing, remove the old filter, clean the housing, install the new filter, and restart the machine.
You must also include safety checks and measurements within these checklists. For example, a checklist for a conveyor belt includes not only lubricating the rollers but also checking the tension and wear on the belt itself. Another example would be a vehicle maintenance checklist that covers tire pressure, brake fluid levels, and engine oil changes.
Best practices suggest that you regularly update these checklists based on feedback from your maintenance team or when new equipment is added. Tailor each checklist to the asset and the complexity of the task, and make them easy to access—whether that’s in a physical binder or within a digital maintenance management system.
7. Assign Maintenance Responsibilities
Clear assignment of responsibilities is essential to the success of your preventive maintenance plan. Without defined roles, tasks can be overlooked, and accountability becomes murky. Every maintenance task needs to be assigned to a specific individual or team to avoid confusion and ensure the job gets done on time.
Roles should be defined based on the expertise and skill levels of your maintenance personnel. For instance, more technical tasks such as electrical repairs or equipment calibration should be handled by skilled maintenance technicians or engineers, while routine inspections or cleanings can be delegated to general maintenance staff. In larger facilities, some organizations divide their maintenance teams into specialized groups, such as mechanical, electrical, and HVAC teams. They use work order management capabilities in maintenance software to meticulously handle the task.
Communication is key when assigning tasks. Make sure each team member understands their responsibilities and the timeline for completing them. For example, if a critical asset is due for maintenance, there should be a clear process for notifying the responsible team and scheduling the work during a non-peak operational period.
Accountability is another important factor. Consider using a tracking system to monitor task completion and hold personnel accountable for their assigned duties. This will also allow you to see which tasks are being delayed or need follow-up, helping you maintain control over the preventive maintenance schedule.
8. Implement a Maintenance Tracking System
With so many assets, tasks, and personnel involved in your preventive maintenance plan, it’s essential to have a system in place for tracking everything. A well-organized tracking system will help you manage maintenance schedules, asset histories, and ensure that tasks are being completed as planned.
Digital tracking systems, such as computerized maintenance management systems (CMMS), offer significant advantages over manual methods. They allow you to schedule tasks, set reminders, store asset data, and generate reports on the performance of your preventive maintenance plan. For instance, a CMMS notifies you when it’s time to service a particular piece of equipment, or track how many times a specific part has been replaced, helping you spot patterns or recurring issues.
In smaller operations, simpler tools like spreadsheets might suffice, but as your facility grows or your maintenance needs become more complex, investing in a dedicated preventive maintenance software system becomes a smart move. These systems can be customized to suit your specific operations, and they integrate with other software platforms, such as inventory management or purchasing systems, making them highly versatile.
Tracking systems also provide you with valuable data that can be used for decision-making. For example, by analyzing maintenance trends, you will be able to discover that a particular asset is costing more to maintain than expected, prompting you to consider replacement or upgrades.
9. Train Maintenance Personnel
Even the best preventive maintenance plan will fall short without well-trained personnel to carry it out. Regular training programs are necessary to keep your maintenance team up to date on the latest procedures, technologies, and safety protocols.
Start by developing a comprehensive onboarding program for new hires. This should cover everything from basic maintenance tasks to more advanced troubleshooting techniques. Hands-on training, paired with theoretical instruction, works best to give personnel the confidence and skills they need. For example, new hires will shadow an experienced technician as they perform scheduled maintenance tasks, gradually taking on more responsibilities as their skills improve.
Beyond initial training, continuous education is also important. Maintenance technologies evolve, and personnel should be kept informed of any changes in best practices or new tools available to streamline their work. You will have to consider providing access to external training resources, certification programs, or online courses to deepen their knowledge.
Regular refresher courses on safety protocols should also be a priority. For example, if your facility uses heavy machinery, regular lockout/tagout (LOTO) training significantly reduces the risk of accidents during maintenance.
10. Review and Optimize Preventive Maintenance Program
Creating a preventive maintenance plan is not a one-time event. Ongoing review and optimization are essential to improving your plan’s effectiveness and adapting to changes in your operations or equipment. Regularly evaluate the performance of your PM program by gathering data on completed tasks, equipment reliability, and maintenance costs.
One effective method is conducting a preventive maintenance audit of your ongoing activities. This allows you to spot inefficiencies, such as tasks being performed too frequently or maintenance actions that aren’t preventing failures as intended. For example, if a machine is regularly breaking down despite routine maintenance, the audit may reveal that task frequency needs to be adjusted or that a different type of maintenance strategy is required.
Also gather feedback from your maintenance personnel. They have firsthand knowledge of the effectiveness of the tasks they perform and may have suggestions for improving the plan. Similarly, feedback from other departments, such as production or operations, to obtain insights into how maintenance activities are affecting overall business goals.
Takeaway: Create an Effective Preventive Maintenance Program with FieldCircle Maintenance Software
Maintenance managers must stay informed about new technologies or trends that are expected to impact your preventive maintenance plan. Each step in the process relies heavily on organization and timely follow-up. This is where maintenance software comes into play.
Our preventive maintenance features reduce the likelihood of missed maintenance schedules and unexpected breakdowns, supporting asset reliability and lowering repair costs. By aligning maintenance tasks with operational goals, organizations not only simplify processes for teams but also experience key preventive maintenance benefits, such as improved asset lifespan, reduced downtime, and optimized resource use. Adopt FieldCircle to keep your assets in top shape and maintain overall operational efficiency.