Transitioning to Smart Maintenance with AI and Machine Learning
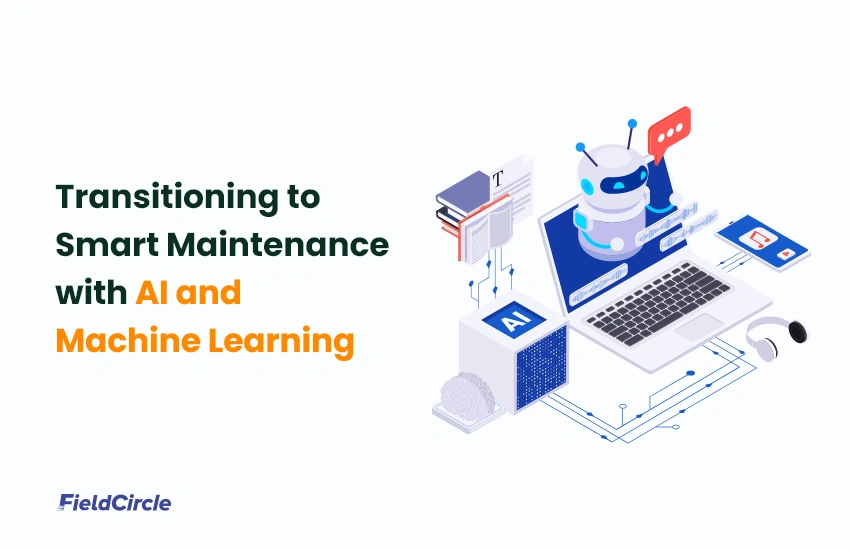
Over time as data gained currency or became an “oil,” AI and Machine Learning dethroned preventative maintenance with predictive maintenance. The rise of analytics techniques like Prognostic Health Management (PHM) and Failure Prediction Models bear testimony to this evolution.
However, the ongoing research and efforts towards discovering the applicability of mathematical models for bettering productivity of maintenance processes shed light on the voracious capabilities of AI in maintenance.
So, while PHM helps predict the future health of equipment based on its current condition and historical data Failure Prediction Models help predict when a specific component or system is likely to fail, the theory offers unending possibilities with diverse mechanisms.
Undoubtedly, the transformation brought by AI and Machine Learning in maintenance is revolutionary as its aiding maintenance professionals plan maintenance activities for the best ROI from maintenance operations. We discuss the length and breadth of opportunities of AI ML for maintenance.
What is the Role of AI in Smart Maintenance?
AI revolutionizes smart maintenance by integrating with Internet of Things (IoT) devices. It uses real-time data generated by the IoT ecosystem, providing predictive insights for proactive maintenance programs. By analyzing operational data, AI creates optimized maintenance schedules and resource allocations, making maintenance more efficient and cost-effective. As a result, maintenance management shifts from being reactive to preventive. As a result, maintenance management shifts from being reactive to preventive.
How AI facilitates Smart Maintenance: Use Cases and Examples
Artificial Intelligence (AI) and Machine Learning (ML) are continuously evolving, and spearheading predictive analytics towards constant improvement. Steadily most business aspects have been brought under their fold. The reason – the sheer improvement they are bringing. Machine Learning and AI have been shaping predictive maintenance which is the norm of the day. Across categories, we look at some of the mechanisms that offer the potential to reengineer maintenance operations.
Anomaly Detection
When machines begin to malfunction, the first signs are rarely dramatic. Instead, they often appear as slight irregularities in sensor readings—minor shifts in vibration, pressure, or temperature. Detecting these early warnings before they escalate into failures is the core purpose of anomaly detection in smart maintenance.
To uncover such patterns, algorithms first learn what constitutes normal operational behavior. Techniques like Isolation Forests and One-Class SVMs specialize in recognizing outliers by modeling normal data distributions. When sensor values stray from expected ranges, these methods raise alerts without requiring historical failure data.
Neural network-based approaches, such as autoencoders, take a different route. They reconstruct normal input data and monitor how well new data matches that reconstruction. A noticeable increase in reconstruction error often signals that something is amiss—helping detect faults in complex systems where subtle degradation might otherwise go unnoticed.
Some scenarios demand a broader view of equipment behavior. Clustering methods like K-Means group similar patterns, and any data point that falls outside these clusters may represent early-stage wear or misalignment. This is especially useful in systems that operate under varying loads or speeds.
Further depth comes from density-based models like DBSCAN and statistical tools like Mahalanobis Distance, which excel in capturing low-frequency or context-specific anomalies. Together, these methods offer a layered, data-driven approach to anticipating equipment failure.
Condition Monitoring
Condition monitoring focuses on tracking equipment health using data rather than dismantling machinery for inspection. By continuously comparing live sensor readings with expected behavior, it helps detect early signs of wear, performance drops, or potential faults—allowing maintenance teams to act before issues become costly breakdowns.
One of the key enablers in this space is the digital twin. It creates a virtual replica of a physical asset that runs in parallel, using real-time inputs to simulate its actual condition. Any mismatch between the real and digital outputs may signal internal problems like thermal stress, fluid imbalances, or misalignment—issues that are otherwise hard to catch early.
To uncover deeper trends in operational data, neural networks—particularly LSTM models—analyze sequences of time-series sensor readings. These models are well-suited to spotting gradual shifts in equipment behavior, such as fluctuating flow rates or rotating speeds, which often point to slow-developing faults.
In systems where internal states can’t be directly measured, Hidden Markov Models step in. They infer unseen machine conditions based on observable outputs, offering insight into components that might be degrading silently over time, like motor drives or hydraulic valves.
Supporting these methods are Kalman Filters for real-time state tracking and signal analysis tools like Fast Fourier Transform and Wavelet Transform. These help isolate vibration anomalies and short-lived disturbances—making condition monitoring not just continuous, but context-aware and predictive.
Natural Language Processing (NLP)
Maintenance insights don’t always come from sensors. A large portion hides in unstructured text—technician notes, service logs, manuals, and work orders. Natural Language Processing (NLP) helps decode this information, revealing patterns, recurring issues, and context that structured data often misses.
One of the most effective uses of NLP in this context is text analysis. By processing written records of faults, component replacements, and repair timelines, organizations can uncover trends that indicate system weaknesses or frequently failing parts. These patterns provide early warnings, helping teams focus on high-risk areas before they escalate.
NLP also strengthens access to technical information through semantic search. Unlike traditional keyword methods, semantic search understands context, making it easier for technicians to locate procedures or part specifications—even if terminology varies across documents. This leads to quicker troubleshooting and more consistent repairs.
Another benefit appears in knowledge management. NLP tools extract and organize information from large volumes of manuals and historical reports, building searchable databases that reflect real operational experience. Teams can retrieve relevant content without sifting through scattered documentation, gaining access to proven solutions instantly.
Generative AI now builds on this foundation by summarizing reports, tagging problems, and suggesting next steps. These advancements turn scattered text into actionable insight, helping maintenance teams save time and make informed decisions faster.
Optimization
Effective maintenance requires more than timely response—it calls for intelligent planning amid competing constraints like technician shifts, equipment availability, spare parts, and budgets. Optimization techniques step in to make sense of these variables, helping organizations choose strategies that align with both operational goals and resource limitations.
Evolutionary methods such as Genetic Algorithms work by iteratively refining schedules, often used in settings where downtime must be tightly managed. These models generate efficient maintenance plans that consider safety rules, operational loads, and staff availability. Reinforcement Learning adds adaptability by learning from historical decisions and updating strategies based on past outcomes and real-time changes.
Nature-inspired approaches like Particle Swarm and Ant Colony Optimization offer practical solutions for organizing inspection routines and service routes. These models are particularly effective in large, distributed environments where technician movement and task sequencing directly impact efficiency.
Other methods focus on navigating complex decision spaces. Simulated Annealing and Tabu Search are used to schedule maintenance across large networks, avoiding bottlenecks while maintaining operational continuity. They help balance conflicting priorities without retracing ineffective strategies.
For precise planning, techniques like Integer Linear Programming enforce rule-based constraints, while metaheuristics like Artificial Bee Colony search for multi-objective balance. Combined with predictive models like Random Forest and decision frameworks like Fuzzy Logic, these tools support proactive, context-aware maintenance decisions.
Image and Video Analysis
Image and video analysis is reshaping equipment inspection by offering a non-intrusive, data-driven view into asset conditions. Through predictive maintenance with computer vision, camera feeds or drone footage are leveraged to detect surface defects, corrosion, and physical wear.
Object detection models like YOLO and Faster R-CNN help pinpoint and track equipment across facilities. By identifying where assets are and how they’re positioned, these tools support better inventory control and prevent misplacement, especially in complex industrial environments.
For deeper insight, segmentation models such as U-Net and Mask R-CNN divide images into labeled sections—highlighting areas of concern like cracks, rust, or structural deformation. This detailed mapping aids in condition assessment and helps prioritize maintenance tasks based on visual cues.
Complementing these techniques are feature extraction methods like HOG and SIFT. These algorithms detect distinct patterns or textures, enabling the recognition of specific components or abnormalities. Such capabilities are useful when comparing live footage with known benchmarks to identify wear trends or misalignments.
Together, these visual analytics approaches provide a continuous, automated view into equipment health—bridging the gap between manual inspection and real-time operational awareness.
How to Implement Artificial Intelligence (AI) for Smart Maintenance?
Putting these algorithms into practice requires going through a series of structured steps which we discuss as follow:
- Data Collection
Collect sensor data measuring parameters like temperature, pressure, and vibration, alongside historical maintenance data. The combination offers crucial time-series insights into equipment condition, aiding in pattern recognition and understanding the relationship between events and failures.
- Feature Engineering
Extract relevant features from raw sensor data, emphasizing the health of equipment. Utilize time series analysis techniques such as rolling averages and Fourier transforms to discern patterns and trends vital for smart maintenance.
- Algorithm Selection
Go for regression models like linear and support vector regression for predicting remaining useful life. Embrace survival analysis techniques, along with advanced models like decision trees, random forests, and deep learning algorithms for accurate equipment failure predictions.
- Model Training
Train the algorithm through supervised learning on labeled data, incorporating input features and corresponding outcomes like time to failure. In some instances, leverage unsupervised learning for anomaly detection, where the algorithm identifies deviations from normal operations.
- Evaluation Metrics
Assess the model using accuracy, precision, recall, and AUROC metrics. These measures gauge how well the model predicts outcomes, its accuracy in positive predictions, and its ability to balance true positive and false positive rates.
- Threshold Setting
Determine maintenance thresholds by setting points based on model predictions and acceptable risk levels. A critical step, it ensures timely interventions, aligning with the algorithm’s predictions and the organization’s risk tolerance.
- Integration and Deployment
Integrate the predictive maintenance model into existing maintenance systems like computerized maintenance management system (CMMS) software, facilitating seamless coordination. Enable real-time monitoring post-deployment, allowing continuous analysis of incoming data for prompt interventions by maintenance teams.
- Continuous Improvement
Establish a feedback loop to continually enhance the model. As more data becomes available, retrain the algorithm to adapt to changing conditions, improving accuracy, and ensuring sustained effectiveness in predicting equipment failures.
What are the Benefits of Artificial Intelligence in Maintenance?
Discussed are the significant benefits of artificial intelligence in maintenance that show how in various ways it contributes to transforming and optimizing maintenance processes.
- Smart Scheduling
AI-driven predictive maintenance ensures interventions at the optimal time, aligning with equipment conditions to minimize disruptions. Apart from preserving the integrity of assets, it also reduces unnecessary maintenance, resulting in significant cost savings.
- Downtime Deterrence
Ai-based predictive maintenance scheduling and optimization schedules activities before failures, ensuring operational continuity and preventing sudden breakdowns.
- Resource Harmony
AI in maintenance optimizes resources, ensuring efficient deployment of personnel and tools. Additionally, ML predicts spare parts needs, optimizing inventory levels to prevent both excess stock and shortages, contributing to cost-effectiveness.
- Prolonged Lifespan
Predictive interventions extend equipment lifespan by addressing issues early, preventing further deterioration. Such proactive care not only enhances reliability but also contributes to preserving the integrity of equipment assets.
- Economical Operations
Predictive maintenance helps slash maintenance costs by reducing the need for expensive emergency repairs. By avoiding sudden breakdowns, organizations experience substantial savings and gain better control over their budgets.
- Safety First Approach Achieved:
Predictive maintenance identifies safety concerns early, enhancing workplace safety by proactively addressing potential hazards. Early detection and resolution of safety issues also contribute to regulatory compliance and a safer working environment.
- Streamlined Efficiency
AI and ML streamline maintenance workflows, enhancing operational efficiency by automating routine tasks and minimizing manual interventions. Productivity improvement in this way results in time and cost efficiencies, allowing organizations to achieve more with existing resources.
- Tailored Strategies
ML adapts to specific equipment needs, allowing tailored maintenance strategies that consider the unique characteristics and requirements of each asset. The ability to adapt strategies based on real-time data ensures that maintenance plans remain effective in dynamic operating environments.
- Continuous Enhancement
Machine learning models continuously learn from new data, improving accuracy and adapting to changing conditions by incorporating the latest insights. The iterative learning process fosters a culture of continuous improvement, where maintenance processes evolve and become more effective over time.
Use AI for Maintenance with FieldCircle
We’ve illuminated the path towards unprecedented efficiency gains with Artificial intelligence and ML for evolving maintenance needs. Understanding the steps to implement these technologies is pivotal. However, it requires two-fold expertise. First, strong proficiency in AI and ML, and second a robust understanding of industry-specific maintenance processes.
FieldCircle helps you overcome these challenges by offering predictive maintenance software that is integrated with advanced AI and ML techniques tailored to best manage maintenance operations. Schedule a demo call to get a better clarity.