CMMS Concept: How Does a CMMS Work?
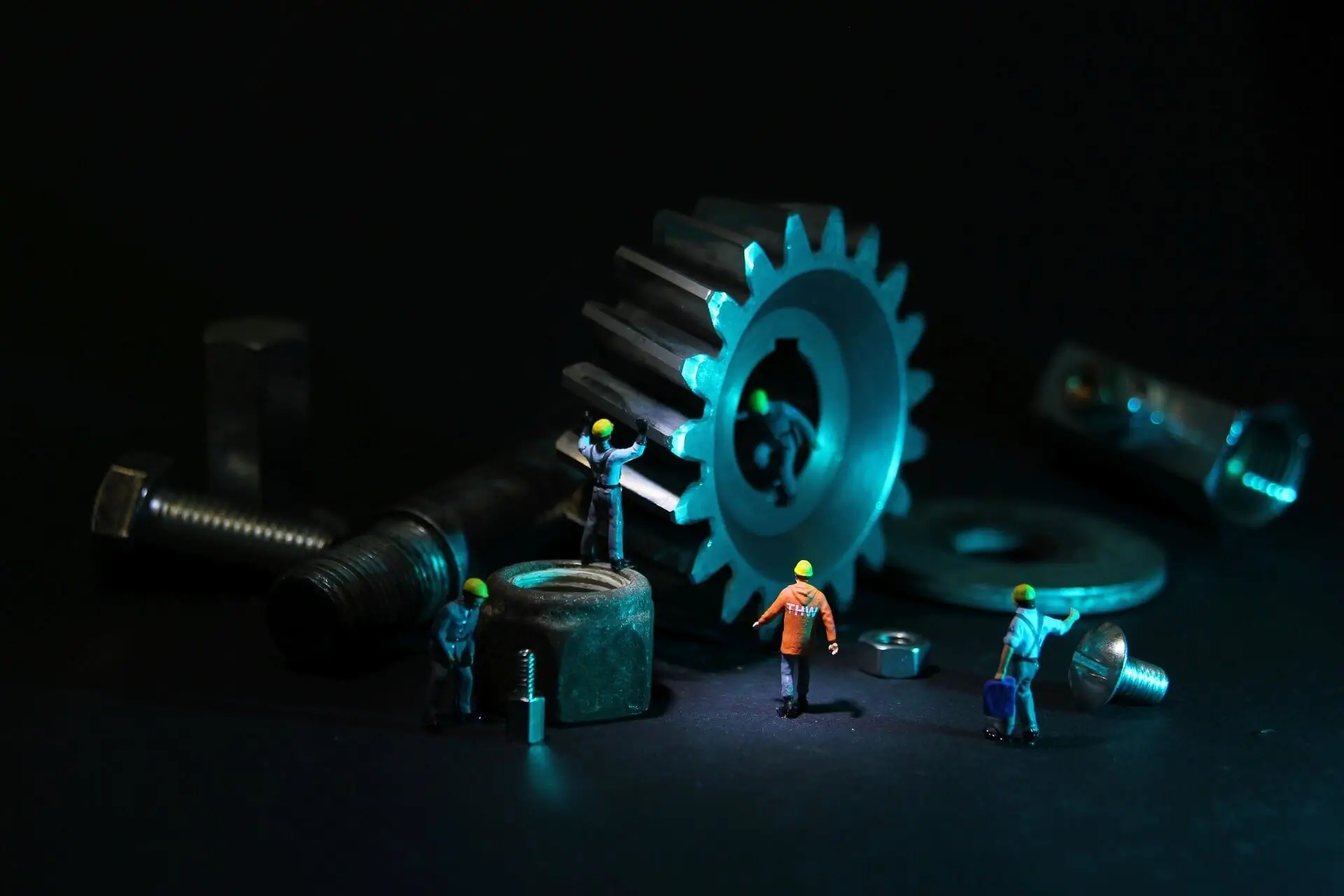
A Computerized Maintenance Management System (CMMS) operates as the backbone of modern maintenance operations, centralizing tasks like scheduling, asset tracking, and work order management into a unified digital platform. By automating preventive maintenance, CMMS ensures timely repairs based on predefined schedules or equipment usage data, reducing downtime and extending asset life.
Advanced integrations with IoT devices enable real-time monitoring, allowing teams to detect anomalies early and take corrective action proactively. Technicians benefit from mobile access to update job statuses, check inventory, and review maintenance histories, promoting efficiency and minimizing delays.
This blog explores how CMMS works, highlights its core features, and provides insights into implementing this powerful tool effectively.
What are the CMMS Features?
Every feature in the maintenance planning tool supports various working functions of the process, and they are as follows:
1. Scheduling features
When multiple employees work on different sites, your platform needs to be accurate. The solution gives you the task calendar that can be easy to view and update. You can filter information in the application for your focus work.
2. Preventive maintenance
A CMMS serves as a dedicated preventive maintenance tool, because of its many useful features. You can automate those work orders with the preferred preventive maintenance schedule. These tasks are already scheduled in advance to make sure to attend the maintenance. This preventive approach helps extend the machines’ life cycle and support the team.
3. System monitoring
System monitoring works when the machine is connected to the solution via an internet connection. If you have machines like this, this monitoring won’t be needed.
4. Mobile Management
The staff needs to update the information in real-time to get accurate data, so you need a compatible management application that operates on mobile devices. Mobile application features allow technicians to update information about repairs on-site, to keep the information more accurate. This mobile application will be easy to use and saves time.
5. Inventory Management
The feature of inventory management in the CMMS lists the inventories of supplies and repair parts to the service department and checks for any shortfalls to avoid scheduling impacts. This function enables the manager to find any equipment’s availability and cost instantly. The platforms will also provide information about the parts vendor, location, and other requirements.
The inventory module updates its total count automatically according to the usage of parts and materials. When a particular item is below minimum availability, the tool notifies your purchasing department about the shortfall. This avoids the additional costs happening during last-minute purchase orders.
6. CMMS and automation
The automation with CMMS software avoids human error, and your staff doesn’t need to remember how often each machine needs care. It will automatically assign work based on the skills and availability of technicians and notifies them about the tasks. Finally, the work order will be created, and technicians will know what to do with the required guidelines.
You can also calculate the time spent on each task, parts availability, and expenses. This helps to find the time taken for each asset, which drains more costs than the planned one. The modern solution with automation and artificial intelligence analyzes each work order to identify abnormalities and alert the employees to take corrective measures.
7. Enterprise asset management
The enterprise solution maximizes your business’s productivity by managing assets across various departments and locations. It enables the tracking of the overall history. This supports managers in making accurate data-driven decisions. The simplified way of managing assets is scheduling and working preventive methods properly. It should also include the capability to track the meter and its reading and the duration of equipment warranties.
8. Vendor Management
The well-designed vendor management will assist any business in handling its assets and vendors. It will easily manage vendors and costs with vendor tracking. Additionally, it tracks the activities to know when they start and close the work. You can quickly generate reports on expenses, work order performance, and response time. This will be more advantageous to the managers because it provides rapid access to vendor data, including contact information.
If your business has assets requiring continuous care and administration, the planning tools are an invaluable addition. It works with you to guarantee your equipment is easily accessible, in good condition and can provide correct care for an extended period.
Example of CMMS Process Flow
This explanation will let you understand the cmms overview and how the features of CMMS software work together to complete a maintenance operation. Here’s an example of a problem that might arrive and how it resolves the process.
Let’s take a manufacturing organization that has a milling machine. You have already noted the preventive method of the equipment that should be performed every 3 months. The digital program will automatically schedule the preventive tasks to the calendar and assign the work to the available technicians.
In some cases, before the service time arrives, you will get an alert from the system monitoring, that one of the milling machine cutters is not working correctly due to some issues. Once you receive the notification, you can send a technician to solve the problem before it gets bigger. For this, you need to look at the availability of skilled technicians in your calendar.
After you assign the work, the technician will head out to the particular unit of your industry and inspect. Using a mobile application, the technicians can get complete information about the machine, its parts, and the history. This helps to resolve the problem more quickly. Once the work is completed, the technician can use the mobile app to mark the work as completed from the field, and this sends a notification to the manager that it’s done.
What Should CMMS Software Deliver?
This concept has been a chattering topic among many industries, so everyone is keen on the new updates. The new application should provide users with specific CMMS benefits in a user-friendly way. These include,
- Streamlined integrations
It should integrate with other interfaces, so teams can effectively utilize, capture and analyze data. - In-built navigation
It should be smooth in user adoption and implementation. The easy-to-use solution is more likely to be adopted, so look for the solution process flow that suited to the employment process and needs. - Security
It should be equipped with high security to keep confidential information safe and secure, including sign-in options, cloud storage, and other access to controls, authority, and restrictions. - Data migration
For the implementation of a CMMS system, data migration is required from disparate solutions. This must be straightforward so that the organizations can collaborate and ensure the data is comprehensive and up-to-date. - Work order management visibility
Effective maintenance work requires smooth work order management and execution. The tool simplifies the workflow by allowing managers to review, assign, schedule, and track work orders with associated maintenance tasks. This will provide complete visibility of the work order and its history. - Reporting
Customized analytics and reports allow businesses to get complete information about the process to get the preventive method needed to optimize the operation and performance. - Audit records
It should help to maintain employee compliance and work records and generate the audit logs needed to demonstrate consent with regulatory, industry, and other legislation. Leveraging CMMS compliance capabilities can further support these efforts by automating record-keeping, ensuring documentation accuracy, and providing a centralized system to track adherence to required standards.
The Applications of The CMMS Concept
Most applications provide a similar set of features and solutions. The key difference between them is how they are implemented. The main work is to collect all relevant information from the database and simplify the workflow.
Some of the distinctive applications are:
- It helps companies ensure they meet all their needs with the operation. It also supports them in predicting future service of equipment so that they can make decisions about purchasing new inventory.
- It helps a business to meet its objectives by collecting information from different sources, such as service reports and equipment information, then organizing it into relevant reports that provide visibility into your work order at both the individual and the enterprise levels.
- It provides the central hub through which you can access all the relevant information regarding the equipment, suppliers, customers, and inventory levels. This makes it easier for your equipment operations by reducing communication time between departments and eliminating redundant processes.
By simplifying all the features of computerized service management solutions, it is designed to provide the following advantages:
- Improve service efficiency
- Reduce repair costs
- Decrease equipment downtime
- Increase the lifespan of the equipment
- Provide history record to assist in planning
- Provides accurate service reports
There are numerous advantages to using the CMMS platform. When selecting the CMMS software, finding and filtering out the best parameters for your needs is crucial.
CMMS for Every Business: The Verdict
An effective CMMS software can save money and time by creating an effective service plan. Surveys show that around 70% of organizations don’t know when their equipment is due for service. It resolves problems before they arise.
For some businesses, the concept of how CMMS works might be new. Still, the good factor is that the platform is designed to work automatically with minimal training to create a significant return on investment. There are numerous providers available to get started with the maintenace programs. Trusting the management tools will ensure the uninterrupted productivity of your business.