Deferred Maintenance: What It Is, Consequences, and How to Avoid It
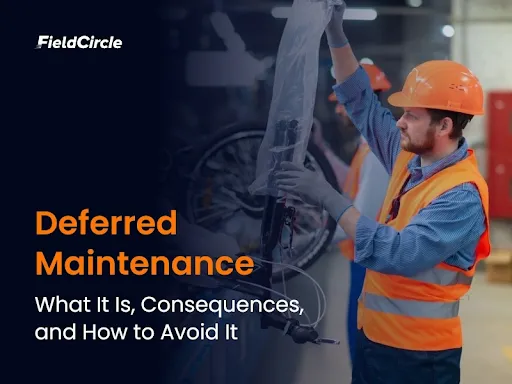
On Christmas Eve 2018, at U.S. Steel’s century-old Clairton plant in Pennsylvania, a corroded sprinkler pipe collapsed, triggering a devastating fire that spread to the size of a football field. Workers had detected vibration in a critical compressor days earlier, but management postponed the inspection until after the holidays to avoid overtime costs. That decision resulted in a $40 million loss for the company.
This catastrophe illustrates how dangerous deferred maintenance can be. When we postpone today’s small repairs, we’re unknowingly writing checks for tomorrow’s disasters. For maintenance leaders, balancing between immediate budget constraints and long-term asset integrity represents perhaps the most challenging aspect of the job.
Understanding Deferred Maintenance
Deferred maintenance refers to the practice of postponing necessary repairs, upkeep, or replacement of assets beyond their recommended service life or scheduled maintenance intervals. This delay leads to deterioration, weakening of functionalities, and increase in the risk of failures over time. The causes of deferred maintenance typically fall into two categories which are:
- Intentional Deferrals: These are strategic postponements where maintenance work is deliberately delayed to focus on higher-priority projects, meet short-term production demands, or address other strategic business needs. One example of deferred maintenance is a seasonal manufacturer postponing non-urgent repairs during peak production periods.
- Forced Deferrals: These occur when maintenance must be postponed due to resource constraints—whether time, limited maintenance budget, parts, or qualified labor. These deferrals aren’t strategic choices but rather reluctant compromises.
The Hidden Costs of Postponing Maintenance
The financial impact of deferred maintenance extends far beyond the immediate savings. According to Rick Biedenweg, President of Pacific Partners Consulting Group, “every $1.00 of maintenance deferred to a later date results in $4.00 of capital renewal”. This 4:1 ratio highlights the exponential cost growth that occurs when maintenance is delayed.
For example, a $1,500 annual maintenance procedure postponed for a year could result in a $6,000 expense the following year, a significant jump that can devastate maintenance budgets.
Then there are other aspects that must be considered. For instance, according to a McKinsey report, frontline workers of most organizations spend less than 50 percent of their time with “hands on tools,” with many operations falling below 30 percent. This sort of low productivity stems not from lack of effort but from complexities in coordinating people, materials, tools, and equipment for performing maintenance tasks which results in costs that go unnoticed.
Beyond direct repair costs, deferred maintenance creates multiple operational consequences such as:
Decreased Asset Efficiency
Equipment that hasn’t received proper maintenance requires more energy to perform at optimal capacity. Poorly maintained equipment consumes significantly more energy while delivering reduced output.
Shortened Asset Lifespan
Regular maintenance prolongs equipment life. Deferring maintenance accelerates deterioration, forcing earlier capital investments in replacement equipment. It results in a vicious cycle where budget constraints lead to deferred maintenance, which then necessitates even larger capital expenditures down the road.
Unplanned Downtime
When deferred maintenance leads to equipment failure, the resulting unplanned downtime creates cascading production losses. For manufacturing operations, this can translate to hundreds of thousands of dollars per hour in lost production.
Tenant and Customer Dissatisfaction
For facility managers, deferred maintenance can lead to dissatisfaction among building occupants, potentially resulting in higher turnover rates and reduction in property values.
Legal and Regulatory Risks
Ignored maintenance can result in violations of building codes, health and safety regulations, or contractual obligations. Organizations are exposed to legal liabilities and compliance issues that far exceed the cost of routine maintenance.
Warning Signs of a Deferred Maintenance Problem
Recognizing early indicators of a problematic deferred maintenance backlog helps organizations intervene before minor issues escalate into major crises. Watch for these warning signs to avoid problems.
Growing Maintenance Backlog
When your maintenance backlogs consistently increase instead of remaining stable, it indicates maintenance tasks are being deferred faster than they’re being completed. The snowball effect can quickly become unmanageable.
Rising Emergency Repair Frequency
A spike in emergency and reactive maintenance often signals that preventive work is being deferred. When you’re constantly putting out fires, you have less time for planned maintenance, and you end up creating a self-reinforcing cycle.
Increasing Energy Consumption
Unexplained increases in utility costs indicate equipment efficiency losses due to deferred maintenance. HVAC systems, in particular, can show dramatic efficiency declines when maintenance is postponed.
Equipment Performance Decline
When machines require more adjustments, produce more errors, or run slower than designed specifications, deferred maintenance is frequently the culprit. Operators then develop workarounds that mask the underlying problems.
Safety Incidents
Minor incidents or near-misses may indicate that equipment isn’t receiving proper maintenance. The U.S. Steel fire example demonstrates how quickly deferred maintenance can escalate into a safety catastrophe with significant financial and reputational damage that increase safety hazards bring.
What are the Strategies to Avoid Deferred Maintenance?
Breaking the deferred maintenance cycle requires both cultural and procedural changes within an organization. Here are proven strategies for maintenance leaders:
Implement Preventive Maintenance Programs
Preventive maintenance involves regular inspections, servicing, and repairs to prevent equipment failures and extend asset life. By implementing a preventive maintenance program, you can identify potential issues before they escalate, reducing the likelihood of deferred maintenance.
McKinsey research shows that digital work-management systems have helped some companies boost maintenance-labor productivity by 15 to 30 percent. Others have used these systems to optimize shutdowns and turnaround projects, reducing outage duration by up to one-third.
Prioritize Maintenance Tasks
Not all maintenance tasks are created equal. Prioritize based on impact on safety, compliance, and operational efficiency. Use a risk-based approach to allocate resources and address high-priority issues first. This strategy helps manage limited resources effectively and prevents critical problems from being deferred.
When resources are tight, focusing on high-risk issues lets teams tackle the most pressing needs first. Repairing equipment that poses safety risks or halting production due to equipment failure demands quick action. By handling these tasks upfront, businesses avoid piling up maintenance problems that only worsen over time.
Have a Strong Maintenance Plan
A well-structured maintenance plan is integral to preventing the risk of deferred maintenance from escalating. Implementing a clear maintenance workflow allows teams to systematically approach tasks, prioritize resources, and track maintenance progress effectively. By building an organized and proactive approach, companies can reduce deferred maintenance costs significantly.
Establishing clear guidelines for routine inspections and setting specific timelines helps maintain accountability across teams. When you identify key responsibilities and expected outcomes, you avoid miscommunication and keep maintenance activities on track.
Leverage Technology Solutions
Modern computerized maintenance management systems (CMMS) and IoT-enabled condition monitoring dramatically improve maintenance efficiency and effectiveness. As more maintenance departments adopt IoT technology, they should see a drop in deferred maintenance tasks. This technology makes it easier to monitor assets and prevent more costly wear.
Digital work management (DWM) systems have become significantly less expensive and easier to implement than their predecessors. A DWM implementation that once required five or six months now can be up and running in three to four weeks.
Allocate Adequate Budget
Ensure your maintenance budget includes provisions for both routine and unexpected maintenance and repairs. By allocating sufficient funds for maintenance activities, you can avoid the temptation to defer tasks due to financial constraints.
Consider setting up a contingency fund specifically for addressing deferred maintenance. The approach allows you to chip away at backlogged tasks without disrupting current maintenance schedules.
Build Maintenance-Aware Culture
Educate all stakeholders about the importance of timely maintenance and the consequences of deferral. When everyone from the maintenance team to executives understands the value of maintenance, support for proper resource allocation follows.
Deloitte points out that assessors and company leadership are often unaware of deferred maintenance issues, despite their significant impact on property values and operational capabilities. Improving communication about these hidden costs can lead to better decision-making.
To Wrap Up
Deferred maintenance represents one of the most challenging aspects of asset management. While postponing maintenance may seem expedient in the short term, the long-term consequences of escalating maintenance costs, reduced efficiency, safety risks, and shortened asset life far outweigh the temporary savings.
As we look to the future, the signs indicate that deferred maintenance will likely decrease as organizations recognize the need for proper maintenance practices.
Remember the wisdom in the old saying, “a stitch in time saves nine.” By addressing maintenance needs proactively and systematically, you protect not just your assets but your organization’s future.