Unveiling Maintenance Scheduling: The Key to Efficient Equipment Management
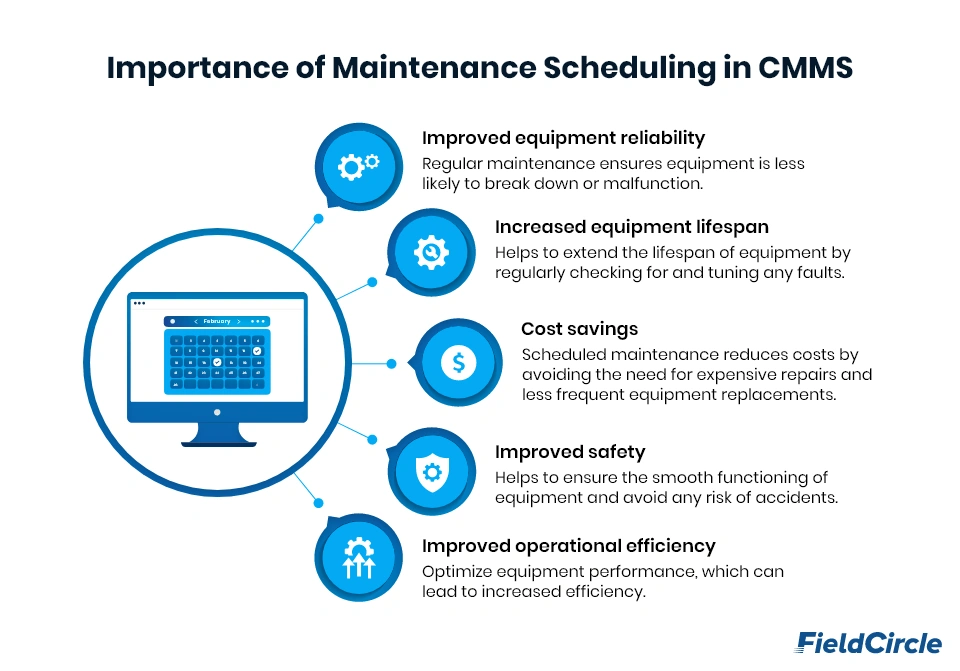
Bill, a mechanic at Delta Ray Inc., arrives at work and receives two assignments from the supervisor. The first task is to fix a leaking valve on the mezzanine floor, while the second is to check a reported leaking flange on the demineralizer.
Bill discovers that the valve requires a complete replacement due to damage, and as he isn’t certified to perform the necessary welding, he informs his supervisor. The supervisor then calls a certified welder to handle the valve replacement. Meanwhile, Bill disassembles the connections at the demineralizer and realizes he needs to cut new gaskets. After obtaining the gasket material, he completes the job.
Now, instead of starting a new assignment, Bill assists a colleague in finishing a control valve job. At the end of the day, he reflects on the constant busyness required to complete even a few tasks. How would have Bill’s day looked like had there been some maintenance planning automation in place?
Richard D. Palmer narrates this episode in his book, Maintenance Planning and Scheduling Handbook, as he goes on elaborating the role of maintenance scheduling in everyday maintenance operations.
Maintenance is a continuous process, and does not take place at a certain time of day. When scheduled, it can turn unsystematic events into a systematic course of action. But in the absence of a schedule, it results in chaos.
With tools like preventive maintenance software, implementing maintenance scheduling has become quite easier for maintenance managers this software application has in-bulit scheduling component.
As we move through the blog, we uncover various aspects of maintenance scheduling and its importance in CMMS software.
Developing the generic understanding: What is Maintenance Scheduling?
This question is as important to answer for maintenance managers as answering “what is maintenance planning.”
Maintenance scheduling helps to ensure that maintenance activities are coordinated and executed in a way that maximizes the availability and reliability of equipment, facilities, and other assets. Effective maintenance planning and scheduling can help to reduce the likelihood of equipment failures, which can lead to costly downtime and lost productivity. It can also help to identify potential problems before they occur, allowing maintenance technicians to address them before they become more serious issues.
Additionally, maintenance scheduling can help to optimize the use of maintenance resources, such as labor, materials, and equipment, by ensuring that the right technicians are available to perform the work at the right time. Overall, the objective of maintenance scheduling is to minimize scheduling maintenance costs and disruptions to operations while maximizing the efficiency and effectiveness of maintenance activities.
Maintenance Scheduling: An important function of CMMS
A Computerized Maintenance Management System (CMMS) includes maintenance scheduling as its primary feature, thereby guaranteeing the efficient operation of assets and machinery.
Under the umbrella of maintenance scheduling, a computerized maintenance management system (CMMS) offers a set of features such as:
Work Order Management: CMMS provides the ability to create, track, and manage work orders for maintenance tasks. It allows users to schedule preventive, corrective, and predictive maintenance activities.
Calendar-based Scheduling: Offering a calendar interface, CMMS lets users view and schedule maintenance activities based on specific dates, days of the week, or time intervals.
Resource Allocation: Managers can manage and allocate resources including personnel, equipment, and materials for scheduled maintenance tasks.
Prioritization and Criticality: You can prioritize maintenance tasks based on factors like equipment criticality, safety concerns, or operational impact, and thereby address the most critical tasks promptly.
Recurring Maintenance Schedules: Easily create recurring maintenance schedules for repetitive tasks such as inspections, lubrication, filter replacements, etc with a CMMS.
Notifications and Reminders: CMMS can send automated notifications and reminders to maintenance personnel, supervisors, or stakeholders regarding upcoming scheduled maintenance tasks, changes, or delays.
Integration with Asset Management: CMMS can integrate with an organization’s asset management system, allowing users to schedule maintenance based on asset condition, meter readings, or other asset-specific parameters.
Historical Data Analysis: CMMS captures and stores maintenance history, allowing users to analyze data to identify patterns, optimize maintenance schedules, and make informed decisions based on past performance.
Mobile Access and Updates: Many modern CMMS solutions offer mobile applications, enabling maintenance technicians to access and update schedules, work orders, and record maintenance activities in real-time from their mobile devices.
What Happens When Maintenance Scheduling Is Not Done?
Absence of maintenance scheduling results in dire consequences for organizations, adversely impacting the operational efficiency and the bottom line. It can result in several problems, including:
Equipment failures
Without proper maintenance scheduling, equipment is more likely to break down or malfunction, leading to costly downtime and lost productivity. It results in accelerated wear and tear, reducing the lifespan of equipment and machinery.
Equipment failure was one key reason contributing to the 2010 Gulf of Mexico oil catastrophe. The blowout preventer, a crucial piece of equipment on rigs, failed, which contributed to the leak, the greatest offshore spill in US history. The failure to follow maintenance schedules played a significant role in the explosion and subsequent oil spill.
If the machinery had worked, it might have been able to prevent the first gas explosion that claimed the lives of 11 employees and prevent oil from flowing into the Gulf of Mexico, which would have prevented widespread contamination. The accident resulted in an estimated 4.2 million barrels of crude oil being spilled into the lake.
Higher maintenance cost
Higher maintenance cost is one obvious outcome of not having maintenance scheduling or having it in a poor form. When maintenance tasks are not scheduled in advance, minor issues can escalate into major problems that require expensive repairs or even equipment replacement. The cost continues to escalate and when maintenance managers finally notice it, they cannot revert and set the process in order.
Many organizations have suffered financial losses due to lack of maintenance scheduling. In 2013, Carnival Corporation experienced a rise in maintenance costs as well as reputational damage when several of their cruise ships resulted in mechanical issues and breakdowns. The incidents were attributed to poor maintenance scheduling, leading to unplanned repairs, cancellations, and compensation for affected passengers.
Operational disruptions
When maintenance is not scheduled or neglected, equipment performance deteriorates over time, affecting efficiency, accuracy, and reliability. Resulting in disruptions, this leads to reduction of productivity and quality issues.
The repercussions of operational disruptions are often huge. For instance, in August 2016, Delta Air Lines faced a widespread operational disruption when a critical power control module at their Atlanta data center failed. Causing a loss of power and subsequent failure of backup systems, the outage resulted in the cancellation of over 2,000 flights and affected millions of passengers. The incident revealed weaknesses in their maintenance scheduling and backup systems.
Increased risk of accidents
The absence of maintenance scheduling has far-reaching consequences, of which increasing the increased likelihood of accidents is significant.
Without timely inspections and necessary upkeep, performance starts degrading due to factors like dust accumulation, lubrication breakdown, or general wear and tear. Diminished performance then results in compromised functionality and reduced reliability.
Safety systems which require regular maintenance and testing to function effectively are hampered when maintenance scheduling is absent, as they do not receive the attention they require. Consequently, safety systems start malfunctioning or even fail to activate when needed, leaving individuals vulnerable to accidents.
In industries where hazardous conditions are present, such as chemical plants or construction sites, the absence of maintenance scheduling for safety systems can have disastrous consequences.
Not having a maintenance scheduling strategy at your disposal can thus come with many negative consequences. They can further cause compliance and legal, lead to negative impact on reputation, increase workload and stress amongst maintenance professionals, and result in missed opportunities for improvement.
What are the benefits of scheduled maintenance?
By establishing a calendar and a fixed start date, scheduled maintenance completes the maintenance tasks that were intended to be completed before a certain date and time. Some of the notable benefits of maintenance planning and scheduling include:
Improved equipment reliability
Equipment reliability is the direct result of the time the equipment runs for without failure. So, if an equipment is supposed to work for 4500 hours or roughly 6 months of operations, it must so without any interruption during that period, or else the reliability score suffers.
Maintaining accurate maintenance records and following scheduled maintenance strategy allows you to identify the areas you can improve if you want to impact plant reliability.
Empowered by scheduled maintenance, you can perform maintenance regularly, and your equipment will be less likely to break down or malfunction. This will lead to improved reliability and availability of equipment, which can increase productivity and reduce downtime.
Increased equipment lifespan
Equipment lifespan is a dynamic component. It varies from industry to industry and is subject to factors such as environmental factors, handling, and maintenance frequency.
By implementing regular maintenance tasks, organizations can effectively manage and prevent potential problems from escalating into major issues that demand costly repairs or replacements.
So, maintenance scheduling processes can help to extend the lifespan of equipment, facilities, and other assets. By performing maintenance tasks regularly, you can help prevent small problems from becoming larger issues that may require more extensive repairs or replacements.
Cost savings
Maintenance costs can be anywhere between 15% to 40% of the production cost, if we are to consider the manufacturing industry. But we do get an idea as to how maintenance costs form a significant part of the overall cost.
With a maintenance schedule, you can optimize these costs.
“Run to fail or repair easily costs somewhere between three and 10 times as much as a good maintenance program. When the equipment does fail, the actual repair costs are exorbitant, and you typically didn’t plan for them so there’s a financial issue,” explains David Auton, VP of Service Excellence, Engineering and Maintenance for Cushman & Wakefield.
Pick up these words carefully: “You typically didn’t plan for them so there’s a financial issue”. When you have a schedule, you can plan flawlessly, and avoid escalation of costs. You arm yourself with a proactive approach rather than responding in a reactive manner. This is where the opportunity is created to drive cost savings.
Improved safety
Electrocution, spinal cord injuries, traumatic brain injuries, crush injuries, and amputations are all that can come along with safety issues caused by the absence of scheduled maintenance. On the contrary, you can effectively prevent occurrences of these risks through implementing a scheduled maintenance strategy.
By conducting routine inspections, servicing, and repairs, potential hazards or malfunctions can be identified and addressed promptly. The approach effectively prevents equipment failures or malfunctions that could lead to accidents, injuries, or property damage.
Moreover, well-maintained equipment operates more efficiently, reducing the likelihood of unexpected breakdowns or performance issues that could jeopardize safety.
Improved operational efficiency
By performing maintenance, you can help to ensure that equipment is running at its optimal level. Properly calibrated and lubricated machinery operates with reduced friction, consuming less energy and resources, leading to improved energy efficiency, lower operational costs, and a smaller environmental footprint.
Reliable and well-maintained machines are less prone to errors, malfunctions, or variations in performance, resulting in higher productivity. So, at the end of the day, maintenance scheduling brings consistency to operations..
How CMMS simplifies maintenance scheduling
In order to reduce expensive reactive maintenance fixes, equipment failure, and backlogs, proper maintenance scheduling is essential. The good news is that a maintenance platform like FieldCircle makes it simple to accomplish all of them. With just one click, you can generate work orders, assign tasks, and monitor progress.
Our tool automates all maintenance tasks, saving you the time and effort of compiling data for a master scheduling document. At critical decision points, you can also monitor equipment performance and maintenance history.
CMMS software helps to streamline the maintenance planning and scheduling processes and leverage reliable data. A modern CMMS software ensures everyone has updated data on maintenance management.
Organizations in many industries have got solid benefits from the CMMS system, including decreased downtime with more efficiency in maintenance management. When selecting a CMMS, it is important to consider not only the features but also the user experience.