What is Preventive Maintenance Compliance (PMC)?
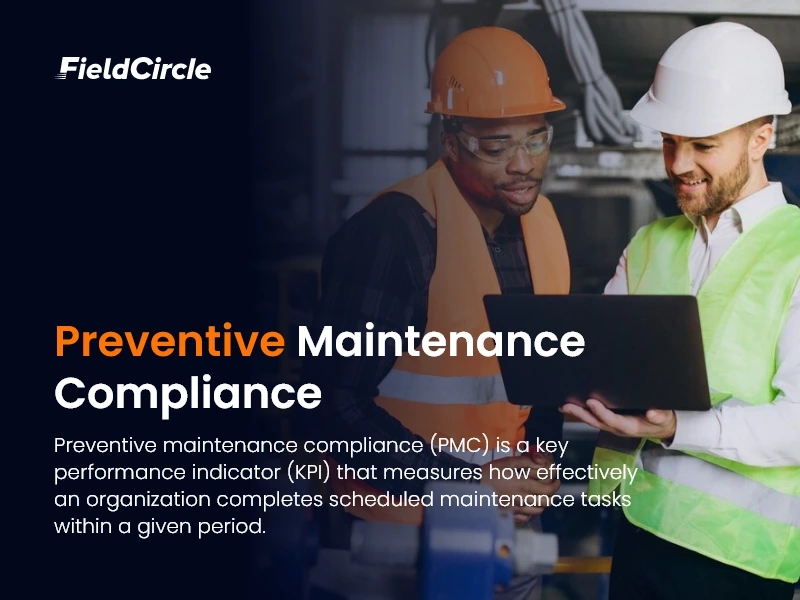
Preventive maintenance compliance (PMC) is a key performance indicator (KPI) that measures how effectively an organization completes scheduled maintenance tasks within a given period. It calculates the percentage of preventive maintenance work completed on time.
A high PMC score indicates that a company is successfully maintaining its assets, reducing the risk of unexpected failures, and optimizing operational performance.
Meanwhile, low PMC score signals gaps in maintenance execution, increasing the likelihood of equipment failures, unplanned downtime, and higher repair costs. Over a period of time, poor compliance also leads to workplace safety hazards, regulatory violations, and costly fines from agencies like OSHA, FDA, and ISO.
In the ensuing discussion, we proceed to understand the various dimensions of preventive maintenance compliance, right from how to calculate it, to its benefits, the associated challenges, and how to improve it.
Why is Preventive Maintenance Compliance Important?
Preventive maintenance software plays a critical role in achieving preventive maintenance compliance, which is essential for businesses across industries to maintain operational efficiency, meet regulatory requirements, and uphold workplace safety. Industries such as manufacturing, healthcare, aviation, and facilities management rely on PMC to keep critical machinery, medical devices, and infrastructures functioning optimally. However, neglecting maintenance brings forth catastrophic issues.
To highlight a real-life case, the iconic Arecibo Observatory telescope in Puerto Rico collapsed in December 2020 after 57 years of operation. ABC News reported that excessive zinc creep caused the breakage of zinc-filled sockets. The National Science Foundation opted not to rebuild it and instead allocated $5 million for an education center.
Likewise, organizations that fail to comply with preventive maintenance regulations are prone to serious consequences, such as hefty legal fines, workplace accidents, equipment malfunctions, and reputational damage. If they neglect PMC requirements, they will be liable for regulatory penalties from OSHA, the FDA, the NFPA, and other governing bodies, which apart from leading to increase in liability can also lead to business shutdown.
Here is an incident bearing testimony: In April 2023, the Central Coast Council in Australia was fined $418,562 after 1.83 million liters of raw sewage spilled into Narara Creek, polluting it, Fagan’s Bay, and Brisbane Water. The NSW Environment Protection Authority stated that the South Sewage Treatment System in Kincumber has neglected preventive maintenance since 2020, which caused severe environmental damage.
Preventive maintenance compliance is thus critical. It calls for a structured preventive maintenance strategy that allows long-term business sustainability while reducing risks and improving asset performance.
What are the Benefits of Preventive Maintenance Compliance?
Downtime minimization, equipment longevity, compliance improvement, and worker safety enhancement are some common ways in which preventive maintenance compliance helps businesses. Digging deeper, it impacts the business in the following ways:
Lower Unexpected Breakdowns and Reduced Failure Rates
In industries such as oil & gas or manufacturing, critical machinery like compressors or turbines are subject to extreme operating conditions. Preventive maintenance compliance takes these components through routine checks, such as vibration analysis or oil quality tests, to spot early signs of failure.
Better Scheduling and Resource Allocation
There is a precise planning of when equipment will be serviced and no guesswork involved in maintenance management with PMC. As a result, there are no bottlenecks or overuse of maintenance staff and spare parts. Since maintenance scheduling takes place during off-peak hours, it minimizes the impact on productivity. For instance, in a large warehouse or distribution center, regular servicing of forklifts or conveyors is scheduled based on usage patterns (e.g., hours of operation).
Extended Equipment and Asset Lifespan
Businesses following scheduled maintenance protocols avoid premature equipment failure with periodic servicing, eliminating the necessity for frequent replacements and lowering operational expenses. The reduction in wear and tear delays the replacement period and saves money on asset investment. As a result, machines function at full capacity and improve reliability and efficiency of the entire operation.
Reduces Long-Term Repair and Replacement Costs
Businesses are able to catch minor issues before they escalate into costly repairs or replacements. For example, replacing a worn-out seal on a pump during a scheduled maintenance check is far less expensive than repairing the entire pump due to a catastrophic failure. Over time, this significantly lowers overall repair costs and improves the equipment ROI.
Reduction in Unnecessary Replacement Costs
Through sensor data (e.g., temperature, vibration, and pressure readings), businesses can identify wear trends in machinery like motors or pumps. Preventive maintenance compliance integrates these sensors to capture data points, allowing businesses to replace parts only when necessary. This significantly reduces maintenance costs because businesses don’t over-replace components that still have operational life, unlike a traditional time-based maintenance schedule.
Enhanced Performance and Efficiency of Energy-Intensive Systems
PMC as a part of its process regularly services energy-intensive systems, such as air conditioning units or power generators. Replacing air filters, cleaning condenser coils, or recalibrating thermostat sensors drastically reduces energy consumption by ensuring that HVAC systems aren’t working harder than necessary. The result: there are direct savings on utility bills and businesses meet their sustainability goals by reducing its carbon footprint.
Safety Adherence and Reduction in Accident Risks
The need for PMC encourages continuous monitoring of whether safety protocols are being adhered to or not. At the same time it calls for using technology for safety improvement. Right tools assist the maintenance team in keeping track of the maintenance and safety metrics to stay on top of hazards. Regular inspections help detect worn-out parts, faulty sensors, or malfunctioning safety mechanisms. This way PMC addresses hazards before they escalate into accidents.
Avoidance of Fines and Penalties
Keeping up with PMC is the best way to steer clear of these costly penalties. With it, businesses are able to stay on the right side of the law since they can keep equipment up to code with regulations from agencies like OSHA and the EPA. To put simply, regular checks on safety mechanisms, pressure valves, emission systems, etc. help avoid violations. There are maintenance logs offering every information and audits are streamlined. Without these measures or documentation, businesses risk hefty fines, legal action, and even shutdowns.
Key Standards and Regulations for Preventive Maintenance Compliance
Each industry requires preventive maintenance for specific critical equipment to maintain operational efficiency and safety. These equipment include HVAC systems, elevators, and escalators, fire alarms and sprinklers, medical equipment, manufacturing machinery, boilers and pressure vessels, and aircraft and aviation systems.
Various government and industry-specific standards dictate health and safety protocols and guidelines, inspection procedures, and maintenance schedules for different types of equipment.
Below is a table showcasing key standards and regulations for preventive maintenance along with their purpose:
Regulations | Purpose |
---|---|
OSHA (Occupational Safety and Health Administration) | Enforces workplace safety regulations for hazardous equipment, including machine guarding, electrical safety, and ventilation systems. |
FDA (Food and Drug Administration) | Governs preventive maintenance in the pharmaceutical and food industries, ensuring equipment operates safely and effectively. |
ISO 55000 (Asset Management Standard) | Defines best practices for asset reliability, maintenance scheduling, and lifecycle management. |
NFPA (National Fire Protection Association) | Regulates maintenance of fire alarms, sprinkler systems, and emergency lighting to ensure fire safety compliance. |
EPA (Environmental Protection Agency) | Enforces preventive maintenance on pollution control equipment such as HVAC, industrial emissions systems, and hazardous waste storage units. |
FAA (Federal Aviation Administration) | Mandates preventive maintenance schedules for aircraft, airport safety systems, and aviation infrastructure. |
API (American Petroleum Institute) | Governs pipeline, pressure vessel, and storage tank maintenance for safety and compliance. |
Common Regulations for Different Industries
- Manufacturing: OSHA 1910.147, ISO 9001, NFPA 70E
- Healthcare: FDA 21 CFR Part 820, JTC Standards, NFPA 99
- Facilities Management: ASHRAE 180, NFPA 72 and 25, ANSI A17.1
- Aviation: FAA Part 43, ISO 55000
- Automotive: ISO 16949, OSHA 191.178
- Oil and Gas: API 510, 570, 653, EPA Clean Air Act
- Data Centers and IT Infrastructure: NFPA 75, ISO 27001, SSAE 16
How to Calculate Preventive Maintenance Compliance (PMC)?
Preventive maintenance compliance is calculated using the below formula:
For example, a manufacturing plant scheduled 120 preventive maintenance tasks to be completed in 6 months and completed 108 of them over the period. Then the PMC will be calculated as
Preventive Maintenance Compliance (PMC) = (108 / 120) * 100 = 90%
This means the business has a 90% preventive maintenance compliance score, reflecting a high level of adherence to the maintenance schedule.
Assessing the Effectiveness of Preventive Maintenance Efforts
While the PMC score is a valuable indicator, its effectiveness should be evaluated in conjunction with other preventive maintenance metrics, such as
- Downtime Metrics (MTD, MTBF)
- Equipment Uptime and Availability
- Asset Performance
- Cost ratio between preventive and corrective maintenance
- Failure Rates (MTBF)
Other factors to consider include critical asset identification, maintenance history analysis, historical maintenance trends, regular equipment assessments, and the integration of a Computerized Maintenance Management System (CMMS).
The ideal PMC score can vary depending on industry standards, equipment criticality, and specific business objectives. The following table highlights various PMC scores and their implications:
PMC Score (%) | Implication |
---|---|
90% and above | Excellent compliance; maintenance tasks are mostly on schedule, leading to reduced downtime and better asset reliability. |
85% – 90% | Good compliance; slight room for improvement, but still well within acceptable limits for most operations. |
80% – 85% | Fair compliance; some tasks may be slipping through, potentially leading to an increase in unplanned downtime. Maintenance scheduling or execution may need to be reevaluated. |
70% – 80% | Below average compliance; a significant portion of preventive tasks are missed. This could lead to higher breakdowns, increased repair costs, and reduced equipment lifespan. |
Below 70% | Poor compliance; maintenance program needs urgent attention. High risk of asset failure, unplanned downtime, and possible production delays. Immediate corrective action is required. |
Common Challenges in Preventive Maintenance Compliance
Ensuring proper staff training and maintaining accurate documentation are some of the biggest hurdles businesses face with preventive maintenance compliance. They also struggle with regulatory updates and budget constraints. These challenges impact efficiency, regulatory adherence, and cost-effectiveness.
Let’s discuss these common challenges in PM compliance
Overcoming Staff Training Gaps
One of the biggest compliance issues with preventive maintenance is the lack of trained personnel. High turnover, new technologies, and changing regulations create knowledge gaps, which lead to incomplete maintenance tasks and ignored compliance requirements.
Untrained staff will perform incorrect repairs or fail to document maintenance activities properly. It leads to equipment failures, safety hazards, and regulatory violations that disrupt operations and result in cost penalties.
Handling Extensive Documentation
Outdated or inconsistent documentation systems make managing detailed maintenance records a significant problem. Incomplete or lost records also make it difficult to track maintenance history, comply with regulations, and analyze equipment performance.
When businesses fail to provide accurate data during regulatory audits or maintenance reviews, they risk failed inspections, legal penalties, and operational setbacks. Poor documentation also hampers troubleshooting, leading to repeated equipment failures, inefficiencies, and increased downtime, ultimately impacting overall productivity and compliance reliability.
Staying Updated with Changing Regulations
Frequently changing regulations pose a great challenge to businesses’ ability to stay compliant. They must adhere to evolving OSHA, FDA, and ISO standards, which require continuous monitoring and adaptation.
Organizations that fail to stay updated can result in non-compliance and fines, shutdowns, and reputation damage. Updating new requirements means changes to maintenance procedures, additional training, and more administrative work, which adds to the burden.
Managing Compliance on a Tight Budget
Limited financial resources make it difficult for businesses to sustain effective preventive maintenance programs. Budget cuts lead to deferred maintenance, reduced training, lower-quality spare parts, and an increased likelihood of equipment failure and repairs.
Without a substantial budget, companies cannot invest in compliance tools and technologies. They are forced to be reactive, which requires higher long-term costs and operational risks.
How to Improve Preventive Maintenance Compliance (PMC)?
Improving PMC requires a structured approach that focuses on automating maintenance tracking, training personnel, maintaining accurate records, prioritizing high-risk equipment, and leveraging data analytics. Implementing these strategies increases PMC scores, ensuring effective proactive maintenance execution that reduces equipment failures, safety risks, and regulatory breaches.
Below are some actionable tips to improve PMC compliance.
Optimize Maintenance Scheduling
A well-structured schedule ensures preventive tasks are completed on time, reducing breakdowns and compliance issues. Here is how you can optimize maintenance scheduling
- Create a Comprehensive Maintenance Plan: Base your schedules on manufacturer guidelines, past performance, and compliance requirements to prevent failures.
- Use Digital Scheduling Tools: Use CMMS or maintenance calendars to track tasks and set reminders.
- Prioritize Critical Assets: Focus on high-risk assets to minimize downtime and costly failures.
- Adjust Based on Data: Analyze records and adjust schedules based on performance trends.
Implement Preventive Maintenance Software
A well-managed preventive maintenance program depends on effective tracking and compliance management. Preventive maintenance software such as Computerized Maintenance Management Systems (CMMS) or Enterprise Asset Management (EAM) streamlines maintenance scheduling, compliance reporting, and real-time monitoring.
These systems send alerts for overdue tasks so critical maintenance tasks are not missed. Plus, centralizing compliance data allows maintenance teams to have up-to-date records, improving regulatory compliance and operational reliability.
Improve Staff Training and Awareness
Well-trained employees are key to preventive maintenance compliance. Staff must be familiar with OSHA, FDA, ISO, and NFPA standards and proper task execution and record-keeping protocols and must be well-versed in avoiding the associated violations. Without proper training, compliance lapses can lead to regulatory violations and higher maintenance costs.
By conducting regular workshops, hands-on training sessions, and digital learning programs, businesses can reinforce the importance of preventive maintenance to reduce costs, extend equipment life, and ensure workplace safety. Keeping staff informed not only improves compliance but also creates a culture of accountability.
Maintain Detailed and Accurate Maintenance Logs
Accurate documentation is key to compliance, audits, and maintenance tracking. Businesses must log all preventive maintenance activities, task details, completion dates, and replaced parts to create a maintenance history.
Using standardized record-keeping templates facilitates compliance verification and inspections. Likewise, shifting from paper-based logs to digital documentation makes data accessible, reduces errors, and simplifies audits so you are always inspection-ready.
Prioritize High-Risk Equipment
The process of equipment maintenance differs from equipment to equipment. You should prioritize the maintenance of mission-critical equipment. Using risk assessment techniques helps to identify critical assets that need to be serviced more frequently for safety or operational reasons.
Increasing the frequency of inspections on these assets reduces the chance of unplanned downtime and minimizes the risk of operational disruption. Allocating resources and budget to high-priority equipment allows you to avoid costly downtime and stay compliant with safety standards.
Utilize Advanced Analytics for Better Tracking
A data-driven approach is key to refining maintenance strategies and improving PMC scores. Predictive maintenance analytics helps businesses detect performance anomalies, early signs of equipment failure, and scheduled repairs before breakdowns occur.
Tracking PMC trends over time allows you to identify areas for improvement and mitigate compliance risk. Integrating IoT sensors and real-time monitoring systems makes proactive maintenance planning even stronger so you can have more equipment reliability and long-term compliance success.
To Wrap Up
Maintaining a high Preventive Maintenance Compliance (PMC) rate can feel like walking a tightrope without the right tools. With constant equipment monitoring, documentation, and compliance tracking, the process can become burdensome, particularly as organizations scale. You need intelligent systems or else it becomes an uphill task.
FieldCircle’s preventive maintenance software offers the perfect solution to this challenge. With all essential features, it is the best tool to achieve and sustain high PMC. AI-powered capabilities, mobile access, and easy IoT integration make it a must-to-have asset for your maintenance management needs.