8 Benefits of CMMS Software In the Oil and Gas Industry
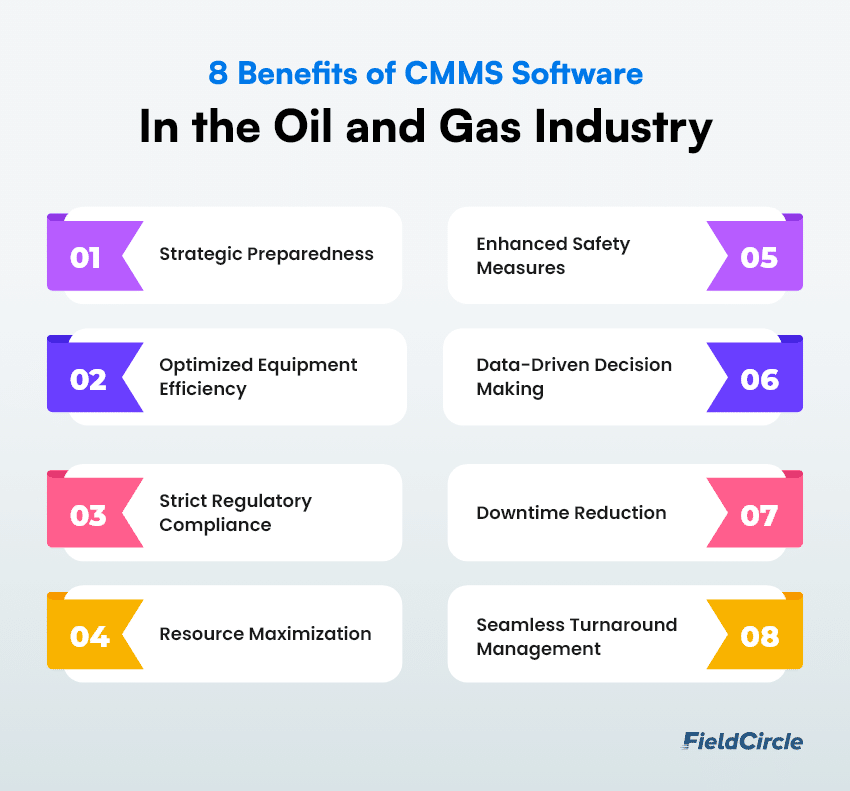
Maintenance in oil and gas relies on the proper care and upkeep of a wide range of highly specialized equipment. From pumps, compressors, and pipelines to storage tanks and gas turbines, each piece of machinery has its role to play in day-to-day operations. Operational efficiency in the industry rests on complex maintenance processes and specialized equipment.
Whether it is drilling equipment, wellhead components, or environmental protection systems like gas flaring units, every equipment must be maintained properly or else it results in costly breakdowns, unplanned downtime, and serious safety hazards. Then there are intricate systems, such as remote monitoring devices, vibration sensors, and non-destructive testing tools.
Given the level of sophistication in oil and gas operations, managing the upkeep of all this equipment demands precise coordination and diligent oversight. Traditional methods of maintenance scheduling, record-keeping, and task allocation quickly become unwieldy and carry a very high risk of failures.
A Computerized Maintenance Management System (CMMS) is a one-stop solution for managing these maintenance complexities. Coming with features like asset management, work order management, inventory management, a CMMS solution caters to the unique demands of the oil and gas sector. We see this through the following 8 significant benefits of CMMS in oil and gas:
- Anticipates Outcomes and Develop Preparedness
- Boosts Paraphernalia Performance
- Precisely Works as per Regulatory Standards
- Takes the best out of Resources
- Acts as a Shield
- Uses Data for Smart Moves
- Defies Downtime
- Standardizes Turnaround Management
Anticipates Outcomes and Develop Preparedness
The ability of a CMMS to support preventative maintenance and predictive maintenance lies in its capacity to collect and analyze maintenance data from equipment across oil and gas facilities. Using a CMMS you can build a solid predictive maintenance program. Sensors attached to critical machinery, pipelines, and drilling rigs continuously monitor operational parameters, including temperature, pressure, and vibration levels. After the CMMS gets this data, it feeds it into integrated AI and machine learning (ML) models that identify patterns, anomalies, and trends. The system’s capacity to analyze large datasets helps technicians detect early signs of wear or degradation, and they can take action well in time.
When anomalies are detected, the CMMS generates recommendations for proactive interventions and guides maintenance teams in addressing potential issues. This is how a CMMS software for oil and gas helps build predictive maintenance strategies for oil and gas. It allows maintenance teams to decide on optimal repair windows and thus extends the life of equipment.
The system continuously refines its algorithms based on historical performance and failure patterns, enabling more accurate predictions over time. A CMMS performs the role of a preventive maintenance software and also tracks the outcomes of each maintenance action, thus creating a feedback loop that helps build preventive maintenance strategies.
Boosts Paraphernalia Performance
There are many specialized equipment used in oil and gas. A computerized maintenance management software (CMMS) for oil and gas is central to sustaining the performance of this equipment. For instance, pigging operations, which are essential to keeping pipelines free of blockages, are managed through the system. Pigging involves deploying a device that cleans and inspects the interior of pipelines, ensuring smooth workflow. The CMMS automates these critical operations, making certain they occur precisely when required, mitigating risks of neglect or oversight. With the automated reminders and comprehensive tracking it offers, maintenance teams can avoid costly operational disruptions.
In drilling rigs, where equipment like top drives, mud pumps, and drill bits endure extreme conditions, any downtime can lead to significant losses. A CMMS helps avoid such losses by scheduling maintenance activities efficiently, and prevents unexpected breakdowns. Monitoring tools within the CMMS keep track of drilling equipment in real time, and enable proactive interventions. By identifying potential issues early on, the system prevents equipment failures that could halt drilling operations, which helps keep projects on schedule and within budget.
CMMS provides valuable insights into equipment wear and tear, extending the longevity of expensive drilling assets. Maintenance schedules aligned with manufacturer recommendations and industry best practices help preserve the operational integrity of rigs. Further, detailed maintenance records offer a clear picture of equipment performance, and operators are well-positioned to make right decisions regarding repairs or replacements.
Precisely Works as per Regulatory Standards
Navigating stringent regulations in oil and gas is made more manageable with the help of a CMMS, particularly in areas like flaring system management. Flaring systems, essential for controlling excess gases, are heavily regulated for environmental compliance. A CMMS schedules routine inspections and tracks repairs, ensuring that flaring systems operate within legal and environmental parameters. The detailed records maintained by the system become instrumental during audits, as they provide proof that compliance standards are consistently met. As CMMS streamlines the compliance process, it prevents potential fines and supports the industry’s commitment to sustainable operations.
In addition to environmental considerations, the system helps manage operational safety by monitoring the performance of the equipment. For example, it can provide real-time alerts when performance deviates from set thresholds, enabling quick corrective actions. By maintaining a thorough history of equipment maintenance and performance, the CMMS supports long-term sustainability goals, and keeps the maintenance tema ahead in the landscape of increasingly strict environmental standards.
Moreover, the system proves invaluable for managing licenses and certifications that come with expiration dates. It generates timely alerts before the due dates of critical certifications, reminding technicians of remaining compliant with regulations such as ATEX, IECEx, and other safety standards. As requirements brought by regulatory compliances grow more complex, the CMMS offers an organized, reliable solution to help oil and gas companies meet them effectively.
Takes the best out of Resources
In the oil and gas industry, resources extend beyond just equipment—they include personnel, spare parts, energy, and time, all of which are optimized with the use of a CMMS. For offshore platforms, where logistics are challenging due to harsh environmental conditions, a CMMS serves as a centralized hub for managing maintenance activities. By tracking the availability of resources and aligning them with maintenance schedules, the system eliminates inefficiencies that arise from poor planning.
The system’s real-time monitoring capabilities ensure that maintenance works are performed as scheduled, helping to preserve critical resources like blowout preventers (BOPs) and drilling systems.
Since offshore operations are particularly sensitive to delays, and the logistical complexity of transporting spare parts and personnel makes the use of a CMMS indispensable. Through scheduled maintenance, implementing a maintenance software helps minimize unplanned trips to the platform, reduces costs and increases resource availability. Using advanced features, the maintenance team can easily track the energy consumption and assess the energy needs of the upcoming maintenance activities.
Acts as a Shield
Maintaining safety in oil and gas, where flammable materials and hazardous environments are the norm, requires an advanced maintenance strategy. Using CMMS software helps in this regard as it schedules and documents inspections for explosion-proof equipment, so that safety-critical devices are always up to standard. Finally, in environments where even a small error could result in catastrophic consequences, the system’s precise management of maintenance tasks is essential to preventing accidents. Safety management, in fact, is one of the key features of CMMS.
The integration of a CMMS allows operators to comply with stringent safety regulations and compliances such as ATEX and IECEx, as we saw, which govern equipment used in explosive atmospheres. By maintaining detailed records of all safety inspections and repairs, technicians are aware as to what practices to follow to avoid potential hazards by identifying when equipment is nearing its inspection deadline. They are always aware that they need to work as per the safety and regulatory norms.
Proactive maintenance through a CMMS thus helps avoid safety-related incidents by addressing equipment vulnerabilities before they escalate into more significant issues. The system’s ability to provide predictive analytics allows operators to anticipate potential hazards, enabling preventive actions that safeguard both workers and assets. While sustaining asset performance, the tool also maintains the health of technicians. In high-risk environments, where safety is paramount, the use of a CMMS can make the difference between safe operations and life-threatening accidents.
Uses Data for Smart Moves
Oil and gas companies benefit immensely from the data-driven insights a CMMS provides. By capturing vast amounts of data from maintenance operations, equipment performance, and environmental factors, the maintenance management system enables decision-makers to base their strategies on real-time information. Maintenance schedules, equipment failure rates, and operational conditions all feed into the CMMS, and provide a holistic view of operational efficiency. Consequently, a diligent use of CMMS reduces downtime and improves equipment uptime.
The system’s ability to consolidate data from various sources, such as sensors and manual inspections, allows for a comprehensive analysis of equipment health. Historical data helps identify trends in equipment performance, which can inform future maintenance schedules and investment decisions. Operators can go through dashboards and gain insights into the actual performance and adopt the right course of action.
Defies Downtime
Downtime brings a drastic change to the equipment performance, and results in high maintenance costs. Let’s understand this with the example of pipelines in oil and gas. The unpredictable nature of pipeline failures in oil and gas can lead to significant downtime and financial losses. A CMMS helps prevent such incidents by maintaining a strict schedule of inspections and repairs. Pipelines are subject to constant monitoring, and the system alerts operators when maintenance is needed, which prevents unexpected breakdowns that could halt production.
Scheduling regular maintenance tasks through the CMMS helps operators keep pipelines in optimal condition, which naturally, extends their lifespan and reduces the likelihood of unplanned downtimes. Furthermore, the system’s real-time monitoring capabilities enable operators to respond quickly to any anomalies detected in the pipeline network. This is how a CMMS reduces downtime and maintains the smooth flow of operations, and contributes significantly to the overall profitability of oil and gas facilities.
Standardizes Turnaround Management
Turnarounds in oil refineries represent one of the most complex and resource-intensive events, requiring meticulous planning and execution to minimize downtime. A CMMS provides a robust framework for organizing, tracking, and executing maintenance activities. Each piece of equipment within the refinery requires specific attention during a turnaround, and a CMMS ensures that every detail, from inspections to repairs, is accounted for, thereby reducing the risk of missing critical tasks.
The system helps streamline the coordination of multiple teams, each responsible for different aspects of the turnaround. Clear scheduling and task tracking within the CMMS prevent bottlenecks and miscommunications, which can otherwise lead to delays. By maintaining a detailed log of maintenance activities, the CMMS allows managers to easily adjust plans on the fly if unexpected issues arise, and keeps the turnaround on schedule.
Refineries benefit from a CMMS by minimizing the duration of turnarounds, as it leads to quicker resumption of production and reduces financial losses associated with downtime. The ability to systematically plan and execute maintenance reduces the frequency of future turnarounds and contributes to long-term cost savings. Moreover, with everything documented, post-turnaround evaluations become more straightforward, which paves the way for continuous improvement in maintenance and operational productivity.
Takeaway
For an industry where even a small hiccup can lead to significant financial repercussions, having a system that keeps everything in sync is crucial for maintaining smooth operations. A CMMS is an essential tool for minimizing operational risks. Beyond just improving daily operations, a CMMS integrates seamlessly with other critical systems like ERP and supply chain management, and provides a holistic view of the business.
Solid maintenance planning demands a good CMMS that is compatible with mobile devices to offer convenience to your maintenance teams. Moreover, as the oil and gas industry continues to evolve, every oil and gas business must invest in a CMMS to well-position itself in dealing with future challenges in maintenance management and avail opportunities of easily adopting to ongoing changes.