What Is Reactive Maintenance and How to Prevent It?
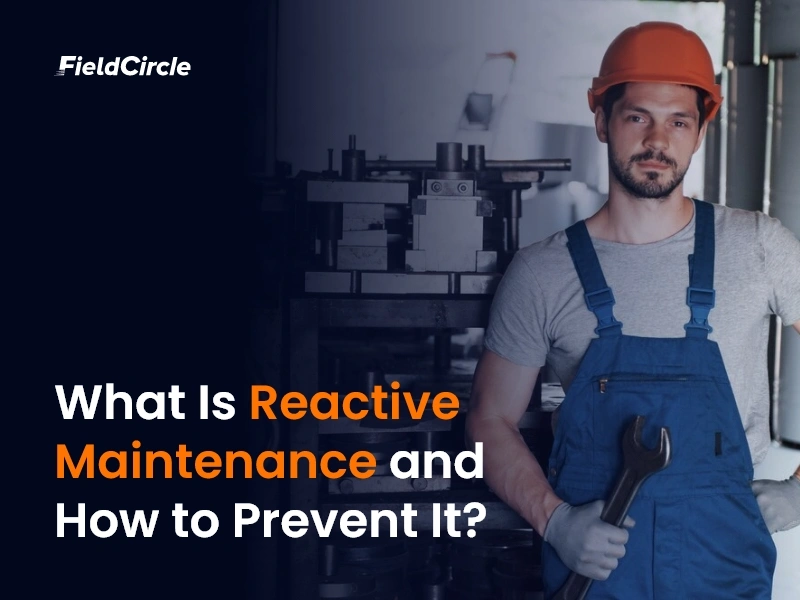
“You never know when it will break—until it does.”
That’s the grim reality maintenance leaders face every day. Unplanned equipment failures disrupt production, lead to expensive emergency repairs, compromise safety, and ultimately chip away at your company’s bottom line.
Plant Engineering’s research shows that reactive maintenance strategy can consume anywhere from 34% to 45% of a maintenance team’s time, costing industries billions annually in lost production and repair expenses. On the other hand, organizations that move to a more proactive maintenance approach face 52.7% less unplanned downtime and 51.8 % less additional costs due to faults/failures of equipment.
If you’re tired of playing catch-up with equipment breakdowns and want to take control of your maintenance costs, it’s time to rethink your strategy.
In this complete guide on reactive maintenance, we delve into the ins and outs of reactive maintenance, the hidden costs that come with its “fix-it-when-it-breaks” approach, and, most importantly, how you can transition to proactive methods that not only save money but also improve safety and asset longevity.
Understanding Reactive Maintenance
Reactive maintenance, also known as breakdown or run-to-failure maintenance, is exactly what it sounds like: waiting until equipment fails before taking action. While this approach might seem attractive because it eliminates the upfront costs of routine upkeep, it comes at a steep price.
There are several types of reactive maintenance approaches:
- Breakdown Maintenance
- Emergency Maintenance
- Run-to-Failure Maintenance
- Corrective Maintenance
Maintenance activities are triggered only after complete equipment failure, typically resulting in unplanned downtime. It is used for non-essential systems where uptime isn’t critical, and repair resources are mobilized post-failure. This approach often lacks diagnostic planning and can lead to extended downtime if spare parts or technicians are not readily available. It’s commonly used for legacy systems where monitoring is not cost-effective.
A rapid-response maintenance action executed immediately after an unexpected equipment failure that jeopardizes safety, regulatory compliance, or critical operations. It often bypasses standard troubleshooting protocols and preventive assessments to prioritize speed. Emergency maintenance is resource-intensive and may involve temporary fixes or system overrides until a permanent solution is planned under scheduled corrective or preventive maintenance tasks.
A strategic approach where specific low-priority, low-cost, or redundant equipment is operated until it fails completely, with replacement or repair pre-planned as part of operational logistics. Typically applied to assets where monitoring or preventive interventions are unjustifiable due to low repair costs or minimal operational impact. Spare parts and repair procedures are usually stocked and documented in advance to reduce restoration time. This type of maintenance is best suited for non-critical assets where downtime has minimal consequences.
Maintenance is conducted after a fault or degradation is detected, but before total system failure occurs. It is often driven by condition-based monitoring, inspections, or operator observations and typically aims to restore equipment to optimal functionality. Corrective maintenance may involve replacing worn components, recalibration, or eliminating root causes to prevent further degradation. It’s a hybrid between reactive and proactive strategies, depending on how early the defect is identified. Technicians usually document the maintenance work performed.
The Consequences of Relying on Reactive Maintenance
Despite its simplicity, reactive maintenance can wreak havoc on your operations. It is one of those areas where time is lost. In many cases, reactive strategies end up draining resources and morale alike. When you depend solely on reactive maintenance, the costs aren’t limited to the price of parts or labor; they extend into every corner of your operation. The disadvantages of reactive maintenance are far-reaching, from unpredictable downtime to rising repair costs and increased safety risks.
Unpredictable Downtime
Unplanned downtime is the nemesis of efficiency. Unplanned downtime costs industries over $50 billion every year, and equipment failure accounts for 42% of this unplanned downtime. When repairs are reactionary, there’s no way to schedule or mitigate the impact, and every minute of lost production translates into lost revenue.
Skyrocketing Repair Costs
Emergency repairs often come with premium pricing. Expedited shipping of parts, overtime labor, and rushed diagnostic procedures add up quickly—especially when reactive maintenance forces teams to act under pressure with no time to negotiate or plan ahead. What seemed like a cost-saving measure initially becomes an expensive cycle of “fixing” that no one saw coming. Many companies find that the unpredictable expenses of reactive maintenance make budgeting a nightmare.
Reduced Asset Lifespan and Safety Risks
Equipment that is only maintained when it breaks down tends to operate under stress for long periods, which can accelerate wear and tear. Reactive maintenance not only shortens the lifespan of assets but also raises the risk of safety hazards. Over time, this approach can result in machinery that is more costly to repair and more dangerous to operate.
Strain on Maintenance Teams
When your maintenance team is constantly reacting to breakdowns, they rarely have the time to perform routine inspections or improvements. This reactive firefighting mode leads to a demoralized workforce, inefficient resource allocation, and, ultimately, a decline in overall operational performance. The absence of routine maintenance further increases the likelihood of undetected issues escalating into major failures.
Challenges for Maintenance Leaders When Relying on Reactive Maintenance
Having reactive maintenance as one of the maintenance strategies comes with its own share of challenges for maintenance leaders. The major challenges are:
- Budgeting Woes: It’s difficult to forecast costs when repairs occur unpredictably. Instead of having a steady, planned expenditure, you’re forced to scramble for funds when an emergency hits—one of the most financially draining aspects of reactive maintenance.
- Operational Disruptions: Unscheduled downtime throws off production schedules and can derail entire projects. This unpredictability makes it nearly impossible to maintain smooth operations.
- Safety and Compliance: The urgency of reactive repairs often means that safety protocols are bypassed in the rush to get equipment running again, increasing the risk of accidents.
- ROI Concerns: Top management is increasingly scrutinizing maintenance strategies. Spending millions on emergency repairs while equipment fails unexpectedly undermines return on investment (ROI) and impacts overall profitability.
How to Prevent Reactive Maintenance: Proactive Strategies
These challenges underscore the need for a more proactive approach. The question is: how can you shift from a reactive “firefighting” mode to a proactive, strategic maintenance model? To break free from the cycle of unplanned repairs, organizations must adopt proactive maintenance strategies.
Two key approaches that have proven their worth across industries are preventive and predictive maintenance. Along with them, you must make reliability-centered maintenance (RCM) a part of your maintenance management program. Let’s understand these various maintenance strategies and how they prove useful.
Preventive Maintenance
Preventive maintenance approach entails scheduling regular inspections and servicing equipment to replace parts or make adjustments before a failure occurs. For instance, independent industry research shows that structured, scheduled maintenance can reduce unplanned downtime by 35–50% and extend the useful life of critical assets by 20–40%.
Although this approach requires a higher upfront investment in planning and labor, studies from industry analysts consistently demonstrate that the long‐term savings through fewer emergency repairs, improved production continuity, and enhanced equipment reliability significantly outweigh these initial costs. A well-designed maintenance plan plays a key role in organizing these tasks effectively and maximizing equipment uptime.
Predictive Maintenance
Predictive maintenance approach takes proactive maintenance one step further by using real-time data and analytics to forecast when a piece of equipment is likely to fail. Using IoT sensors, advanced algorithms, and maintenance software, predictive maintenance allows you to plan maintenance activities optimally before a breakdown occurs.
According to a study by Deloitte, on average, predictive maintenance increases productivity by 25%, reduces breakdowns by 70%, and lowers maintenance costs by 25%.
Reliability-Centered Maintenance (RCM)
RCM is a risk-based approach that helps determine which assets need proactive care. By evaluating the potential consequences of failure and the likelihood of occurrence, RCM allows you to allocate maintenance resources more effectively. This method ensures that critical assets receive the attention they need while non-critical equipment can be managed with a run-to-failure strategy.
RCM also encourages cross-functional collaboration by involving operations, maintenance, engineering, and safety teams in the decision-making process. It comes with an integrated approach that leads to a deeper understanding of asset functions, failure modes, and operational context, which in turn supports more informed maintenance strategies.
Take Away
Relying solely on reactive maintenance is no longer a viable long-term strategy. While reactive maintenance may still serve a purpose in specific scenarios, organizations must recognize that its role should be limited within a broader, more forward-thinking maintenance framework. Striking the right balance—where only a small portion of the workload is reactive—helps minimize unexpected failures without burdening the system with unnecessary preventive tasks.
Looking ahead, the shift toward proactive maintenance isn’t just a recommendation—it’s a necessity. As technologies like CMMS, IoT, and data analytics continue to evolve, they empower teams to predict issues before they occur, protect critical assets, and streamline operations. By investing in these tools and adopting preventive strategies, businesses successfully move from fighting fires to building resilience and efficiency into every layer of their maintenance program.