Preventive vs Predictive Maintenance: Which Strategy is Right for Your Assets?
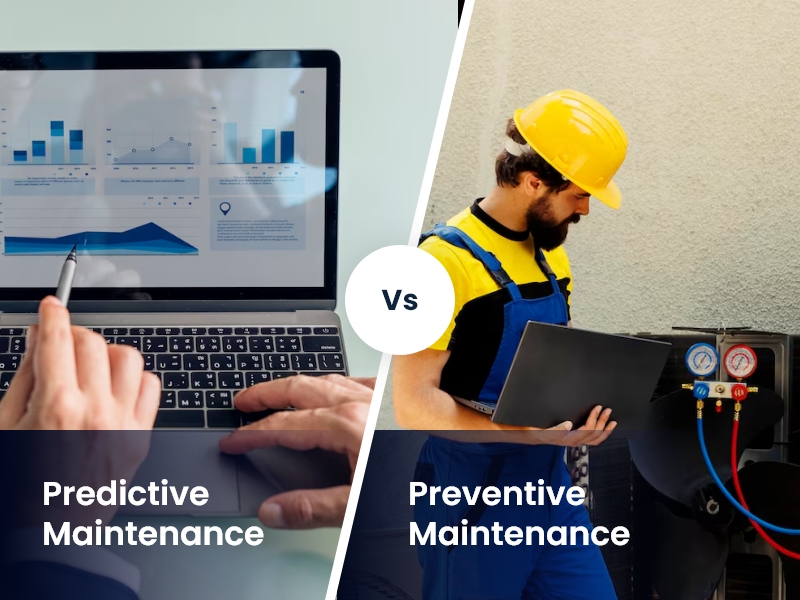
Imagine a high-speed production line that comes to a sudden halt because of an unexpected equipment failure. The ripple effect? Lost productivity, expensive repairs, and missed deadlines. In industrial and operational environments where every second counts, these kinds of disruptions can be catastrophic. This is where a well-planned maintenance strategy comes in, acting as the backbone of asset reliability and operational efficiency.
Companies use two main maintenance strategies to prevent these disruptions: preventive maintenance and predictive maintenance. Preventive maintenance is where the maintenance team performs routine inspections and scheduled servicing to prevent breakdowns, such as changing your car’s oil at regular intervals regardless of its condition.
On the other hand, predictive maintenance takes a more advanced approach, using real-time data, sensors, and analytics to identify potential issues before they become problems, thereby performing maintenance only when necessary.
Each strategy is viable in its own terms and deciding which strategy is right for your assets depends on factors like equipment criticality, operational goals, and budget. Understanding how each strategy fits into your operations can be the key to maximum productivity and minimum unexpected failures. In this discussion we draw a thorough comparison between these two strategies and help you decide which strategy you should pick up and when.
What is Preventive Maintenance?
Preventive maintenance is a proactive strategy for maintaining equipment, systems, and infrastructure for efficient operation. It includes regular and routine inspection, servicing, and repairs to keep equipment and machinery in optimal working condition and increase reliability.
Instead of conducting maintenance after breakdowns or malfunctions, preventive maintenance relies on systematic steps to identify potential risks, schedule tasks, and intervene on time before they escalate.
Preventive maintenance is widely used in the manufacturing, transportation, facility management, and IT industries. One of the common examples of preventive maintenance in a manufacturing plant is the inspection of mechanical and software components of CNC machines. It includes regular assessments of coolant levels, axis alignment, electrical connections, calibration, and firmware to keep the machines operating smoothly.
Some of the key features of preventive maintenance are
- Scheduled inspection to detect equipment wear and tear early.
- Systematic servicing, such as lubrication, routine cleaning, part replacements, and equipment adjustments.
- Documentation and tracking of maintenance activities for future reference.
- Standardized maintenance procedure for maintaining consistency in maintenance tasks.
- Resource planning to manage spare parts and labor efficiency.
What is Predictive Maintenance?
Predictive maintenance (PdM) is a condition-based approach that uses real-time data to predict equipment failures before they occur. It continuously monitors asset conditions through sensors and data collection to perform maintenance activities only when necessary.
By integrating IoT sensors, machine learning algorithms, and advanced data analytics, predictive maintenance focuses on actual machine conditions to optimize performance.
Prominently used in manufacturing, energy, transportation, oil and gas, healthcare, and automotive sectors, predictive maintenance helps to minimize unplanned downtime and streamline maintenance costs, among other benefits. For example, an aluminum manufacturer implemented a specialized predictive maintenance solution, reducing unplanned downtime by 20% and achieving its ROI goals within 6 months.
Some essential features of predictive maintenance include
- Condition-based monitoring using IoT sensors to track real-time equipment data.
- Predictive analytics with AI and machine learning to identify failure patterns.
- Automated alerts based on analytics data for timely interventions.
- Data-driven decision-making to optimize maintenance schedules.
- CMMS integration for streamlined operations.
Key Differences Between Preventive and Predictive Maintenance
While both preventive and predictive maintenance aim to keep equipment and assets in best shape to sustain operational continuity, their implementation approaches differ. The scheduling process, maintenance costs, and overall effectiveness are other areas of distinction between these proactive maintenance strategies.
Below is a comparison between the two maintenance approaches that will help understand these key aspects becomes crucial for organizations to choose the right maintenance strategy that aligns with their operational needs, budget, and equipment criticality.
Aspect | Preventive Maintenance | Predictive Maintenance |
---|---|---|
Maintenance Schedule | Time or usage-based intervals | Condition-based, relies on real-time data |
Implementation | Periodic checks and routine servicing | Advanced monitoring tools and predictive analytics |
Cost Considerations | Lower upfront costs but risk of over-maintenance | Higher initial investment but optimized maintenance cycles |
Effectiveness | May lead to unnecessary maintenance | Tailored to asset conditions; reduces waste and downtime |
Comparison Based on Maintenance Schedule
Preventive maintenance follows a time-based or usage-based approach. It means that organizations implementing this strategy conduct inspections and servicing at regular intervals, regardless of the assets’ actual condition. By examining equipment periodically, maintenance teams can track equipment performance, detect potential issues early, and reduce the risk of unexpected failure. However, regularly scheduled inspections add up to operational costs with unnecessary maintenance.
In contrast, predictive maintenance follows a condition-based approach. It relies on real-time data from IoT sensors and analytical tools to determine when maintenance is actually needed and intervene before letting the potential issues cause significant impact. By continuously tracking equipment performance, organizations minimize disruptions and ensure that servicing occurs only when an asset shows signs of potential failure. But, if the data is inaccurate, it can lead to missed maintenance, costly emergency repairs, and unplanned breakdowns.
Comparison Based on Implementation
Implementing preventive maintenance is relatively simple and relies on scheduled inspections, routine servicing, and planned part replacements. These interventions are driven by time intervals or asset usage. Since this method does not require complex technology, it becomes a perfect fit for businesses with limited resources or small-scale operations. The only drawback is that they do not account for the actual and current equipment conditions, making maintenance works imprecise.
Conversely, deploying predictive maintenance involves leveraging advanced monitoring tools, such as IoT sensors, vibration analysis devices, machine learning algorithms, and specialized computer maintenance management system (CMMS) software. These technologies continuously gather and analyze real-time data to detect anomalies and forecast potential failures. Despite PdM providing greater accuracy, it requires specialized expertise and integrated software systems, which may lead to a complex and resource-intensive implementation process.
Comparison Based on Costs
Since preventive maintenance does not require the installation of a specific technology or sophisticated tools, it requires a low upfront investment and related initial expenses. The only visible costs associated with this strategy include labor, routine inspections, and replacement parts expenses. However, this approach calls for scheduled inspections and routine equipment servicing, which leads to over-maintenance. As a result, it increases long-term expenses due to wasted resources and downtime during scheduled maintenance.
On the contrary, predictive maintenance requires a higher upfront investment in technologies such as condition monitoring sensors, data analytics platforms, and specialized staff training. Despite the high initial costs, PdM is a cost-efficient option in the long run as it helps to avoid unexpected breakdowns, prevent costly emergency repairs and unnecessary repairs, minimize unplanned downtime, and extend asset lifespan.
Comparison Based on Effectiveness
Preventive maintenance reduces the risk of equipment failure by servicing the machinery periodically. It is suitable for noncritical assets with predictable wear and tear. However, it can be inefficient because it does not consider the actual condition of the equipment. It may lead to unnecessary maintenance and waste, which in turn results in increased operational costs and downtime for fully functioning equipment.
On the other hand, predictive maintenance is highly effective because it uses real-time data to implement maintenance at the exact moment it is needed. It minimizes maintenance waste by only servicing when needed and significantly prevents downtime and unexpected failures. These advantages make PdM very valuable for high-value or critical infrastructure where unplanned failures can be costly.
How Do the Benefits of Preventive and Predictive Maintenance Compare?
Both preventive and predictive maintenance are beneficial for enhancing the overall operational productivity. Although their agenda or the end goal is the same, their benefits contradict due to the diverse approaches they take for implementation and scheduling. Understanding the unique advantages of each maintenance strategy helps organizations choose the most suitable approach.
Benefits of Preventive Maintenance
- Reduces failure risks through regular servicing and inspections.
- Easier to plan and budget due to predictable maintenance schedules.
- Suitable for simple, less-critical systems.
- Improves safety by reducing the likelihood of unexpected breakdowns or hazardous failures.
- Minimizes costly emergency repairs by addressing issues before they escalate.
Benefits of Predictive Maintenance
- Minimizes downtime through precise, real-time monitoring and interventions.
- Extends asset lifespan with data insights.
- Ideal for critical, high-value assets that require continuous reliability.
- Reduces maintenance costs by avoiding unnecessary routine checks and addressing critical needs.
- Enhances resource efficiency by optimizing labor, spare parts, and operational schedules.
- Improves decision-making through data-driven insights and predictive analytics for better asset management.
When Should Each Maintenance Strategy Be Used?
Preventive maintenance is used for equipment with predictable wear and moderate criticality, and predictive maintenance is for high-value, mission-critical assets where failure can cause significant downtime or safety risks. Each of these two maintenance strategies optimizes asset performance and reduces downtime and maintenance costs, but effectiveness depends on the equipment, operational demands, and resources.
When to Choose Preventive Maintenance?
This approach is appropriate for equipment with predictable wear patterns, where routine, scheduled interventions help avoid failure risks. The best way to implement it is using a preventive maintenance software that offers all necessary features.
Regular tasks like filter changes and duct inspections for the HVAC system are part of preventive maintenance. They help prevent breakdowns and maintain efficiency, and ensure smooth operations without advanced monitoring.
All-in-all, organizations should choose preventive maintenance when
- Equipment has consistent usage patterns with predictable wear and tear.
- Maintenance schedules are regulatory requirements (e.g., fire safety systems).
- The cost of failure is moderate, not justifying advanced monitoring investments.
- Downtime windows for maintenance are easily scheduled without affecting operations.
- Maintenance tasks are simple and do not require real-time condition monitoring.
When to Choose Predictive Maintenance?
Predictive maintenance is ideal for critical, high-value assets where equipment failure leads to massive financial losses, safety hazards, and production delays. Like the earlier one, this too can be permeated with a dedicated predictive maintenance application.
With the help of such tools airlines implement predictive maintenance to monitor aircraft engines, analyzing real-time data like vibration and temperature.
In general, organizations should choose predictive maintenance when
- Asset failure has high repair or downtime costs.
- Equipment operating in complex environments has unpredictable failure patterns.
- Access to real-time data with advanced analytics capabilities is available.
- Downtime is costly.
- Unexpected failures can disrupt core operations.
Takeaway: Get the Best of the Both Worlds
Shifting from reactive strategies to well-planned maintenance approaches can transform how businesses manage assets. While preventive maintenance minimizes unexpected failures through scheduled servicing, predictive maintenance leverages real-time data and AI-driven insights to optimize interventions.
However, a hybrid approach—integrating both methods—can offer the best of both worlds, balancing cost, efficiency, and reliability. Businesses that adapt to this evolving landscape will not only cut downtime but also future-proof their operations against disruptions. Effectively, FieldCircle maintenance applications are a key enabler in this process.