CMMS Vs EAM: Know How CMMS is Different From EAM
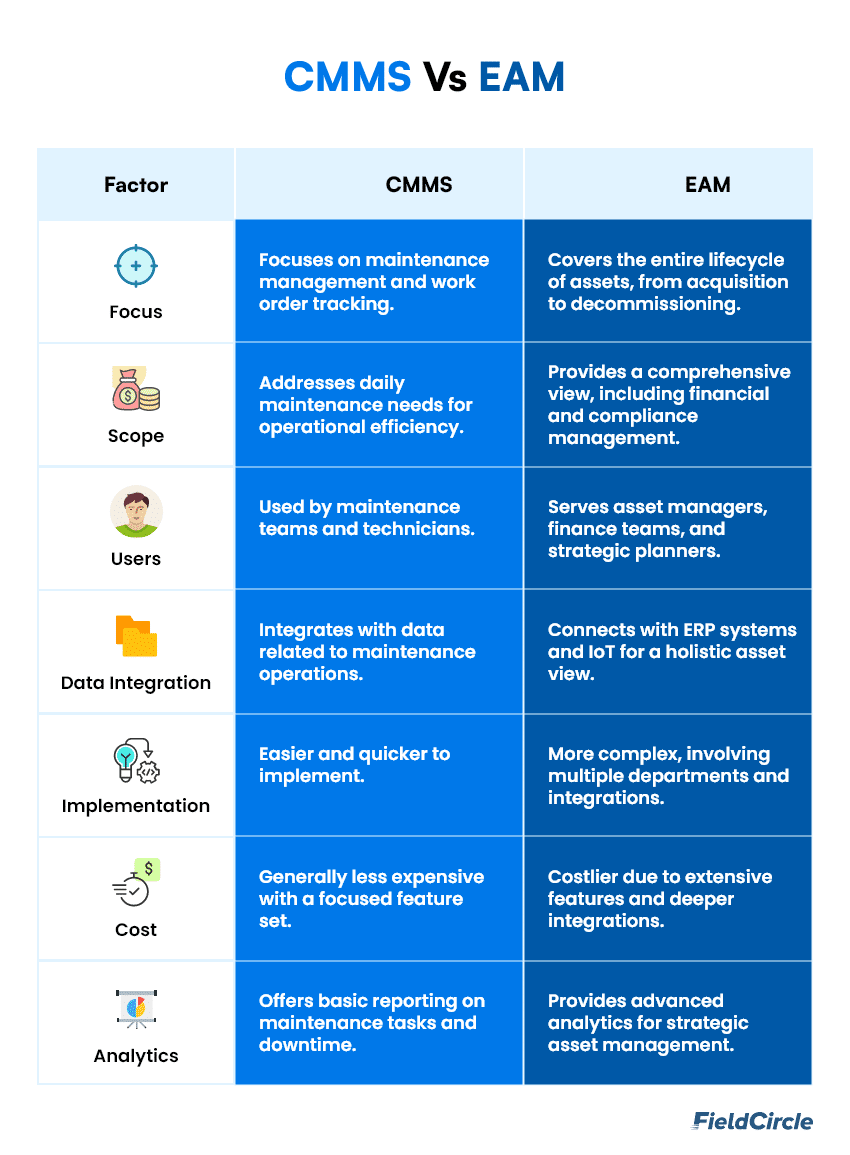
The CMMS (Computerized Maintenance Management System) and EAM (Enterprise Asset Management) software solutions are both important for asset management but serve different purposes. CMMS is maintenance focused, with work order management, scheduling and asset tracking, for facilities that want to reduce downtime and optimize equipment reliability through daily maintenance. EAM covers the entire lifecycle of an organization’s assets from acquisition to decommissioning. Its broader functionality includes compliance, financial management and data analytics, so it’s a more comprehensive tool for larger organizations with bigger asset portfolios and strategic planning.
In short, while CMMS is a straightforward choice for teams managing immediate maintenance tasks, EAM’s expansive scope makes it indispensable for organizations requiring a holistic view that aligns asset performance with long-term business goals. Below we discuss at length about how CMMS compares with EAM, where it differs and where both of them fall in the same plane.
What is CMMS (Computerized Maintenance Management System)?
A Computerized Maintenance Management System (CMMS) is software designed primarily for maintaining and managing an organization’s assets. It provides a centralized platform for tracking maintenance activities, so that equipment operates efficiently and downtime is minimized.
Key features of CMMS:
- Work Order Management: Allows teams to create, track, and prioritize work orders. Maintenance staff can easily manage requests, ensuring prompt responses to issues.
- Preventive Maintenance Scheduling: Helps schedule regular maintenance tasks to prevent equipment failure.
- Asset Tracking: Organizations can keep tabs on all assets, including their condition, location, and maintenance history.
- Maintenance History Recording: A maintenance software records all maintenance activities performed on each asset. Stakeholders can use historical data, analyze trends and make informed decisions about future maintenance needs.
- Inventory Management: Helps track spare parts and inventory levels, ensuring that necessary components are available when needed.
You can read more about CMMS features here: 17 Key CMMS Features to Look For
Use Case:
CMMS capabilities are best for facilities aiming to automate maintenance workflows and cut equipment downtime. Organizations are able to schedule maintenance tasks efficiently, track work orders easily, and proactively address issues before they escalate into loss-causing agents. As a result, equipment lasts longer, reliability improves, and repair costs drop over time.
What is EAM (Enterprise Asset Management Software)?
An EAM software is a tool designed to assist organizations in managing their physical assets throughout their entire lifecycle. The best thing about EAM software is that it integrates various functions such as tracking and maintenance, procurement, compliance, decommissioning etc. into a single system. So, it serves as a comprehensive platform to manage asset management needs.
Key Features:
- Asset Lifecycle management: Tracks assets from acquisition to disposal, providing insights for maintenance and replacement decisions.
- Procurement: Supports effective asset acquisition through analysis of historical data and budgeting for future needs, helping organizations make informed purchasing choices.
- Work Order Management: Helps create, prioritize, and track work orders, so that teams are able to address issues swiftly.
- Compliance: Assists in maintaining adherence to industry regulations and standards, simplifying audit preparation by keeping necessary documentation organized.
- Financial Management: Provides tools for analyzing asset-related costs, aiding in budget planning and investment decisions.
- Analytics: Offers data analysis capabilities to evaluate asset performance, identify trends, and inform future equipment and asset maintenance and upgrade strategies.
Use Case:
EAM systems prove particularly beneficial for organizations with extensive and complex asset portfolios, such as manufacturing plants and utilities. By implementing an EAM application, businesses operating in these industries can easily improve asset reliability, extend equipment lifespan, and reduce repair costs.
EAM vs CMMS: What are the Key Differences Between EAM and CMMS?
CMMS is maintenance-centric, while EAM software provides a broader view of asset management across all phases. EAM applications are generally more complex, suited for large enterprises with strategic asset planning needs. CMMS is more user-friendly and easier to implement for straightforward maintenance needs. We dissect the difference between CMMS and EAM further in detail across the following key factors:
Focus
CMMS zeroes in on maintenance management. Its primary goal revolves around creating work orders, scheduling preventive maintenance, and addressing repairs as they arise. The day-to-day functionality allows technicians to respond quickly to equipment issues, and keep operations running smoothly.
In contrast, EAM software encompasses the entire lifecycle of assets. It spans from the planning and acquisition phase through to operations, maintenance, and eventual decommissioning. This broader focus allows EAM systems to track not only the condition of assets but also their financial implications over time.
Scope
CMMS attends to the daily maintenance requirements of an organization. Its design keeps equipment operational while managing tasks efficiently. Maintenance personnel can organize their workloads effectively and address immediate equipment needs without getting bogged down in long-term planning.
In contrast, an EAM tool presents a much wider scope, overseeing assets from a holistic perspective. Financial tracking, compliance, and strategic planning become integral components of its functionality. Organizations manage not just the upkeep of assets but also their financial and regulatory obligations throughout their lifecycle.
Users
CMMS primarily serves teams, facilities managers, and technicians focused on daily equipment upkeep. Users engage with a maintenance management software to efficiently handle immediate maintenance tasks and repairs.
Conversely, EAM software caters to a broader audience, supporting asset managers, operations managers, finance departments, and strategic planners. A unified view of the organization’s asset performance allows for insights that impact various business decisions.
Data Integration
A computerized maintenance management software integrates with maintenance-related data. Such integration keeps maintenance tasks running smoothly but a CMMS may not provide a complete view of how assets impact broader organizational goals.
EAM, however, connects with Enterprise Resource Planning (ERP) systems, financial management tools, and even IoT devices. This connectivity offers a comprehensive perspective on assets and their influence on the entire organization, making it possible to analyze how asset performance relates to overall business objectives.
Implementation
Implementing a CMMS tends to be more straightforward, leading to a quicker setup for organizations due to its focused nature.
On the flip side, an EAM application requires a more extensive approach, involving multiple departments and integrating with various systems. The complexity reflects the depth and breadth of features offered by EAM applications.
Cost
CMMS solutions generally sit at a lower price point. A concentrated focus on maintenance functions and simpler implementation processes contribute to affordability. Organizations seeking to address basic maintenance needs without extensive investment find CMMS appealing.
In comparison, EAM tools come with a higher price tag. The wealth of features, deeper integrations, and advanced analytics capabilities justify the costs. Organizations looking to optimize their entire asset portfolio see value in investing in EAM.
Analytics
CMMS provides basic reporting on maintenance tasks and equipment downtime. These insights assist staff in making operational decisions based on immediate data. However, analytics capabilities remain relatively limited, which can impact a facility’s ability to fully measure CMMS ROI and uncover long-term value from the system.
EAM systems offer advanced analytics that encompasses asset performance metrics and return on investment (ROI) analysis. Such features support strategic decision-making and help organizations align asset management with long-term business goals.
Here is the summary of CMMS Vs EAM:
Factor |
CMMS |
EAM |
Focus |
Focuses on maintenance management and work order tracking. |
Covers the entire lifecycle of assets, from acquisition to decommissioning. |
Scope |
Addresses daily maintenance needs for operational efficiency. |
Provides a comprehensive view, including financial and compliance management. |
Users |
Used by maintenance teams and technicians. |
Serves asset managers, finance teams, and strategic planners. |
Data Integration |
Integrates with data related to maintenance operations. |
Connects with ERP systems and IoT for a holistic asset view. |
Implementation |
Easier and quicker to implement. |
More complex, involving multiple departments and integrations. |
Cost |
Generally less expensive with a focused feature set. |
Costlier due to extensive features and deeper integrations. |
Analytics |
Offers basic reporting on maintenance tasks and downtime. |
Provides advanced analytics for strategic asset management. |
What are the Similarities between CMMS and EAM System?
Computerized Maintenance Management Systems (CMMS) and Enterprise Asset Management (EAM) play complementary roles in optimizing asset performance. Both solutions assist organizations in managing physical assets effectively, leading to increased efficiency.
A core similarity lies in asset management. These systems help businesses organize equipment and machinery operations. Proper oversight minimizes downtime and ensures that assets perform at their best.
Both CMMS and EAM software enable teams to create, track, and manage work orders efficiently. Preventive maintenance as well as predictive maintenance are equally crucial. CMMS and EAM support scheduled maintenance based on time intervals or usage metrics. Both tools are useful for reducing the likelihood of unexpected breakdowns and help embrace a proactive maintenance culture within organizations.
Inventory management is a key feature in CMMS as well as EAM. It helps keep track of spare parts and supplies. With any of them at their disposal, maintenance staff can focus on their tasks rather than searching for necessary materials.
Finally, data tracking and reporting capabilities are present in both tools. Users can generate detailed reports on maintenance activities and equipment performance and understand how they are faring in compliance. With these insights organizations can fine-tune their maintenance and asset management strategies.
CMMS or EAM: Which is the Best Pick for Your Business Requirement?
Choosing between a CMMS and EAM depends on your organization’s specific needs and operational goals
If your primary focus is on day-to-day maintenance activities then choose a CMMS software. If you need a comprehensive solution that manages assets throughout their entire lifecycle then use EAM software.
To understand the fitment of both these tools for your niche needs and perfectly identify which amongst the two – EAM and CMMS solutions – your business needs, take a few minutes and have a discussion with our consultants.