Equipment Maintenance Software
Manage your heavy equipment maintenance operations in a more proactive and predictive way using FieldCircle’s equipment maintenance program configurable to your business needs.
How FieldCircle’s Equipment Maintenance Software Works
Explore how the key features work without signing up for a trial or demo.
Asset and Equipment Installation
Import your data and setup machinery and equipment installation projects. Import all your assets and equipment and track information about each asset, including specifications, maintenance history, and relevant documentation.
Maintenance Scheduling and Dispatch
Offering real-time updates and intelligent route optimization, our equipment maintenance program’s AI-powered scheduling and dispatch component helps you in optimizing your scheduling and streamlining coordination amongst stakeholders, saving significant time and cost.
Work Order, Inspections and Preventive Maintenance
Allow users to define service and maintenance schedules, set up recurring or one-off maintenance tasks like work order, PM or inspections, and track maintenance history, ensuring timely service and reducing equipment downtime. Using our product leads to fewer emergency calls and extends equipment life, and brings massive improvement in operational efficiency.
Real-Time Location Tracking
Bring next level of visibility in your operations with real time field team tracking. With automated time tracking and detailed analytics that offer vital insights, our equipment maintenance program empowers you to improve individual productivity and promote transparency across entire equipment service operations.
Spare Parts Management
Never let your equipment service team to run out of critical spare parts and inventory items by keeping a track of real-time inventory availability across all locations and trucks. Get notified at minimum order points and achieve better first-time fix rate.
Reporting & Dashboards
Generate custom reports, analyze key performance indicators (KPIs), and visualize data trends through interactive dashboards. Make more informed decisions with work order profitability data, asset health and cost insights and technician performance data.
Mobile Access
Our equipment maintenance mobile app for equipment companies offers instant access to crucial insights around customer information, work orders, and inventory levels, directly from the field, helping you achieve better first-time fix rate. Equipped with integrated GPS tracking capabilities, mobile capabilities reduce paperwork and let technicians have the most optimal routes at their fingertips.
Features of Our Equipment Maintenance Software that Unlock Efficiency
Full Mobile Accessibility
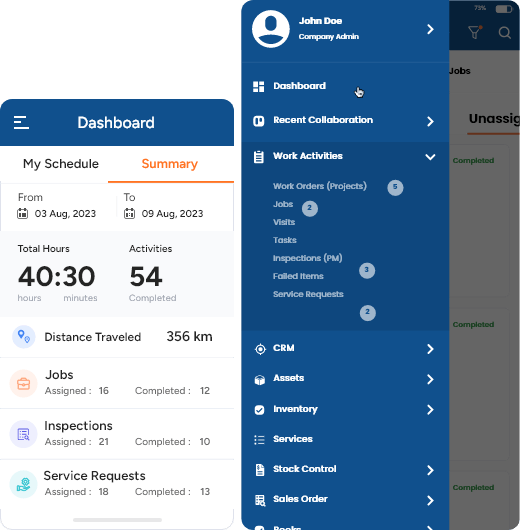
Our equipment maintenance mobile app for equipment manufacturers offers instant access to crucial insights around customer information, work orders, and inventory levels, directly from the field, thereby enhancing job complete rates. Equipped with integrated GPS tracking capabilities, mobile capabilities reduce paperwork and let technicians have the most optimal routes at their fingertips.
Customer and Location Management
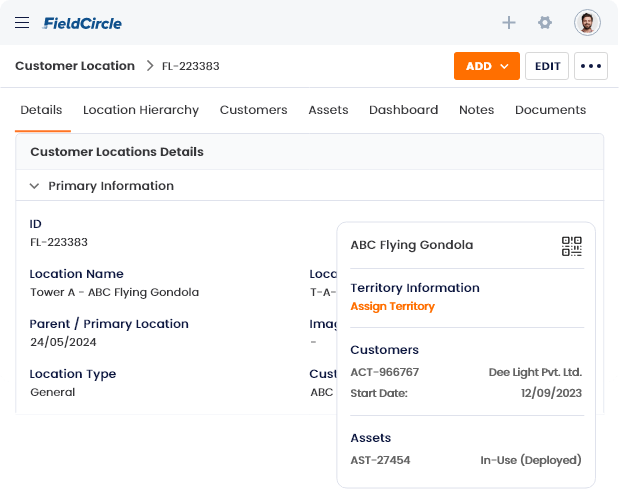
Effortlessly track customer preferences, location and other required details,and frame a strategy that helps provide a personalized touch to each interaction. So, with our field service software for equipment manufacturers, you offer an attractive service experience that keeps your customers coming happy and service operations costs low.
Service Request Management(Tickets)
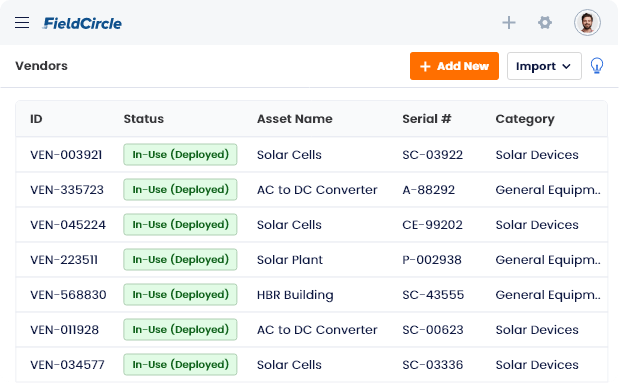
Effectively manage interactions with service contractors and establish and maintain strong relationships with external partners. Through its specialized features, our tool enhances service delivery and streamlines communication and coordination across the entire service ecosystem.
Technician and Crew Management
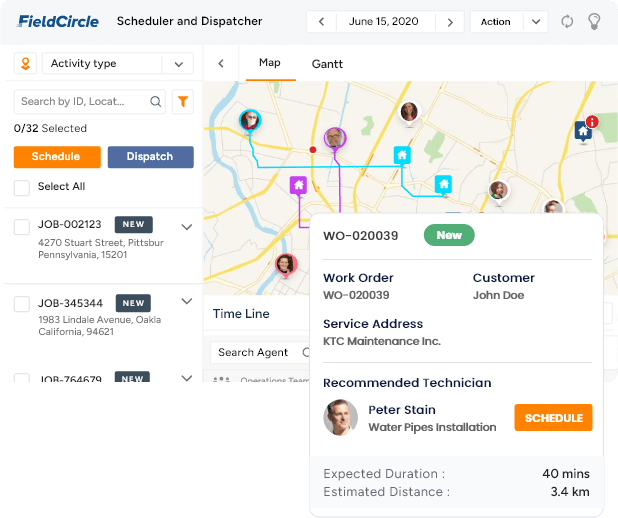
Effectively assign tasks based on technician skill sets, availability, and location, for optimal resource utilization and job allocation. With features for tracking technician schedules, monitoring job progress, and evaluating individual performance metrics at your disposal, you have a centralized technician and crew management framework.
Scheduling and Dispatch
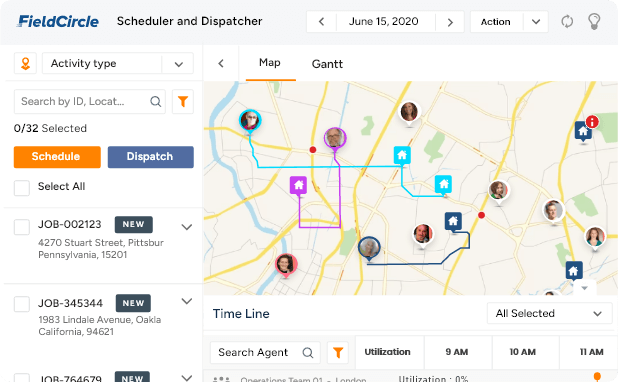
Offering real-time updates and intelligent route optimization, our equipment maintenance program works as a scheduling software, optimizing your scheduling and dispatch efforts. Streamlining coordination amongst stakeholders, it keeps your team at the right place at the right time.
Route Planning and Optimization
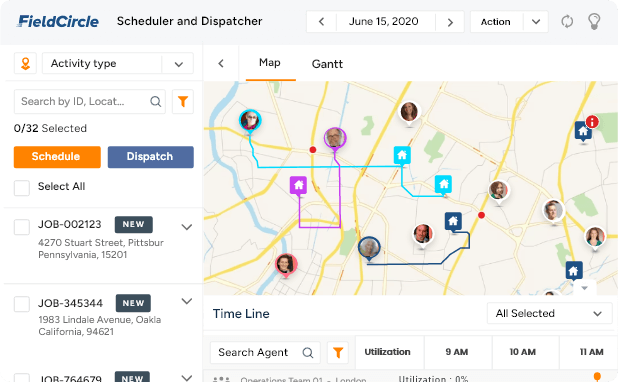
Leverage real-time data and intelligent algorithms to optimize technician routes based on factors such as service location, traffic conditions, and job priorities. The software provides interactive maps, route optimization algorithms, and scheduling tools that prove crucial for improving service response times and increasing job completion rates.
Work order management
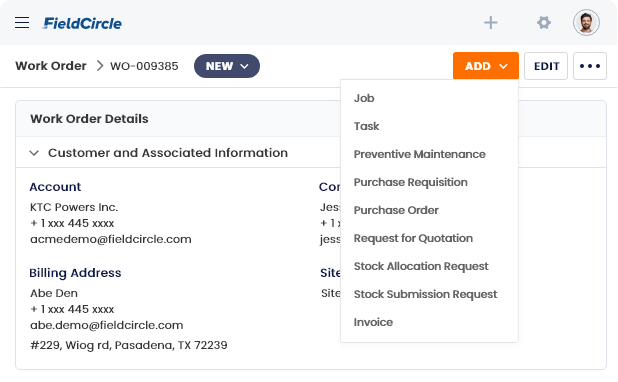
Streamline the entire word order management process from creation to closure, including real-time updates and status tracking. Our product provides tools for documenting work performed, capturing photos and signatures, and generating invoices that helps you achieve faster resolution times and improvement in service quality.
Preventive Maintenance and Inspection
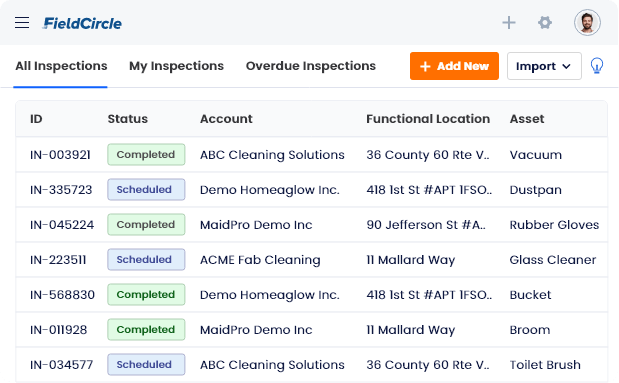
Allow users to define maintenance schedules, set up recurring maintenance tasks, and track maintenance history, ensuring timely service and reducing equipment downtime. Using our product leads to fewer emergency calls and extends equipment life, and brings massive improvement in operational efficiency.
Inspection Score and Failed Item Reports
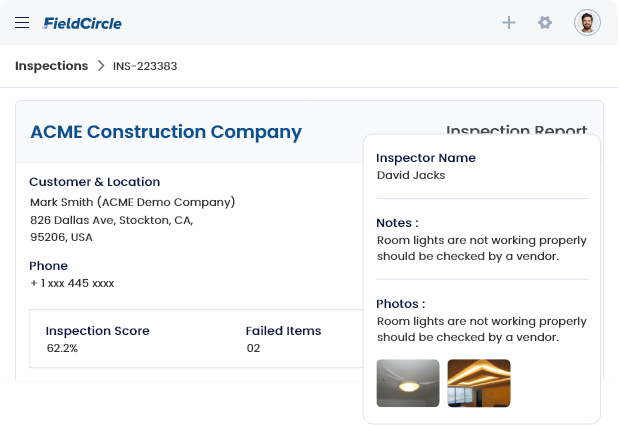
Enable technicians to capture inspection data, document any failed items or deficiencies, and generate inspection reports in real-time. Our product provides tools for analyzing inspection data, identifying trends, and making data-driven decisions, thereby maintaining high service quality standards, prioritizing corrective actions, and optimizing equipment performance.
Equipment and Assets Management
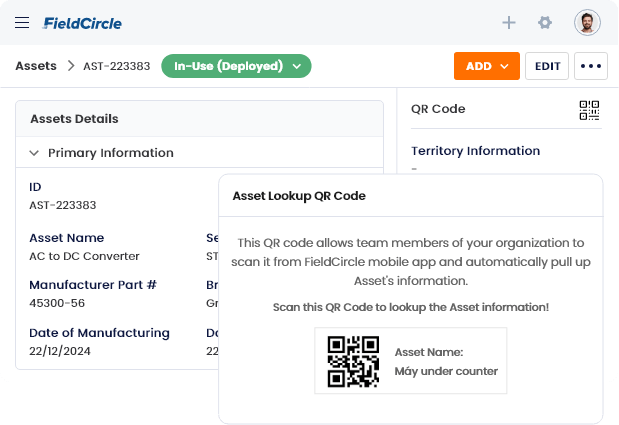
Seamlessly integrated with scheduling and inventory systems, our solution optimizes asset utilization. From acquisition to retirement, our system meticulously tracks each item’s lifecycle, offering real-time insights into usage patterns thereby paving the way for optimal equipment and assets performance.
Contract and Warranty Management
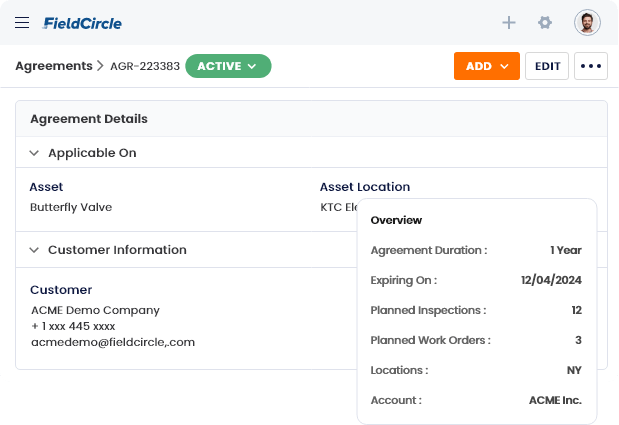
Have a centralized platform for tracking contract terms, renewal dates, and warranty information. With automated reminders and notifications, our tool offers timely action, and reduces the risk of missed renewals or expiration. It provides easy access to contract details and warranty coverage, and assists service teams to deliver prompt and accurate support.
Spare Parts and Inventory Management
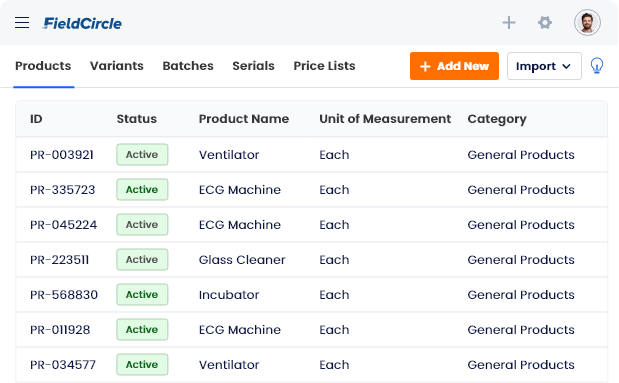
Benefit from real-time visibility, automated ordering, and efficient equipment tracking. Also, leverage forecasting tools, barcode scanning, and seamless vendor integration for streamlined processes, as you benefit from serialized inventory tracking and insightful historical inventory analysis.
Time-tracking and Timecards
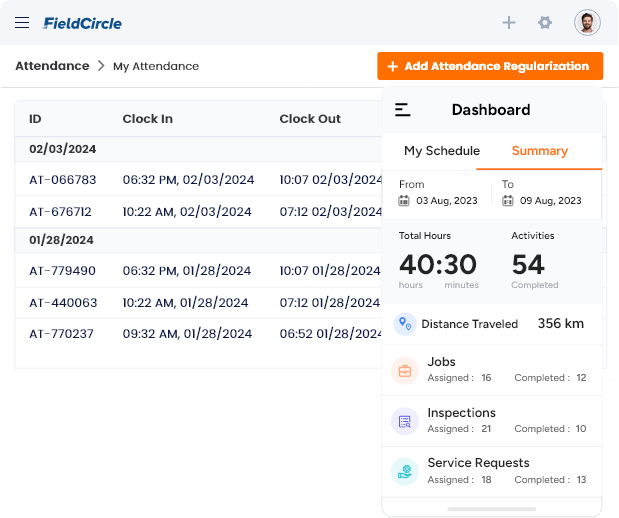
Excellently track technician timesheets and have accurate project and business data at your fingertips. With automated time tracking and detailed analytics that offer vital insights, our tool empowers you to improve individual productivity and promote transparency across entire equipment service operations.
Profitability Analysis and Invoice Management
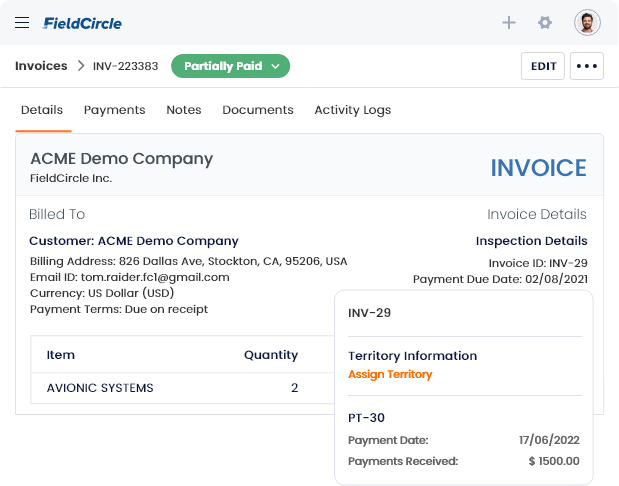
Convert your ordinary invoicing and payment processes into highly optimized financial processes with our comprehensive equipment maintenance software. Automate invoicing and integrate effortlessly with accounting software such as Quickbooks and multiple payment options. Benefit from expense tracking and robust reporting, ensuring accurate billing, and improved cash flow.
Customer Hub with Customer App
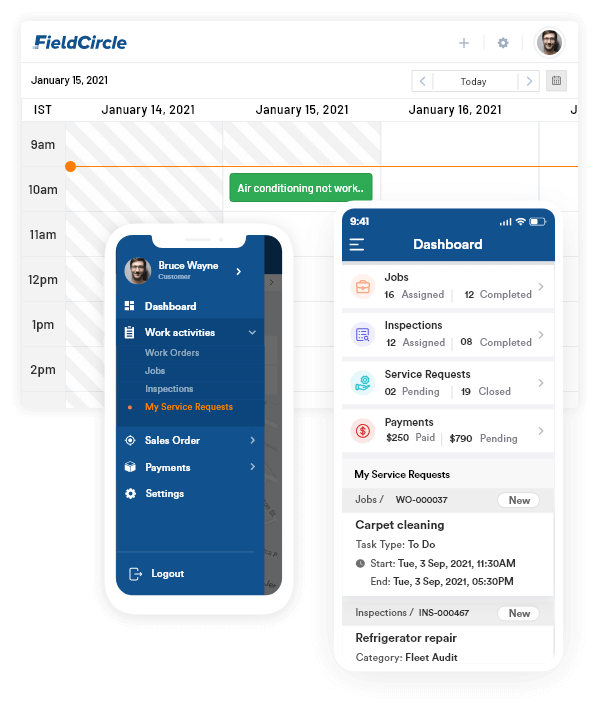
Create and modify checklist templates for various types of service tasks, inspections, and maintenance activities, while configuring workflow rules with ease. Our tool helps in standardization of checklist templates, and streamline tasks execution.
QR Code Labeling and Scanning
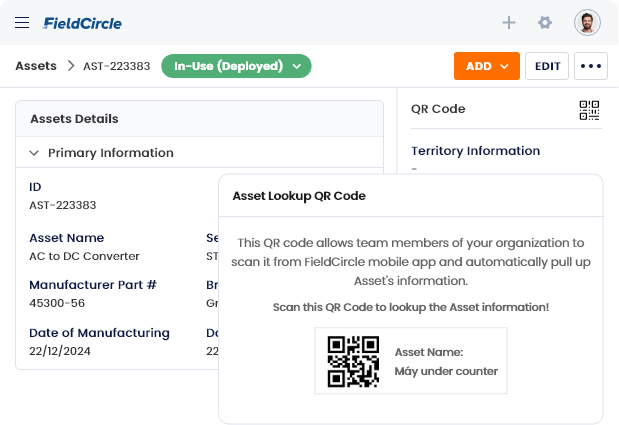
Assign unique QR codes to equipment, parts, and inventory items, and enable easy identification and tracking. Our product supports excellent QR code scanning using mobile devices, handheld scanners, and integrated barcode readers, assisting in better inventory tracking, eliminating data entry errors, and improving asset visibility.
Reports, Analytics and Dashboards
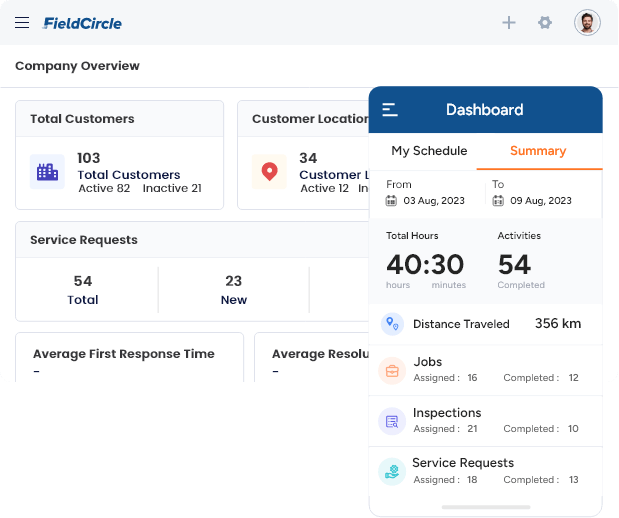
Generate custom reports, analyze key performance indicators (KPIs), and visualize data trends through interactive dashboards. With advanced analytics capabilities for predictive maintenance forecasting, resource optimization, and trend analysis, our tool lets you make informed decisions and drive continuous optimization.
Equipment Maintenance App – Manage Operations On-the-go
Drive operational effectiveness and achieve greater efficiency with our equipment maintenance app.
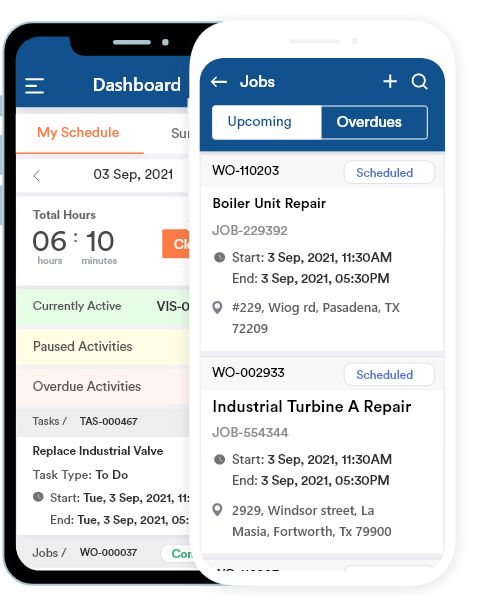
- Allow seamless data exchange between your field teams and back-office staff to keep them in sync
- Enable your field teams to track their schedule, job and customer details, and receive notifications on their mobile device
- Make equipment details such as service contracts, warranties, asset detail and historical service logs easily accessible for field teams to resolve issues faster
- Enable your teams to create, organize, and manage data throughout the service lifecycle to build company knowledge and use them effectively
Businesses Like Yours Are Seeing These Results with FieldCircle’s Equipment Maintenance Software
Why Choose Fieldcircle For Equipment Maintenance Software?
What Our Customers Think of Our Equipment Maintenance Program
FieldCircle has provided a positive experience by significantly improving our service and maintenance operations through its robust features and reliable performance.

FieldCircle has been transformative for our ops. We were already using technologies but FC has replaced most due to its comprehensiveness and awesome support team.

Success Stories Led by Our Equipment Maintenance Management Software
Discover the remarkable impact of FieldCircle’s equipment maintenance program as our customers share their success stories
and
feedback on how they have transformed their equipment maintenance and service operations. Following clients showcase why
FieldCircle’s is the amongst
best equipment maintenance software.

Cushman & Wakefield
Cushman & Wakefield, a global powerhouse in the commercial real estate services sector, enhances customer satisfaction, improves operational profitability, and achieves better vendor collaboration with FieldCircle.
Read the Story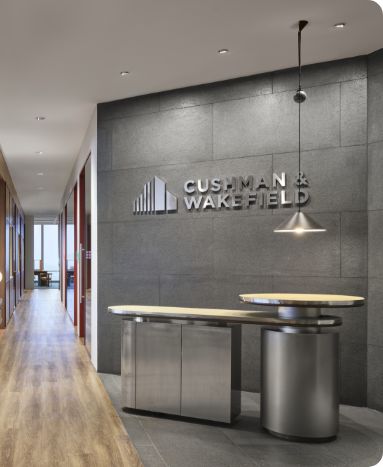

TSI Power
A leading US-based manufacturer, TSI Power Corporation, USA improves resource utilization, enhances productivity with FieldCircle implementation.
Read the Story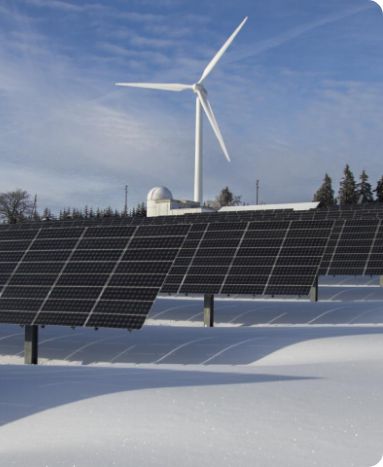

Yourspace
YourSpace partners with FieldCircle to achieve service operations excellence leading to higher profitability and customer experience.
Read the Story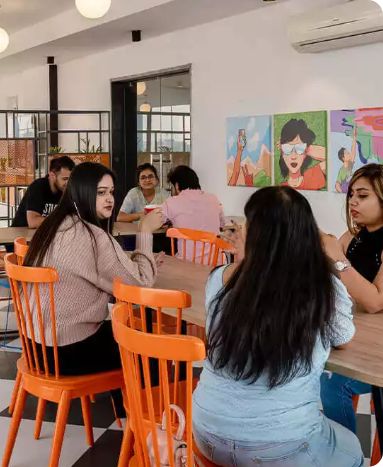

Nicco Engineering
Speciality maintenance service provider achieves more agile, transparent, and resilient service operations with FieldCircle.
Read the Story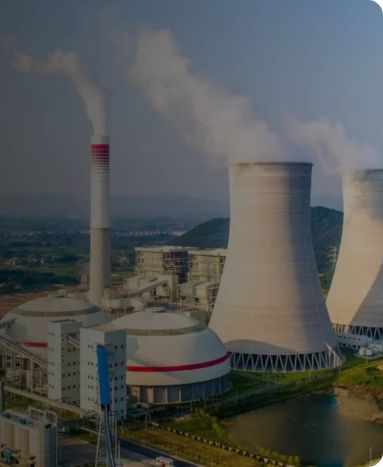
Book a Personalized Demo
Learn how your business can use FieldCircle’s equipment maintenance program to achieve more efficient,
transparent, and profitable service operations.
By submitting your details, you agree that we may contact you by call, email, and SMS and that you have read our terms of use and privacy policy.
Frequently Asked Questions (FAQs)
Quick answer to questions you may have.
What is FieldCircle’s Equipment Maintenance Software?
FieldCircle’s software can help you solve critical challenges around asset management and their service operations. It enables you to bring all your equipment information including location, spare parts, service history, associated contacts and work orders, and service manuals on a single platform. You could visualize the entire service journey from the first contact to the service delivery, track and monitor every aspect of service operations, and get actionable insight to make informed decisions.
Who uses equipment maintenance software?
Yes, our software includes a recurring work order feature that enables users to automate repetitive tasks like routine maintenance or inspections. The functionality saves time and ensures that important tasks are consistently performed without manual intervention, leading to improved service quality and customer satisfaction.
Can it track work orders and job status?
Absolutely, our equipment maintenance management software product seamlessly integrates and syncs with QuickBooks. By automatically syncing invoices, payments, and other financial data between the two platforms, the integration helps in efficient financial management, minimizes errors and saves time on manual data entry tasks.
Is our Equipment Maintenance software customizable to our workflow?
We deploy a dedicated support team that is available at your disposal 24/7. It provides timely assistance and resolves inquiries or issues promptly to ensure uninterrupted operations.
Is there real-time visibility into all maintenance activities?
Yes, FieldCircle’s equipment maintenance program offers integration capabilities with the help of APIs. These integration options allow seamless connectivity with third-party systems, such as CRM software or ERP systems, so that businesses can customize and extend the functionality of FieldCircle to meet their specific needs and integrate it into their existing workflows seamlessly.
Does the system track equipment condition or performance?
Our tool offers myriad benefits to businesses that adopt and implement it. It helps in scheduling and dispatching field technicians efficiently, reducing response times and increasing customer satisfaction. Additionally, it streamlines invoicing and payment processes, ensuring timely payments and improving cash flow. Moreover, the software provides real-time tracking of field activities, enabling better resource allocation and decision-making.