A Detailed Air Compressor Preventive Maintenance Checklist
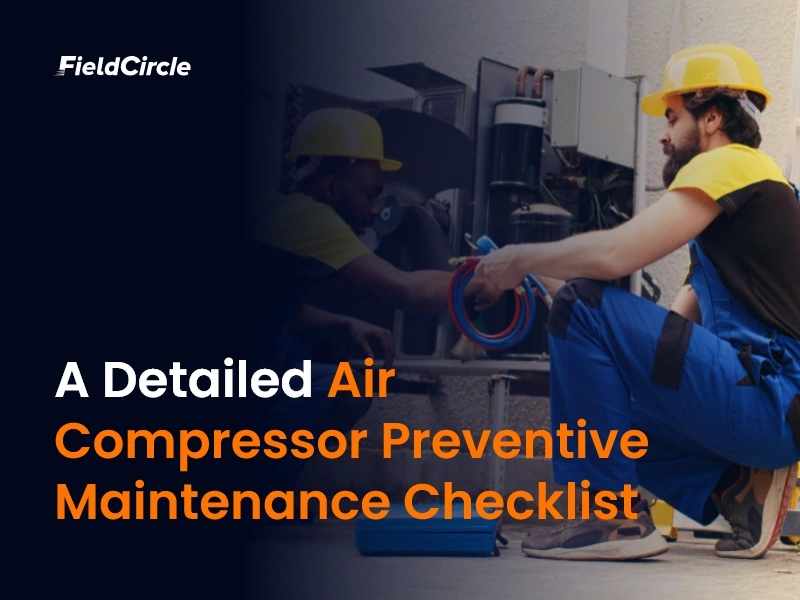
Air compressors are important in many industries. From powering machinery in manufacturing plants to supplying compressed air in automotive workshops, they are key to smooth operations. But when they break down unexpectedly, the impact can be significant—disrupted maintenance schedules, production halts which ultimately lead to costly repairs.
A solid preventive maintenance checklist helps keep these machines running without a hitch. By regularly inspecting key parts, you can catch minor issues and there are no shocks. We bring you a comprehensive checklist for various types of air compressors, including industrial air compressor, rotary vane air compressor and rotary screw air compressor.
What is an Air Compressor Preventive Maintenance Checklist?
An air compressor preventive maintenance checklist outlines the tasks needed to maintain the air compressor system. This includes checking and replacing filters, inspecting oil levels, belts, hoses, and connections, testing pressure, and cleaning components.
What are the Benefits of an Air Compressor Preventive Maintenance Checklist?
A preventive maintenance checklist streamlines the routine maintenance of air compressors and offers many benefits. Outlined below are the major benefits of using an air compressor preventive maintenance checklist:
- Consistency in Maintenance: A checklist ensures that each essential task is completed consistently, reducing the chance of missed steps and ensuring uniformity in preventive actions, thus streamlining maintenance scheduling.
- Simplified Troubleshooting: Having a checklist makes it easier to identify specific areas where issues may arise, allowing for quicker troubleshooting and resolution of minor problems before they escalate.
- Standardization Across Teams: Checklists help ensure that different team members or contractors perform the same set of maintenance tasks, leading to consistent performance and reliability regardless of who is handling the job.
- Better Air Quality: Regular maintenance ensures air filters and dryers are functioning correctly, preventing contaminants from entering the compressed air system. Dry, clean air protects sensitive machinery and tools downstream, which improves the quality of the final product.
- Stable and Predictable Energy Usage: When an air compressor is properly maintained, it runs more efficiently, consuming less energy. Consistent and regulated energy usage reduces strain on the power system, which automatically brings down energy costs.
Air Compressor Preventive Maintenance Checklist
Following are the essential 23 items that comprise a comprehensive maintenance checklist for an air compressor:
1. Visual & General Inspection
-
Check overall cleanliness of the compressor and surrounding area.
-
Inspect for any visible oil, air, or coolant leaks around the machine.
-
Look for physical damage, rust, or wear on components such as the compressor block, motor, valves, and piping.
-
Ensure all nameplates and warning labels are legible and in place.
-
Verify that safety guards and panels are secure and undamaged.
-
Inspect base frame, vibration isolators, and foundation bolts for stability and looseness.
-
Check that the machine is level and firmly mounted to prevent vibrations.
2. Air Intake System
-
Inspect the air filter element for dust, oil, or clogging — clean or replace if needed.
-
Check air intake housing and piping for cracks, holes, or signs of suction leaks.
-
Ensure intake ductwork (if installed) is free from obstructions and securely mounted.
-
Examine silencers or pre-filters for dirt accumulation or restriction.
-
Ensure proper sealing between air intake and filter housing to avoid unfiltered air entry.
3. Compressor Element / Pump
-
Listen for abnormal operating sounds such as knocking, grinding, or squealing.
-
Check the compressor head for excessive heat during operation using an infrared thermometer.
-
Verify lubrication of rotating parts if accessible (without opening pressurized parts).
-
Inspect sight glass or external indicators for unusual oil foaming or bubbling.
-
Check for signs of oil carryover in the discharge lines or downstream equipment.
-
Check piston, vane, or screw element alignment and wear (depending on compressor type).
4. Lubrication System
-
Inspect oil level through dipstick or sight glass — refill with correct grade if low.
-
Examine oil for discoloration (dark, milky), foul smell, or particulates.
-
Drain a small oil sample and test for water or sludge presence.
-
Check oil fill cap, drain plug, and breather for cleanliness and secure fit.
-
Inspect oil lines, joints, and seals for leakage or sweating.
-
Replace oil filter if clogged, bypassing, or overdue.
-
Replace oil entirely based on runtime hours or oil analysis results.
5. Cooling System
-
Check that cooling fans rotate freely and without obstruction.
-
Inspect fan motor condition and confirm automatic start/stop operation.
-
Clean external cooling fins or radiator with compressed air or soft brush.
-
Inspect coolant or water flow through jackets or intercoolers (for water-cooled systems).
-
Check coolant quality — look for rust, scale, or contamination in the reservoir.
-
Ensure thermostatic valves, temperature gauges, and flow indicators are functional.
-
Inspect radiator for leaks, corrosion, or physical damage.
6. Drive System
-
Check V-belt tension using a belt tension gauge — adjust if out of spec.
-
Inspect belt surface for cracks, fraying, or glazing.
-
Confirm pulleys are aligned and not worn or loose.
-
For direct drives: inspect coupling alignment using dial gauge or laser tool.
-
Check flexible coupling for wear or misalignment.
-
Inspect shaft bearings and housing for abnormal noise or play.
-
Listen for high-pitched or scraping noises that may indicate drive misalignment.
7. Air-Oil Separator
-
Monitor pressure differential across separator element — replace if above OEM threshold.
-
Inspect separator tank for internal oil coating or emulsification.
-
Check the housing gasket for cracks, degradation, or improper seating.
-
Confirm that the drain pipe from the separator is free-flowing and unobstructed.
-
Examine vent line for clogging and verify correct routing back to inlet or sump.
- Tighten separator cover bolts uniformly to avoid air leaks.
8. Control System & Instrumentation
-
Inspect control panel for physical damage, dirt accumulation, or signs of overheating.
-
Check indicator lights, selector switches, buttons, and HMI displays for proper function.
-
Verify emergency stop button operation and reset functionality.
-
Inspect all wiring connections, terminals, and insulation for signs of wear or arcing.
-
Test safety interlocks (e.g. high temperature, low oil pressure) to confirm responsiveness.
-
Calibrate pressure switches, sensors, and transmitters to OEM-specified tolerances.
-
Confirm programmable logic controller (PLC) input/output modules function correctly.
-
Review settings in digital controllers for alarm thresholds, timings, and sequence logic.
-
Ensure that the automatic load/unload mechanism triggers as designed.
9. Electrical System
-
Check tightness of power terminals and control wiring in MCC or panel boards.
-
Inspect motor starter contacts for pitting, overheating, or carbon buildup.
-
Confirm that all protective relays (e.g., overload, under-voltage, phase failure) operate correctly.
-
Measure insulation resistance of motor windings using a megger tester.
-
Check motor current draw under load against nameplate FLA to identify overloading.
-
Inspect and clean cooling fans or ventilation grills of electrical panels and motor housings.
- Verify continuity of the grounding system and bonding of all components.
10. Discharge Piping & Check Valves
-
Inspect discharge pipework for scaling, vibration damage, or corrosion.
-
Check pipe clamps and hangers for tightness and proper load distribution.
-
Verify tightness of threaded, flanged, or welded joints.
-
Inspect and test check valves for proper seating, spring tension, and reverse leak.
-
Confirm that flex connectors or compensators are intact and not overstretched.
-
Look for signs of overheating or oil/carbon buildup at discharge outlets.
11. Moisture Separator & Drain System
-
Inspect and clean mechanical moisture separators or centrifugal separators.
-
Test automatic drain valves (timed or zero-loss) for correct operation and no clogging.
-
Check manual drain valves for ease of operation and no leakage.
-
Examine drain lines for kinks, back pressure, or improper slope.
-
Ensure that condensate is being collected and disposed of according to environmental norms.
-
Confirm that condensate treatment units (if installed) are operating correctly.
12. Air Receiver (Storage Tank)
-
Inspect external surfaces for corrosion, dents, or physical damage.
-
Check the tank drain valve (manual or automatic) for proper operation and draining efficiency.
-
Test pressure relief valve (PRV) — replace or recalibrate if it doesn’t activate at set pressure.
-
Inspect internal surface for rust, scale, or trapped condensate (during scheduled shutdown).
-
Confirm pressure gauge accuracy by cross-verifying with a calibrated handheld gauge.
-
Ensure that the tank is compliant with local safety regulations and has a current inspection certificate.
13. Safety Devices & Alarms
-
Verify operation of all pressure relief valves on the compressor, separator, and receiver.
-
Test high temperature shutdown switch for activation threshold and response.
-
Check low oil level and low oil pressure alarms for sensitivity and timing.
-
Inspect thermal overload protection on motors and confirm reset mechanisms work.
-
Confirm that audio-visual alarms on the HMI or control panel activate as per fault simulation.
-
Inspect safety interlock wiring and test their operation with system start/stop commands.
- Review alarm log history and maintenance alerts to identify recurring issues.
14. Pressure System & Relief Devices
-
Inspect pressure relief valves for visible rust, cracks, or tampering.
-
Test safety valves periodically for activation at designated pressure limits.
-
Confirm valve seals are intact and seat properly without continuous leakage.
-
Check manual pressure release valves for ease of operation and full discharge path.
-
Verify pressure gauges across all stages (inlet, inter-stage, discharge) are functional and accurate.
-
Calibrate pressure relief valves per manufacturer guidelines or as per statutory inspection requirements.
15. Vibration & Noise Monitoring
-
Measure vibration levels at key points (motor, pump housing, piping) using a vibration analyzer.
-
Record and trend vibration values to detect early signs of bearing failure or misalignment.
-
Check mounting bolts and isolators for wear or looseness that may cause excess vibration.
-
Listen for mechanical knocks, hissing, or pulsation sounds that deviate from normal operation.
-
Examine nearby piping and supports for resonance or vibration transmission.
16. Temperature Monitoring
-
Use an infrared thermometer to measure surface temperatures of the motor, compressor, and coolers.
-
Check that running temperatures are within OEM-specified limits.
-
Monitor and record ambient temperature in the compressor room; verify proper ventilation.
-
Inspect temperature sensors for proper connection and response to load changes.
-
Verify accuracy of displayed temperatures on control panel versus physical readings.
17. Pneumatic Control & Solenoid Valves
-
Inspect solenoid valves for proper wiring, coil integrity, and mechanical movement.
-
Test response time of control valves during load/unload operations.
-
Check for air leakage around valve seats, bodies, and fittings.
-
Confirm that pilot-operated valves respond to system pressure correctly.
-
Clean or replace internal filter screens if present.
18. Automatic Start/Stop & Load/Unload Function
-
Test auto-start and shutdown by simulating conditions like pressure drop or peak demand.
-
Verify load/unload sequence timing and pressure range as per system design.
-
Observing if the compressor stays in load too long or cycles excessively — may indicate control issues.
-
Inspect pneumatic or electronic actuators for correct switching.
-
Monitor system recovery time to assess air delivery health.
19. Unloader Mechanism
-
Inspect mechanical or solenoid unloader for movement and proper response during startup and shutdown.
-
Clean carbon deposits or sludge from moving parts and orifices.
-
Check O-rings, springs, and diaphragms for wear, tear, or brittleness.
-
Test unloader cycle time and noise level during actuation.
-
Verify that the unloader disengages during off-load or stop state.
20. Motor & Bearings
-
Inspect motor casing for dust accumulation and overheating signs.
-
Measure bearing temperature during operation using infrared or contact sensors.
-
Listening for bearing noise — humming, rattling, or grinding indicates early failure.
-
Measure shaft alignment between motor and compressor with precision tools.
21. System Leak Detection
-
Perform ultrasonic leak detection or soap bubble testing on all pressurized joints.
-
Check fittings, hoses, valves, and quick-connect couplings for air leakage.
-
Record estimated air loss and repair or replace faulty components.
-
Inspect control valves and piping in downstream air systems (tools, dryers, etc.).
-
Maintain a log of recurrent leak zones to address root causes.
22. Air Dryer (If Installed)
-
Verify dryer operation and dew point using monitoring systems or hygrometer.
-
Inspect pre- and post-filters for pressure drop and contamination.
-
Check refrigerant levels and temperature in refrigerated dryers.
-
Inspect desiccant beads in desiccant dryers for oil saturation or dusting.
- Clean or replace purge valves and confirm the regeneration cycle is functional.
23. Documentation & Record Keeping
-
Maintain a detailed logbook of all maintenance checks, replacements, and anomalies.
-
Record oil and filter change dates, vibration readings, and temperature trends.
-
Retain calibration certificates for gauges, valves, and sensors.
-
Keep track of total runtime hours, motor starts, and shutdowns.
- Review OEM manuals for updates on service intervals and critical alerts.
What are the Tips to Follow for Air Compressor Maintenance?
As a standard, you should regularly consult your compressor’s manual for specific maintenance intervals and manufacturer guidelines. Alongside, follow these preventative maintenance tips to prolong the life of your air compressor:
- Check Air Intake Filters Regularly
- Monitor Oil Levels and Quality
- Examine Belts and Pulleys
- Drain Moisture from the Air Receiver Tank
- Check for Leaks
- Inspect and Clean Heat Exchangers
- Lubricate Bearings and Moving Parts
- Check the Compressor’s Pressure Settings
- Test the Safety Relief Valve
- Inspect Electrical Components
- Ensure Proper Ventilation
- Inspect and Test Pressure Gauges
Inspect filters every 1000 of hours of operation or as recommended by the manufacturer. Clean or replace them when dirty to ensure proper airflow and efficiency.
Check the oil level regularly (at least once per shift if running continuously). Replace the oil as per the manufacturer’s recommendations and ensure the oil is free of contaminants (e.g., water, dust).
Inspect belts for wear, cracks, or misalignment. Replace any worn or damaged belts immediately and ensure the correct tension for optimal performance.
Drain the moisture from the air receiver tank regularly, typically once a day or as needed. Install automatic drain valves if possible to prevent moisture buildup without manual intervention.
Perform a leak test by listening for hissing sounds or using a soapy water solution to identify leaks. Tighten fittings and replace faulty seals promptly.
Clean air-cooled or water-cooled heat exchangers at regular intervals to ensure they are not obstructed by dirt or debris. A clean heat exchanger enhances cooling efficiency and prevents overheating.
Follow the manufacturer’s lubrication schedule for greasing bearings, connecting rods, and other moving parts. Use the recommended lubricants to avoid premature failure.
Regularly check the compressor’s cut-in and cut-out pressures to ensure they match the operating requirements of your application. Adjust as needed based on the specific needs of the equipment and system.
Test the safety relief valve periodically to ensure it opens at the proper pressure level. Replace it if it shows signs of malfunction.
Check all wiring, connectors, and electrical components for signs of wear or damage. Ensure connections are tight, clean, and corrosion-free. Test motor windings for resistance and verify that all electrical components are functioning correctly.
Keep the compressor room well-ventilated. Make sure there are no obstructions around the compressor that could restrict airflow. Use cooling fans or air conditioning systems if necessary to maintain an optimal temperature.
Periodically check the accuracy of the pressure gauges and replace them if they become inaccurate. Faulty gauges can lead to improper pressure settings, potentially damaging the system.
To Wrap Up
To keep your air compressor running efficiently, a well-structured air compressor maintenance checklist is key. It is a key part of the air compressor maintenance plan. Regularly checking and addressing the components that power your system—from oil levels and filters to belts and pressure settings—can extend its lifespan and improve performance. Proactively monitoring your air compressor is essential to make sure your operations stay smooth, cost-effective, and ready for the challenges ahead.