Total Productive Maintenance: What and Why for SMEs
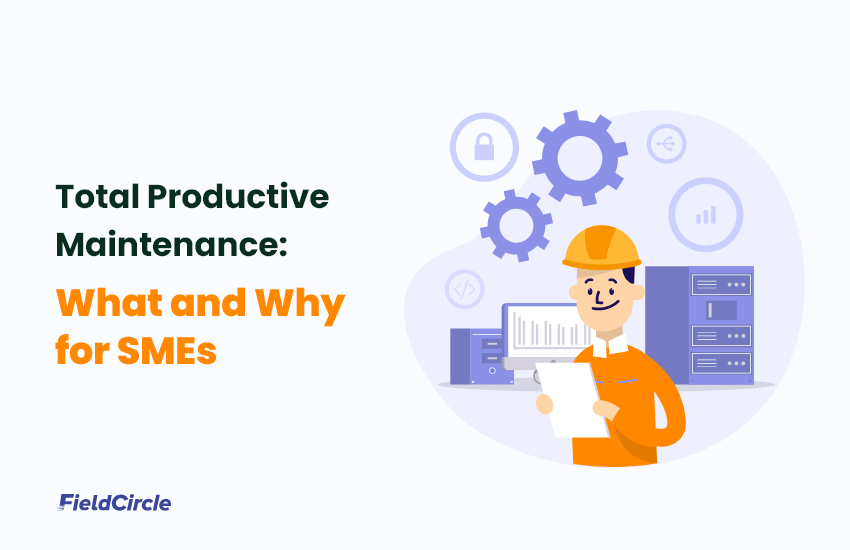
In their relentless pursuit of operational excellence, enterprises strive to maximize maintenance performance while minimizing the risks of failures. They arrive at Total Productive Maintenance (TPM) to achieve these objectives.
TPM can empower businesses to uphold their processes through enhanced equipment effectiveness and the integration of digital, data-driven solutions. Since its evolution, TPM has been a lynchpin in bettering maintenance efficiency for those who have adopted and implemented it.
We know how Toyota leveraged TPM to establish a reputation for operational excellence and efficiency. And more recently, giants like Procter & Gamble and Coca-Cola have showcased the value of TPM.
Stories and experiences of success realized through TPM abound today.
Going ahead, we shed light on this transformative maintenance philosophy and how it can generate value for small to medium enterprises (SMEs) across industries.
What is Total Productive Maintenance (TPM)?
Total Productive Maintenance (TPM) is often seen as a concept the seeds of which germinated in the Toyota Production System in Japan in 1970. It is a comprehensive approach to equipment maintenance that aims to maximize the efficiency and effectiveness of production machinery.
TPM goes beyond traditional maintenance practices and suggests that not only maintenance professionals but everyone in the organization must participate in maintenance. Through this “All-inclusive” and “Out-of-the-box” philosophy, it emphasizes and enables proactive and preventive measures to eliminate breakdowns, defects, and accidents.
The key components and principles on which Total Productive Maintenance (TPM) is based are:
1. Overall Equipment Effectiveness (OEE)
OEE is a key performance indicator in TPM and is used to measure the overall efficiency of a production system. It rests on:
- Availability: The percentage of time that equipment is available for production.
- Performance: The rate at which equipment operates as compared to its designed speed.
- Quality: The percentage of good-quality products produced by the equipment.
– 5S Principles:
- Sort: Organize and eliminate unnecessary items from the workplace.
- Set in order: Arrange necessary items logically and efficiently.
- Shine: Keep the workplace clean and well-maintained.
- Standardize: Establish and maintain standards for workplace organization and cleanliness.
- Sustain: Ensure that the 5S principles are continuously followed and improved.
2. Kaizen (Continuous Improvement)
TPM promotes a culture of continuous improvement where small incremental changes are made by employees at all levels to enhance efficiency and eliminate waste.
3. Equipment Life Cycle Management
TPM considers the entire life cycle of equipment, from design and procurement to operation and disposal. It proposes that by addressing maintenance needs at each stage, organizations can improve the overall reliability and efficiency of the equipment.
4. Visual Management
Visual tools and indicators are used to make information easily accessible to all employees. From displaying equipment status, maintenance schedules, and performance metrics, the visual tools encompass all metrics and information that is important for managing maintenance operations.
5. Zero Breakdowns, Defects, and Accidents
TPM lays stress on achieving zero breakdowns, defects, and accidents through proactive measures for addressing issues and continuously improving processes.
What are the pillars of Total Productive Maintenance (TPM)?
TPM is built on eight pillars, and each plays an equally vital role in fostering a culture of continuous improvement. We see what these pillars are and how they make TPM a transformative strategy.
1. Autonomous Maintenance (Jishu Hozen):
Autonomous Maintenance places the onus on operators to actively engage in the care of equipment. By integrating routine maintenance tasks into daily operations, operators become the first line of defense against equipment deterioration.
For maintaining a packaging line in a food processing plant, operators, through autonomous maintenance, regularly inspect machines for wear, clean accumulated debris, and ensure proper lubrication. Apart from preventing sudden breakdowns, it also fosters a sense of ownership among operators, leading to increased attentiveness to equipment conditions.
2. Planned Maintenance (Keikaku Hozen):
Here operators systematically schedule and execute maintenance activities to prevent unplanned downtime. In a manufacturing facility, as per this principle, you will schedule preventive maintenance regularly to replace worn parts.
For instance, a CNC machine might undergo routine checks for calibration, lubrication, and belt tension. Predictive maintenance, using tools like vibration analysis, allows organizations to anticipate failures and plan interventions proactively. Such scheduled overhauls will ensure that comprehensive maintenance is conducted at planned intervals, and disruptions to production schedules are minimized.
3. Focused Improvement (Kobetsu Kaizen):
Focused Improvement is the engine driving the continuous enhancement of operational processes. Imagine an automotive assembly line facing recurrent delays at a particular workstation. Through a Kaizen event, a cross-functional team, including operators, engineers, and managers, collaborates to identify root causes.
The use of tools like root cause analysis is central to this principle, which lets stakeholders understand inefficiencies and optimize processes for streamlined workflows. The outcome is an agile and responsive production system that continually evolves to meet or exceed performance expectations.
4. Early Equipment Management (EEM):
Early Equipment Management emphasizes integrating maintenance considerations during the design and installation of new equipment. So, let’s say, in a scenario where a pharmaceutical company is installing a new blending machine, failure mode and effect analysis (FMEA) is employed to anticipate potential issues.
Now, design for reliability principles will make your equipment not only efficient but also easy to maintain. Installation quality checks further validate that the equipment is installed correctly, which will make your equipment lifecycle reliable.
5. Quality Maintenance (Hinshitsu Hozen):
It prevents defects and ensures consistent product quality through concepts such as Six Sigma. So, if you are managing a chemical manufacturing plant, you know how critical it is to maintain precise temperature and pressure.
Quality Maintenance involves using statistical process control (SPC) to monitor and control such variables, along with implementing error-proofing mechanisms such as sensors and alarms. Again, this is a proactive approach that will maintain process and product quality, as it will massively reduce the likelihood of defects.
6. Safety, Health, and Environment (SHE):
Critical to any maintenance operations is the Safety, Health, and Environment (SHE) principle as it calls for a workplace that prioritizes employee well-being and minimizes environmental impact.
In maintenance, rigorous risk assessments are conducted to identify and mitigate potential hazards. As per this principle, comprehensive training programs must be carried out to make employees well-versed in safety protocols and make the supervision staff accountable for adhering to compliances. A robust SHE strategy not only safeguards personnel but also contributes to a positive organizational image.
7. Education and Training (Kyoiku):
Education and Training form the bedrock of a skilled and adaptable workforce. In an enterprise, operators undergo continuous training on the operation and maintenance of diverse machines.
Here, a skills matrix acts as a ready-to-use tool to identify and address skill gaps, while cross-training ensures that employees can seamlessly transition between different tasks. Through this principle, TPM equips employees with the knowledge and skills needed to navigate evolving technologies and challenges.
8. Administrative and Office TPM (Shitsuke):
This principle of TPM extends to non-production areas, recognizing the integral role of support functions. It stresses that the standardization of processes in an office setting establishes efficient workflows, akin to the standardized procedures implemented on the shop floor.
Even for administrative functions, visual management tools, such as Kanban boards, provide a transparent view of tasks. Through continuous improvement in administrative processes, the principles of TPM permeate every facet of the organization, which completes your aim to achieve holistic operational excellence.
What transformation does Total Productive Maintenance (TPM) bring?
The effect of TPM can be witnessed across several areas, and there are countless benefits that an organization implementing it will experience. Enlisted below are some ways it will bring improvement in your maintenance operations.
- Less Unplanned Maintenance and Equipment Downtime:
Through proactive and preventative maintenance, as TPM keeps the equipment in a well-maintained state, it automatically reduces the need for unplanned maintenance and reduces downtime.
- Lower Costs:
By optimizing equipment availability and performance, TPM can lead to a significant reduction in maintenance and conversion costs over time.
- Safer Work Environments:
TPM empowers employees to take ownership of equipment, and makes them accountable for adhering to industry-specific regulations, which potentially mitigates the risk of injuries.
- Improved Efficiency and Overall Staff Morale:
TPM’s focus on continuous improvement and employee empowerment leads to improvement in efficiency and encouragement amongst all employees, who actively participate in maintenance management.
- Improvement in Quality and Customer Satisfaction:
TPM’s quality maintenance pillar integrates quality improvements in business processes, which can deliver better services to customers, who, as a result, develop a positive impression of the businesses.
- Cultural Transformation: TPM brings a cultural shift within the organization, due to its emphasis on continuous improvement, collaboration, and empowerment. As contributing to improvement in processes is a part of every team member’s role, it automatically keeps adding value to processes.
- Frequent Continuous Improvement Events:
TPM often involves the organization of continuous improvement events, where cross-functional teams come together to address specific challenges or opportunities for improvement. These events, often known as Kaizen events, are focused on achieving tangible results within a short timeframe.
- Accurate identification of Root Causes:
When equipment issues do occur, TPM emphasizes the importance of conducting a thorough root cause analysis. Stakeholders are committed to the philosophy to investigate underlying factors and implement corrective actions to prevent recurrence.
How can total productive maintenance be used across different industries?
In each industry, maintenance brings its own set of technicalities and challenges. We look at how Total Productive Maintenance (TPM) applies across various industries, against this backdrop:
1. Manufacturing
- Automotive Manufacturing: TPM focuses on reducing downtime for critical machinery such as robotic arms in assembly lines. Predictive maintenance using sensors and IoT devices can be integrated to anticipate issues and plan maintenance during scheduled downtimes.
- Pharmaceutical Manufacturing: TPM assures the reliability and cleanliness of production equipment in pharmaceutical manufacturing. Clean-in-place (CIP) and sterilize-in-place (SIP) processes need to be well-maintained to meet strict hygiene and quality standards.
2. Food and Beverage
- Breweries: TPM can be applied to the maintenance of brewing equipment, including fermentation tanks and bottling lines. Preventive maintenance software will avoid contamination and ensure the consistency of the brewing process.
- Dairy Processing: In dairy processing plants, TPM can focus on maintaining pasteurization equipment, and make it operates at optimal temperatures to meet safety regulations.
3. Energy
- Power Plants: TPM can play a vital role in power generation by optimizing the performance of turbines, generators, and other critical equipment. In nuclear power plants, where safety is paramount, TPM can contribute to ensuring the reliability of safety systems.
- Renewable Energy: In wind or solar farms, TPM can be used to maintain and monitor the performance of turbines or solar panels. Remote monitoring systems can be integrated to collect data for predictive maintenance.
4. Chemical
- Chemical Processing: In chemical plants, TPM can maintain the integrity of vessels, reactors, and piping systems. Proactive maintenance strategies can prevent leaks or failures that may result in hazardous situations.
- Specialty Chemicals: Industries producing specialty chemicals have unique equipment. TPM can be tailored to address specific challenges in maintaining specialized reactors, distillation columns, and mixing equipment.
5. Aerospace
- Aircraft Manufacturing: TPM is critical in aerospace for maintaining precision machinery used in the manufacturing of aircraft components. In particular, CNC machines and robotic systems must undergo routine maintenance to ensure accuracy and reliability.
- Airport Operations: TPM can be applied to airport ground equipment, such as baggage handling systems and aircraft de-icing equipment, to minimize delays and ensure efficient operations.
6. Healthcare Industry:
- Medical Device Manufacturing: TPM is essential in maintaining the reliability and cleanliness of machinery used in the production of medical devices. Strict adherence to regulatory standards requires a robust maintenance program.
- Hospitals: TPM principles can be applied to medical equipment maintenance so that diagnostic and treatment devices are consistently available and meet stringent quality and safety standards.
Conclusion
TPM is not just a maintenance strategy but a transformative philosophy integral to organizational excellence. Its significance extends beyond machinery and applies to every single process within an enterprise.
Aligning TPM with the foundational elements of digitized Standard Operating Procedures (SOPs) and remote expert guidance can usher in a new era for businesses. With this amalgamation, operators can use contextual information, to guide themselves towards achieving the highest efficiency in the process.
Adopting a (computerized maintenance management system) CMMS software can be one great step towards realizing TPM potential. Integrating the tool into your TPM plan will permeate it across all the pillars and help you derive value through TPM implementation.