Role of Augmented Reality in Maintenance: Gauging the Future Impact
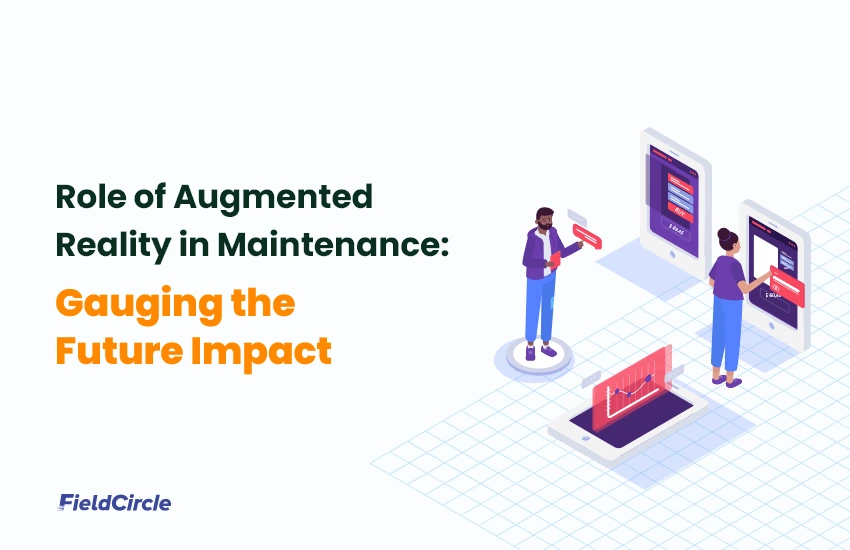
Most enterprises grapple with longstanding issues in maintenance, exacerbated by today’s uncertainties, including physical distancing and travel restrictions. These challenges have forced organizations to rethink on-site staff deployment, mull skeleton crews, and embrace remote collaboration.
Obviously, amidst the dire need to explore every single channel for ROI enhancement, the imperative to cut costs and address skills gaps has been a driving force behind these trends.
The pressure to maintain quality maintenance persists, given that up to 40 percent of abnormal situation losses are caused by human factors such as insufficient knowledge and maintenance mistakes.
With the introduction of smart glasses like Google Glass and Microsoft’s HoloLens, the 2010s witnessed a shift towards enterprise adoption of augmented reality (AR). Some early uses of AR in maintenance can be traced to this period. The developments allowed hands-free AR experiences, particularly beneficial in maintenance scenarios. The release of ARKit and ARCore by Apple and Google in 2015 took AR capabilities to the next level, by making them accessible on mobile devices.
In traditional maintenance approaches there was a room for accommodating inefficiencies, either through run-to-failure strategies or periodic maintenance schedules. However, with the advancement in technology, and especially with AR, stakeholders aren’t willing to sacrifice the quality of maintenance.
Augmented by the Industrial Internet of Things (IIoT), AR provides maintenance workers with powerful insights, enhancing situational awareness and directing them to problem sources swiftly. Beyond this, it carries the potential to transform maintenance schedules into genuinely condition-based programs. The use of connected devices is vital here. They detect early signs of impending issues and optimize work assignments to eliminate unnecessary tasks.
There are many ways augmented reality (AR) is shaping and will shape the maintenance sphere. The current adoptions in the maintenance industry are just planting the seeds, as the transformation AR will bring will be quite significant.
Augmented Reality in Maintenance: A Precursor
The research paper, Augmented Reality in Maintenance—History and Perspectives talks about the AR’s various types. They will guide maintenance professionals to go for area-specific AR implementation.
- Marker-based AR: Relies on visual markers like QR codes as reference points for virtual objects. When the system recognizes these markers, virtual content is superimposed on the real view through a camera.
- Markerless AR: Doesn’t require specific markers. It employs computer vision techniques like localization or object recognition to detect the user’s environment and place virtual objects in their view.
- Location-based AR: Gathers real-time information using GPS or other location systems to overlay AR content based on the user’s geographic position.
- Projection-based AR: Applies virtual content to real-world objects via projectors or projector-equipped glasses, eliminating the need for screens.
- Recognition-based AR: Recognizes real-world objects or images and overlays relevant information or virtual content onto them.
- Outlining-based AR: Uses image recognition to understand the environment, allowing users to create contours or shapes and highlight real-world components with special cameras.
- Motion tracking: This type of AR enables systems to follow the user’s movements, adjusting the position and/or orientation of virtual objects for a more interactive and immersive experience.
- Simulated Physics and Interactions: Involve virtual objects interacting with the real-world environment or each other, enhancing the realism of AR experiences.
AR in Maintenance Management: How the adoption will boost the yield
AR has been instrumental in bringing changes in areas that businesses have tapped for its implementation. Prompted by the positive experiences, maintenance professionals are building plans to use augmented reality in maintenance. Let’s understand how the change for betterment has been unfolding.
Predictive Maintenance through AI and AR Integration
Maintenance professionals have already understood the need for transferring from preventive maintenance to predictive maintenance. AR is turning out to be a keystone in this transformation.
By leveraging historical data and real-time sensor information, AR overlays predictions of potential equipment failures onto a technician’s view. Technicians can proactively intervene, reducing downtime and preventing costly breakdowns before they escalate into bigger problems.
For example, a technician wearing AR glasses can see maintenance alerts, generated by AI, highlighting components at risk of failure. In the near years, maintenance teams will rely heavily on AR to empower themselves with such capabilities.
Smart Documentation and Equipment History Visualization
Documentation is central to any maintenance operations. Maintenance teams cannot move even a step forward if they are not thorough with the documentation. Before involving themselves in maintenance tasks they must go through manuals and guides so that they find themselves on the right tracks during the operations.
With AR, rather than relying on static manuals, technicians can access live, interactive documentation linked to specific equipment components. Dynamic, context-aware information overlays offered by AR glasses can display a maintenance history timeline focusing on a particular machine part, detailing past repairs, replacements, and performance metrics.
Technicians have comprehensive, up-to-date information at their fingertips, that will enable them to be quick at initiating important decisions. AR will thus contribute to a more efficient and informed approach to equipment maintenance in the long run.
Immersive Virtual Collaboration for Complex Repairs
Maintenance technicians work with diverse teams, including procurement, finance, etc, based on the nature of the business. At a time when stakeholders are keen on streamlining this process and eliminate all impediments to smooth coordination, AR stands as the promise.
Technicians can use AR devices to share a real-time view of their workspace with remote experts. In cases where the nature of maintenance is intricate and involves multiple challenges, AR can significantly benefit to collaborate.
While guiding the repair process, AR will annotate the technician’s field of view, and even virtually manipulate components. A field technician working on a specialized piece of machinery can receive guidance from an expert located continents away.
Enhancing Asset Lifecycle Management
AR will extend its influence to the entire asset lifecycle, providing a holistic approach to maintenance operations. By integrating with Asset Lifecycle Management (ALM) systems, AR will offer a visual representation of an asset’s journey from procurement to retirement.
So, your maintenance team will be able to use AR to visualize equipment installation dates, track component replacements, and plan for upgrades. Such a comprehensive view will be beneficial for optimal asset utilization. Overall, by adopting AR you can transform maintenance into a strategic asset management function.
AR’s integration into asset lifecycle management provides a visual roadmap of an asset’s journey from installation to retirement. By visualizing past maintenance activities, replacements, and upgrades, technicians will be more accurate in taking appropriate actions. They will perform maintenance, upgrade components, as well as retire assets, optimizing the entire asset lifecycle for maximum efficiency and cost-effectiveness.
Training Simulations with Haptic Feedback
Simulation is a much-used term in the enterprise world. In practice, it’s a coveted exercise as it offers insights into aimed implementation. In maintenance, simulations are key to predictive maintenance. By simulating equipment functioning against various conditions, maintenance teams can define the course of maintenance.
Future AR applications will incorporate haptic feedback technology to enhance training simulations for maintenance personnel. By receiving haptic feedback technicians will develop muscle memory and fine-tune their skills in a risk-free virtual environment. Soon, they will find themselves engaging in realistic, hands-on simulations using AR devices that provide tactile sensations.
Your technicians wearing AR gloves will sense resistance or vibrations mimicking real-world conditions during a simulated maintenance task. As simulations will train them to gauge the impact of vibrations, they will initiate the actions well in time and prevent occurrence of possible issues.
Transforming Inventory Management
Inventory in the context of maintenance has a different connotation – not referring to the inventory of raw materials or processed goods as we commonly imagine for ‘inventory’. Every maintenance process is dependent on implements and parts of equipment that replace the worn-out/malfunctioning parts. These comprise the inventory in maintenance.
Sustaining sufficient levels in these inventories is critical for maintenance operations. In the event of inventory dipping beyond thresholds, maintenance can be adversely affected, coming to a halt for a dumb reason.
AR transforms inventory management by offering instant, on-the-go access to critical information. Technicians can effortlessly view current inventory levels, order status, and part specifications through AR overlays. Detailed insights significantly reduce downtime by ensuring the availability of necessary spare parts when and where they are needed.
How AR shaped up Maintenance: Using experiences as inspiration
The journey of AR adoption in maintenance is underway, as the stories of some recognized organizations highlight. So, those thinking about the prospects of AR can take inspiration from these stories and craft implementation plans for targeted areas.
ARMAR project expands AR’s horizon in Maintenance
A study by Henderson and Feiner highlighted the ARMAR (Augmented Reality for Maintenance and Repair) project, an AR system for training maintenance interventions. This can be considered as one important early experimentation of AR in maintenance.
It was a system implemented to monitor the user’s head movements, enabling the identification of target components through various augmented reality (AR) output techniques. The aim was to assess the duration spent on each method.
The study was noteworthy for its examination of the Graphical User Interface (GUI) functionality and the performance assessment of gesture recognition. It highlighted some significant benefits of AR such as reduction in head and eye movement, less need of context switching, and optimized repair sequences.
Since then, enterprises across sectors, such as manufacturing, healthcare, and logistics, have adopted AR for maintenance purposes. The use of AR in maintenance has become more widespread as the technology has matured.
Boeing writes a new chapter
Boeing implemented augmented reality technology for aircraft maintenance, particularly with the introduction of its Skylight platform. Skylight is an AR system designed to assist technicians in performing complex tasks by overlaying digital information onto the physical environment. Boeing began testing Skylight in the early 2010s and gradually expanded its use in aircraft maintenance.
The AR program imparted crucial skills in object identification and complex repair processes. Participants engage in activities such as identifying fault sources and receiving step-by-step instructions for repairs, practicing complex repair procedures, and overlaying detailed 3D diagrams of diverse automotive components.
This innovative training approach enables learners to access vital, just-in-time information concerning various automotive objects and procedures. It notably expedited automotive workshop processes, offering a more efficient and effective means of skill acquisition.
BMW stands out in the Automobile sector
World’s leading automobile manufacturer, BMW leverages AR techniques supporting complex maintenance tasks, using markerless CAD-based models and a virtual camera with a 90-degree field of view. The AR system is tested with different hardware setups. It has proven effective in diverse maintenance and repair scenarios, demonstrating its practical utility in the automotive industry.
Bosch sets the course in Industrial Maintenance
Bosch has incorporated augmented reality (AR) technology into its automotive workshops, aiming to enhance the efficiency of service repair tasks. The implementation involves a specialized AR training activity designed for workshop technicians, utilizing tablets and Microsoft HoloLens 2 glasses.
The AR activity offers learners visual guidance through features such as 3D diagrams, on-screen text, and charts, aiding in the identification of objects. Moreover, technicians can access step-by-step instructions tailored to various car models. The HoloLens 2 headsets make it simple for technicians to interact seamlessly with digital objects, further enriching the learning experience.
The AR initiative has paid off by significantly reducing the time required for technicians to complete tasks, concurrently minimizing errors made by technicians by an impressive 15%.
What do studies indicate for future AR adoptions?
Augmented Reality (AR) is proving to revolutionize electrical equipment maintenance. Research conducted by Zhukovskiy and Koteleva reveals that the integration of AR modules significantly reduces maintenance expenses by incorporating scripted tasks, minimizing errors, and improving the overall quality of interventions.
Another investigation utilizes Vuforia, a program for 3D object recognition within an AR system, resulting in cost savings through decreased travel time and heightened technician safety.
Peng et al. in their study on the power sector, used AR to optimize operations and effectively train substation power grid personnel. Enedis, a French electricity company, employs AR applications for low voltage control panels, providing advantages such as reduced intervention time and better operator safety.
How will the application of AR benefit maintenance operations?
Those implementing AR have been witnessing substantial improvements in maintenance. In the long-run, they can find themselves getting benefitted in myriad ways. These include.
- Deep Focus on Machine Faults
Augmented reality enhances maintenance by providing insights into machine faults, minimizing downtime and improving efficiency. - Detailed 3D Preview of Machines in Motion
You will have immersive 3D previews for better understanding, training, troubleshooting, and optimizing equipment performance. - Greater Accuracy and Efficiency
AR provides precise instructions, reducing errors and improving accuracy in tasks such as assembly, repairs, and maintenance, thus bringing down the mean time to repair (MTTR) - Transparency in Equipment Audits and Surveys
AR overlays real-time data onto physical equipment, streamlining audits, fostering better decision-making, and ensuring compliance. - Performance Modeling and Simulation of Equipment
You will be equipped with virtual models for in-depth analysis, scenario testing, and optimization of maintenance procedures. - Supporting Equipment Risk Identification and Management
Identifying and managing risks by providing real-time data on equipment health and safety parameters will be possible with perfection. - Hands-Free Tech for Workplace Efficiency
You will have hands-free access to critical information, allowing technicians to focus on tasks at hand and enhance efficiency. - Simplified Entry in Workspaces
AR simplifies tasks by overlaying relevant information directly into technicians’ workspaces, reducing cognitive load. - Data at Your Fingertips for Real-Time Solutions
Process offering real-time access to operational data will undergo further refinement, improving response times and contributing to overall operational efficiency. - Swift Plant Maintenance with On-the-Spot Historical Data
With on-the-spot access to historical maintenance data at their fingertips, maintenance professionals will be able to initiate actions without any delay. - Bridging Gaps Among Technicians
AR will bridge knowledge gaps by providing interactive training materials, on-the-job guidance, and knowledge sharing. - Real-Time Training for Empowering Technician Skill Sets
Real-time maintenance training by overlaying instructions and simulations onto physical equipment to accelerate the learning curve will be a reality.
How can AR-CMMS be a comprehensive solution for your maintenance needs?
Augmented Reality (AR) systems integrated with Computerized Maintenance Management Systems (CMMS) can leap towards high efficiency levels.
Specifically designed for a 3D capability, an AR-CMMS system offers both preventive and predictive measures. Such AR solutions deliver maintenance guidance through text, spoken instructions, and dynamic 3D models or videos. By utilizing a marker to pinpoint the target, the system allows quick responses to unforeseen breakdowns, demonstrating its real-time effectiveness in resolving issues for operators.
Reach out to our experts to know how you can combine the power of AR with a CMMS.