Facility Condition Assessment Starter Guide: Benefits, Process, and Checklist
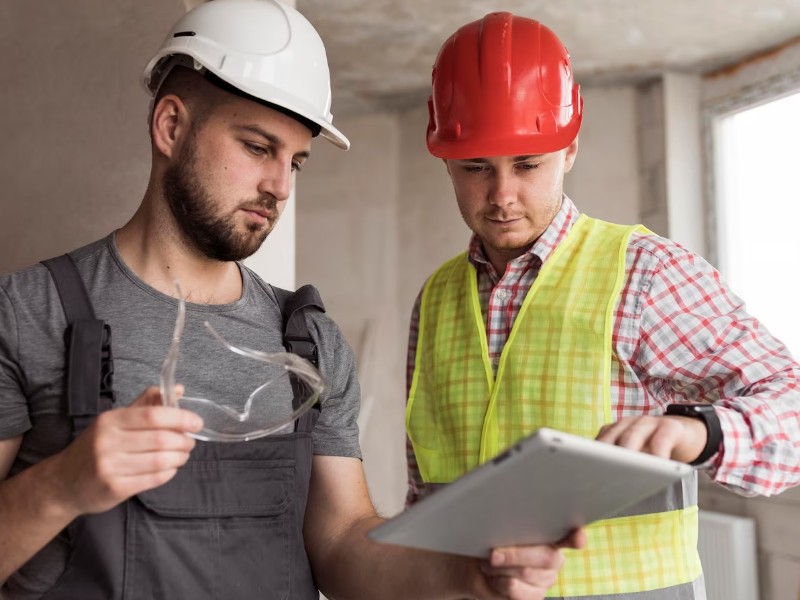
Facility conditions affect everyone inside them. As a facility manager with an eye on the future, understanding your facility’s health is crucial. Think of it as your facility’s medical record and chart rolled into one.
Imagine missing a weakening wall that could lead to disaster. By assessing facilities, you catch problems early and save lives. IBM research proves people spend 87% of their time indoors. So, evaluating conditions matters.
Our guide dives deep, addressing what Facility Condition Assessment (FCA) means, its significance, and how to perform one seamlessly. We even provide a practical template for a step-by-step journey. So, let’s get started on ensuring your facility’s future is as bright as its present.
Defining Facilities Condition Analysis
As you step into your facility every day, working tirelessly to keep everything running smoothly.
As you step into your facility every day, you embark on working tirelessly to keep everything running smoothly. But have you ever wondered about the hidden issues that might be lurking beneath the surface?
That’s where a facilities condition assessment comes into play. It’s not just about checking boxes; it’s a strategic approach that can save you time, money, and stress down the road.
So, what is facility condition assessment? Simply put, it’s a comprehensive evaluation of your facility’s physical condition. It goes beyond the surface and delves into the nitty-gritty details that might go unnoticed.
Why should you invest time and effort in an FCA? Well, let’s break it down. First off, it helps you predict future maintenance needs. Think about it: spotting that leaky roof or a worn-out HVAC system before they turn into major problems can save you from costly repairs. It’s like giving your facility a health check-up to catch ailments before they escalate.
But that’s not all. When you have a detailed facility condition assessment report in your hands, you hold the power to make informed decisions. It’s like having a plan for facility management that isn’t based on guesswork. Whether it’s setting budgets, prioritizing repairs, or planning for upgrades, the insights from an FCA are your secret weapon.
Why Do You Need FCA?
An FCA is like that mechanic’s inspection, but for your buildings. It reveals the current state of your facilities – from the roof down to the foundation. This isn’t just about appearances; it’s about ensuring your facilities are functional, safe, and compliant. Let’s dive into answering why do we need facility condition assessment? It will let you foresee maintenance needs and allocate resources smartly by:
-
Extending the Lifespan of Facilities
You know how proper self-care can add years to your life? Well, the same goes for your facilities. By identifying issues early through an FCA, you can address them before they snowball into major headaches.
For instance, a minor leak in the HVAC system might seem harmless, but if left unchecked, it can lead to mold growth and structural damage.
-
Cost-Effectiveness in Maintenance and Repairs
Think about your home – ignoring that dripping faucet often results in an inflated water bill. Similarly, delaying facility maintenance can inflate your budget. FCAs save you from this money pit by helping you prioritize repairs.
You get a clear picture of what’s urgent and what can wait. Fixing a cracked window is always a way cheaper than dealing with a full-blown insulation problem later.
-
Ensuring Safety and Compliance
Remember that creaky staircase you’ve been avoiding at home? Imagine that multiplied by the number of people in your facility. Yikes, right? FCAs are like your safety checklist. They spot potential hazards before they become accidents waiting to happen.
Not to mention, being non-compliant with regulations can result in hefty fines and reputation damage. An FCA ensures your facility aligns with all safety and accessibility requirements.
-
Enhancing Operational Efficiency
Ever tried cooking in a kitchen with a malfunctioning stove? It’s frustrating and slows you down. Facilities in disrepair work the same way – they hinder your operations.
An FCA gives you insights into your facility’s efficiency bottlenecks. Maybe your outdated lighting system is draining energy, or that ancient plumbing system is causing unnecessary water wastage. By fixing these, you not only save resources but also make daily operations smoother.
Key Components of FCA
As a facility manager, you know that maintaining a facility is akin to maintaining your car—it requires regular check-ups to ensure optimal performance and longevity. Just as you wouldn’t skip your car’s oil change, you can’t afford to overlook your facility’s condition assessment.
FCA guides your maintenance strategy and financial planning. So, let’s embark on a journey through the key components of facility condition assessments and explore why it’s the backbone of effective facility management.
-
Physical Site Inspection
Consider this: you’re inspecting an aging office building. Cracks in the walls catch your eye—similar to how a doctor notices fine lines on a patient’s face. This is where your structural integrity evaluation comes into play. You assess the foundation, walls, and roof, understanding that these building blocks hold everything together. Just like your body needs a strong skeleton, your facility requires a solid structure to thrive.
Now, let’s delve into systems and utilities inspection. Think about a hospital without functional HVAC systems. Patients and staff would suffer like you would in a sweltering room without air conditioning. Examining heating, ventilation, plumbing, and electrical systems ensures your facility breathes comfortably, providing a conducive environment for all its occupants.
-
Identification of Wear and Tear
Identifying wear and tear is like reading the history of your facility. You spot faded carpets, chipped paint, and malfunctioning doors. These aren’t just cosmetic concerns; they signal deeper issues that could impact safety and efficiency. This is where your keen observational skills come into play, ensuring that you address issues before they snowball into major problems.
-
Documentation and Data Collection
As you gather facility information, think of it as assembling puzzle pieces. Each document – whether blueprints, warranties, or maintenance manuals—adds a fragment to the complete picture. Just as you treasure a family heirloom, these documents hold the essence of your facility’s story.
Reviewing maintenance records is like revisiting old diaries. You notice patterns: a leak that reoccurs every rainy season, a recurring circuit issue. These insights guide your strategy, preventing recurring problems.
How to Perform a Facility Condition Evaluation: A Practical Guide for Facility Managers
As a facility manager, you know that maintaining your facility in tip-top shape isn’t just about keeping appearances. It’s about ensuring the safety of occupants, optimizing operational efficiency, and making wise financial decisions. That’s where a FCA comes into play – your strategic roadmap for facility maintenance and improvements. Let’s explore the step-by-step process to answer how to do a facility condition assessment?
1. Preparing for the Assessment: Setting the Stage for Success
Before diving into the assessment, take a moment to define your objectives. Ask yourself, “What do I want to achieve from this assessment?” Whether it’s identifying critical repairs, enhancing energy efficiency, or prolonging the lifespan of your building, having clear objectives will steer the entire process.
To ensure a comprehensive evaluation, assemble a diverse assessment team. Just like a symphony needs different instruments, your team should include structural engineers, energy efficiency experts, and maintenance personnel. This mix of expertise will provide a well-rounded perspective on your facility’s condition.
2. Gathering Historical Data: Unraveling the Past
The journey into your facility’s history is akin to delving into an old treasure chest. Gather blueprints, maintenance logs, and past inspection reports. This historical data will help you understand how your facility has weathered time and give you a baseline for comparison.
With the aid of modern facilities management software, this process becomes seamless and incredibly insightful. Here’s how facilities management software transforms the way you gather historical data:
- Digital Archives: It allows you to digitize and store essential documents like blueprints, maintenance logs, and inspection reports in a centralized digital archive. This eliminates the need for physical storage and makes accessing historical data as easy as a few clicks.
- Easy Retrieval: Traditional manual retrieval of historical documents can be time-consuming and prone to errors. However, with software, you can search and retrieve specific records instantly using keywords or filters. This saves valuable time and ensures accurate data retrieval.
- Real-Time Accessibility: It grants authorized users access to historical data from any location with an internet connection. This is particularly useful for teams spread across different locations or for remote working situations.
- Comparison and Trend Analysis: It enables you to compare current conditions with past data effortlessly. You can track changes, identify trends, and gain insights into how your facility’s components have performed over time.
- Data Integration: The software can integrate with other systems like maintenance management or asset management. This enables cross-referencing historical data with ongoing maintenance activities, creating a comprehensive picture of your facility’s lifecycle.
- Data Preservation: Digital records are less susceptible to wear and tear compared to physical documents. It ensures the preservation of historical data for years to come, safeguarding critical information.
- Collaboration: Software fosters collaboration among team members. Different stakeholders can access historical data simultaneously, facilitating discussions, planning, and decision-making.
3. Visual Inspection and Data Collection
Now, it’s time for the boots-on-the-ground phase. During the exterior inspection, focus on structural integrity. Is there any visible damage, like cracks or leaning walls? Recall the example of the historical building on Main Street – its sagging roof was a red flag that led to immediate reinforcement.
Inside the facility, assess deterioration and energy efficiency. Peeling paint and worn-out flooring may seem minor, but they’re indicators of deeper issues. Remember the chilly conference room that was always a topic of complaint? Upgrading its insulation was a smart move that saved on heating costs.
Don’t forget the building systems. Safety and performance go hand in hand. An HVAC system past its prime can lead to uncomfortable work environments and reduced productivity. Addressing these issues now can prevent larger headaches later.
4. Evaluating Your Facility’s Health with Facility Condition Index (FCI)
You’ve probably had those moments when you step into your facility and wonder, “How’s everything holding up?” As a facility manager, your mission is to ensure everything runs smoothly. But how do you assess the overall condition of your facility?
That’s where the Facility Condition Index (FCI) steps in – a tool that can give you valuable insights into the health of your building.
Think of FCI as a health checkup for your facility. It’s a metric that reflects the condition of your building’s physical assets compared to their ideal state. FCI considers factors like maintenance, repair, and replacement costs to give you a clear picture of where your facility stands in terms of wear and tear.
Calculating FCI: Crunching the Numbers
Now, you might be wondering, “How do you calculate facility condition index?” Well, the formula is quite straightforward. FCI is calculated by dividing the total cost of required repairs and replacements by the total current replacement value of the facility. The result is then multiplied by 100 to get the FCI percentage.
Simply put:
FCI = (Total Cost of Repairs and Replacements / Total Current Replacement Value) * 100
You’re probably thinking, “Okay, I have this FCI number. But what do I do with it?” Great question! FCI offers you a reality check on the state of your facility. It helps you prioritize your maintenance budget and make informed decisions. For instance, if your FCI is high, indicating a significant backlog of repairs, it might be time to allocate resources strategically to address critical issues.
Let’s dive into a real-life example. Imagine you manage a university campus. Your FCI assessment reveals a score of 25%. This means that your facility is in relatively good shape, with only a quarter of the ideal replacement value needed for repairs and replacements. However, this doesn’t mean you kick back and relax. Instead, you can focus on preventive maintenance to keep that FCI number from creeping up.
Remember, FCI isn’t just about numbers. It’s about understanding the story they tell. A higher FCI might signify years of deferred maintenance, indicating the need for urgent attention. Conversely, a lower FCI could be a result of proactive upkeep efforts.
5. Creating the Facility Condition Report: From Data to Action
Think of the report as your masterpiece canvas. Structure it logically: methodology, findings, and recommendations. A picture is worth a thousand words, so don’t skimp on photos and detailed notes. Remember, the report isn’t just about documenting issues – it’s about outlining actionable steps. Let’s delve into how to create a report that not only presents data but provides you with clear, actionable insights.
-
Organizing Assessment Findings:
In facility management, a picture really is worth a thousand words. Photos and videos are your allies in capturing the essence of a facility’s current state.
For instance, a facility manager at a manufacturing unit can document rusted pipelines that are crisscrossing the premises, which would showcase an urgent need for repair. So, data collection would encompass traditional as well as non-traditional ways of obtaining data. Be it temperature logs or equipment performance metrics, hard data adds depth to your findings.
-
Reporting Condition Ratings:
Presenting assessment findings isn’t just about sharing data; it’s about telling a compelling story. Imagine you’re showcasing the progress of your favorite sports team. Similarly, the condition scores give your facility’s “performance” a scorecard.
For instance, the efficient HVAC system might score a 7 due to its age and intermittent malfunctions. But it’s the critical issues that deserve the spotlight. Like a coach, highlight these concerns, such as a worn-out fire suppression system, demanding immediate attention.
-
Providing Recommendations:
The FCA report offers a roadmap. Short-term and long-term planning is akin to managing your personal finances.
Just as you set aside money for emergencies and invest for the future, allocate resources for immediate repairs and plan for long-term upgrades. Say you’re managing a school facility – immediate fixes could include addressing leaky roofs before the rainy season, while a gymnasium upgrade might be a long-term endeavor to boost student engagement.
-
Delivering Clear and Actionable Insights
Now, let’s step into your shoes. Armed with a comprehensive FCA report, you’re ready to lead your team into action. The insights you glean from this report empower you to make informed decisions.
For instance, you can leverage the FCA report to schedule elevator maintenance during off-peak hours, thereby minimizing disruption. It will not only streamline daily operations but also improve your facility’s overall efficiency.
6. Implementing Findings: Turning Plans into Reality
This is where your strategic prowess takes center stage. Develop a maintenance plan that covers both immediate needs and long-term goals. You can implement a regular roof inspection schedule after the FCA and reveal recurring issues. This proactive approach will save money and prevent major disruptions.
As budgeting is your financial roadmap, allocate resources based on priority and projected costs. Collaborate closely with contractors who understand your facility’s needs. The renovation of the outdated conference room will show that with the right contractor, even seemingly complex projects can proceed smoothly.
Assessing Facilities: A Dive into Facility Condition Evaluation Standards
Facility condition assessment standards and guidelines might sound like just another set of rules, but they’re the compass that helps us navigate the complex world of facility management with finesse and accuracy. So, let’s roll up our sleeves and explore these standards that form the backbone of our profession.
1. Setting the Stage with Industry Standards and Guidelines
You know how every industry has its rulebook? These standards aren’t just pieces of paper but our guiding stars. Take the ASTM E2018-15 Standard, for instance. It’s like the North Star of FCA. It gives us a systematic approach to evaluating facilities, helping us identify issues and make informed decisions.
Speaking of stars, have you come across BOMA’s Facility Assessment Standard? It defines a common language for assessments, ensuring consistency across the board. And then there’s IFMA’s Facility Management Standards, that provides us with best practices to enhance the value of our facilities. These standards aren’t about stifling creativity but about giving us a solid foundation to build upon.
2. Compliance: More than Just a Checkbox
Now, let’s talk about compliance. Think of it this way: compliance isn’t about fitting into a mold; it’s about meeting regulatory requirements that ensure the safety and functionality of our facilities.
Remember that one time a facility got hit with hefty fines because they didn’t follow proper assessment guidelines? Yeah, that’s the price of not playing by the rules.
Adhering to these standards creates a consistent baseline that makes communication smoother and decisions more transparent.
Facility Condition Assessment Checklist
Below is a specimen of Facility Condition Assessment Checklist for comprehensive property evaluation, ensuring optimal functionality, safety, and maintenance strategies.
|
Inspection Item Status Guide:
|
Area: Building Exterior | Status |
Roofing System:
|
|
Exterior Walls:
|
|
Area: Interior Spaces | |
Floor condition and wearWall and ceiling condition
Interior windows and doors |
|
Area: Mechanical and Electrical Systems | |
HVAC Systems:
|
|
Electrical Systems:
|
|
Plumbing Systems:
|
|
Area: Site and Grounds | |
Landscaping:
|
|
Pavement and Walkways:
|
|
Area: Health and Safety Compliance | |
Fire Safety:
|
|
Accessibility:
|
|
Emergency Exits:
|
|
Area: Other Considerations | |
Sustainability:
|
|
Maintenance Schedule:
|
|
Additional Notes: ___________________________ |
Conclusion
Facility condition assessment is not just an optional process; it’s a strategic tool that empowers organizations to manage their assets effectively. By extending the lifespan of facilities, optimizing maintenance efforts, ensuring safety, and enhancing operational efficiency, FCA contributes to the overall success of any organization.
The detailed assessment components and standards discussed in this blog underscore the importance of implementing facility condition assessment services.
You can repose your trust in FieldCircle platform for FCA and gain a distinct advantage in making well-informed decisions that not only contribute to their financial stability but also enhance overall operational success. This integrated approach empowers businesses to proactively identify potential issues, allocate resources effectively, and implement timely maintenance strategies.