A Detailed Centrifugal Pump Preventive Maintenance Checklist
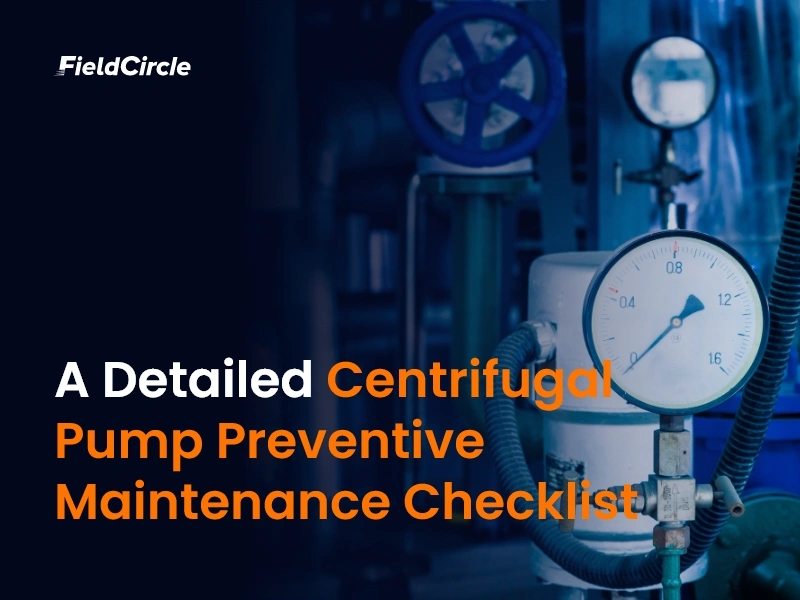
Centrifugal pumps are integral to operations in many industrial applications, as they move liquids through systems efficiently. Over time, parts like the impeller, seals, and bearings experience wear and over time start affecting performance.
Regular maintenance tasks such as checking for impeller damage, verifying shaft alignment, and inspecting seals is thus a necessity for the maintenance of your industrial pumps. Likewise, monitoring lubrication levels in bearings and checking for leaks in the pump casing is equally important in preventing pump failures. All this is made possible via a centrifugal pump maintenance checklist. Let’s understand what an all-encompassing checklist for preventive maintenance of a centrifugal pump covers so that it continues to function uninterruptedly.
What is a Centrifugal Pump Preventive Maintenance Checklist?
A centrifugal pump preventive maintenance checklist is a structured tool used to systematically monitor and maintain pump performance. It organizes tasks to verify key pump components, monitor operational conditions, and track performance and aids in the consistent evaluation of critical areas, such as alignment, seals, vibration, and lubrication, thereby streamlining the centrifugal pump maintenance schedule and helping maintain reliable pump operation.
What are the Benefits of a Centrifugal Pump Preventive Maintenance Checklist?
Offering a structured approach to identifying early warning signs, keeping mechanical components in check, and supporting uninterrupted pump performance over time, a centrifugal pump maintenance checklist benefits in multiple ways. Like it:
- Stops impeller damage before it snowballs
- Keeps cavitation out of the picture
- Prevents bearings from grinding themselves to failure
- Stops seals from leaking and causing chaos
- Catches shaft misalignment before it wrecks couplings
- Stops wear rings from killing your efficiency
- Protects motor from pulling more amps than it should
- Holds vibration levels within safe limits
- Avoids heat spikes that shut you down
- Preserves flow rate by keeping suction clear
- Avoids costly pressure drops at the discharge
By catching early signs of vane erosion or metal loss, the checklist prevents uneven wear that throws the impeller off balance and messes with the hydraulic flow.
Tracking suction pressure and inspecting for blockage helps avoid low-pressure pockets that hammer the impeller and wreck the internals from the inside out.
Lubrication checks, noise assessment, and temperature readings pick up bearing wear before it leads to overheating, friction spikes, and sudden seizure.
Seal face inspection and flush plan checks help prevent leakage that can lead to contamination, dry running, or pump motor short circuits.
A quick alignment check saves the shaft from wobbling, which otherwise chews through coupling sleeves, loads the motor unevenly, and leads to downtime.
Measuring the clearance between impeller and wear rings keeps internal leakage in check and avoids a gradual drop in head and flow rate.
Amp draw tracking during inspection helps spot abnormal resistance caused by internal friction, partial blockages, or rotor drag before the motor gives out.
Routine maintenance of pump vibration helps catch rotor imbalance, baseplate looseness, or shaft deflection early—before bearings crack or casing bolts back out.
Oil level and temperature checks prevent dry bearings and overheating issues that force shutdowns and require full bearing replacements.
Checklist tasks like inspecting suction strainers or pipe inlet prevent debris build-up that starves the pump and reduces delivery volume across the system.
Monitoring diffuser vanes and volute surfaces during inspections helps retain the pump’s pressure head, avoiding the slow bleed of hydraulic performance.
Centrifugal Pump Preventive Maintenance Checklist
A maintenance checklist for centrifugal pump maintenance is incomplete without the following 12 items. Go through them for a comprehensive maintenance of your centrifugal pump.
1. Pump Casing and Volute Maintenance
- Visual Inspection of Casing
- Check for cracks, chips, or corrosion: Look for visible signs of damage or stress on the casing. These may include cracks, pitting, or rust.
- Inspect for leaks: Ensure there are no signs of fluid leakage from the pump casing.
- Check for deformation: Inspect the pump casing for any signs of warping or distortion.
- Check for cracks, chips, or corrosion: Look for visible signs of damage or stress on the casing. These may include cracks, pitting, or rust.
- Condition of Casing Gaskets and Seals
- Inspect gaskets for wear and aging: Examine all gasket materials for cracks, fraying, or hardening.
- Ensure proper sealing: Check that the gaskets fit snugly and create a proper seal.
- Replace worn gaskets: If gaskets are damaged, replace them with the correct material and dimensions specified by the manufacturer.
- Inspect gaskets for wear and aging: Examine all gasket materials for cracks, fraying, or hardening.
- Casing Bolt Tightening
- Check bolt integrity: Examine the casing bolts for any signs of corrosion, loosening, or wear.
- Ensure even bolt tightness: Tighten the casing bolts in a star pattern to ensure even pressure distribution across the casing.
- Check bolt integrity: Examine the casing bolts for any signs of corrosion, loosening, or wear.
- Casing Cleanliness
- Remove debris or sediment: Clean the interior and exterior surfaces of the pump casing, removing any debris, dirt, or sediment.
- Inspect internal surfaces: Look for any build-up of minerals, scale, or sludge that could impede fluid flow.
- Remove debris or sediment: Clean the interior and exterior surfaces of the pump casing, removing any debris, dirt, or sediment.
2. Impeller Maintenance
- Impeller Inspection
- Check for wear and tear: Inspect the impeller blades for any signs of damage, erosion, or wear.
- Inspect for corrosion: Examine the impeller for signs of rust or corrosion, especially if the pump handles aggressive or corrosive fluids.
- Verify blade condition: Ensure the blades are intact and without cracks.
- Check for wear and tear: Inspect the impeller blades for any signs of damage, erosion, or wear.
- Impeller Clearance Check
- Measure impeller-to-casing clearance: Measure the gap between the impeller and casing.
- Adjust clearance if necessary: If the gap exceeds the manufacturer’s specified range, adjustments or replacement of parts may be required.
- Impeller Balancing
- Check for imbalance: Verify that the impeller is balanced.
- Perform dynamic balancing: If necessary, use dynamic balancing equipment to bring the impeller back into proper balance.
- Check for imbalance: Verify that the impeller is balanced.
- Impeller Shaft Inspection
- Examine shaft for alignment: Check the impeller shaft for proper alignment.
- Inspect shaft for wear: Check the impeller shaft for signs of wear, corrosion, or scoring. Worn shafts may need to be replaced or refurbished.
- Examine shaft for alignment: Check the impeller shaft for proper alignment.
3. Shaft Sleeve Maintenance
- Shaft Sleeve Visual Inspection
- Check for wear and corrosion: Inspect the shaft sleeve for signs of wear, pitting, or corrosion.
- Inspect for cracks or fractures: Examine the shaft sleeve for cracks.
- Check for wear and corrosion: Inspect the shaft sleeve for signs of wear, pitting, or corrosion.
- Shaft Sleeve Fit
- Verify proper installation: Ensure the shaft sleeve is securely and correctly fitted onto the shaft..
- Check for axial movement: Make sure the sleeve does not exhibit excessive axial or radial movement.
- Verify proper installation: Ensure the shaft sleeve is securely and correctly fitted onto the shaft..
- Shaft Sleeve Lubrication
- Check for lubrication: Ensure the shaft sleeve is properly lubricated if it requires lubrication.
- Verify lubricant condition: Inspect the condition of any lubricant used and if contaminated, replace it with the recommended type.
- Check for lubrication: Ensure the shaft sleeve is properly lubricated if it requires lubrication.
- Sleeve Replacement
- Replace worn or damaged sleeves: If the shaft sleeve shows significant wear, cracks, or corrosion, replace it promptly.
- Replace worn or damaged sleeves: If the shaft sleeve shows significant wear, cracks, or corrosion, replace it promptly.
4. Bearings and Bearing Housing Maintenance
- Bearing Condition
- Inspect for wear or damage: Examine the bearings for excessive wear, cracks, or corrosion.
- Check bearing play: Measure the axial and radial play of the bearings.
- Inspect for wear or damage: Examine the bearings for excessive wear, cracks, or corrosion.
- Bearing Lubrication
- Check lubrication levels: Ensure the bearings are properly lubricated according to manufacturer specifications.
- Inspect for lubricant contamination: Check for any contamination in the lubricant, such as dirt, water, or metal particles.
- Check lubrication levels: Ensure the bearings are properly lubricated according to manufacturer specifications.
- Bearing Housing Condition
- Inspect bearing housing for cracks or wear: Examine the bearing housing for any visible cracks, damage, or signs of corrosion.
- Check for proper alignment: Ensure that the bearing housing is properly aligned with the shaft and pump casing.
- Inspect bearing housing for cracks or wear: Examine the bearing housing for any visible cracks, damage, or signs of corrosion.
- Temperature Monitoring
- Check bearing temperature: Use temperature sensors or infrared thermometers to monitor the bearing temperature during operation.
- Investigate abnormal temperatures: If the bearing temperature exceeds the recommended range, identify the cause and take corrective actions.
- Check bearing temperature: Use temperature sensors or infrared thermometers to monitor the bearing temperature during operation.
5. Seals and Gaskets Maintenance
- Mechanical Seal Inspection
- Check for leakage: Inspect the mechanical seal for any visible fluid leakage around the sealing faces.
- Inspect sealing faces for wear: Examine the faces of the mechanical seal for scoring, pitting, or wear.
- Inspect for corrosion: Look for any signs of corrosion on the mechanical seal.
- Check for leakage: Inspect the mechanical seal for any visible fluid leakage around the sealing faces.
- Seal Face Alignment
- Ensure proper alignment of seal faces: Verify that the mechanical seal faces are aligned properly.
- Check for proper compression: Ensure that the seal faces are compressed correctly and provide a tight seal.
- Ensure proper alignment of seal faces: Verify that the mechanical seal faces are aligned properly.
- Seal Material Condition
- Examine seal material for deterioration: Inspect the material of the mechanical seal for signs of deterioration.
- Verify compatibility: Ensure that the mechanical seal material is compatible with the pumped fluid.
- Examine seal material for deterioration: Inspect the material of the mechanical seal for signs of deterioration.
- Gasket Inspection
- Inspect gaskets for wear and degradation: Examine gaskets for signs of wear, cracking, or hardening.
- Check for proper gasket compression: Ensure that the gasket is compressed evenly and creates a proper seal.
- Check gasket surface condition: Ensure that the sealing surfaces where gaskets sit are smooth and free of debris.
- Inspect gaskets for wear and degradation: Examine gaskets for signs of wear, cracking, or hardening.
- Gasket Replacement
- Replace worn or damaged gaskets: If gaskets are showing signs of wear or degradation.
- Verify correct gasket material: Always use the appropriate gasket material that can withstand the temperature, pressure, and chemical properties of the pumped fluid.
- Replace worn or damaged gaskets: If gaskets are showing signs of wear or degradation.
6. Motor and Coupling Maintenance
- Motor Condition Check
- Inspect for external damage: Visually inspect the motor casing for any visible cracks, dents, or signs of wear.
- Verify motor cooling: Check that the motor cooling fins and air vents are clean and free of blockages.
- Inspect for unusual noise: Listen for any unusual sounds from the motor, such as grinding or screeching.
- Motor Alignment
- Check motor alignment: Verify that the motor is properly aligned with the pump shaft.
- Check for axial and radial movement: Ensure there is no abnormal movement or play in the motor shaft.
- Check motor alignment: Verify that the motor is properly aligned with the pump shaft.
- Bearing Check (Motor)
- Inspect motor bearings: Check the motor bearings for wear, excessive play, or overheating.
- Lubricate bearings: Ensure motor bearings are properly lubricated per the manufacturer’s specifications.
- Inspect motor bearings: Check the motor bearings for wear, excessive play, or overheating.
- Motor Electrical Connections
- Inspect wiring for wear or damage: Check all electrical wiring for any signs of wear, loose connections, or exposed wires.
- Check terminal block for tightness: Ensure that all electrical terminals are securely tightened and free from corrosion.
- Verify motor insulation resistance: Use an insulation resistance tester to check the condition of the motor’s insulation.
- Inspect wiring for wear or damage: Check all electrical wiring for any signs of wear, loose connections, or exposed wires.
- Coupling Inspection
- Inspect coupling for damage: Examine the coupling between the motor and pump for any signs of wear, cracks, or misalignment.
- Check coupling alignment: Verify that the coupling is properly aligned.
- Lubricate coupling if required: Ensure that the lubricant is applied according to the manufacturer’s specifications.
- Inspect coupling for damage: Examine the coupling between the motor and pump for any signs of wear, cracks, or misalignment.
- Vibration and Temperature Monitoring
- Monitor vibration levels: Use vibration sensors to monitor the motor and coupling’s operation.
- Check motor temperature: Use temperature sensors or an infrared thermometer to check the motor’s operating temperature.
- Monitor vibration levels: Use vibration sensors to monitor the motor and coupling’s operation.
7. Pump Performance Testing
- Flow Rate Testing
- Measure the flow rate: Periodically test the flow rate to ensure that it matches the design specifications.
- Check for consistent performance: Compare the actual flow rate against historical data.
- Measure the flow rate: Periodically test the flow rate to ensure that it matches the design specifications.
- Head and Pressure Testing
- Measure pump head: Regularly check the pump head to ensure it meets the required specifications.
- Test discharge pressure: Check the discharge pressure to confirm that the pump is operating within the expected range.
- Measure pump head: Regularly check the pump head to ensure it meets the required specifications.
- Efficiency Check
- Monitor pump efficiency: Perform efficiency tests to ensure the pump is operating at its optimal energy consumption.
- Compare input vs output power: Verify that the power input and output match the manufacturer’s specifications.
- Monitor pump efficiency: Perform efficiency tests to ensure the pump is operating at its optimal energy consumption.
- Cavitation Inspection
- Monitor for cavitation signs: Listen for cavitation noise, which can be caused by improper flow, pressure issues, or incorrect impeller clearance.
- Check for cavitation damage: If cavitation is suspected, inspect the impeller and casing for erosion or pitting.
- Monitor for cavitation signs: Listen for cavitation noise, which can be caused by improper flow, pressure issues, or incorrect impeller clearance.
- System Pressure Monitoring
- Ensure system pressure is within limits: Regularly check that the system pressure does not exceed the design parameters.
- Inspect pressure relief valves: Ensure that the pressure relief valves are functioning properly.
- Ensure system pressure is within limits: Regularly check that the system pressure does not exceed the design parameters.
8. Suction and Discharge Piping Maintenance
- Suction Piping Inspection
- Check for blockages or restrictions: Inspect the suction piping for any signs of blockages, restrictions, or build-up of debris.
- Inspect suction strainer (if applicable): Check the suction strainer for clogging, corrosion, or damage.
- Verify proper pipe alignment: Ensure that the suction pipe is correctly aligned and free from any kinks, bends, or misalignments.
- Check for air leaks: Inspect the suction piping for any signs of air leaks, particularly around joints and fittings.
- Monitor for vibration: Ensure that the suction pipe is properly secured.
- Check for blockages or restrictions: Inspect the suction piping for any signs of blockages, restrictions, or build-up of debris.
- Discharge Piping Inspection
- Inspect for leaks or damage: Check the discharge piping for leaks, cracks, or signs of wear.
- Check for pipe alignment: Ensure the discharge piping is properly aligned with the pump outlet.
- Verify pressure rating: Check that the discharge piping is rated for the required pressure.
- Check for corrosion: Inspect the discharge piping for signs of corrosion or material degradation.
- Check discharge valve operation: Test the discharge valve to ensure it opens and closes properly.
- Inspect for leaks or damage: Check the discharge piping for leaks, cracks, or signs of wear.
- Piping Supports and Braces
- Inspect piping supports for wear: Examine the supports and braces that hold the suction and discharge pipes.
- Check for proper pipe strain: Ensure that the piping does not experience excessive strain from improper supports or alignment.
- Verify that all supports are secured: Confirm that all pipe supports are securely fastened and not showing signs of wear or failure.
- Inspect piping supports for wear: Examine the supports and braces that hold the suction and discharge pipes.
- Piping Flow Testing
- Perform flow rate test: Regularly test the flow rate through the suction and discharge pipes.
- Measure pressure drop: Measure the pressure drop between the suction and discharge sections of the piping.
- Perform flow rate test: Regularly test the flow rate through the suction and discharge pipes.
9. Pump Shaft and Shaft Bearings
- Pump Shaft Inspection
- Inspect for wear or corrosion: Examine the pump shaft for signs of wear, scoring, or corrosion.
- Check for shaft runout: Measure the shaft’s runout to ensure it is within tolerance.
- Check for cracks or fractures: Inspect the shaft for cracks or fractures, particularly around keyways and threading areas.
- Inspect for wear or corrosion: Examine the pump shaft for signs of wear, scoring, or corrosion.
- Shaft Bearings Inspection
- Check bearing play: Measure the axial and radial play of the shaft bearings.
- Check for bearing wear or damage: Inspect the bearings for signs of wear, corrosion, or damage.
- Ensure proper lubrication: Check that the shaft bearings are properly lubricated, and the lubricant is clean and at the correct level.
- Check bearing play: Measure the axial and radial play of the shaft bearings.
- Shaft Alignment
- Ensure proper alignment of shaft: Use an alignment tool to verify that the pump shaft is correctly aligned with the motor and coupling.
- Check for axial and radial misalignment: Measure both axial and radial misalignment.
- Realign shaft if necessary: If misalignment is detected, take corrective actions to realign the shaft.
- Ensure proper alignment of shaft: Use an alignment tool to verify that the pump shaft is correctly aligned with the motor and coupling.
10. Supporting Systems and Safety Devices
- Pressure Relief Valves
- Inspect for proper operation: Check that the pressure relief valve is functioning correctly and opens when the system pressure exceeds the set limit.
- Check for leaks: Ensure there are no leaks around the pressure relief valve or its seat.
- Test pressure settings: Regularly verify that the pressure relief valve is set to the correct pressure, according to system requirements.
- Inspect for corrosion or damage: Examine the valve components for signs of corrosion, wear, or damage.
- Inspect for proper operation: Check that the pressure relief valve is functioning correctly and opens when the system pressure exceeds the set limit.
- Vibration Monitoring System
- Inspect vibration sensors: Check the condition and calibration of vibration sensors installed on the pump.
- Monitor vibration levels: Continuously monitor vibration data to identify any abnormal patterns.
- Check sensor wiring: Inspect the wiring of vibration sensors for any loose connections, damage, or wear.
- Inspect vibration sensors: Check the condition and calibration of vibration sensors installed on the pump.
- Temperature Monitoring System
- Check temperature sensors: Ensure that all temperature sensors installed on the pump, motor, and bearing housings are operational and properly calibrated.
- Monitor pump and motor temperatures: Regularly check the temperature readings to ensure that they fall within acceptable limits
- Inspect sensor wiring and connections: Ensure that the wiring and connections for temperature sensors are secure and free from damage.
- Check temperature sensors: Ensure that all temperature sensors installed on the pump, motor, and bearing housings are operational and properly calibrated.
- Control Panel Inspection
- Inspect control panel for damage: Check the control panel for signs of external damage, such as dents, cracks, or overheating.
- Check control panel wiring: Inspect the wiring in the control panel to ensure that connections are secure and not showing signs of wear, corrosion, or overheating.
- Test alarm and shutdown systems: Regularly test the alarm and emergency shutdown systems.
- Inspect control panel for damage: Check the control panel for signs of external damage, such as dents, cracks, or overheating.
- System Safety Devices
- Check for operational safety devices: Ensure that all safety devices (e.g., automatic shut-off valves, thermal protection devices) are in good working condition.
- Test system shutdown response: Simulate failure scenarios to test the system’s response.
- Check for operational safety devices: Ensure that all safety devices (e.g., automatic shut-off valves, thermal protection devices) are in good working condition.
11. Fluid Handling System
- Fluid Quality and Compatibility
- Check for fluid contamination: Inspect the fluid for signs of contamination, such as debris, rust, or foreign particles.
- Verify fluid compatibility: Ensure that the pump is compatible with the fluid being handled by checking the fluid’s pH, temperature, viscosity, and chemical composition.
- Inspect fluid filters: If the system uses fluid filters, ensure that they are clean and functioning properly.
- Check for fluid contamination: Inspect the fluid for signs of contamination, such as debris, rust, or foreign particles.
- Fluid Level and Consistency
- Monitor fluid level: Regularly check the fluid level in the pump system to ensure it is within the required operating range.
- Check for fluid consistency: Ensure the fluid consistency remains stable over time.
- Monitor fluid level: Regularly check the fluid level in the pump system to ensure it is within the required operating range.
- Handling Slurries or Abrasive Fluids
- Inspect pump seals: When handling slurries or abrasive fluids, ensure that the pump seals are in good condition.
- Check for wear on internal components: Monitor for excessive wear on the impeller, volute, and diffuser due to the abrasive nature of the fluid.
- Use specialized materials: If pumping abrasive fluids, ensure that all wetted parts are made from wear-resistant materials such as stainless steel or ceramic.
- Inspect pump seals: When handling slurries or abrasive fluids, ensure that the pump seals are in good condition.
- Fluid Temperature Monitoring
- Monitor fluid temperature: Keep track of the fluid temperature during operation.
- Ensure cooling system efficiency: If the pump or fluid requires cooling, verify that the cooling system is functioning properly.
- Monitor fluid temperature: Keep track of the fluid temperature during operation.
- System Drainage and Leak Detection
- Inspect drainage systems: Regularly check drainage lines to ensure that fluids are draining properly and that there are no blockages or backflows that could damage the pump.
- Check for leaks: Inspect the system for leaks, especially around seals, gaskets, and connections.
- Ensure proper leak detection mechanisms: If applicable, ensure that leak detection sensors are functioning correctly.
- Inspect drainage systems: Regularly check drainage lines to ensure that fluids are draining properly and that there are no blockages or backflows that could damage the pump.
12. Pump Efficiency Testing and Documentation
- Performance Testing
- Test pump flow rate: Periodically test the pump’s flow rate to ensure that it meets the design specifications.
- Test discharge pressure: Measure the discharge pressure to ensure that it is within the acceptable range.
- Measure power consumption: Record the pump’s power consumption and compare it to the manufacturer’s specifications.
- Conduct efficiency calculations: Calculate the pump’s overall efficiency (i.e., hydraulic efficiency, mechanical efficiency, and overall system efficiency) by comparing the input power to the output power.
- Test pump flow rate: Periodically test the pump’s flow rate to ensure that it meets the design specifications.
- Vibration and Noise Testing
- Monitor vibration levels: Test and monitor vibration levels during pump operation.
- Record pump noise levels: Measure noise levels generated by the pump.
- Use vibration analysis tools: Use advanced tools such as vibration analyzers and accelerometers to assess the condition of pump bearings, shaft alignment, and overall system health.
- Monitor vibration levels: Test and monitor vibration levels during pump operation.
- Maintenance Documentation
- Maintain log of inspections and repairs: Keep a detailed log of all maintenance and inspection activities, and repairs performed on the pump. Include dates, issues identified, and corrective actions taken.
- Document replacement parts: Maintain records of any parts that have been replaced, including the part numbers, dates of replacement, and reasons for replacement.
- Track performance metrics: Regularly update and track performance metrics, such as flow rates, pressure readings, energy consumption, and vibration levels.
- Record manufacturer recommendations: Follow the manufacturer’s maintenance recommendations and document any specific guidelines provided for your pump model.
- Maintain log of inspections and repairs: Keep a detailed log of all maintenance and inspection activities, and repairs performed on the pump. Include dates, issues identified, and corrective actions taken.
- Calibration of Instruments and Sensors
- Check instrument calibration: Periodically calibrate instruments used to measure flow rate, pressure, temperature, and vibration.
- Calibrate sensors: Ensure that any sensors involved in monitoring the pump system (e.g., temperature, pressure, vibration) are regularly calibrated.
- Record calibration results: Keep a record of all calibration results, including the date, instrument used, and any adjustments made to the system.
- Check instrument calibration: Periodically calibrate instruments used to measure flow rate, pressure, temperature, and vibration.
- Reporting and Communication
- Generate maintenance reports: Create regular maintenance reports that summarize the status of the pump, including any issues encountered, repairs made, and performance data.
- Share reports with relevant personnel: Ensure that maintenance reports are shared with key personnel such as operators, engineers, and management.
- Review historical data: Regularly review historical maintenance and performance data to identify trends, recurring issues, and opportunities for improvement.
What are the Tips to Follow for Centrifugal Pump Maintenance?
Following are some highly useful tips that you must follow while carrying out the maintenance and inspection procedures for your centrifugal pump:
- Monitor Vibration Patterns Specific to Operating Speed
Excessive vibration can be a sign of potential danger. So, don’t just track overall vibration — compare vibration spectra against baseline signatures at specific RPMs. Unusual spikes at harmonics can indicate misalignment or bearing wear that isn’t obvious at startup.
- Flush Seal Chambers When Pumping Slurries or Hot Liquids
In applications like mining or thermal oil circulation, install a proper flush plan to prevent solids buildup or thermal coking around mechanical seals, which can cause premature failure.
- Record Suction Pressure Daily in Multi-Pump Systems
Especially in parallel pumping systems, suction starvation or differential pressure imbalance can lead to cavitation. Logging these readings helps spot upstream blockage or pump competition early.
- Inspect Impeller Eye for Scaling if Handling Hard Water
In HVAC or water treatment plants using untreated hard water, limescale often forms at the impeller eye, reducing flow. Clean it periodically to prevent flow loss and overload conditions.
- Check Motor and Pump Alignment After Any Thermal Cycle
For pumps in steam service or systems that frequently heat and cool (like CIP cycles in food plants), alignment should be verified post-temperature changes, as thermal growth causes shaft misalignment.
- Change Oil Only After Analyzing Oil Color and Odor
Instead of relying solely on hours-run, inspect oil for discoloration or burnt smell — signs of overheating or contamination, especially in pumps running near BEP (Best Efficiency Point) limits.
- Bleed Air from Casing Before Every Start in Top-Suction Pumps
Top-suction, top-discharge configurations trap air in the casing. If not vented, this leads to dry-running and seal burnout. Use the air release valve or manually crack a high-point plug before starting.
- Use Laser Alignment for Pumps with Flexible Couplings
Old dial methods can miss angular misalignment, especially on pumps with flexible couplings. Laser alignment provides better accuracy, essential for high-speed or close-tolerance systems like booster stations.
- Inspect Gland Packing Adjustments Weekly for Process Pumps
In abrasive or corrosive service, gland packing gets eaten quickly. Don’t wait for leaks — check weekly and re-tighten or repack before process fluid starts dripping excessively.
- Backflush Cooling Jackets in Chemical Process Units
In applications like polymer or resin manufacturing, cooling jackets can clog over time. Backflushing these jackets during scheduled downtime helps maintain thermal regulation and prevents overheating of the pump casing.
- Log Amperage Draws on Startup and Compare with Baseline
A rising trend in starting amps may point to increased system resistance, impeller fouling, or motor degradation. Logging amperage instead of relying on feel avoids undetected power inefficiencies.
- Inspect Foot Valves and Check Valves in Vertical Sump Installations
In wastewater or stormwater setups, stuck or leaking check valves can cause reverse flow, water hammer, or even dry running. Inspect during low-load periods or simulated drainage cycles.
To Wrap Up
With this preventive maintenance checklist for centrifugal pumps at your disposal, you can be assured of a sustainable performance from your pump. With it, your periodic (quarterly, biannually, and annually) inspection and maintenance process will be streamlined and the equipment will be in top shape ever. As a result, the fluid movement will be uninterrupted and the connected operations will continue smoothly.
- Generate maintenance reports: Create regular maintenance reports that summarize the status of the pump, including any issues encountered, repairs made, and performance data.