Top Ten Areas Preventive Maintenance Teams Lose Most Time During Work Hours
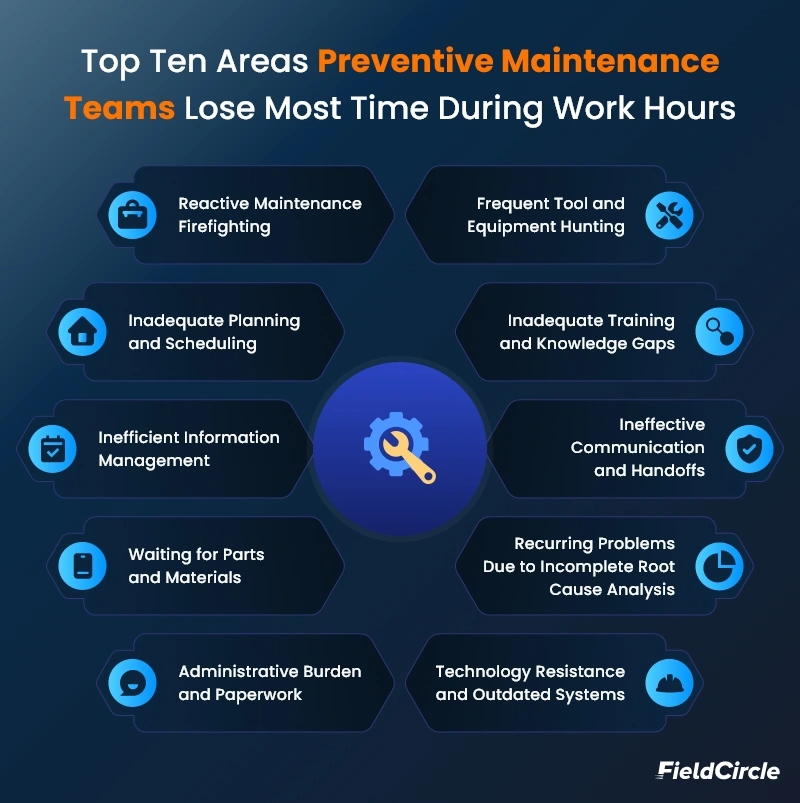
Your maintenance team is putting in long hours, yet equipment reliability continues to decline. Despite having skilled technicians and adequate resources, productivity seems stuck in quicksand. If this scenario sounds familiar, you’re experiencing what maintenance leaders across industries struggle with daily – the invisible time thieves that silently erode your team’s effectiveness.
Maintenance departments typically operate at just 25-30% wrench time – meaning technicians spend less than one-third of their day actually maintaining equipment. The rest? Lost to inefficiencies that have become so embedded in daily operations that they’re often invisible to management. These time drains don’t just impact maintenance metrics – they directly affect your bottom line.
Let’s explore the ten areas where maintenance teams lose the most valuable time during work hours, and more importantly, how forward-thinking maintenance leaders are successfully addressing them.
1. Reactive Maintenance Firefighting
Nothing devours a maintenance team’s productivity quite like an unplanned, reactive maintenance process. When equipment unexpectedly fails, it triggers a cascade of emergency responses that pull resources from scheduled maintenance work, creating a vicious cycle that’s difficult to escape.
Reactive maintenance typically consumes 3-5 times more resources than planned maintenance activities. Organizations operating in a predominantly reactive mode spend approximately 40% of their maintenance hours on emergency work that could have been prevented with proper condition monitoring and preventative maintenance.
Organizations that successfully break this cycle allocate dedicated resources specifically for reliability improvement projects, even during periods of high reactive demands. By protecting these resources from being pulled into firefighting mode, they gradually reduce the frequency of emergencies.
2. Inadequate Planning and Scheduling
When maintenance tasks begin without proper planning, technicians face a barrage of preventable delays and complications that significantly extend completion times. This inefficiency stems from technicians spending time gathering information that should have been provided upfront, discovering additional issues once work begins, and realizing mid-job that different tools or parts are needed.
The most successful maintenance programs implement structured planning processes where dedicated planners prepare detailed job plans that include parts lists, safety requirements, estimated time, and clear success criteria. These plans are created well in advance of scheduled work, allowing for materials to be staged and potential complications to be identified before a technician ever picks up a tool.
3. Inefficient Information Management
Access to accurate information can mean the difference between a 30-minute repair and a half-day struggle. Maintenance technicians frequently lose valuable time searching for equipment manuals, historical repair data, or troubleshooting guides.
Legacy systems exacerbate this problem, with information scattered across disparate locations – some digital, some paper-based. When information finally is found, it’s often outdated or incomplete, leading to incorrect repairs that will need to be redone later.
High-performing organizations centralize all maintenance-related information in accessible knowledge repositories, ensuring technicians can quickly find what they need. They also establish clear processes for keeping this information current, recognizing that outdated information can be worse than no information at all.
4. Waiting for Parts and Materials
Few situations frustrate maintenance professionals more than having equipment down, technicians ready, but being unable to proceed because necessary parts aren’t available. This scenario plays out daily in maintenance departments worldwide. This waiting time directly impacts equipment availability and team productivity. When a $5 gasket isn’t available, it can idle both a million-dollar machine and your highest-paid technician.
Organizations can address this through integrated inventory management systems that align with maintenance planning, establishing minimum/maximum levels for critical parts, and developing relationships with suppliers that can provide rapid response when needed.
5. Administrative Burden and Paperwork
While documentation is necessary for compliance, knowledge transfer, and analysis, excessive administrative requirements can significantly reduce the time technicians spend performing actual maintenance. These include filling out work orders and completion reports, logging time against multiple cost centers, documenting parts usage, completing safety documentation, and attending non-essential meetings.
Many maintenance departments still rely on paper-based systems that require duplicate data entry and create information silos. Even those with computerized systems often struggle with cumbersome interfaces that make simple documentation tasks unnecessarily complex.
These processes can be streamlined by eliminating redundant paperwork, implementing user-friendly mobile solutions for real-time documentation, and automating routine reporting. Focus on capturing essential information while eliminating administrative tasks that don’t add value.
6. Frequent Tool and Equipment Hunting
A seemingly simple issue with profound implications: technicians regularly waste time searching for the tools and equipment needed to perform their work. This time drain is particularly frustrating because it’s entirely preventable with proper organization systems, which directly impact equipment maintenance.
The causes typically include the absence of a standardized tool management system, tools not returned after use, shared equipment without clear checkout procedures, lack of accountability for specialized tools, and insufficient quantities of commonly used tools.
Maintenance departments can implement visual management systems like shadow boards, tool tracking technologies, and clear accountability processes. Many have adopted the 5S methodology (Sort, Set in order, Shine, Standardize, Sustain) specifically for their tool management, creating dramatic improvements in technician efficiency.
7. Inadequate Training and Knowledge Gaps
As equipment becomes increasingly sophisticated, the knowledge required to maintain it effectively also grows. Technicians with inadequate training or experience take significantly longer to diagnose and repair issues. Less experienced technicians not only work more slowly but also more frequently make errors that require rework.
This challenge is compounded by several factors:
- An aging workforce taking institutional knowledge into retirement
- Increasing technological complexity in modern equipment
- Budget constraints limiting formal training opportunities
- Poor documentation of specialized repair procedures
- Siloed knowledge held by individual “expert” technicians
Leading organizations combat this through structured knowledge transfer programs, detailed procedure documentation, and regular cross-training. Many have implemented mentoring systems where experienced technicians work alongside newer staff, accelerating skill development through practical application.
8. Ineffective Communication and Handoffs
Maintenance and inspections rarely happen in isolation. It requires coordination between shifts, departments, and sometimes external contractors – creating numerous opportunities for communication breakdowns. This manifests in several ways:
- Incomplete shift handovers leading to duplicated efforts
- Miscommunication between operations and maintenance about equipment availability
- Unclear expectations with contractors or specialized service providers
- Ambiguous priority systems creating confusion about what work should be done first
In maintenance, communication failures don’t just waste time—they directly impact safety and equipment reliability. We see increased incidents and repeat failures when critical information doesn’t transfer between shifts or departments.
Establish structured communication protocols, particularly around shift handovers and department interfaces, to improve effectiveness. Implement digital solutions that ensure critical information flows seamlessly between all stakeholders and create clear escalation paths for when communication breaks down.
9. Recurring Problems Due to Incomplete Root Cause Analysis
Perhaps the most insidious time drain is the one hidden in plain sight: the same problems occurring repeatedly because root causes are never properly addressed. This repetitive work represents an enormous opportunity cost, as resources spent fixing the same problems repeatedly could instead be directed toward preventing new ones.
Maintenance departments can implement structured root cause analysis (RCA) processes for significant or recurring issues. They can allocate dedicated time for these activities and track corrective actions to completion. Most importantly, measure success not by how quickly equipment returns to service after a failure but by how long it operates without failing again.
10. Technology Resistance and Outdated Systems
While maintenance has traditionally been a hands-on discipline, technology now plays a crucial role in efficiency. When maintenance teams are reluctant to adopt new methodologies or tools, they may continue using outdated, less effective practices, consume more time, and deliver suboptimal results.
Common technology gaps include:
- Paper-based work order systems requiring manual data entry
- Absence of mobile solutions for technicians
- Disconnected systems that don’t share information
- Limited or no use of predictive technologies
- Resistance to automation of routine tasks
Progressive maintenance teams take a strategic approach to maintenance technology, focusing first on foundational systems that eliminate the most significant time wasters. They involve frontline technicians in technology selection and implementation, ensuring solutions address real-world needs rather than creating additional burdens.
Takeaway: Adopt FieldCircle Preventive Maintenance Software
To truly tackle the time thieves that plague maintenance teams, it’s not just about having the right tools—it’s about transforming the way the team operates.
A game-changing shift happens when technology isn’t merely a support tool but an active participant in decision-making. For example, using AI-powered maintenance software to analyze historical failure patterns and adjust maintenance schedules in real-time can predict failures before they happen, drastically reducing emergency fixes and costly downtime.
By integrating such advanced technology, maintenance teams save time and also shift focus from fixing the same problems over and over to tackling more complex, strategic improvements.