How Manufacturing Companies Can Improve Service Efficiency
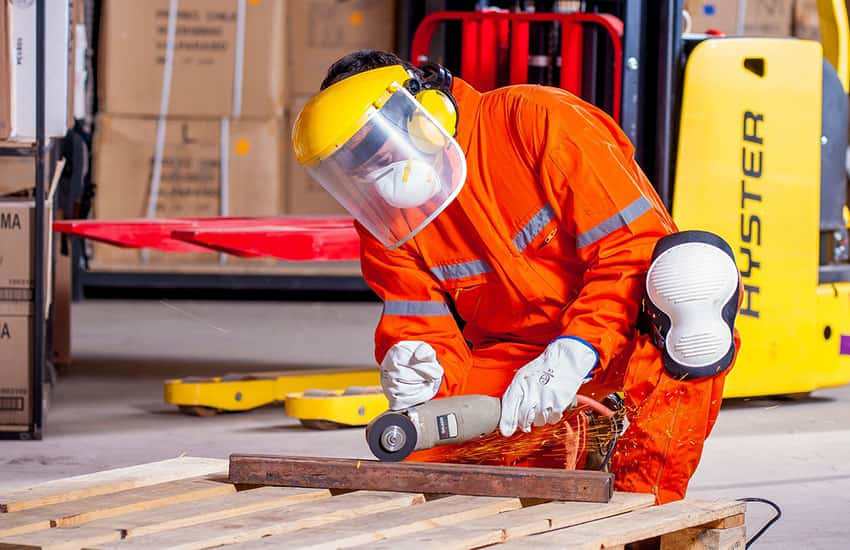
Each manufacturing organization works on one thumb rule – there exists a strong correlation between operational efficiency and productivity. Ultimately this relation shows its impact on profitability. The loss of output is a permanent loss as it cannot be recovered. When we trace back, operational efficiency rests on service efficiency, which becomes a critical aspect of overall performance.
Consistently improving service efficiency is thus an important goal for manufacturing companies. Reasons abound! Apart from commonly known customer satisfaction, efficient service can significantly reduce unplanned downtime, reduce interruptions, upkeep the value of the assets, and improve quality.
All these factors bring service efficiency high on the list of priorities for manufacturers. So, to ensure operational success and build a loyal consumer base, manufacturers must provide efficient service.
But how do you ensure that your service efficiency remains above thresholds and your customers have a great experience? We have identified 10 important strategies on how to consistently improve the service efficiency of your manufacturing business and remain at the top in your segment.
10 Ways How Manufacturing Companies Can Improve Service Efficiency
The key lies in implementing practical strategies that optimize operations, enhance customer satisfaction, and drive growth. Below are the 10 actionable strategies that manufacturing companies can adopt to improve their service efficiency.
Shorten your response time
In a recent SuperOffice annual customer service study, it was revealed that a staggering 62% of companies do not respond to customer emails. This lack of responsiveness creates a significant gap in customer satisfaction and presents an opportunity for companies to differentiate themselves from their competitors.
The study further highlighted that for companies that do respond, the average response time is 12 hours, with the slowest response taking longer than 8 days. This delay in customer communication can lead to frustration and dissatisfaction.
Source: SuperOffice
Imagine a manufacturing company that produces electronic devices. A customer contacts their customer support team with a technical issue they are facing with their recently purchased device. In the past, the average response time for addressing such inquiries was three days.
Recognizing the need for improvement, the company implements measures to shorten response time. Here are more practical actions that a manufacturing company can take to shorten response time and improve service efficiency:
- Streamline customer support processes to eliminate bottlenecks.
- Provide comprehensive training to support agents for better skills and product knowledge.
- Implement an advanced ticketing system for efficient query management.
- Utilize customer relationship management (CRM) software for centralized customer data.
- Leverage automation and AI-powered tools like chatbots for quicker responses.
- Continuously gather customer feedback to identify areas for improvement.
Implementing these actions can help manufacturing companies shorten response time, enhance service efficiency, and improve overall customer satisfaction.
Implement preventive maintenance
Prevention is better than cure, they say. Apply this philosophy to your service operations by implementing preventive maintenance. To execute preventive maintenance tasks in manufacturing and improve service productivity and efficiency, several key aspects need attention.
Companies should carefully plan and schedule maintenance activities, ensuring they align with equipment criticality and manufacturer recommendations. Proper resource allocation is essential, assigning skilled technicians and providing necessary tools and spare parts.
During execution, technicians should follow established procedures, document their activities, and address any issues encountered. Analyzing collected data enables identifying trends and areas for improvement. Integrating preventive maintenance with the overall maintenance strategy ensures a comprehensive approach. For example, a manufacturing company could schedule regular inspections and lubrication for machinery to prevent breakdowns and optimize equipment performance.
Optimize work order management
Optimizing work order management is instrumental in improving service efficiency. By implementing a streamlined and efficient system to manage work orders, companies can enhance their overall service delivery. Cloud-based work order management solutions offer significant advantages in this regard.
Cloud-based work order management allows for centralized storage, easy accessibility, and real-time updates of work orders. Service teams can access work orders from anywhere, eliminating delays and improving response times. Additionally, cloud-based solutions provide automated workflows, enabling efficient assignment of tasks, tracking of progress, and timely notifications.
Moreover, cloud-based work order management systems facilitate seamless collaboration among team members, enabling real-time communication, document sharing, and issue resolution. This eliminates manual processes, reduces errors, and enhances overall operational efficiency.
Overall, leveraging cloud-based work order management optimizes service efficiency by streamlining workflows, improving communication, and ensuring timely and accurate execution of tasks.
Enhance technician training
There is one thing that can be easily overlooked in this line of business – your technicians are the face of the service you provide. To enhance service efficiency, it is essential to empower technicians and help them reach their full potential.
Enhancing technician training through the use of virtual reality (VR) and augmented reality (AR) can significantly improve service efficiency. VR and AR technologies provide immersive and interactive training experiences that allow technicians to learn and practice in simulated environments.
Practical actionable tasks for implementing VR and AR training can be:
- Develop VR training modules for simulated learning experiences.
- Implement AR-based on-the-job support for technicians.
- Utilize AR for collaborative remote assistance from experts.
- Track and assess technician performance using VR and AR platforms.
- Continuously update and improve VR and AR training materials.
By implementing these tasks, technicians can benefit from enhanced training experiences using VR and AR technologies, leading to improved service efficiency in manufacturing.
Utilize IoT and remote diagnostics
By integrating IoT devices and leveraging remote diagnostic capabilities, you can monitor equipment performance in real-time, detect issues remotely, and proactively address them. A digital twin, which is a virtual replica of a physical asset or system, can be connected to the IoT network, allowing you to simulate and analyze equipment behavior in real-world scenarios.
This integration enables you to compare real-time data from the physical equipment with its digital twin, facilitating predictive maintenance and optimization. By continuously monitoring and analyzing data, you can detect anomalies, anticipate failures, and schedule maintenance before issues occur. This not only reduces the need for physical inspections but also minimizes response times, as you can remotely diagnose and resolve problems based on the insights provided by the digital twin.
Embrace field service management tool
Enhancing digital capabilities by implementing an excellent field service Management app can significantly raise the level of your service. The tool will revolutionize service operations by providing a comprehensive platform for efficient management.
With FSM software, you can optimize technician scheduling, dispatch assignments based on proximity and skillset, and track real-time progress. The software’s mobile-friendly features enable technicians to access job details, customer information, and relevant documentation on their smartphones or tablets, enhancing their productivity and decision-making capabilities in the field.
FSM app also facilitates seamless communication between technicians, customers, and the back office, ensuring that everyone stays updated on job statuses, changes, and updates. By implementing FSM software, you can streamline your service operations, improve response times, and deliver exceptional customer experiences.
Optimize resource allocation
Optimizing resource allocation is vital for improving service efficiency, and Digital Twin technology proves to be instrumental in achieving this objective. By creating virtual replicas of physical systems, companies can simulate different scenarios and test resource allocation strategies without disrupting actual operations in manufacturing industry.
Real-time monitoring and integration of sensor data enable companies to identify bottlenecks and make proactive adjustments. Moreover, predictive analytics and machine learning algorithms help anticipate future demands, enabling dynamic allocation of resources and optimized scheduling.
Continuous monitoring and improvement based on real-time feedback drive ongoing enhancements in resource allocation, resulting in optimal resource utilization, reduced costs, and improved service efficiency. Digital Twin technology offers a powerful solution for intelligently optimizing resource allocation in pursuit of operational excellence.
Streamline parts and inventory management
Streamlining parts and inventory management is a vital step towards improving service efficiency in manufacturing. By optimizing the management of parts and inventory, companies can ensure timely availability of required components, minimize production downtime, and enhance overall customer satisfaction.
To achieve this, manufacturers can implement various strategies. They can employ inventory management software to track stock levels, monitor usage patterns, and automate reordering processes. Utilizing barcoding or RFID technology can improve accuracy and speed in identifying and locating specific parts within the inventory.
Additionally, adopting just-in-time (JIT) or lean manufacturing principles can help minimize excess inventory and reduce storage costs. By maintaining closer relationships with suppliers and establishing reliable delivery systems, manufacturers can ensure a steady supply of parts when needed.
Efficient parts and inventory management leads to streamlined production processes, faster turnaround times, and reduced costs associated with excess inventory or delays due to parts unavailability. Overall, it improves service efficiency by enabling manufacturers to meet customer demands promptly while maintaining optimal inventory levels.
Strive for continuous improvement
Encouraging employees at all levels to actively seek ways to improve processes, identify bottlenecks, and propose innovative solutions, organizations can unlock new levels of efficiency.
To establish this culture, companies can implement practices such as regular performance reviews, where employees are encouraged to share their ideas and suggestions for improvement. Engaging employees in problem-solving discussions and empowering them to take ownership of their work fosters a sense of accountability and drives a proactive mindset towards service efficiency.
Additionally, providing opportunities for ongoing training and professional development equips employees with the skills and knowledge needed to implement process improvements effectively. Promoting cross-functional collaboration and knowledge sharing further strengthens the culture of continuous improvement.
Recognizing and rewarding employees for their contributions to service efficiency reinforces the desired behaviors and encourages a collective effort towards innovation and optimization. Regularly measuring and analyzing key performance indicators (KPIs) enables companies to identify areas for improvement and track progress.
Implement performance metrics
Implementing performance metrics is a crucial step to improve service efficiency in manufacturing. By defining and tracking key performance indicators (KPIs), companies can measure and evaluate various aspects of their service operations.
First, identify relevant KPIs such as response time, resolution time, customer satisfaction ratings, and first-time fix rate. These metrics provide insights into the speed, effectiveness, and customer-centricity of the service provided.
Next, establish performance targets for each metric and regularly monitor progress. This allows for early detection of bottlenecks or inefficiencies, enabling timely interventions and process improvements.
Additionally, share performance data with the service team, fostering a culture of accountability and continuous improvement. Conduct regular performance reviews and provide feedback to support agents, recognizing exemplary performance and addressing areas for development.
By implementing performance metrics, manufacturing companies can gain visibility into service efficiency, identify areas for enhancement, and drive continuous improvement efforts, ultimately leading to higher customer satisfaction and optimized service operations.
Foster collaboration and communication
To improve service efficiency, fostering collaboration and communication within the organization is essential. Establishing effective communication channels and promoting collaboration among different teams and departments enables seamless information sharing, faster decision-making, and improved problem-solving.
Encourage regular cross-functional meetings where representatives from various departments, such as production, customer service, and logistics, can discuss challenges, share insights, and align their efforts. This collaborative approach ensures that everyone is on the same page and working towards common goals.
Additionally, leverage digital tools and platforms for communication, such as project management software, internal messaging systems, and shared document repositories. These tools facilitate real-time communication, document sharing, and collaborative project management, promoting efficient information exchange and reducing response times.
By fostering collaboration and communication, companies can break down silos, streamline processes, and enhance service efficiency by enabling effective coordination and alignment across the organization.
Conclusion
Efficiency is the lifeline of manufacturing companies, and greater efficiency in manufacturing is no exception. By aligning service performance with well-defined maintenance goals, businesses can optimize operations, reduce downtime, and unlock their true potential through a more strategic and proactive approach.
Keep an eye on emerging trends and evolving customer expectations. With these principles in mind, you can pave the way for a successful journey towards improved service efficiency. By doing so, manufacturing companies can propel themselves towards a brighter future where efficiency reigns supreme. For further assistance, connect with our experts at FieldCircle.