A Detailed Lathe Machine Preventive Maintenance Checklist
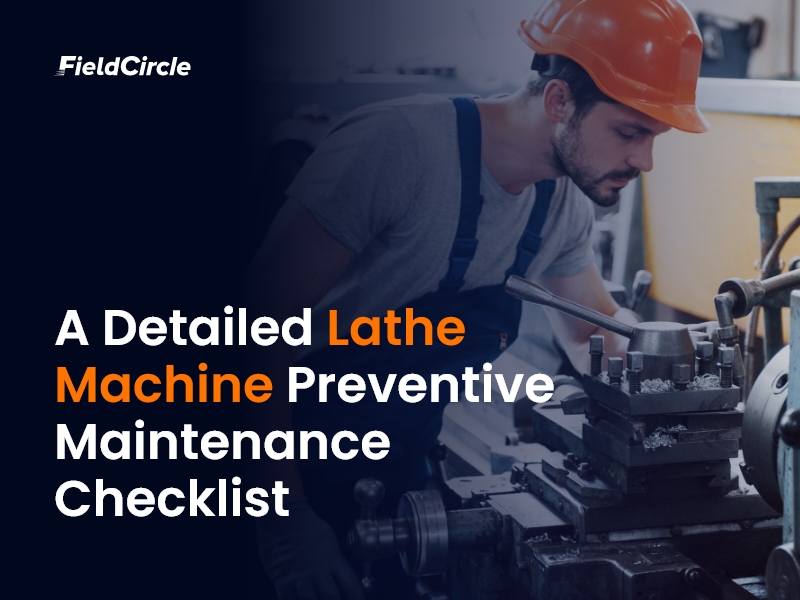
Found across industries such as automotive, aerospace, and metal fabrication, lathe machines play a key role in shaping, cutting, and drilling various materials with precision.
From turning basic cylindrical parts to crafting complex mechanical components, their repetitive use in demanding environments gradually impacts their performance. Over time, factors like vibration, friction, and continuous load begin to degrade critical elements such as spindles, bearings, slides, and tool posts.
A comprehensive maintenance program for smooth lathe operations rests on a checklist. By following a structured checklist, maintenance technicians can spot alignment issues, lubrication gaps, or abnormal sounds early on.
Let’s discuss a comprehensive checklist for lathe maintenance, its benefits, and the best practices for maintenance of these key equipment.
What is a Lathe Machine Preventive Maintenance Checklist?
A lathe machine preventive maintenance checklist is a fixed set of maintenance and inspection checks for all parts of a lathe machine – spindle, chuck, tool post, bedways, carriage, tailstock, etc. It outlines steps for cleaning, tightening, oiling, and testing functions to keep the lathe running without any hassles.
What are the Benefits of a Lathe Machine Preventive Maintenance Checklist?
A lathe machine maintenance checklist comes with a range of benefits for maintenance teams. For instance it:
- Reduces Downtime from Sudden Failures
A maintenance checklist helps detect blocked coolant lines, loose parts, and chip accumulation early. Operations stay on schedule without frequent halts that affect delivery targets.
- Keeps Machining Accuracy within Standard Limits
Routine checks on alignment, backlash, and tool conditions help manage wear before it affects output. Part rejection stays low, and dimensional precision stays consistent.
- Extends Life of High-Wear Components
Regular attention to bearings, belts, and couplings prevents premature failure. Shops get more operating hours from every installed part.
- Cuts Repair Costs Significantly
Early identification of lubrication gaps or tool imbalance avoids larger mechanical faults. Service costs stay low, and the machine avoids unnecessary downtime.
- Brings Structure to Operator Tasks
Operators follow a defined standard instead of relying on memory. Each shift handles the equipment with consistency, reducing misuse or skipped steps.
- Protects Finished Part Quality
Accurate spindle movement and stable feed rates remain intact under routine checks. Surface finish, tolerance, and repeatability stay within acceptable production standards.
Lathe Machine Preventive Maintenance Checklist
Following are the 12 checklist items to look at during the preventive maintenance of lathe machines including CNC machines, engine lathes, bench lathes, and toolroom lathes:
1. Lubrication & Fluid Maintenance
- Oil and Lubrication System
- Verify oil levels in the gearbox, spindle, and critical moving parts.
- Ensure oil is within the specified range and not contaminated.
- Drain and replace oil in the gearbox, hydraulic system, and lubrication points.
- Use the correct type and grade of oil recommended by the manufacturer.
- Check for signs of oil leaks around seals, gaskets, and fittings.
- Tighten or replace seals to prevent further oil leakage.
- Clean or replace oil filters regularly to maintain proper fluid circulation.
- Replace filters if they are clogged, damaged, or worn.
-
Ensure the grease used matches manufacturer specifications and is applied evenly.
- Coolant System
- Ensure coolant is within the recommended levels.
- Verify coolant concentration for optimal cooling and performance.
- Drain the coolant tank to remove sludge, contaminants, and metal debris.
- Use a non-abrasive cleaning solution to clean the tank and prevent residue buildup.
- Check the coolant pump(s) for proper functionality, ensuring there are no blockages.
- Inspect coolant supply and return lines for blockages, cracks, or leaks.
- Change coolant regularly to avoid bacterial contamination and oil buildup.
- Follow manufacturer’s guidelines for coolant replacement intervals.
2. Spindle & Drive System
- Spindle and Bearings
- Inspect the spindle for signs of wear, overheating, or damage.
- Check spindle bearings for smooth rotation and minimal play.
- Replace if there’s noticeable wear or noise.
-
Lubricate spindle bearings as per the manufacturer’s guidelines to avoid friction and overheating.
- Motor and Drive Mechanism
- Test the motor’s operation to ensure smooth and efficient running without unusual vibrations or noises.
- Check electrical connections to ensure proper wiring and that there are no signs of wear, overheating, or corrosion.
- Inspect the motor’s cooling system (if applicable) and clean any air vents to prevent clogging.
- Monitor motor performance under load to ensure it’s operating within the specified range of speed and torque.
- Test for proper functionality of motor speed control, including acceleration and deceleration processes.
- Belt, Pulley, and Gearbox
- Inspect belts and pulleys for signs of wear, cracking, or misalignment.
- Adjust belt tension if needed to prevent slippage and ensure optimal transmission of power.
- Clean and lubricate pulleys to reduce friction and wear.
- Check the gearbox for proper oil levels and ensure there are no leaks.
- Inspect gears inside the gearbox for wear or damage. Replace gears that show signs of excessive wear or damage.
3. Hydraulic System
- Hydraulic Fluid and Reservoir
- Check hydraulic fluid levels and ensure they are within the recommended range.
- Inspect the condition of the hydraulic fluid for contamination, discoloration, or impurities.
- Check for signs of fluid leaks around the reservoir, pump, and hoses.
- Tighten connections or replace seals as needed.
- Clean the hydraulic reservoir to remove any sludge, debris, or buildup that could impair fluid circulation.
-
Ensure the hydraulic fluid meets the recommended viscosity and temperature specifications for optimal performance.
- Hydraulic Pumps and Valves
- Test hydraulic pump(s) for proper operation, checking for noise, excessive vibration, or overheating.
- Inspect the pump’s seals and fittings for wear or leakage.
- Check pressure relief valves to ensure they are functioning correctly and are not stuck or leaking.
- Test the flow rate of the hydraulic pump to ensure it is within the specified range.
-
Clean any filters or strainers in the hydraulic system to prevent blockages and ensure smooth fluid flow.
- Hoses and Fittings
- Inspect hydraulic hoses for cracks, abrasions, or bulging that could lead to failure.
- Check hose connections and fittings for tightness and leaks.
- Ensure all hose supports are properly positioned to prevent stress or kinks in the lines.
- Verify that hoses are routed away from heat sources and sharp edges to avoid damage.
- Inspect quick-connect fittings to ensure proper sealing and easy disconnect when required.
4. CNC or Control System
- Control Panel and Interface
- Inspect the control panel for physical damage, such as cracked buttons, broken switches, or faulty display screens.
- Check all buttons, switches, and knobs to ensure they respond correctly and there are no signs of wear or malfunction.
- Test the emergency stop button and ensure it functions properly in all circumstances.
- Clean the control panel, including buttons, display screens, and wiring connections, to remove dust or contaminants.
-
Verify that the interface is displaying accurate machine parameters (e.g., speed, feed rate, tool changes) and there are no error messages.
- Wiring and Electrical Connections
- Inspect wiring for signs of wear, fraying, or exposure. Ensure that all wires are properly insulated.
- Check electrical connections for signs of corrosion, loose connections, or overheating.
- Tighten any loose terminal connections, ensuring proper contact and avoiding electrical failures.
- Verify that grounding connections are intact and that the machine is properly grounded to prevent electrical hazards.
-
Ensure that fuses and circuit breakers are in good condition and correctly rated for the machine’s power supply.
- Software and Calibration
- Ensure that the CNC software is up to date with the latest patches or updates installed.
- Test the CNC program to verify that it communicates with the machine’s hardware without errors.
- Perform a calibration check on the CNC system to ensure that it is reading the correct positions for all axes.
- Verify that the software settings are optimized for the current machine configuration and operating conditions.
- Recalibrate the machine if any discrepancies are found between the actual machine position and the programmed position.
5. Feed Mechanism & Motion Control
- Lead Screws, Ball Screws, and Nuts
- Inspect lead screws and ball screws for signs of wear, scoring, or damage.
- Check for proper lubrication on all screw threads and replace grease if it has hardened or deteriorated.
- Measure and verify the alignment of the lead and ball screws to ensure smooth movement and accurate positioning.
-
Clean lead screws and ball screws to remove any debris or metal shavings that could impede motion.
- Feed Motors and Drives
- Inspect feed motors for smooth operation and check for excessive heat generation during use.
- Test motor performance at various load levels to verify proper function and response.
- Examine motor bearings for noise or excessive play and replace them if necessary.
- Inspect drive belts and gears for wear, cracking, or misalignment and adjust or replace as needed.
-
Check the performance of servos or stepper motors, ensuring they are delivering the correct torque and speed for the feed system.
- Slideways and Guide Rails
- Inspect slideways for smoothness and check for wear, scratches, or signs of uneven movement.
- Clean guide rails of any debris, oil buildup, or metal chips that could cause friction and affect accuracy.
- Verify that slideways are properly lubricated and that lubrication points are easily accessible and functioning.
- Check for any signs of misalignment or binding in the slideways and guide rails, and adjust or repair as necessary.
- Ensure that all mounting bolts or screws holding the slideways are tightened properly to prevent shifting.
6. Tooling, Chucking, and Workholding Systems
- Tool Holders and Magazine
- Inspect tool holders for wear, cracks, or damage.
- Check the tool retention mechanism for proper operation, ensuring tools are securely held during machining.
- Clean tool holders to remove any built-up debris, coolant, or material residue.
-
Test the tool changer mechanism for smooth operation, ensuring machine tools are picked up and placed without error or jamming.
- Chucks, Collets, and Clamping Devices
- Inspect chucks and collets for any damage or excessive wear, especially on the gripping surfaces.
- Ensure that chucks and collets are securely mounted to the spindle and are properly aligned.
- Clean and lubricate chuck jaws to ensure smooth operation and prevent jamming or slipping during use.
- Check the clamping mechanism for proper tension and secure clamping of workpieces.
- Verify that the chuck operates without excessive wobbling or vibration, which could affect machining accuracy.
7. Structural and Machine Bed
- Machine Alignment and Leveling
- Verify the overall alignment of the machine’s frame and bed to ensure all components are properly positioned.
- Check the machine’s level, particularly after any relocation or adjustments.
- Use a precision level to confirm horizontal alignment.
- Ensure that the base of the machine is stable and free from any warping or deformation that could affect machining accuracy.
-
Perform a test cut or operation to confirm that the machine maintains consistent dimensional accuracy during use.
- Check for Loose Fasteners and Bolts
- Inspect all fasteners, bolts, and screws for tightness, ensuring that no critical components are loose or improperly secured.
- Tighten any loose fasteners on the frame, bed, or other structural parts to avoid vibrations that could compromise precision.
- Check the mounting bolts for major components (such as motors, spindle, and feed systems) to ensure they are properly secured.
-
Inspect the condition of the fasteners and replace any that show signs of wear, rust, or failure.
- Inspect Base, Frame, and Columns
- Inspect the machine’s base, frame, and columns for any signs of cracks, deformation, or stress fractures.
- Check that the frame is rigid and free from any visible damage that could affect machine performance.
- Ensure that all structural parts are tightly bolted together with no gaps or looseness that could result from wear.
- Perform a visual check for any excessive vibrations or movement of the base, particularly during high-speed operations.
-
Examine the foundation beneath the machine to ensure that it is solid and provides proper support.
8. Electrical System
- Main Electrical Panel and Circuitry
- Inspect the electrical panel for any signs of wear, overheating, or damage.
- Ensure circuit breakers, fuses, and safety switches are functioning properly.
-
Check all power cables and connections for signs of wear, corrosion, or loose connections.
- Motors, Servos, and Drives
- Inspect motors and servos for smooth operation without unusual vibrations or noise.
- Verify that electrical connections to motors are secure and that no cables are frayed or exposed.
-
Test the performance of drives, ensuring that they respond correctly to control inputs.
- Grounding and Power Supply
- Check grounding systems to ensure proper earth connections are intact.
-
Test the machine’s power supply for stability, ensuring voltage levels are consistent and within the required range.
9. Safety Features & Systems
- Emergency Stop Mechanism
- Test the emergency stop button to ensure it operates correctly during an emergency.
-
Check for any obstruction around the emergency stop button and ensure it is easily accessible.
- Light Curtains, Sensors, and Interlocks
- Inspect light curtains and sensors for proper operation, making sure they respond correctly to obstructions.
-
Test safety interlocks to ensure they prevent machine operation when a safety guard is open.
- Safety Guards and Covers
- Inspect safety guards and covers for integrity and correct positioning.
-
Ensure that all covers are securely fastened and do not have cracks or damage.
10. Vibration, Noise, and Operational Checks
- Check for Excessive Vibration
- Run the machine and monitor for any unusual vibrations, especially during high-speed or heavy-load operations.
-
Inspect bearings, motors, and other moving components if vibration levels are higher than normal.
- Listen for Unusual Noises
-
Listen for any grinding, squealing, or rattling sounds that could indicate worn bearings, misalignments, or lack of lubrication.
- Load and Stress Test
-
Test the machine under normal operating load to ensure it operates within its designed capacity without excessive noise or overheating.
11. Dust, Debris, and Chip Management
- Clean Machine Bed and Surrounding Area
- Remove chips, dust, and debris from the machine bed and surrounding areas using a vacuum or brush.
-
Ensure that no chips or debris are left in the machine’s moving parts or spindle area.
- Airflow and Ventilation System
- Clean or replace filters in the ventilation system to ensure the machine is adequately cooled and air is circulating properly.
- Check air ducts and vents for any blockages that could impair cooling or ventilation.
What are the Tips to Follow for a Lathe Machine Preventive Maintenance Checklist?
Lathe machines demand disciplined upkeep to deliver consistent performance. Their complex assemblies—spindles, slides, motors, and control systems—function best when the following practices are followed without fail:
- Stick to a Fixed Maintenance Schedule
Build a routine maintenance timetable and follow it strictly, instead of waiting for faults to appear, so that machine wear stays in check from the start.
- Never Allow Debris or Coolant Residue to Accumulate
Clear away metal chips, dust, and leftover coolant after every use to stop abrasion, clogging, and surface damage from creeping in over time.
- Rely on Proper Tools to Check Alignment and Tolerances
Use precision instruments like dial indicators and test bars regularly to catch misalignments before they lead to part defects or tool damage.
- Replace Worn Parts Promptly—Don’t Wait for a Breakdown
Act as soon as any wear signs show up on belts, bearings, or tool holders rather than stretching their use, because delays often lead to more costly damage.
- Keep an Eye on Unusual Noises or Vibrations During Operation
Pay close attention to abnormal sounds or shaking during use and halt operations immediately to trace and fix the source before it escalates.
- Train Operators to Spot Maintenance Red Flags
Make sure operators know how to recognize early symptoms like uneven tool marks, overheating, or fluctuating feed so they respond without hesitation.
To Wrap Up
A structured checklist turns an often-overlooked routine into a reliable process of lathe maintenance. For lathe machines, having clearly defined checkpoints helps streamline upkeep without second-guessing what’s been done or missed. You follow instructions and you build consistency into your operations. Once that rhythm is set, reliability follows.
Download our comprehensive lathe maintenance checklist for weekly, monthly, quarterly, and annual maintenance of your lathe machines and leave no room for downtime.