Top 11 Best Practices for Manufacturing Maintenance
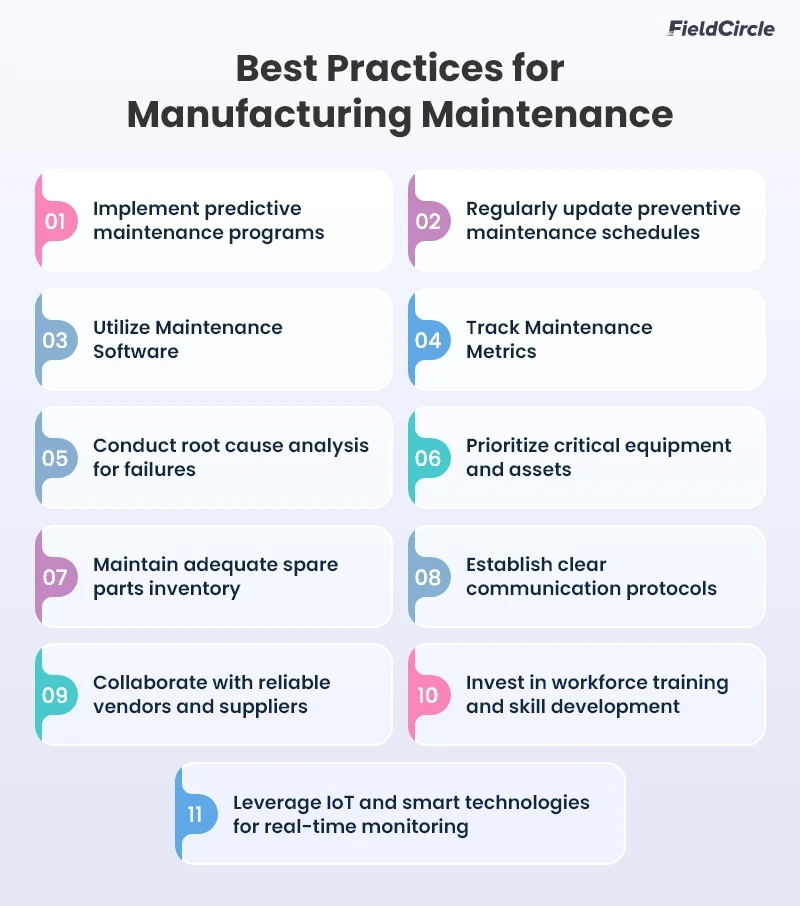
Effective manufacturing maintenance is the backbone of successful operations, because it keeps machines in peak condition. However, when maintenance takes a back seat, it comes with many adverse consequences surrounding cost and performance.
Smart manufacturers don’t wait for things to go wrong, because they follow maintenance best practices to keep everything in top shape and avoid costly surprises.
Drawing from insights gained through years of working with top manufacturers, we’ve compiled the following list of manufacturing maintenance best practices:
- Implement predictive maintenance programs
- Regularly update preventive maintenance schedules
- Utilize Maintenance Software
- Track Maintenance Metrics
- Conduct root cause analysis for failures
- Prioritize critical equipment and assets
- Maintain adequate spare parts inventory
- Establish clear communication protocols
- Collaborate with reliable vendors and suppliers
- Invest in workforce training and skill development
- Leverage IoT and smart technologies for real-time monitoring
We lay these best practices all out in the following discussion and help understand why every manufacturing business looking to streamline its maintenance processes must adhere to them. Read on.
1. Implement Predictive Maintenance Programs
Predictive maintenance in manufacturing includes using IoT sensors to monitor real-time equipment performance and condition monitoring devices, such as vibration analysis, thermal imaging, and oil analysis, to identify early signs of wear and tear, leaks, overheating, and other components that degrade machinery performance, output, and lifespan.
Manufacturers utilize AI-driven predictive analysis through CMMS to analyze real-time data from IoT sensors and condition monitoring devices and provide actionable insights to anticipate failures, reducing unplanned downtime and costly repairs. It is further acknowledged by the statistics that AI predictive maintenance in the automotive industry helps reduce breakdowns by 70% and reduce downtime by up to 50%.
With timely maintenance schedules based on analytics, maintenance technicians intervene early before minor issues become significant problems. This helps achieve seamless data-driven operations, ensuring better asset reliability and enhanced productivity. Maintenance teams regularly inspect machines and tools and schedule necessary maintenance tasks to achieve optimal performance, extending asset lifespan.
2. Regularly Update Preventive Maintenance Schedules
Manufacturers regularly update preventive maintenance schedules, which effectively schedules and tracks maintenance activities and automates reminders for equipment servicing. This eliminates the need for emergency repairs, which are 3-5 times more expensive than planned maintenance.
The maintenance team also conducts manual inspections periodically and maintains proper maintenance logs to keep detailed records of all the maintenance activities. This helps determine the next major maintenance task for specific equipment and schedule a planned breakdown for maintenance without disrupting production. It also provides information on spare parts and tools, helping inventory management stock the required parts. It helps minimize repair delays due to unavailability or shortage of spare parts.
Focusing on a regularly maintained preventive maintenance schedule fosters a proactive maintenance culture, builds customer trust through reliable and consistent product delivery, and helps stay competitive in the market with minimum delays.
3. Utilize Maintenance Software
Manufacturing plants utilize manufacturing maintenance software to streamline maintenance operations. They offer a centralized data platform for enhanced collaboration between production, maintenance, and management teams, enabling easy and accessible tracking, assigning, planning, and managing maintenance activities. This maintenance method ensures interrupted production, minimizes downtime, prolongs equipment lifespan, and enhances operational efficiency.
Besides maintenance tasks, maintenance software also tracks equipment performance, handles work orders, and helps in efficient inventory management. Proper equipment data analysis via maintenance software provides data-driven insights for better decision-making, effective resource allocation, and reduced repair response time.
Prioritizing the use of preventive maintenance software ensures scalable and efficient operations. It helps reduce unexpected breakdowns by proactively scheduling maintenance tasks, mitigates repair and replacement costs through early issue detection, and improves workplace safety and compliance with regulations by ensuring timely and systematic maintenance.
4. Track Maintenance Metrics
Tracking maintenance metrics like downtime hours, repair costs, and failure rates helps the maintenance team generate KPIs like Mean Time Between Failures (MTBF) and Mean Time To Repair (MTTR), reflecting the current state of maintenance processes. These KPIs evaluate equipment performance and identify improvement areas and inefficiencies in manufacturing processes. MTBF provides average operational time between equipment failures, indicating asset reliability, while MTTR indicates the mean time needed to repair and restore equipment failure to original functionality. Using tools like data dashboards and analytics platforms enhances visibility into maintenance performance.
Maintenance metrics track operational details and feed them to KPIs to interpret and align maintenance strategies with organizational goals. Tracking metrics enables manufacturers to enhance equipment reliability by identifying maintenance needs and preventing failures. It helps reduce maintenance costs by optimizing resource usage and increasing uptime. This technique allows manufacturers to gain actionable insights for adjusting and optimizing maintenance strategies based on KPI data, ensuring long-term success.
5. Conduct Root Cause Analysis for Failures
Manufacturing maintenance conducts root cause analysis (RCA) for failures to identify and address underlying equipment issues and prevent recurring asset failures in manufacturing. This technique involves six major steps: defining the problem, gathering data, identifying potential causes, analyzing and selecting primary causes, developing corrective actions, and implementing and monitoring solutions. Various tools and methods necessary for successfully implementing this manufacturing maintenance practice include a Fishbone Diagram, 5 Whys, Fault Tree Analysis (FTA), and Pareto Analysis. Manufacturers utilize structured methodologies like Failure Mode and Effects Analysis (FMEA) to develop robust preventive strategies.
RCA reduces the risks of repeated breakdowns, lowers repair and replacement expenses, enhances equipment reliability, mitigates the probability of equipment failure, improves workplace safety, increases production efficiency, and boosts customer satisfaction. For example, a leading automotive manufacturer tackling recurring quality issues experienced a 30% reduction in defects after conducting RCA. This proactive approach prioritizes sustainable solutions and fosters a culture of continuous improvement.
6. Prioritize Critical Equipment and Assets
Manufacturers should prioritize critical equipment and assets to ensure that the most essential machinery receives the necessary attention to maintain production continuity. Asset Criticality Analysis identifies and allocates resources to high-priority assets. Failure Mode and Effects Analysis (FMEA) identifies and prioritizes potential failure points to reduce the risks of major breakdowns that disrupt the supply chain. Manufacturers implement preventive and predictive maintenance plans to analyze asset performance and schedule maintenance tasks based on their criticality.
Implementing the practice of prioritizing critical equipment and assets helps allocate limited resources most effectively so maintenance goals are best aligned with business objectives. This practice prevents cascading failures that disrupt production lines. It supports a proactive, data-driven maintenance culture that enhances equipment reliability and efficiency for long-term success.
Other benefits include lower maintenance costs due to targeted efforts, extended asset lifespan, reduced replacement frequency, and improved safety and compliance with industry standards. To provide a better perspective, a precision parts manufacturer prioritized the five most critical CNC machines and experienced a 32% reduction in unplanned downtime, a 21% decrease in maintenance costs, and 3.2 times ROI.
7. Maintain Adequate Spare Parts Inventory
Using inventory management software, which tracks stock levels and usage trends of parts and tools, helps maintain adequate spare parts inventory. This software provides a centralized database that production and maintenance teams can easily access to ensure proper stocking and avoid under/overstocking.
Proper spare parts inventory management also saves storage space and lowers operational costs. It also reduces repair and replacement delays, as scarcity or unavailability of parts is eliminated.
For effective spare parts inventory practice, regular stock audits must be conducted to ensure the availability of essential components. Manufacturers must establish reliable vendor relationships and have multiple vendors to obtain a regular and timely supply of assets. They should also have a backup plan in the form of local suppliers during emergencies. These practices help reduce repair delays due to the quick accessibility of parts during failures, save procurement costs by avoiding over/understocking, and enhance equipment longevity with timely repairs.
8. Establish Clear Communication Protocols
In the manufacturing industry, it is crucial to establish clear communication protocols for seamless collaboration between production, maintenance, and management teams regarding maintenance activities. Manufacturers must implement tools like Slack, MS Teams, or standardized maintenance request forms to streamline information sharing and task allocation. They must conduct physical or online team meetings to discuss maintenance strategies and align them with organizational goals.
Another method for efficient communication is to implement standardized maintenance logs and shift reports that provide detailed historical and current maintenance information. Manufacturers also use visual management tools like dashboards and color-coded systems to distribute and track tasks effectively.
They also centralize communication, enhancing team collaboration by enabling members across departments to track, assign, monitor, manage, and plan maintenance activities. These techniques reduce misunderstanding and delays in addressing maintenance issues, enhance productivity by streamlining workflows, facilitate proactive maintenance planning, and minimize breakdowns and errors in maintenance activities.
9. Collaborate with Reliable Vendors and Suppliers
Strong collaboration with reliable vendors and suppliers ensures access to quality parts and materials for efficient manufacturing operations. It also builds trust for timely support and partnership during emergencies.
Manufacturers must establish service-level agreements (SLAs) to clearly define maintenance expectations and turnaround times to create a trustworthy relationship with suppliers. They must conduct periodic audits to evaluate vendor performance and maintain multiple supplier relationships for a smooth flow of parts and equipment. Maintaining open communication for transparent issue resolution is also essential.
Reliable vendors ensure the timely delivery of assets and technical support, reducing downtime and operational risks. They also provide consistent quality, helping manufacturers avoid unexpected expenses. The availability of high-quality replacements extends asset lifespans and minimizes maintenance costs. Manufacturers should prioritize a good partnership with vendors and suppliers to strengthen business relationships, foster long-term growth, avoid operational disruptions, and enhance productivity and customer satisfaction.
10. Invest in Workforce Training and Skill Development
Manufacturing sectors should invest in workforce training and skill development to hone skilled employees who can handle complex equipment and adapt to advanced technologies. Providing training sessions to staff via on-the-job training, workshops, and certification courses in emerging tools like IoT and computerized maintenance management system (CMMS) ensures continuous skill enhancement.
Manufacturers leverage e-learning platforms to allow employees to develop skills and gain the knowledge necessary to operate machines and technologies safely and efficiently. Other methods include cross-functional training and mentorship programs.
These investments help develop problem-solving capabilities, improve resource utilization, and enhance manufacturing efficiency. Well-trained staff swiftly identify and resolve issues, reducing downtime. They also handle equipment correctly to minimize workplace hazards and prevent expensive repairs and replacements. By prioritizing workforce development, manufacturers develop a knowledgeable and adaptive team that influences equipment reliability and operational success.
11. Leverage IoT and Smart Technologies for Real-time Monitoring
Manufacturing maintenance leverages IoT and smart technologies, such as IoT sensors, AI-powered analytics, and smart alarms that monitor real-time data to detect anomalies and provide actionable insights instantly.
Manufacturers use IoT sensors to track machine performance, cloud platforms and predictive maintenance software for data analysis, and mobile apps for real-time monitoring and alerts. These practices reduce unplanned maintenance costs and equipment failure, improve workplace safety, extend machinery lifespan, enhance data-driven decision-making, and optimize energy and resource usage for sustainability.
For example, a large industrial equipment manufacturer implemented AWS IoT Core, AWS IoT SiteWise, and Amazon SageMaker to collect real-time sensor data and use ML algorithms to predict machine failures. This reduced downtime by 25% and lowered maintenance costs by 30%. Prioritizing advanced technologies helps the manufacturing sector stay competitive with evolving tech, align operations with industry 4.0 technologies, and achieve long-term cost savings and operational reliability.
Conclusion
Choosing essential manufacturing maintenance strategies reduces frequent breakdowns, enhances efficiency, and boosts production. Practices such as predictive maintenance, preventive scheduling, utilizing maintenance software, conducting RCA, and leveraging IoT tools and advanced technologies enable real-time monitoring for data-driven decisions. These innovations minimize downtime, optimize resource utilization, and ensure seamless operations. By integrating these strategies, manufacturers achieve sustainable growth and maintain a competitive edge in an ever-evolving industry.