Key Maintenance Statistics That You Shouldn’t Miss
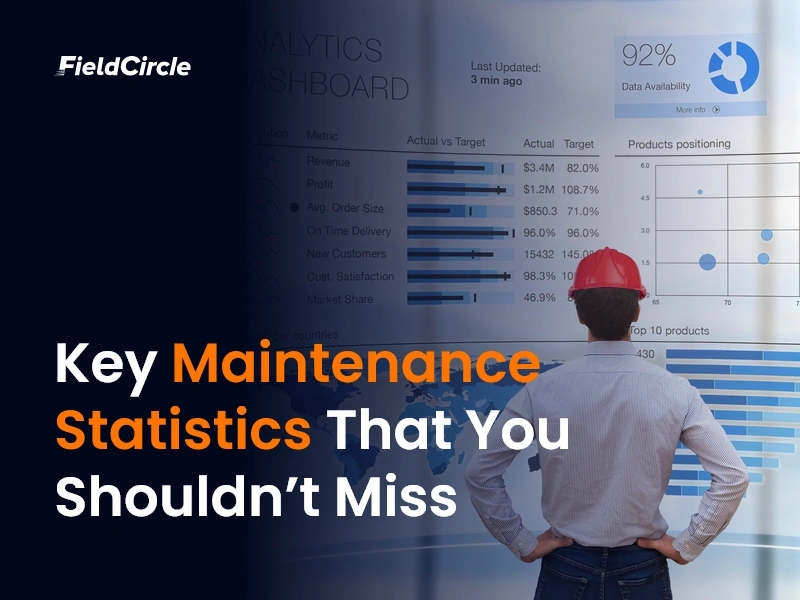
For maintenance managers, statistics guide everything right from determining when to service equipment to spotting trends in failures that might otherwise go unnoticed. A good industry data gives direction and maintenance professionals can stay one step ahead. How the industry is growing, how the technology is increasing its sway, and how various maintenance strategies are making an impact are all captured by statistics.
With our meticulous research, we have culled key maintenance statistics from credible sources. Ranging from the market size, technology to sustainability and safety, these statistics provide a comprehensive study of the maintenance industry. By understanding these numbers, you can stay ahead and tackle maintenance challenges with confidence.
Market Dynamics
- The global market for maintenance, repair, and operations (MRO) is expected to reach USD 700.80 billion by 2025. Projections indicate the market will grow to USD 842.6 billion by 2033, reflecting a compound annual growth rate (CAGR) of 2.33% from 2025 to 2033. As of 2024, Europe holds the largest share of the market, accounting for over 32.7% of the global share. (imarc)
- In 2021, the global MRO market was valued at USD 629.50 billion. It is anticipated to expand to USD 779.28 billion by 2030, with a CAGR of 2.40% during the period from 2022 to 2030. (straits research)
Technology Adoption
- On average, organizations rate their readiness for the transition to digital asset productivity at 7.6 out of 10, indicating a strong but evolving readiness for digital transformation in maintenance (Mckinsey).
- Advanced organizations have realized technology-driven improvements, leading to a 20-30% decrease in maintenance costs and substantial increases in labor productivity. (Mckinsey).
- Emerging technologies in maintenance lead to a 20-50% reduction in downtime (Mckinsey).
- 26% of manufacturing facilities are already using AR for equipment and machinery maintenance (Resonai).
- The global computerized maintenance management system (CMMS) market size was estimated at USD 1.29 billion in 2024 and is projected to grow at a CAGR of 11.1% from 2025 to 2030 (Grand View Research).
- Fully integrated smart buildings can reduce maintenance cost by 20% through proactive, predictive maintenance and analytics (Schneider Electric).
- Around 80% of maintenance techs now use mobile devices or tablets to receive and update work orders (Technology Advice).
- 49% of businesses see maintenance automation as the top benefit of AR technology (Resonai).
- Computerized Maintenance Management Software (CMMS) is utilized in 59% of facilities, while 39% of facilities employ an Enterprise Asset Management (EAM) system. (Plant Engineering).
- Over 60% of respondents report a broad shift from on-premises systems to cloud computing, whereas 30% of those surveyed indicated they are either not planning to transition or have no plans for cloud adoption. (Plant Engineering).
- 57% of major maintenance service providers are planning to incorporate advanced technologies such as AI and IoT into their service models by 2026. (Global Growth Insights)
Cost and Budget
- 62% of organizations evaluate their maintenance costs and see an increase in maintenance costs during the past year, even though most have adopted modern approaches for tracking workforce utilization (Mckinsey).
- Maintenance expenses typically account for 20-60% of a company’s total operating expenditure, which presents significant opportunities for cost-saving initiatives depending on the industry and type of assets (McKinsey).
- Digitizing maintenance operations (through ERP, Digital Works Management, CMMS) can cut costs by approximately 15-30% (McKinsey).
- Inconsistent or inefficient maintenance processes often lead to wasted time, with the average maintenance operation losing around 30% of time annually (fnPrime).
- Delaying maintenance due to budget cuts or scheduling issues can lead to future costs of three to four times the initial maintenance cost due to necessary capital renewal (fnPrime).
- Operating assets to failure can result in maintenance costs up to 10 times higher than the cost of having a preventive program in place (Schneider Electric).
- Unplanned downtime costs industrial manufacturers an estimated $50 billion annually (WSJ).
- Every $1 in maintenance deferred due to budget cuts or delays can end up costing $4 in capital renewal down the line (CHT).
- Preventive maintenance accounts for about 54% of total maintenance costs, with the remainder spent on corrective and predictive approaches (IFMA).
Productivity and Efficiency
- Over the past five years, nearly all organizations (99%) have engaged in some form of maintenance transformation. Of these, 84% have embraced predictive maintenance strategies for their critical assets (McKinsey).
- In organizations with advanced reliability-centered maintenance (RCM) capabilities, approximately 70 to 85 percent of technician hours are dedicated to preventive maintenance programs (McKinsey).
- In the oil and gas sector, companies have seen a 20% average reduction in downtime, leading to production increases that amount to over 500,000 additional barrels of oil annually, even within fleets already performing at the top-tier level in the industry.(McKinsey).
- If maintenance teams are not properly organized, they can spend up to 20% of their time searching for tools or parts. (fnPrime).
- Organizations that follow best practices in planning and scheduling are able to increase wrench time to between 60% and 65% (Prometheus Group).
- The cost ratio between planned and unplanned work is 1:5, meaning unplanned work can be five times more expensive than planned work (Prometheus Group).
- A small percentage (5%) of roles are responsible for generating 95% of transformational value—identifying and filling these roles is crucial to success. (The Manufacturer).
- A strong commitment across all relevant areas of change in maintenance boosts the likelihood of a successful transformation by up to 79%. (The Manufacturer).
Challenges and Issues
- Over half (51%) of the surveyed individuals identified issues such as excessive downtime, aging equipment and infrastructure, and workforce-related challenges as among their top three current concerns (Manufacturing Digital).
- A significant 70% of maintenance transformation efforts fail, primarily due to employee resistance and a lack of change in leadership behaviors. (The Manufacturer).
- Enterprises are implementing various strategies to minimize unplanned downtime caused by unexpected equipment breakdown. The most prevalent approaches include upgrading equipment and enhancing employee training, both at 49%, followed by the introduction of preventative maintenance plans at 40%, and a shift in maintenance strategy at 30% (The Manufacturer).
Types of Maintenance
Effectiveness of Maintenance Approaches on OEE (Overall Equipment Effectiveness) metric:
- Reactive Maintenance: Leads to less than 50% OEE
- Planned Maintenance: Results in 50%-75% OEE.
- Proactive Maintenance: Can increase OEE to greater than 90%.
- Predictive Maintenance (PdM): Improves OEE, leading to 50%-75% OEE, similar to planned maintenance. (Deloitte)
Impact of Predictive Maintenance (PdM):
1. Time and Cost Efficiency:- Reduces the time required to plan maintenance by 20–50%.
- Reduces overall maintenance costs by 5–10%.
- Reduces new equipment costs by 3% to 5%.
- Increases equipment uptime and availability by 10–20%.
- Results in 5% to 15% reduction in facility downtime.
- 5%–10% reduction in material costs (MRO material spend).
- 5%–20% reduction in inventory carrying costs.
- 10% to 30% reduction in inventory levels.(Deloitte)
Workforce
- Around 73% of businesses face challenges in hiring new maintenance technicians (McKinsey).
- An overwhelming 97% of companies focus on encouraging knowledge transfer among maintenance technicians (McKinsey).
- Only 55% of businesses have established formal systems for documenting and sharing maintenance knowledge between technicians (McKinsey).
- A more-efficient workforce is one of the important reasons to have increased profitability by 4 to 10 percent (McKinsey)
- While attracting talent was among the top three concerns for maintenance engineers in 2023, staffing challenges have now emerged as the primary issue for 2024. Half of the respondents view it as a key concern, with over a third (37%) highlighting it as their number one challenge. This figure rises to 42% in larger organizations (The Manufacturer).
- Open communication has been shown to increase the chances of successful transformations by 4.4 to 8 times (The Manufacturer).
- Businesses that focus on skill development are 2.4 times more likely to succeed in transformational initiatives (The Manufacturer).
- Leveraging virtual experts could potentially boost the capacity of maintenance technicians by 15 to 35 percent (McKinsey).
Environmental & Sustainability Impact
- Preventive maintenance can help reduce the use of raw materials by approximately 20% (Hrcak).
- Preventive maintenance has the potential to lower vehicle emissions by about 30% (ResearchGate)
- Sustainable maintenance practices can cut energy consumption by 5-15%, particularly when considering the energy saved by avoiding operational downtimes (Quant).
Safety and Compliance
- Fall protection violations, which are particularly relevant to maintenance tasks performed on rooftops, ladders, and mezzanines, have remained the top cited issue for the thirteenth consecutive year. These violations contributed to a total of $47.4 million in fines (MSC).
- In 2023, maintenance and custodial workers experienced one of the highest fatal injury rates in the workforce, with 337 fatalities recorded in the U.S. This translates to a fatality rate of 7.1 per 100,000 workers, nearly double the national average which ranged between 3.5 and 4.0. (U.S. Bureau of Labor Statistics and (Census of Fatal Occupational Injuries Summary, 2023).
- According to OSHA, falls were the primary cause of workplace fatalities in 2022, claiming 865 lives. Falls represent the leading hazard in construction and pose a significant risk in facilities maintenance activities. (MSC).
Vendor Engagement
- A McKinsey case study showed that by consolidating their global maintenance suppliers under a single primary FM partner and standardizing their services, a company was able to reduce costs by over $150 million over three years, along with simplifying maintenance management processes. (McKinsey)
- 64% of enterprises believe that in order to retain their business, enterprise asset management (EAM) vendors must prove their ability to integrate systems effectively. (Plant Engineering).
- 69% of maintenance professionals in the manufacturing and facility sectors are focusing on diversifying their supplier base to overcome challenges within their supply chains. (Manufacturing Digital).
To Wrap Up
While statistics may never be set in stone, as they are part of an ongoing study and subject to change, they offer valuable insights for any given period. These statistics shed light on key trends and shifts that businesses need to keep an eye on, especially in industries like maintenance, where precision and adaptability hold the key.
As we can see, the rising numbers in technology adoption indicate a clear shift towards technology-driven solutions in maintenance operations, which emphasizes the need for smarter, more efficient management. As these statistics reveal, integrating tools like preventive maintenance software has become increasingly essential. Enterprises that base their future maintenance strategies on solid digitally-equipped foundation will reap significant benefits.